Die BLISK-Stückzahlen (Blade Integrated Disk) im Flugzeugbau steigen massiv an. Große Triebwerke verfügen mittlerweile über mehrere dieser Hochdruckverdichter, die in einem Stück aus superharten Hochleistungswerkstoffen gefertigt werden. Folglich rückt derzeit ihre effiziente Bearbeitung in den Fokus der Produktionsplaner – allerdings steht eine Vielzahl von denkbaren Verfahren und Verfahrenskombinationen von der spanenden Bearbeitung bis zum Wasserstrahlschneiden zur Verfügung. Eine aktuelle Studie des Fraunhofer-Instituts für Produktionstechnologie (IPT) und des Werkzeugmaschinenlabors (WZL) der RWTH Aachen zeigt jetzt: Gerade beim Schlichten der Bauteiloberfläche führt das Precise Electro Chemical Machining (PECM) von EMAG zu enormen Kostenvorteilen beim Anwender.
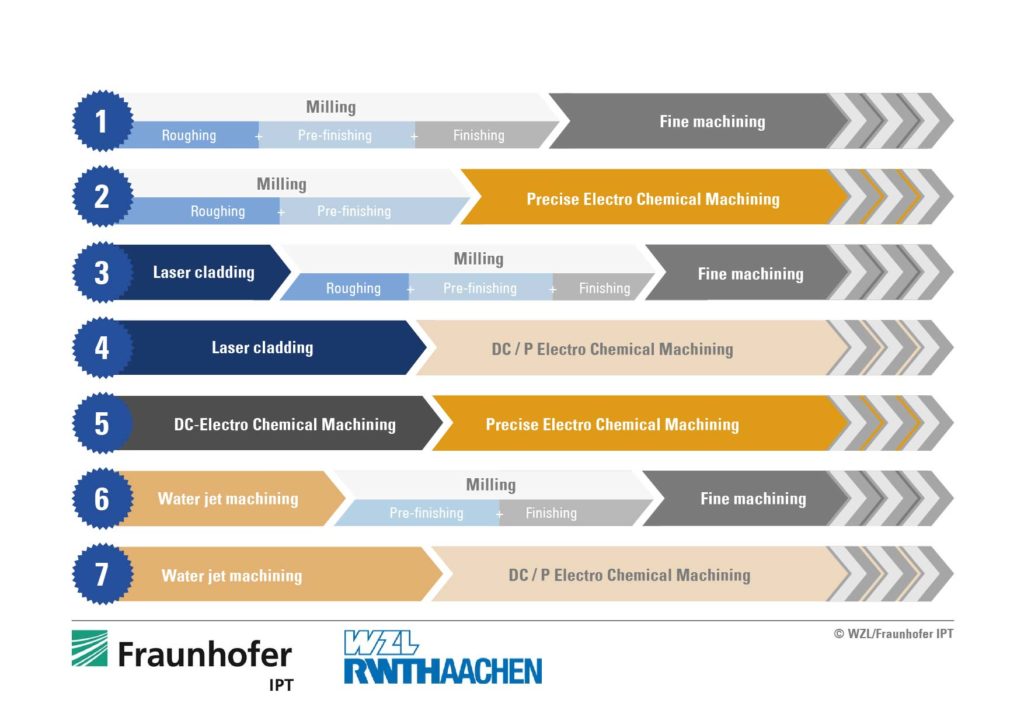
Sieben verschiedene Bearbeitungskombinationen kamen in der Studie von Fraunhofer IPT und dem WZL der RWTH Aachen zum Einsatz. Die komplett spanende Bearbeitung diente dabei als Benchmark.
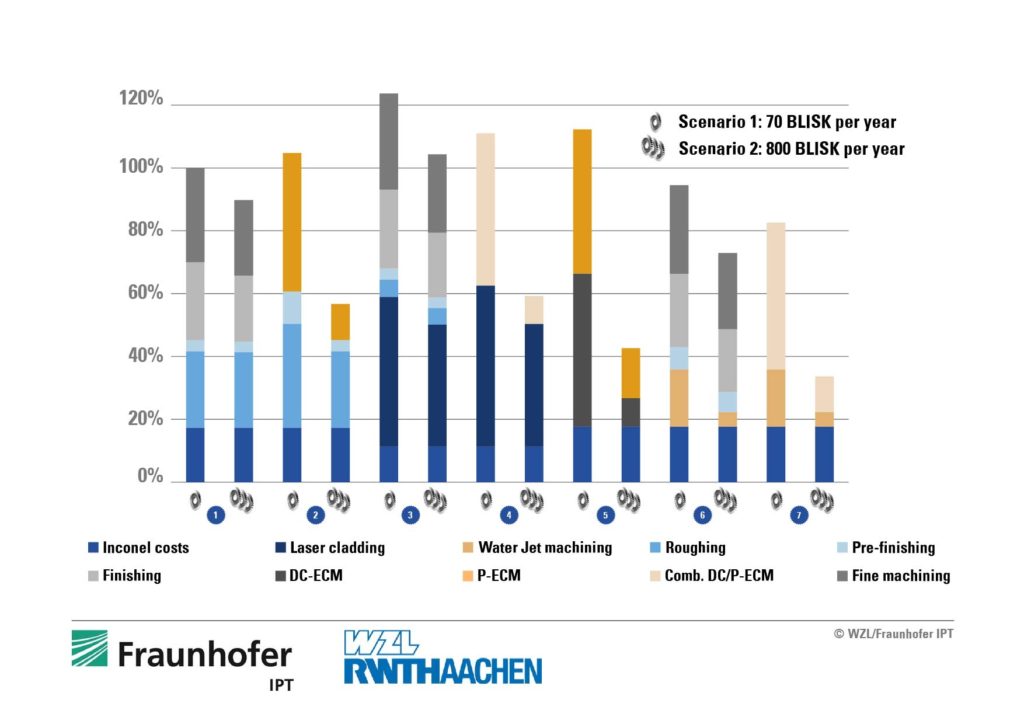
Hier betragen die Kosten bei einer angenommenen Stückzahl von 70 BLISKs pro Jahr 100 Prozent, bei 800 Stück rund 90 Prozent (ganz links). Bereits in der Bearbeitungskombination Nummer 2 (Schruppfräsen und PECM) sinken die Kosten auf unter 60 Prozent ab. Quelle: Fraunhofer IPT/WZL
Hohe Temperaturen, lange Laufzeiten – die Bauteile im Inneren eines Triebwerks werden extrem belastet. Entwickler setzen deshalb bei der Konstruktion der Blade Integrated Disk (BLISK) und bei Disks mit Einzelschaufeln auf sehr harte und hitzebeständige Werkstoffe wie Superlegierungen aus Nickel. Für Produktionsplaner ist diese Entwicklung nicht unproblematisch, denn die etablierte spanende Bearbeitung stößt an wirtschaftliche Grenzen – zum Beispiel, weil mit zunehmender Werkstoffhärte die Standzeit der teuren Werkzeuge sinkt und die Stückkosten somit ansteigen. Vor diesem Hintergrund sind die aktuellen Ergebnisse einer Studie des Fraunhofer IPT besonders interessant. Gemeinsam mit dem WZL und der EMAG ECM GmbH verglichen die Spezialisten insgesamt sieben verschiedene BLISK-Bearbeitungsstrategien – vom mehrachsigen Fräsen, kombiniert mit dem Polieren, bis hin zum Hochdruck-Wasserstrahlschneiden, kombiniert mit dem PECM-Schlichten. Die Ergebnisse sind beeindruckend: Bei einer angenommenen Jahresproduktion von 800 nickelbasierten HPC-BLISKs können die Stückkosten im Vergleich zur spanenden Bearbeitung um mehr als 50 Prozent absinken, wenn Anwender auf die richtige Bearbeitungsstrategie setzen. Das PECM-Schlichten ist dabei als abschließender Prozess unverzichtbar (siehe Infografik), um die Effizienz der Produktion deutlich zu verbessern.
Sanfter Abtrag – schnelle Prozesse
Vor diesem Hintergrund rückt die PECM-Technologie der EMAG ECM mit Sitz in Gaildorf derzeit bei vielen OEMs und deren Zulieferunternehmen in den Fokus. Das elektrochemische Verfahren sorgt für einen besonders sanften Abtrag von Werkstoff bei minimalem Werkzeugverschleiß. Zudem ist es schnell und prozesssicher. Das Grundprinzip lässt sich einfach erklären: Während des Prozesses wird das Werkstück zur positiven Anode, das Werkzeug zur negativen Kathode. Zwischen beiden fließt eine Elektrolytlösung, und es lösen sich Metall-Ionen vom Werkstück ab. Die Form der Kathode bzw. des Werkzeugs mit den aktiven, stromleitenden Bereichen ist so gewählt, dass der Materialabtrag am Werkstück zur gewünschten Bauteilkontur führt. Berührungslos entstehen Konturen, Ringkanäle, Nuten oder Auskesselungen – und das mit höchster Präzision und Oberflächenqualität. Mit ihrer PECM-Technologie haben die Experten von EMAG ECM dieses Verfahren gezielt weiterentwickelt und perfektioniert. Zwei Faktoren spielen dabei eine entscheidende Rolle: Erstens ist der Spalt zwischen Werkstück und Werkzeug, durch den die Elektrolytlösung fließt, besonders schmal. Zweitens ist die Versorgung mit Elektrolytlösung durch eine mechanische Oszillationsbewegung optimiert. Beide Faktoren zusammen sorgen für ein noch effektiveres und genaueres Abtragen des Werkstoffes.
Von einzelnen Turbinenschaufeln bis zum BLISK
Für unterschiedliche Bearbeitungsaufgaben im Triebwerksbau verfügt EMAG ECM über zwei Maschinentypen: Während das kleinere Modell PO 100 SF für die Bearbeitung von einzelnen Turbinenschaufeln ausgelegt ist, dient die größere Maschine PO 900 BF für die Bearbeitung der kompletten (und damit viel größeren) BLISK. Folglich unterscheiden sich die Maschinen mit Blick auf die Größe des Arbeitsraums, des Footprints, der Generatorenleistung und der Zahl der Bearbeitungsachsen – präzise PECM-Technologie und EMAG-Hochleistungskomponenten stehen freilich in beiden Fällen zur Verfügung. „Mit der PO 900 BF sind wir im Jahr 2011 mit Blick auf die BLISK-Fertigung an den Markt gegangen. Die PO 100 SF-Entwicklung erfolgte in einem zweiten Schritt im Jahr 2013, als ein immer größer werdender Kundenkreis nach einer elektrochemischen Maschinenlösung für die Einzelschaufel verlangt hat. Jetzt verfügen wir über eine ideale Basis, um passgenaue und kostengünstige Produktionslösungen für kleine und große Triebwerksbauteile zu entwickeln“, so Richard Keller, Mitglied der Geschäftsleitung bei der EMAG ECM GmbH. Bei beiden Maschinentypen profitieren die Anwender zudem von zentralen EMAG-Innovationen wie Mineralit-Maschinengrundkörper, intelligente Soft- und Hardware-Schnittstellen oder effizienten Automationslösungen.
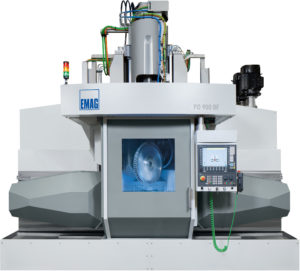
Blisk-Bearbeitungsmaschine PO 900 BF
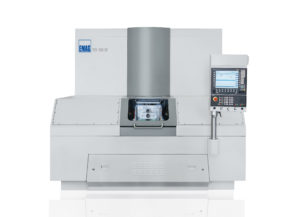
Das kleinere Modell PO 100 SF ist für die Bearbeitung von einzelnen Turbinenschaufeln ausgelegt.
Bauteile für Praxiseinsatz zertifiziert
In der Praxis führt dieser Ansatz aktuell Schritt für Schritt zu den erhofften Erfolgen. Beispielsweise hat ein renommierter Triebwerkshersteller die auf einer PO 100 SF gefertigte Einzelschaufel bereits 2014 für den Einsatz im Flugzeug zertifiziert – ungewöhnlich schnell nach dem Produktionsstart der Maschine bei einem Zulieferunternehmen. Ein ähnlicher Schritt steht derzeit auch in der BLISK-Fertigung an. Verschiedene Unternehmen der Triebwerkstechnik befinden sich mit ihren Bauteilen in der Qualifizierungsphase für den Praxiseinsatz. „Die Technologie ist derzeit in vielen Testprogrammen in der Validierungsphase“, fasst Keller die aktuelle Arbeit von EMAG ECM zusammen. „Die langfristige, strategische Ausrichtung auf diese Bauteile und Anwendungstechnik trägt Früchte und wird mit jeder weiteren Zertifizierung von PECM-gefertigten Bauteilen den Verkaufserfolg einspielen.“
Ein entscheidender Erfolgsfaktor ist dabei nicht zuletzt die geometrische Bearbeitungsgenauigkeit. Zudem entstehen hohe Oberflächenqualitäten mit niedrigem Rauigkeitswert. Nachfolgende Veredelungsprozesse an den Schaufeln, wie zum Beispiel das Gleitschleifen, können deshalb entfallen oder sie laufen deutlich verkürzt ab – im Endeffekt ist beides gleichbedeutend mit einer weiteren Senkung der Stückkosten. Bei einem Bauteil, das immer wichtiger wird und dessen Stückzahlen massiv ansteigen, ist das ein herausragendes Argument.
Mehr zur ECM-Technologie finden Sie hier: http://www.emag.com/de/technologien/ecm.html