Die Achterbahnen von Mack Rides stehen überall auf der Welt: Das Unternehmen mit Sitz in Waldkirch bei Freiburg ist ein Global Player der Freizeitindustrie und produziert mit hoher Fertigungstiefe die komplette Lösung inklusive Schienen, Fahrzeugen, Dekorationen, Animationen und vielem mehr. Bei der Schienenproduktion mit an Bord: Induktionstechnologie von EMAG eldec. Sie sorgt für eine präzise Wärmebehandlung vor dem abschließenden Richten der Bauteile. Ein Gespräch mit Marcel Martinetz, Leiter der Betriebsmittelkonstruktion, über das besondere Know-how seines Unternehmens und die dazugehörenden Produktionslösungen.
Hohe Anforderungen beim Achterbahn-Bau
Herr Martinetz, was zeichnet Mack Rides im Besonderen aus?
Zunächst einmal gehen wir sehr intensiv auf die Kundenwünsche ein. Bei Achterbahnen gibt es keine „Zwillinge“. Jede Lösung ist also anders, zumal wir vom Engineering über die Schienen- und Fahrzeugproduktion bis zur Animation, Endmontage und dem Aufbau alles übernehmen. Eine weitere Besonderheit ist, dass die Eigentümerfamilie von Mack Rides auch Betreiber von Achterbahnen im Europa-Park Rust ist. Die Kunden können sich hier an einem Ort verschiedene Modelle ansehen und testen.
Was bedeutet das für den Produktionsbereich?
Achterbahnen sind Einzelanfertigungen. Die Stückzahlen der dazugehörigen Bauteile sind folglich eher klein. Gleichzeitig ist unser technischer Anspruch aber sehr hoch. Deshalb setzen wir auf eine große Fertigungstiefe, mit der wir einerseits die Perfektion der technischen Details sicherstellen, andererseits aber effizient und schnell die Kundenwünsche umsetzen. Wir verfügen über einen großen Maschinenpark, der anspruchsvolle Roboterlösungen, CNC-Technologie und Manufaktur-Anwendungen intelligent kombiniert. Wenn neue Produktionslösungen anstehen, haben wir im Vorfeld immer sehr genaue Vorstellungen. Für uns ist es deshalb wichtig, dass der Maschinenbauer wie wir „tickt“, also sehr zielgerichtet arbeitet und die gewünschte Lösung mit schlanken Prozessen umsetzt.
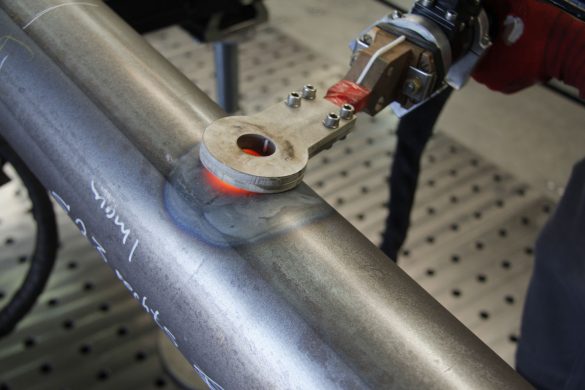
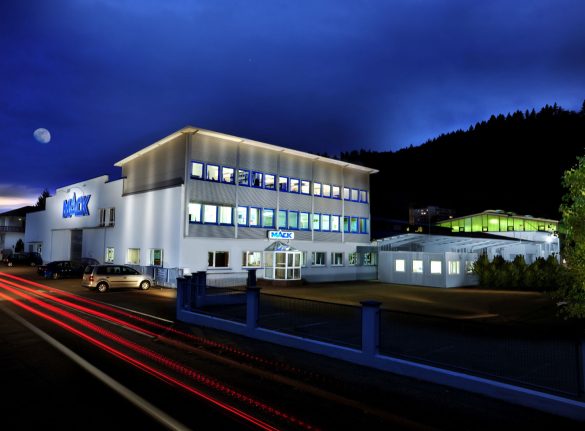
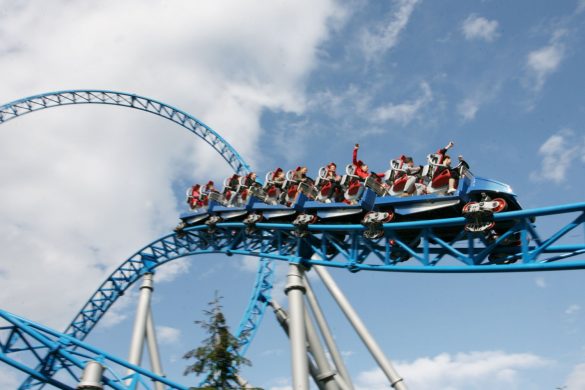
Wie kam es aktuell zu der Zusammenarbeit mit EMAG eldec?
Bei der Produktion der Achterbahn-Schienen kommt es auf eine extreme Präzision an. Sie sind bis zu rund zwölf Meter lang. Trotzdem darf ihr geschwungener Verlauf nach der Produktion maximal 3 Millimeter in der Länge und maximal 2 Millimeter in der Spurweite an Abweichung aufweisen. Das stellen wir in zwei Schritten sicher: Nach dem Biegen wird die Schiene in eine Vorrichtung eingesetzt und per Laser vermessen. Wir erkennen dann sofort jede Abweichung, die wir mithilfe dieser speziellen Roboter-Spannlösung korrigieren. Dafür müssen die Schienen allerdings zuvor an definierten Punkten erwärmt werden. Hierfür haben wir in der Vergangenheit eine offene Acetylen-Flamme eingesetzt. Allerdings bedeutet das auch einen erhöhten Arbeitsaufwand und ein höheres Arbeitsrisiko. Außerdem erfolgt die Wärmeeinbringung mit der Flamme nur oberflächlich. Folglich benötigt man einen größeren Kraftaufwand beim Richten des Rohres. Vor diesem Hintergrund rückte hier das induktive Erwärmen als Alternative in den Fokus. Wir kennen das Verfahren von einer anderen Produktionslösung in unserem Haus.
Worauf kam es bei der Umsetzung der Produktionslösung an?
Wir haben zunächst eine alternative Induktionstechnologie getestet und dabei festgestellt, dass eine prozesssichere Umsetzung im konkreten Anwendungsfall nicht einfach ist. Dazu muss man wissen, dass der Bediener einen Ringinduktor per Hand mit Kontakt zum Schienenrohr positionieren muss – und das an verschiedenen Stellen. Dabei genügt eine kleine Unachtsamkeit und der Kontakt des Induktors zum Rohr geht verloren. Das führte bei der zuerst getesteten Lösung direkt zu Überlastungsschäden am Generator. Wir sind dann auf EMAG eldec mit der Aufgabenstellung zugegangen, eine deutlich robustere Lösung zu entwickeln. Kleine Bedienfehler dürfen nicht dazu führen, dass die Anlage ausfällt.
Welchen Eindruck haben Sie heute von der fertigen EMAG eldec Lösung?
Wir sind sehr zufrieden. Die Lösung inklusive Hand-Ringinduktor sowie PICO-SC-Generator mit einer Leistung von 15 Kilowatt inklusive Kühlsystem ist seit rund einem Jahr bei uns im Einsatz. Der Prozess ist sehr stabil und es macht keine Probleme mehr, wenn der Ringinduktor den Kontakt zur Schiene verliert. Insgesamt profitieren wir zudem von einem sehr schnellen und einfachen Ablauf: Bediener starten das jeweilige Programm über die Touchpad-Oberfläche des Generators und führen den Induktor zum Bauteil. Nach einem fest definierten Zeitraum ist die gewünschte Temperatur erreicht und das Richten kann beginnen. Dabei ist die Induktionstechnologie pro Wärmepunkt rund 30 Sekunden schneller als das Erwärmen mit der Acetylen-Flamme.
Wie vollzog sich aus Ihrer Sicht die Zusammenarbeit mit EMAG eldec?
Der ganze Prozess war schnell und zielgerichtet, wobei EMAG eldec bereits bei der Projektierung mitgewirkt hat. Außerdem haben wir im Vorfeld ein Testrohr an den Standort von eldec gesendet, damit hier experimentelle Untersuchungen mit Versuchsinduktoren und -generatoren stattfinden konnten. Auch bei der Inbetriebnahme haben uns Servicemitarbeiter unterstützt. Insgesamt passt die Philosophie von eldec zu unseren Ansprüchen: Wir brauchen Partner, die flexibel sind und individuelle Anforderungen schnell umsetzen.
1 comment
Sehr wichtige Informationen, die Sie in Ihrem Blog geteilt haben. Vielen Dank.