Combined with innovative drive and clamping solutions, the MIND-M plus by eldec provides its users with huge increases in productivity for induction hardening, leading to a decrease in overall unit costs. The powerful generator inside plays an extremely important role.
Author
Markus Isgro
Historically, the power of a car’s engine was dependent on the number and size of cylinders – today, that’s a thing of the past! Electronic engine control, turbochargers or compressors are responsible for the overall performance. The turbocharger has a particularly important role—a Swiss invention dating back to 1925, the turbocharger was used to considerably increase engine power. What distinguishes this component, why is it increasingly important and what are the benefits of using electrochemical machining? —Five interesting facts about turbochargers:
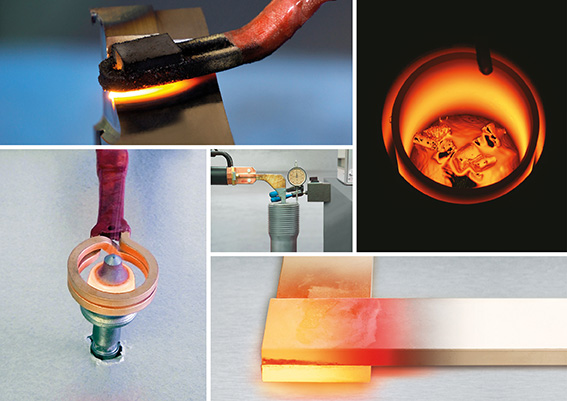
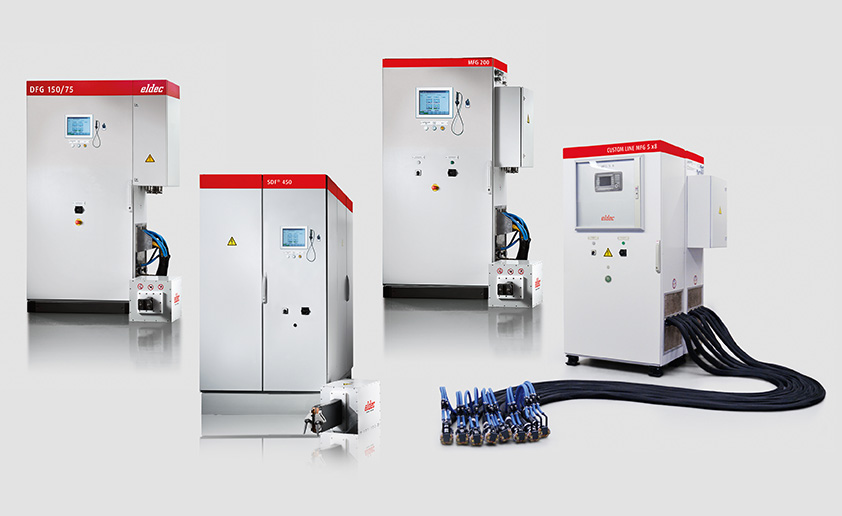
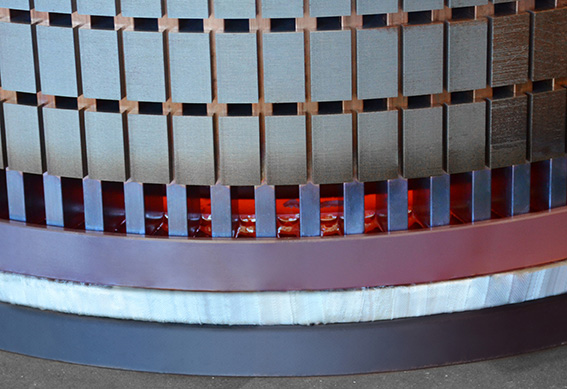
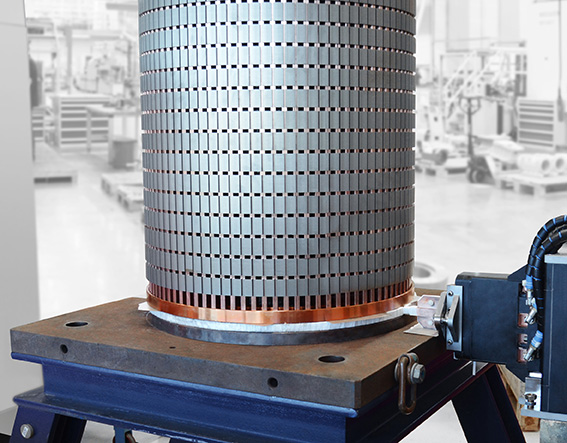
eldec CUSTOM LINE generators: customized energy source for perfect induction heating
by Markus Isgro
“Customized” is the key word when it comes to delivering a perfect production solution for building systems and machinery. Each technology is individually tailored to the customer’s environment, guaranteeing a highly efficient and optimally configured process. Induction heating in particular is one of the technologies that requires customization because the quality of the customer’s process depends on a whole range of very specific details. As the energy source, the generator plays an important role here. The experts at EMAG subsidiary eldec, based in Dornstetten, Germany, know this very well.
Experts are predicting an increased production of cars with electric motors. Though most of these cars will be hybrids, the increase in production will still pose a challenge to production planners. The question is how to process these larger quantities?
The Swiss company Humbel has been involved in gear production since 1928—specializing in particularly sophisticated types of gears and transmission components, eventually evolving into a full-service supplier. At their facility in Kradorf, approx. 20 kilometers (12 miles) from St. Gallen, they produce both individual parts as well as complete assemblies. The company recently expanded their machine inventory to include a VL 4 vertical turning center by EMAG. — We spoke with Alex Humbel, Managing Director of Humbel Zahnräder AG in Kradolf, on the challenges facing gear producers, the importance of E-mobility, as well as their company strategy.
Brazing offers many benefits to every user, including: low heat input, good electric conductivity and permanently leak-tight connections. However, the method of choice is critical. For example, if ovens or gas flames are used, heat transfers into the material relatively slowly. Induction brazing, on the other hand, has many advantages over flame soldering or furnace soldering.
In many ways, the production of large components presents a particular challenge in manufacturing. Used in commercial vehicles, large transmission, or wind power, these parts are large – making them difficult to handle and slowing down production speeds. Adding to the production challenge is the additional technological requirements being placed on the parts, as well as the demand for improved reliability and precision, with decreased costs per piece. All of which needs to be achieved while improving process speeds.
Inductor building is a key growth sector for eldec for a combination of reasons. First, more and more companies — in industries such as automobile production or aerospace — are discovering the vast potential of induction heating. Increasingly complex parts are being heated, hardened, or annealed. Second, these developments call for specialized expertise in inductor building.
For more than 30 years, eldec has developed and built inductors that perfectly match the geometry of the workpiece.
Even though statistics on electric mobility show only moderate growth in automotive markets, the Center of Automotive Management (CAM) predicts a significant upswing in market dynamics from 2020. For Germany and the EU, this means an exponential increase in electric car sales and a fundamental change in drive technologies.
Mass customization – mass producing customer-specific products – is one of the mega trends impacting industrial production today. Automobile manufacturers became early adopters as well as experts of this practice because they quickly realized that buyers want customizable options. A study by puls market research on the significance of customization found that 28 percent of car buyers feel that it is important or very important that a new car differs from standard vehicles and equipment. Now, sophisticated, online software allows buyers to build a custom, dream model with a few clicks, choosing motor specifications, transmission types, assistance systems and countless interior equipment details. Catering to the desires of car buyers and allowing thousands of combinations of options for each model complicates manufacturing because cars have become unique items. Suppliers must produce certain components and parts in many more variants than they did just a few years ago. Furthermore, the life cycle of parts is ever shorter, because technological development is advancing at such a fast pace.