Die Achterbahnen von Mack Rides stehen überall auf der Welt: Das Unternehmen mit Sitz in Waldkirch bei Freiburg ist ein Global Player der Freizeitindustrie und produziert mit hoher Fertigungstiefe die komplette Lösung inklusive Schienen, Fahrzeugen, Dekorationen, Animationen und vielem mehr. Bei der Schienenproduktion mit an Bord: Induktionstechnologie von EMAG eldec. Sie sorgt für eine präzise Wärmebehandlung vor dem abschließenden Richten der Bauteile. Ein Gespräch mit Marcel Martinetz, Leiter der Betriebsmittelkonstruktion, über das besondere Know-how seines Unternehmens und die dazugehörenden Produktionslösungen.
Tag:
induktives Erwärmen
EMAG eldec geht bei der Herstellung von Induktoren für die Induktive Erwärmung neue Wege und setzt dabei auf modernste Fertigungsmethoden, wie z.B. die Additive Fertigung.
Was dies für Vorteile bringt und welche neuen Möglichkeiten dies eröffnet, darüber haben wir mit Kadir Yilmazli gesprochen, der als Entwicklungsingenieur für Additive Fertigung bei EMAG eldec für die Weiterentwicklung in diesem Bereich zuständig ist.
Ventilatoren kommen bei vielen Produktionsprozessen zum Einsatz – sie spielen eine zentrale Rolle zum Beispiel beim Absaugen von Gasen, dem Kühlen von Werkstoffen oder der Förderung von Feststoffen im Herzen von Lufttechnik-Anlagen. Einer der international führenden Hersteller von Industrieventilatoren und Seitenkanalverdichtern ist Elektror airsystems mit Stammsitz in Ostfildern sowie zwei Produktionsstandorten in Waghäusel und Chorzów (Polen). Hier entstehen rund 60.000 Geräte pro Jahr. Bei der Herstellung der Elektromotoren, die in den diversen Ventilatoren zu Einsatz kommen, setzt der Standort Waghäusel seit Mai 2018 auf die UNI HEAT von EMAG eldec: Das System sorgt für die präzise induktive Erwärmung des Statorleergehäuses vor einem Fügeprozess. Ein Gespräch mit Roland Sand, Gruppenleiter Produktion bei Elektror airsystems, über die Wahl des richtigen Zulieferers, die Zusammenarbeit mit EMAG eldec und die Bedeutung der Prozesssicherheit:
Neben Härtemaschinen und Induktoren entwickelt EMAG eldec auch die dazugehörigen Generatoren. Eine sehr flexible Lösung stellt dabei die sogenannte Dual-Frequency-Technologie dar: Mit diesen Zweifrequenz-Generatoren lassen sich unterschiedliche Härteprozesse am Bauteil hintereinander ausführen.
Die Entwicklung von kundenspezifischen System- und Integrationslösungen ist ein wichtiger Erfolgsfaktor im deutschen Maschinenbau. Eine Zielsetzung, die EMAG Automation seit Jahren verfolgt. Das Unternehmen entwickelt ganzheitliche und perfekt angepasste Produktionslösungen für den Automobilbau, bei denen die Technologien Laserschweißen und thermisches Fügen zum Einsatz kommen. Dabei häufig mit an Bord: Generatoren von EMAG eldec aus Dornstetten im Schwarzwald. Sie dienen als Energiequelle für den induktiven Erwärmungsprozess, der beim Fügen und Laserschweißen einen wichtigen Teilprozess darstellt.
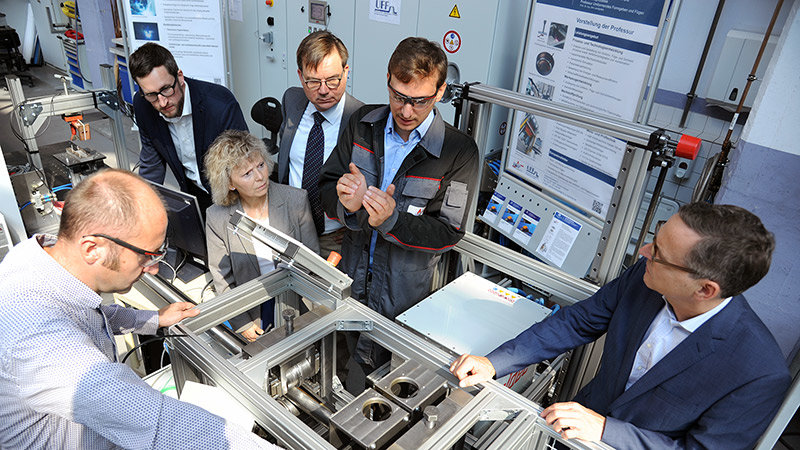
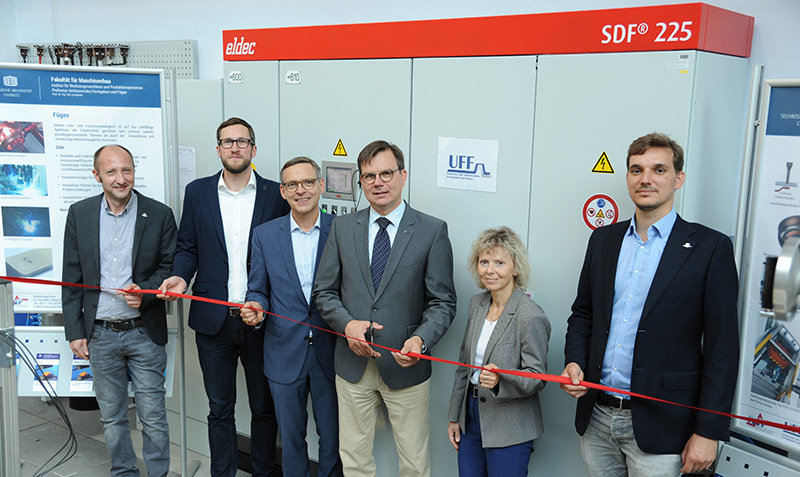
Effektiv und ressourcenschonend: Zielgerichtetes Erwärmen und Fügen moderner Werkstoffkombinationen
by Markus Isgro
Professur für Umformendes Formgeben und Fügen der TU Chemnitz erweitert ihre Anlagentechnik, um neue Forschungsfelder im Bereich komplexer Schweiß-, Wärmebehandlungs- und Umformaufgaben zu erschließen
An der Professur Umformendes Formgeben und Fügen der Technischen Universität Chemnitz wurde am 29. Juni 2018 ein neuer Induktionsgenerator in Betrieb genommen, mit dem beispielweise Halbzeuge, die aus mehreren Schichten unterschiedlicher Werkstoffe bestehen, durch unterschiedliche Frequenzen zielgerichtet erwärmt werden können. Dies könnte insbesondere für die Herstellung von plattierten Rohren in der chemischen Industrie oder im Kraftwerksbereich von Bedeutung sein. Für diese Sektoren werden allein in Deutschland jährlich 62.000 Tonnen Rohre produziert.
Experten prognostizieren steigende Stückzahlen von Neuwagen mit elektrischen Antrieben. Auch wenn ein Großteil davon über Hybridsysteme verfügen wird –, die größeren Produktionsmengen werden die Planer im Automobilbau herausfordern. Die Frage lautet: Wie lassen sich (viel) größere Mengen von E-Motor-Komponenten verarbeiten?
Kommen im Automobilbau Schweißprozesse zum Einsatz, stehen Produktionsplaner häufig vor besonderen Herausforderungen. Der Prozess muss im Sekundentakt und ohne jede negative Beeinflussung des Werkstoffs ablaufen – und genau das ist angesichts der hohen Bearbeitungstemperaturen keine selbstverständliche Forderung. Eine wichtige Rolle spielt deshalb das Vorwärmen vor dem Schweißen. Die Komponente wird punktgenau auf die benötigte Bearbeitungstemperatur von rund 160 bis 180 Grad Celsius gebracht. Das verhindert eine Aufhärtung des Werkstoffgefüges in der sogenannten Wärmeeinflusszone – der Bereich direkt neben der Schweißnaht. Auf diese Weise ist die Gefahr einer Rissbildung am Bauteil nach dem Schweißen weitestgehend gebannt.
Für die Etablierung von automatisierten Produktionsprozessen ist die induktive Erwärmung in idealer Weise geeignet: Das Verfahren lässt sich ohne Aufwand in einen übergeordneten Ablauf integrieren. Anschließend lassen sich selbst größte Stückzahlen schnell, präzise und sicher verarbeiten. Viele wichtige Verfahren wie Härten, Fügen, Löten oder Vorwärmen profitieren von der flexiblen Technologie.
Seit mehr als vier Jahren ist eldec bereits ein Teil der EMAG Gruppe – eine Erfolgsgeschichte, von der unsere Kunden profitieren. Gemeinsam haben wir zum Beispiel eine Pick-Up-Härtemaschine entwickelt, die für extrem schnelle und präzise Härteprozesse im Linientakt sorgt. Auf der anderen Seite kommen unsere Generatoren und Induktoren in vielen EMAG Füge- und Laserschweiß-Anlagen zum Einsatz. Gemeinsam treiben wir die induktive Technologie voran: Noch kürzere Taktzeiten? Eine noch präzisere Erwärmung? Wir sind auf dem Weg zu neuen Leistungskennzahlen.