The VLC GT series is one of the most successful new product developments for EMAG in recent years. The combination of the proven pick-up automation system, vertical machining operation and the option of using different technologies for hard machining in the spacious machining area, has made some fantastic production solutions possible.
With the VLC 350 GT, the next biggest expansion stage is being launched. We spoke to Marina Manger, assistant team leader of the TPM-1 application team, about the new machine and the ideas its development was based on.
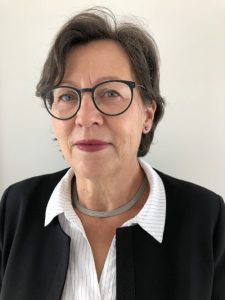
We spoke to Marina Manger, team leader of the TPM-1 application team about the new machine and how it was developed.
Ms. Manger, the predecessor to the VLC 350 GT, the VLC 200 GT, was very well received in the market. Why do you believe this was?
This machine was simply perfect. Our decades of experience in hard machining was shown in this series – we know what our customers need and have continuously developed our technology – both with regard to the engineering itself, as well as to the use of machining technologies, such as grinding and hard turning. The VLC 200 GT then evolved from all this past experience.
What does this mean exactly?
There is the pick-up automation system that is featured on many EMAG machines. This means that the machine is already automated, with a clamping device that is aligned to the respective workpiece. This completely eliminates clamping operation errors. Added to this is the spacious machining area that can be flexibly configured. Outer and inner grinding spindles can be installed and block tool holders, and of course, the EMAG turret are part of the repertoire too. This enables optimal process combinations to be developed, minimizing machining times considerably. Greatly reducing the overly component costs.
I assume that the VLC 350 GT still incorporates these elements. What additional innovations will be included?
Yes, we will of course continue to use these elements, but now they are incorporated into a bigger machine. As the name suggests, the VLC 350 GT is designed for components up to 350 mm (14 in) in diameter. This means that the entire machining area has gotten bigger, with corresponding X- and Z- stroke. Consequently, we also use a linear motor in the machine’s X-axis, so that the components can be transported quickly. The biggest innovation, however, is the option of using a B-axis under the inner grinding spindle. This makes it possible to grind not just cylinders, but also tapers, in one clamping operation. This offers great flexibility in the machining range of the machine, so that part families can be machined with very little tooling effort.
On the subject of tooling, we have not yet spoken about the machine’s accessibility. What was the feedback like here?
Very positive, both from our own employees, who set up the machine, and from customers. The machining area is large enough that all tools, as well as the spindle and clamping device, can be reached easily. This leads to quick tooling times, and satisfied machine setters.
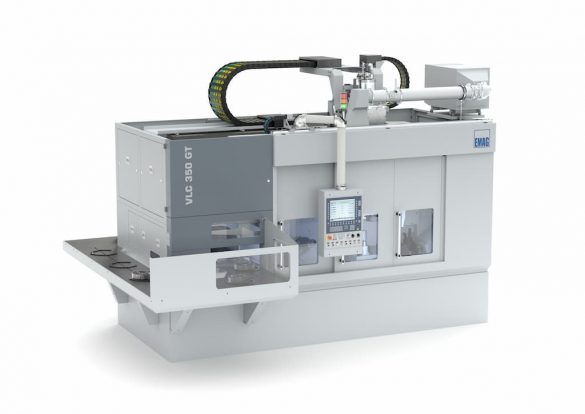
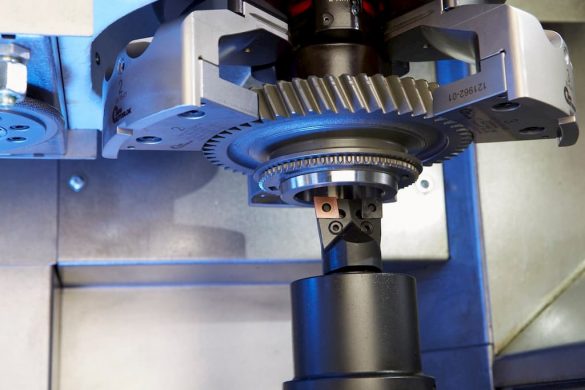
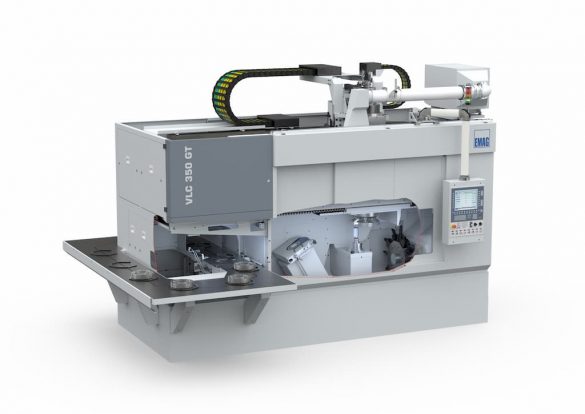
What additional advantages does the size of the machining area offer?
The large machining area expands the machining possibilities that we can implement in one clamping operation. In one case, for example, we were able to completely hard-machine a flange part. In other words, the end faces were turned to finish quality and the cylindrical and tapered inner contours were pre-turned. These contours were then ground by means of the inner grinding spindle mounted on the B-axis. Even the synchronizing taper on the outside could be ground with the inner grinding element under certain circumstances. In this case, however, we used the external grinding spindle for this. This system allows the customer to achieve a variety of technological possibilities.
Are there any other advantages of such a machining scenario?
On conventional grinding machines, end faces have to be ground, although surface and tolerance requirements can often be produced by hard turning. This frequently results in long cycle times. Hard turning has clear advantages here, as internal end faces in particular often complicate the necessary use of cooling lubricant. This frequently results in overheating.
To avoid these technological limits, EMAG consistently relies on combination machining. Where possible, pre-turning and turning to finish quality take place. Grinding is performed where necessary. The process that makes the most technological sense can always be used. By using the dressing spindle, it is possible to work with both CBN and corundum grinding elements.
The customer can react to changing technical requirements without any problems.
That really sounds like a well thought-out product. Who do you consider as the main target group for this machine?
The machine has a high power capacity so we recommend it for middle to large-scale production. Its high flexibility makes the machine interesting for customers who produce lower volumes.
The integrated automation system makes it possible to run the VLC 350 GT as a standalone machine. In this case, the circulating belt is an inexpensive way to store parts, which is a good option when it comes to small batch sizes. The machine can also be easily integrated into production lines.
There are a variety of possibilities, and with the common parts strategy we can use standard components. This allows us to achieve an excellent price-performance ratio. Just reach out to us, then we can work together to determine if the VLC GT series is the appropriate solution for you.
Ms. Manger, thank you very much for talking to us.
More information about the VLC 350 GT can be found here…