Es gibt nicht „einen“ großen Hebel, mit dem man die Energieeffizienz von Werkzeugmaschinen verbessern kann. Stattdessen kommt es auf eine ganzheitliche Betrachtung aller Energieflüsse an – so der Ansatz von EMAG, den die Spezialisten sowohl bei jeder Neuentwicklung als auch beim Retrofit von älteren Maschinen zum Einsatz bringen. Im Gespräch mit Konrad Heimbach, Lead Engineer Energieeffizienz, wird deutlich: Bereits mit relativ einfachen Maßnahmen sinken die Verbräuche massiv.
Herr Heimbach, wie reduziert man den Energieverbrauch einer Werkzeugmaschine?
Es gibt auf diese Frage nicht die eine richtige Antwort, denn in einer Maschine und in ihren Peripheriegeräten spielt sich eine Vielzahl von Prozessen ab – und hier kann man überall ansetzen. Insgesamt haben wir sechs Themenfelder für mehr Energieeffizienz definiert, an denen wir uns orientieren.
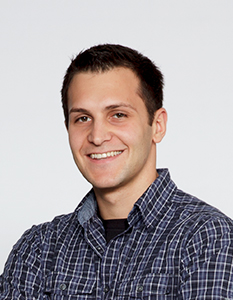
K. Heimbach, Lead Engineer Energieeffizienz
Welche Themenfelder sind das genau?
Den größten Einfluss auf den Verbrauch hat die Wahl des Fertigungsverfahrens. Man kann das einfach erklären: Es macht beispielsweise einen großen Unterschied, ob ein Teil gegossen und dann nachgedreht oder „aus dem Vollen heraus“ gefräst wird. Weitere Themenfelder sind das Maschinenkonzept, die einzelnen Komponenten, das Energiemanagement, die KI-basierte Optimierung des Fertigungsprozesses sowie die datengetriebene Produktionsplanung. Hier setzen wir überall an.
Warum spielt auch das Maschinenkonzept so eine große Rolle?
Nehmen wir das Beispiel „Automation“: Jedes Werkstück-Handling benötigt natürlich Energie. Im Umkehrschluss sorgen Maschinen, die sich einfach in den Produktionsfluss integrieren lassen, für einen sinkenden Verbrauch. Das erreichen wir etwa durch integrierte Teilespeicher und einfache Be- und Entladungsmöglichkeiten. Ähnlich interessant ist das Beispiel der Duo-Maschinen, bei denen nur ein Satz Peripheriegeräte zum Einsatz kommt – bei zwei Single-Maschinen braucht man hingegen zwei Sätze, die natürlich mehr Strom benötigen.
Haben Sie auch konkrete Zahlen rund um diese und ähnliche Einsparungen?
Wir haben zum Beispiel den Verbrauch verschiedener Verfahren verglichen, die für die gleiche Bearbeitungsaufgabe an einem Bauteil zum Einsatz kamen.
Ergebnis: Der auftretende Energiebedarf pro zerspantes Volumen ist extrem unterschiedlich. So benötigt man für das Schleifen 663 J/mm3, für das Hartdrehen 220 J/mm3 und für das Schäldrehen sogar nur 57 J/mm3. Mit anderen Worten heißt das: Bei bestimmten Aufgaben sollte man bei der Auswahl des jeweiligen Verfahrens den Energiebedarf unbedingt im Blick behalten.
Stichwort „Retrofit“ – woher wissen Sie bei einer älteren Maschine, an welcher Stellschraube man für mehr Energieeffizienz drehen muss?
Dazu erstellen wir am Anfang ein sogenanntes Energieflussdiagramm, das die Verbräuche von Antriebsverbund, Kühlung, Hydraulik und Schmierung detailliert offenlegt. Auf diese Weise haben wir zum Beispiel bei einer Wellen-Drehmaschine VTC 250, die seit 15 Jahren bei einem Kunden im Einsatz ist, die größten Problemfelder identifiziert. Hier waren es Hydraulikaggregat, KSS-Pumpe und Kühlaggregat. Alle drei Einheiten wurden getauscht. Im Endergebnis spart der Anwender rund 18.000 kWh pro Jahr oder 6,7 Tonnen CO2 ein. Das ist mehr als der Verbrauch von zwei Einfamilienhäusern pro Jahr.
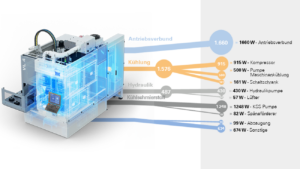
Die Energieeffizienz einer Maschine wird bei EMAG per Energieflussdiagramm ermittelt.
Wie lange dauert ein solcher Tausch?
Es geht sehr schnell, denn der Einbau erfolgt direkt beim Kunden. In diesem Fall war alles in rund eineinhalb Tagen erledigt. Übrigens amortisieren sich die anfallenden Kosten hier bereits nach rund 2,5 Jahren inklusive staatlicher Förderung.
Gibt es auch Ansätze dafür, Produktionsstandorte ganzheitlich zu optimieren?
Wir arbeiten seit einiger Zeit mit an der ETA-Fabrik – einem Forschungsprojekt der TU Darmstadt, an der sich verschiedene Industriepartner sowie Unternehmen beteiligen. In der ETA-Fabrik gibt es Demo-Prozessketten, wobei alle Fertigungsschritte abgestimmt und eng mit dem Produktionsgebäude vernetzt sind. Die Abwärme der Maschinen wird etwa genutzt, um Bürogebäude zu heizen. Übrigens gibt es im Rahmen der ETA-Fabrik auch Weiterbildungsangebote für interessierte Unternehmen.
Welche Rolle spielen IoT-Lösungen bei diesem Thema?
Sie werden immer wichtiger. Wir arbeiten aktuell zum Beispiel daran, die anfallenden Messdaten zu nutzen, um den Warmlauf der Maschinen zu kompensieren und somit überflüssig zu machen. Das ist ein wichtiges Thema, weil in dieser Startphase relativ große Energiemengen verbraucht werden – ohne jeden Output. Ähnlich interessant ist der EMAG Energy Monitor. Die Anwender können Informationen rund um Strom und Druckluft abrufen und zugleich einen Bezug herstellen und Kennwerte bilden wie „Energieverbrauch pro Schicht“, „Energieverbrauch pro Werkstück“ und „Energieverbrauch pro unproduktiver Zeit“. Unübliche Abweichungen fallen direkt auf und werden somit schneller abgestellt, was am Ende die Energiebilanz verbessert. Insgesamt kann man sicher sagen, dass wir alle Stellschrauben für eine nachhaltige Produktion nutzen, wobei wir noch am Anfang stehen – der Weg geht weiter.
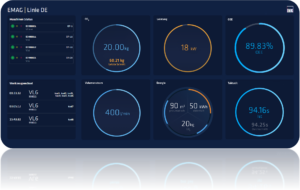
Per EMAG Energy Monitor haben Anwender die Verbrauchsdaten ihrer Maschine immer im Blick.
Mehr Informationen zur Energieeffizienz bei EMAG finden Sie auf unserer Website