EMAG laser technology has become essential in the production of modern transmission components – the ELC machines (EMAG Laser Cell) enables effective lightweight car construction with lower component costs. The laser specialists from EMAG based in Heubach, near Stuttgart, have changed their name to “EMAG LaserTec”. What’s the reason for the change? – An interview with EMAG LaserTec Managing Director Andreas Mootz about growing success, new technologies and promising applications explains.
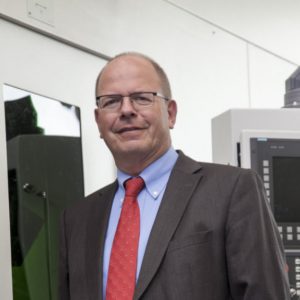
“Our process opens up great opportunities for lightweight design.”
Mr. Mootz, why has EMAG Automation been renamed to“EMAG LaserTec”?
First, it’s important to understand how quickly our core technology has evolved in recent years. Laser solutions are a major part of our sales in Heubach. Additionally, the name “EMAG Automation” no longer really matches our scope of work anymore because EMAG automation solutions are now being developed at other locations. Our new name “EMAG LaserTec” clearly emphasizes the importance of laser welding to us, both now and in the future. This technology is becoming ever more important.
What is behind the success of laser welding technology?
Consider the importance placed on “lightweight design” in the automotive industry. Practically every major component in the industry is supposed to become lighter if possible. This is very difficult however in the production of transmissions because the number of overall components continues to increase. For example, when hybrid drives are integrated, or when speeds are added in the automatic transmission. This is where our laser welding solution stands out because in many components it can replace the much heavier process using screw connections.
Can you give us some numbers to illustrate that?
The screw connection between differential gear and ring gear is a good example. By using a welded joint instead, we can reduce the weight by about 1.2 kilograms or 2.6 lbs. This reduction is an enormous factor in the lightweight design. Meanwhile, the costs for machining the individual parts are significantly reduced. Some modern double-clutch transmissions have more than 16 laser-welded seams – on the various transmission wheels, the double clutch and the differential.
How do you estimate your overall market position in the laser welding industry?
Over 160 of our ELC systems are in operation with practically all leading automobile manufacturers – and this trend is continuing to rise. The reason is our genuine and unique selling proposition: We have experience in the complete production process for laser welding, and can design the entire process chain from machining and welding, to final ultrasonic testing. As a result, the planning of new production sites and the expansion of existing ones is very simple. In addition, proven components from modular EMAG machine construction are being used. This combination of comprehensive process expertise, knowledge of components and mechanical engineering quality is something quite unique. This is the way our customers see it as well.
What will be the future role of thermal joining, another of EMAG LaserTec’s specialties?
It is, and will continue to be, equally as important. This is illustrated by the example of an “assembled” gear shaft that is no longer manufactured from a single piece. The result is an extremely compact and lightweight component, with the ability to integrate new functions. Thanks to our extensive empirical knowledge, we can support our customers as early as the component design phase and in our application laboratory. Incidentally, our established expertise in clamping technology continues to be important as well. Increasingly narrower weld seam requirements and concentricity that is more precise and positioning components. Uneven outer contours and rough surfaces present special challenges for clamping and gripping.
Are you expanding your expertise beyond the applications and technologies that you have mentioned?
Recently, for instance, we have supplied a whole series of machines with integrated laser cleaning processes. This process effectively removes residues from upstream procedures or conserving agents before welding or other process. A decisive advantage is that this kind of process is much easier to integrate into a production line than a conventional washing unit, which would interrupt the actual manufacturing process. Laser beam hardening is also important, as it can be used for partial hardening of the outer layers with minimal distortion. We have already extensively tested and applied this method in our application laboratory in Heubach. It will be used in our machines in the future, when appropriate.
What market potential do you see for laser technology?
We have several factors aiding to the success of our systems: For one thing, unit volumes in the automotive industry continue to rise, and with the ongoing success of hybrid drives our technology is becoming even more important. This, in turn, increases the number of parts that include components joined by laser welding. Additionally, the applications for laser welding and joining continue to expand. Right now, for example, we are building the first ELC system designed for commercial vehicle production. New opportunities are also opening up in the field of e-mobility – for example, in the production of rotor shafts, stators for electric motors or differentials.