Bereits seit 1928 ist das Schweizer Unternehmen Humbel in der Zahnradproduktion tätig – ein Spezialist für besonders anspruchsvolle Zahnräder und Getriebekomponenten, der sich zu einem Full-Service-Anbieter entwickelt hat. Am Standort in Kradorf, rund 20 Kilometer entfernt von St. Gallen, entstehen sowohl Einzelteile als auch komplette Baugruppen. Aktuell haben die Schweizer ihren Maschinenbestand um eine Vertikaldrehmaschine VL 4 von EMAG erweitert. – Ein Gespräch mit Alex Humbel, Geschäftsführer bei Humbel Zahnräder AG in Kradolf, über Herausforderungen für Zahnradproduzenten, die Bedeutung der E-Mobilität und die Strategie im Unternehmen.
Herr Humbel, was zeichnet das Know-how Ihres Unternehmens aus?
Letztlich geht es bei uns immer um Präzision – und das in ganz extremer Weise. Wir produzieren an unserem Hauptstandort in der Schweiz sehr anspruchsvolle Zahnräder und Getriebebauteile in kleineren Stückzahlen. Sie kommen zum Beispiel im Motorsport wie der Formel 1 oder als Prototypen im Bereich der E-Mobilität zum Einsatz. Oft sind die Kunden dabei auch auf unsere Geschwindigkeit angewiesen, denn das Entwicklungstempo in vielen Branchen ist hoch. Dementsprechend liefern wir die gewünschten Prototypen in sehr kurzen Zeitfenstern aus.
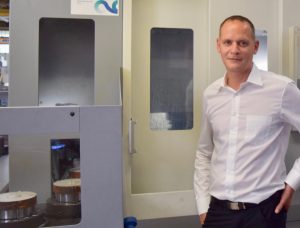
Alex Humbel, CEO bei Humbel Gear Technology, vor der neuen Maschine.
Können Sie uns ein Anwendungsbeispiel nennen?
Die Entwicklungen im Bereich der E-Mobilität sind besonders beeindruckend. Hier können wir seit 2015 auf eine ganze Reihe von Projekten verweisen. Für einen großen deutschen Automobilzulieferer produzieren wir zum Beispiel Prototypen von E-Achsen. Sie haben verschiedene Verzahnungselemente und zahlreiche geometrische Besonderheiten. Solche und ähnliche Jobs bewältigen wir effizient auf Basis unserer großen Fertigungstiefe. Alle relevanten Verfahren vom Drehen, Verzahnen und Schleifen über die kubische Bearbeitung und das Erodieren bis zum Härten stehen zur Verfügung. Außerdem verfügen wir über eigene Entwicklungsteams, die den Kunden bereits in der Konzeptionsphase unterstützen.
Warum haben Sie aktuell für eine VL 4 von EMAG entschieden?
Die integrierte Pick-up-Automation gab den Ausschlag. Mit ihrer Hilfe können wir die Produktivität bei der Herstellung vieler Flanschteile deutlich verbessern, weil der ganze Bearbeitungsprozess mannarm und schnell abläuft. Gleichzeitig ist diese integrierte Automation relativ einfach aufgebaut. Das ist wichtig für uns, weil wir komplizierte und somit fehleranfällige Automationssysteme vermeiden wollten. Darüber hinaus zeigt sich eine hohe Bearbeitungsqualität. Hier profitieren wir etwa vom Polymerbeton Mineralit®, der die Schwingungen während des Fräsprozesses reduziert. Insgesamt hat uns die Stabilität und Leistung der Maschine übrigens positiv überrascht. Wir fahren höhere Zustellungen und Vorschübe, als wir vorher erwartet hatten. Es erfolgt eine Weichbearbeitung von sehr unterschiedlichen Flanschteilen mit Losgrößen von 50 bis 200. Wir sind darauf angewiesen, kurze Rüstzeiten zu realisieren, um effizient und automatisiert produzieren zu können.
Und Sie haben in der Folge in weitere EMAG Maschinen investiert?
Das ist richtig. Seit einigen Monaten steht bei unserem rumänischen Tochterunternehmen eine VL 3 DUO und eine VL8 sowie beim tschechischen Tochterunternehmen eine VL 8. Eine VMC 450 für Tschechien wird erst noch geliefert. Es unterscheiden sich die grundsätzlichen Zielsetzungen, denn in Tschechien produzieren wir größere Teile für Schienenfahrzeuge und in Rumänien entstehen Bauteile in größeren Stückzahlen. Allerdings streben wir über alle Standorte hinweg eine Vereinheitlichung des Maschinenbestands an, um auf diese Weise bestimmte Prozesse vereinfachen und ein übergreifendes Know-how aufbauen zu können.
Welche strategischen Ziele verfolgen Sie in den nächsten Jahren?
Wir konzentrieren uns in der Schweiz auch in Zukunft auf besonders anspruchsvolle Bauteile. Seit rund zwei Jahren treten wir zudem verstärkt als ein Systemanbieter auf, der komplette Getriebebaugruppen fertigt – zum Beispiel aus dem Bereich der Elektromobilität. Diesen Weg wollen wir weitergehen. Hier eröffnet uns die grundsätzliche Flexibilität und Wirtschaftlichkeit der EMAG Technologie alle Möglichkeiten. Aber auch das Engineering für unsere Kunden wird im Fokus stehen. Wir setzen deshalb auch in Zukunft auf diese Lösungen und streben eine dauerhafte Partnerschaft mit EMAG an.