Wie lassen sich typische Getriebe-Massenbauteile wie Planetenräder noch effizienter produzieren? Eine passgenaue Antwort auf diese Frage gibt die EMAG Gruppe mit der Entwicklung der zweispindligen Pick-up-Drehmaschine VL 1 TWIN. Sie bearbeitet zwei gleiche Bauteile simultan in einem Arbeitsraum. Auf dieser technischen Basis eröffnen sich weitreichende Möglichkeiten: Wenn zwei Maschinen zu einer Linie verbunden werden, kann eine Bearbeitung des Planetenrads von zwei Seiten erfolgen – und das mit niedrigen Taktzeiten. Wie genau sieht die Linienlösung für Planetenräder aus?
Category:
Maschinen
Die neue HLC 150 H von EMAG KOEPFER besticht durch eine Vielzahl von Neuentwicklungen und deckt ein einzigartiges Fertigungsspektrum ab. Die horizontale Wälzfräsmaschine ist eine perfekte Allround-Lösung für Werkstücke bis Modul 3 mit einer maximalen Länge von 500 Millimetern. Es kommen dabei nicht nur alle relevanten Verzahnungstechnologien wie Wälzfräsen, Schälwälzfräsen, Schneckenfräsen und Schneckenschälen zum Einsatz. Zusätzlich ist auch das Drückentgraten bzw. Chamfern in den Arbeitsraum integriert. Somit lässt sich ein riesiges Werkstückspektrum von Getriebe- und Ankerwellen über Lenkritzel bis zum Planetenrad und Schneckenrad ohne Grat fertigstellen.
Mehr als 42 Millionen Euro hat die Pankl Gruppe in das neue „High Performance Antriebswerk“ am Standort Kapfenberg investiert, zu dem auch eine hochmoderne Getriebefertigung mit insgesamt 16 EMAG Maschinen gehört. Sie kommen bei der Weich- und Hartbearbeitung von zahlreichen Wellen und Getrieberädern zum Einsatz. Ein Gespräch mit Bernd Kögler, Werksleiter Getriebefertigung bei Pankl, und Stefan Zinner, Technischer Leiter Getriebefertigung, über die besondere Qualität des neuen Werkes, die planerische Herausforderung zu Beginn und den Einsatzbereich der Maschinen.
Bereits seit 1928 ist das Schweizer Unternehmen Humbel in der Zahnradproduktion tätig – ein Spezialist für besonders anspruchsvolle Zahnräder und Getriebekomponenten, der sich zu einem Full-Service-Anbieter entwickelt hat. Am Standort in Kradorf, rund 20 Kilometer entfernt von St. Gallen, entstehen sowohl Einzelteile als auch komplette Baugruppen. Aktuell haben die Schweizer ihren Maschinenbestand um eine Vertikaldrehmaschine VL 4 von EMAG erweitert. – Ein Gespräch mit Alex Humbel, Geschäftsführer bei Humbel Zahnräder AG in Kradolf, über Herausforderungen für Zahnradproduzenten, die Bedeutung der E-Mobilität und die Strategie im Unternehmen.
In vielerlei Hinsicht stellt die Schwerzerspanung eine besondere Herausforderung in der Produktion dar: Einerseits sind jene Bauteile, die in Nutzfahrzeugen, Schwerlastgetrieben oder der Windkraft zum Einsatz kommen, natürlich besonders groß und ihr Handling ist verhältnismäßig schwierig – schnellen Prozessen steht das im Weg. Andererseits steigen (wie in anderen Branchen auch) die technologischen Anforderungen. Produktionsplaner fordern mehr Prozesssicherheit und Präzision sowie sinkende Stückkosten. Außerdem gilt: Die großen Bauteile sollen in immer schnellerem Wechsel bearbeitet werden.
Eine erfolgreiche Messewoche auf der AMB liegt hinter uns. Laut Messe Stuttgart war es die erfolgreichste AMB aller Zeiten. An fünf Messetagen strömten zahlreiche Besucher auf unseren Messestand und informierten sich über unsere neuesten Entwicklungen. Themen wie E-Mobilität, moderne Getriebe und Digitalisierung der Fertigung standen dabei, wie auf der gesamten Messe, auch auf dem EMAG Stand im Fokus.
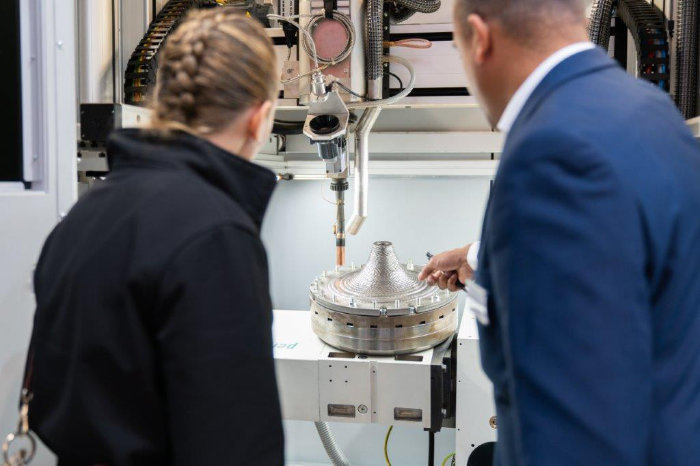
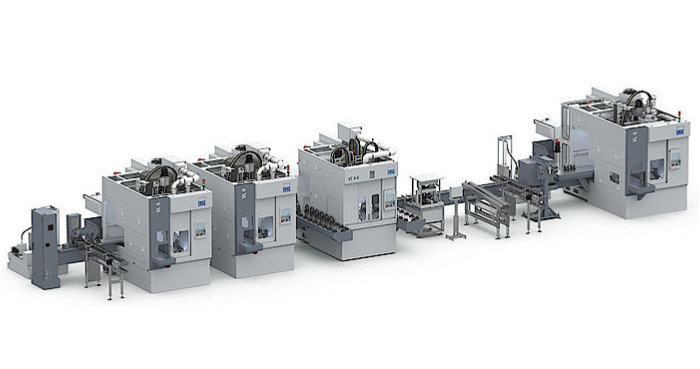
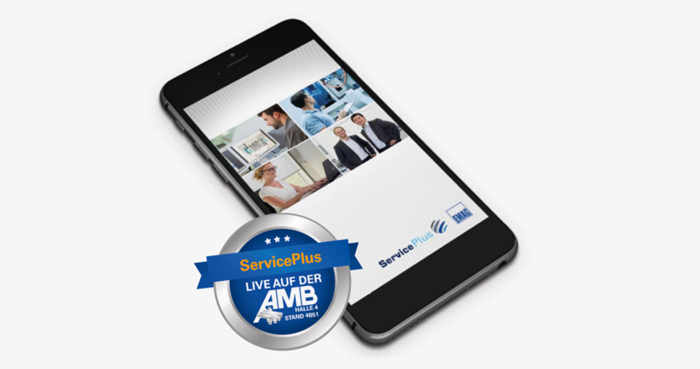
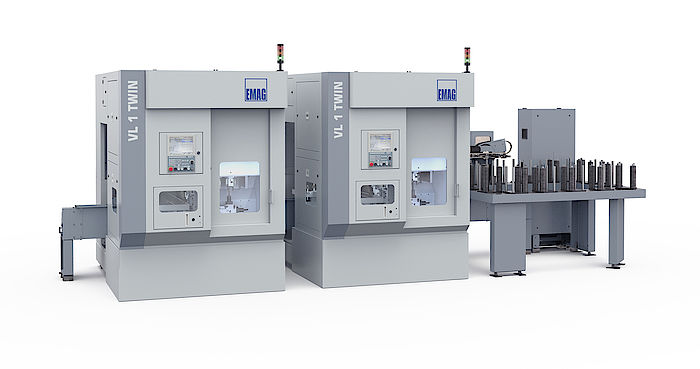
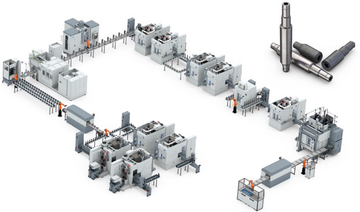
Unser Messestand auf der diesjährigen AMB steht ganz unter dem Motto „Lösungen für moderne Mobilitätskonzepte“. Auf zahlreichen Maschinen zeigen wir Anwendungen für die Fertigung von Bauteilen für die E-Mobilität wie für moderne Getriebe. Besuchen Sie uns am Stand 4B51 in Halle 4 und erleben Sie selbst, wie EMAG auch Ihre Produktion mit intelligenten Fertigungslösungen revolutionieren kann.
Genau 1.223 Innovationen haben im letzten Jahr in der Automobilindustrie das Licht der Welt erblickt – so zumindest eine Zählung des Center of Automotive Management und der Beratungsgesellschaft PwC. Rund 27 Prozent dieser Innovationen entstammen demnach dem Bereich der Sicherheits- und Fahrerassistenz-Systeme, jede fünfte gehört zum Motorenbereich. Mit Blick auf die dazugehörige Automotive-Produktion setzt sich dabei eine Entwicklung fort, die seit Jahren anhält: Die Branche ist einem immer schnelleren Wandel unterworfen, der mit der Forderung nach einer hochflexiblen Produktion einhergeht. Anders gesagt: Neue Bauteile und Komponenten müssen sich mit den bestehenden Produktionslösungen effizient und vollkommen fehlerfrei produzieren lassen.
Die BLISK-Stückzahlen (Blade Integrated Disk) im Flugzeugbau steigen massiv an. Große Triebwerke verfügen mittlerweile über mehrere dieser Hochdruckverdichter, die in einem Stück aus superharten Hochleistungswerkstoffen gefertigt werden. Folglich rückt derzeit ihre effiziente Bearbeitung in den Fokus der Produktionsplaner – allerdings steht eine Vielzahl von denkbaren Verfahren und Verfahrenskombinationen von der spanenden Bearbeitung bis zum Wasserstrahlschneiden zur Verfügung. Eine aktuelle Studie des Fraunhofer-Instituts für Produktionstechnologie (IPT) und des Werkzeugmaschinenlabors (WZL) der RWTH Aachen zeigt jetzt: Gerade beim Schlichten der Bauteiloberfläche führt das Precise Electro Chemical Machining (PECM) von EMAG zu enormen Kostenvorteilen beim Anwender.
Dass die Nachfrage nach kundenspezifischen System- und Integrationslösungen weiter steigt, prognostizierte bereits im Jahr 2014 eine Umfrage unter deutschen Maschinen- und Anlagenbauern im Rahmen der Studie „Zukunftsperspektive deutscher Maschinenbau“. Angesichts des Megatrends „Industrie 4.0“ ist das wenig überraschend. Schließlich ist die weitgehende Automatisierung per kundenspezifischer Systemlösung eine Grundbedingung für die Digitalisierung des Produktionsstandorts. Anschließend bilden die eingesetzten Maschinen ein ganzheitliches System, das Produktionsplaner von zentraler Stelle aus steuern. Zudem gilt: Viele Unternehmen müssen immer schneller und flexibler auf die technologische Entwicklung reagieren. Eine große Zahl von Teilevarianten und wechselnde Stückzahlen prägen mittelständische Produktionsunternehmen im Automobilbau.