Die Laserschweißanlage EMAG ELC 6 spielt eine Schlüsselrolle in der Produktion von Antriebskomponenten für Elektromotoren. In unserem Interview mit Konrad Eibl erhalten Sie einen tieferen Einblick in die Funktionsweise, die technischen Aspekte sowie die vielfältigen Einsatzmöglichkeiten der ELC 6. Dabei erfahren Sie, wie diese innovative Maschine zur Effizienzsteigerung in der Produktion beiträgt und welche Rolle sie in der Zukunft der Fertigungstechnologie spielen wird. Besonderes Augenmerk wird dabei auf die Herstellung von Rotorwellen gelegt, einem kritischen Element in der schnell wachsenden Branche der Elektromobilität, bei dem Präzision und Prozesssicherheit von höchster Bedeutung sind.
Herr Eibl, was ist das Besondere an der EMAG Laserschweißanlage ELC 6?
Die ELC 6 ist eine Spitzenlösung für das Laserschweißen von Powertrain-Komponenten. Ihre Besonderheit liegt in der Kombination von hoher Geschwindigkeit, Präzision und Flexibilität. Sie integriert verschiedene Prozesse – vom Zusammenpressen über das Vorwärmen bis zum Schweißen – auf effiziente Weise.
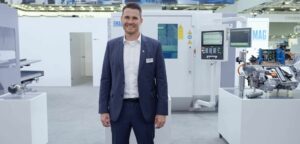
Konrad Eibl, Teamleiter Angebot, Business Unit LaserTec bei der EMAG LaserTec GmbH
Können Sie auf die spezifischen Funktionen eingehen, die die ELC 6 für die Produktion von Rotorwellen so effizient machen?
Natürlich. Bei Rotorwellen, den zentralen Bauteilen von Elektromotoren, kommt es auf Präzision an. Ein Fertigungssystem mit einer ELC 6 ermöglicht dies durch eine Reihe von Funktionen:
- Laserreinigung: Vor dem Schweißen werden die Teile mit unserer Laserreinigungsmaschine LC 4 gereinigt. So wird sichergestellt, dass die Schweißnähte sauber und frei von Verunreinigungen sind.
- Induktives Vorwärmen: Vor dem Fügen der Bauteile sorgt die Induktionstechnik für eine optimale Bearbeitungstemperatur, wodurch das Risiko von Defekten der Schweißnaht minimiert wird.
- Präzise Positionierung: Vor dem Schweißen überprüfen wir die Lage der Schweißnaht und passen die Bauteilposition exakt an. Dies geschieht durch präzises Scannen vor dem Schweißen und anschließendem Justieren der Schweißoptik mit einer NC-Achse.
- Rotationsschweißen: Beim Schweißen selbst rotiert das Werkstück während die Laseroptik fest steht. Dieses Verfahren ermöglicht einen fokussierten und präzisen Energieeintrag entlang der Rundnaht.
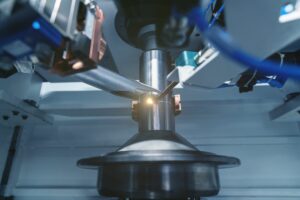
ELC 6 im Einsatz: Laserschweißen von Rotorwellen
Wie trägt die ELC 6 zur Verbesserung der Gesamtproduktivität bei?
Die ELC 6 kann in einem umfassenden Fertigungssystem eingesetzt werden. Eine clevere Integration steigert die Gesamteffizienz erheblich. Zum Beispiel ermöglicht der Drehtisch der ELC 6 das Be- und Entladen während des Schweißens, was die Nebenzeit drastisch verkürzt. Darüber hinaus sind die Prozesse in der Maschine perfekt synchronisiert, was eine kontinuierliche und störungsfreie Produktion ermöglicht.
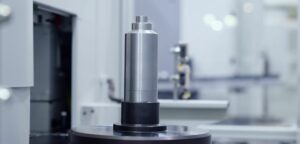
Der Rundtisch der ELC 6 ermöglicht gleichzeitiges Be- und Entladen für eine höhere Produktivität.
Wie fügt sich die ELC 6 in das Technologieportfolio von EMAG ein?
EMAG bietet ein breites Spektrum an Lösungen für die Automobil- und Zulieferindustrie. Die ELC 6 ist ein Schlüsselelement dieses Portfolios, insbesondere im Bereich der Elektromobilität. Mit unserem Know-how in einer Vielzahl von Fertigungstechnologien – vom Drehen über das Verzahnen bis hin zum Schleifen – und der Integration dieser Technologien in eine Gesamtlösung können wir unseren Kunden einzigartige, maßgeschneiderte Produktionssysteme anbieten. Es ist wichtig zu betonen, dass die Herstellung von Rotorwellen für Elektromotoren sehr anspruchsvoll ist. Mit der ELC 6 können wir diesen Herausforderungen mit Präzision und Effizienz begegnen. Durch die optimierte Werkstückaufnahme und den daraus resultierenden minimalen Verzug bietet die ELC 6 eine hervorragende Schweißnahtqualität.
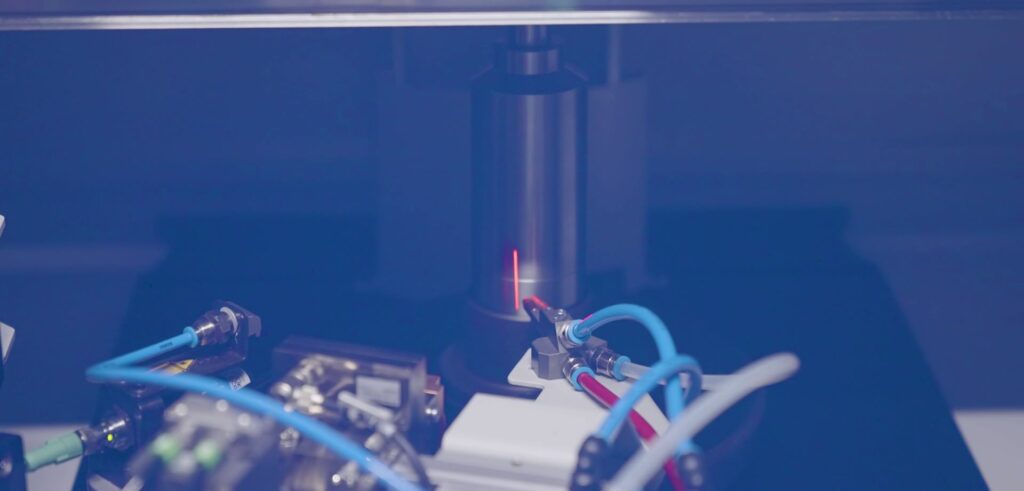
Präzise Kontrolle: Die ELC 6 bei der sorgfältigen Nahtlagekontrolle vor dem Laserschweißen
Und abschließend: Welche Zukunftsperspektiven sehen Sie für die ELC 6 und ähnliche Technologien bei EMAG?
Wir stehen am Anfang einer spannenden Entwicklung in der Fertigungstechnik, insbesondere im Bereich der Elektromobilität. Die ELC 6 ist ein Beispiel dafür, wie fortschrittliche Technologien Produktionsprozesse entscheidend voranbringen können. So haben wir mit der ELC 6 bereits herausfordernde Rotorwellenprojekte realisiert. Wir entwickeln Technologien ständig weiter, um den wachsenden Anforderungen der Industrie gerecht zu werden und unseren Kunden die beste Lösung für ihre Fertigungsanforderungen zu bieten.
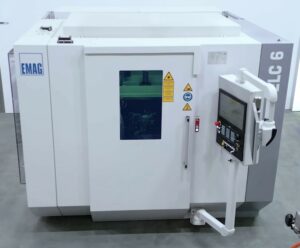
ELC 6: Innovation in der Präzisionsfertigung von Rotorwellen
Die Zukunft liegt für uns also in Lösungen z.B. für Varianten der Rotorwelle und weiteren Antriebskomponenten von Elektromotoren.