Wer seine Maschinen regelmäßig wartet, verhindert viele ungeplante Stillstände und verbessert somit die gesamte Produktionssicherheit seines Standorts. Nichtsdestotrotz lassen viele Anwender ihre Maschinen immer noch so lange laufen, bis gravierende Schäden auftreten – ohne vorher jemals einen umfassenden Check durchzuführen. Auf was kommt es bei Wartung und Inspektion genau an und was für Möglichkeiten eröffnet IoT-Technologie in diesem Zusammenhang? Ein Gespräch mit Patrick Theiss, Leiter Business Unit After Sales / Service bei der EMAG.
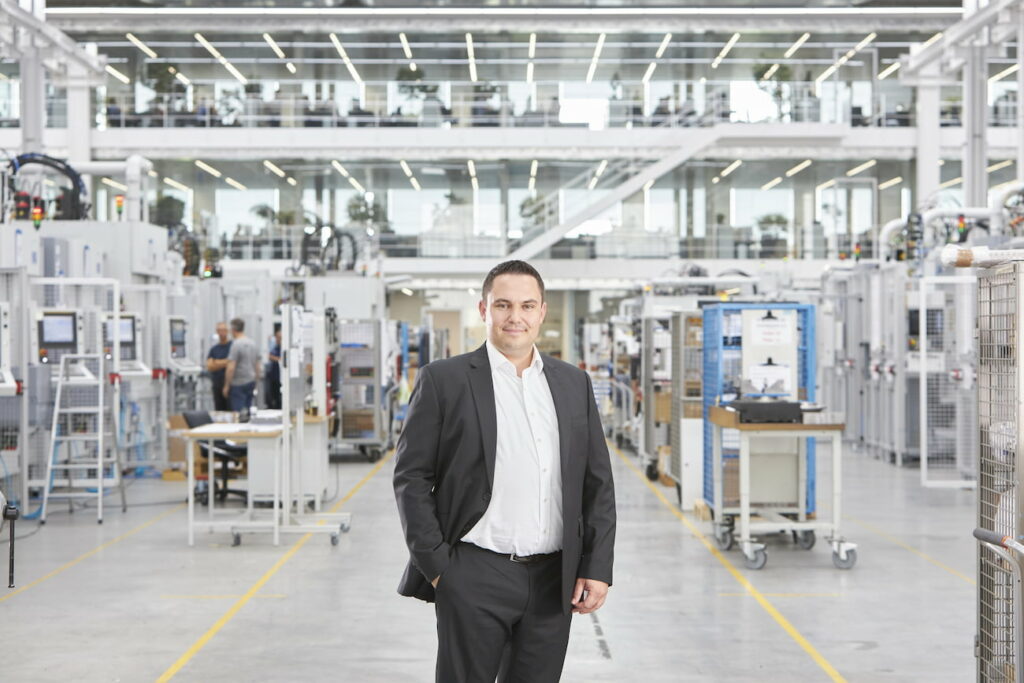
Patrick Theiss, Leiter Business Unit After Sales / Service bei der EMAG
Herr Theiss, was für eine Bedeutung haben Inspektion und Wartung ganz allgemein im Maschinenbau?
Eine sehr große Bedeutung! Eigentlich liegt das auch auf der Hand, denn eine moderne Werkzeugmaschine ist eine komplexe Technologie mit vielen beweglichen Elementen und perfekt angepassten Software-Lösungen. Zudem treten große Kräfte auf und das Ganze kommt nicht selten in einer rauen Umgebung mit Staub und Qualm zum Einsatz. Zudem sorgen Wartungen allgemein für effizientere Produktionsprozesse mit gleichbleibender Produktionsqualität. Folglich macht es sehr viel Sinn, die Maschinen regelmäßig durchzuchecken und verschlissene Kleinteile auszutauschen. Sie lassen an ihrem Auto ja auch regelmäßig die Bremsen erneuern und fahren nicht immer weiter, bis es zu einem Unfall kommt.
Können Sie uns ein Beispiel für die Wirksamkeit von Wartungen und Inspektionen bei Kunden geben?
Nehmen wir einen süddeutschen Kunden aus dem Bereich Landmaschinen- und Fahrzeugbau. Hier führen wir jährlich eine vorgelagerte Inspektion mit anschließender Wartung durch – und zwar an insgesamt 18 Maschinen des Typs VSC/VT. Dazu muss man wissen, dass es hier um Gussbearbeitung an Getriebeteilen im Vierschicht-Betrieb geht. Die Maschinen werden also stark beansprucht. Nichtsdestotrotz ist es uns gelungen, ungeplante Stillstände drastisch zu senken. Es werden im Schnitt nur noch zwei bis drei pro Jahr gemeldet – und das im gesamten Maschinenpark! In der Folge konnten wir die laufenden Instandhaltungskosten durch gezielte Wartungen um bis zu 30 Prozent senken.
Warum gibt es trotzdem Anwender, die ihre Maschinen nie warten oder checken lassen?
Zunächst einmal ist das auch ein indirektes Lob für EMAG. Viele Anwender haben einfach die Erfahrung gemacht, dass unsere Lösungen sehr stabil sind und mitunter viele Jahre lang ohne größere Probleme ihren Dienst verrichten. Dann entsteht schnell der Eindruck, dass Wartungen oder Inspektionen gar nicht nötig sind. Aber letztlich ist das natürlich ein Trugschluss. Wir können nicht die physikalischen Gesetze außer Kraft setzen – Reibungshitze und Vibrationen führen mit der Zeit zu kleineren Schäden, die man in der Regel mit kleinem Serviceaufwand schnell beseitigen kann.
Aber könnte man diese Schäden nicht einfach immer dann beheben, wenn die Maschine einmal zum ungeplanten Stillstand kommt?
Das Problem ist, dass in diesen Fällen der Schaden häufig schon viel größer ist. Man muss also beispielsweise den kompletten Revolver und andere hochwertige Komponenten der Maschine austauschen, die leicht einen Wert von mehreren Zehntausend Euro haben – und genau das könnte man durch den einfachen Tausch von sehr günstigen Dichtungen oder der Zustandsprüfung bestimmter Füllstoffe zu einem früheren Zeitpunkt leicht verhindern. Im Übrigen führen wir unsere Wartungen und Inspektionen natürlich zu optimalen Zeitpunkten durch – also etwa dann, wenn die Produktion ohnehin still steht. Zudem geht es schnell, weil wir die sensiblen Details genau kennen. Die Stillstandszeit ist also denkbar minimal. Hingegen kann der Stillstand wegen eines technischen Schadens im schlimmsten Fall mehrere Wochen lang andauern – und das ungeplant. Man müsste also eigentlich produzieren und kann es nicht. Das treibt die Kosten zusätzlich in die Höhe.
Was für eine Bedeutung hat die Wartung mit Blick auf die Produktionsqualität?
Wenn Sie keine regelmäßige Wartung oder Inspektion durchführen, können sich wichtige Parameter der Maschine verstellen oder zentrale Bauteile abnutzen. Darunter leidet natürlich die Produktionsqualität. Das Thema ist also auch in diesem Themenfeld wichtig.
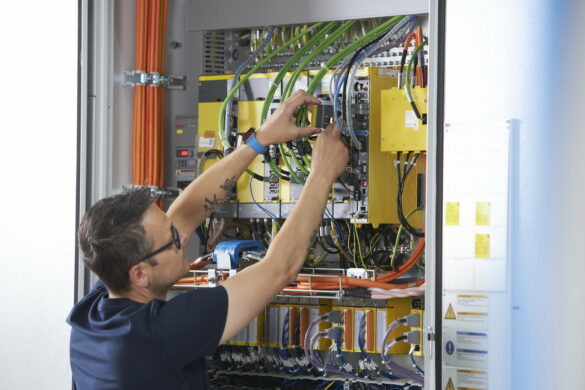
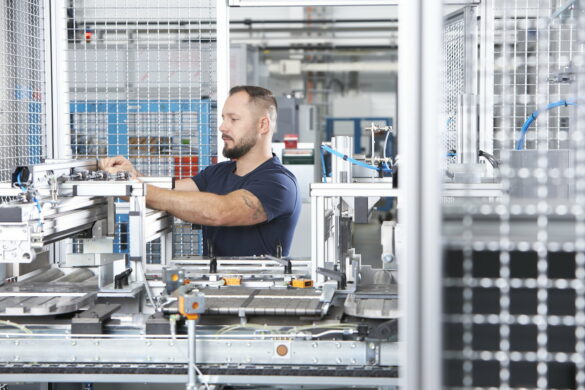
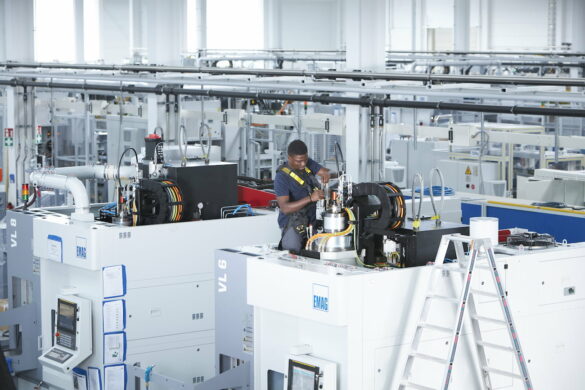
Wie kann man sich die Gestaltung eines Wartungs- oder Inspektionsvertrags vorstellen?
Wir definieren gemeinsam mit den Kunden sehr präzise, was wir machen, und behalten dabei die Kosteneffizienz immer im Blick. Es geht um viele Fragen – von der Laufzeit des Wartungsvertrags über den Umfang der Prüfungen bis zum geplanten Austausch von Wartungsteilen. Die Zielsetzung lautet immer: maximale Transparenz. Anschließend profitieren Anwender von sehr viel Erfahrungswissen: Unsere Servicetechniker kennen „ihre“ Technologie – von der Verfahr- und Wiederholgenauigkeit der NC-Achsen über die Schwenkgenauigkeit des Werkzeugträgers bis zur Leichtgängigkeit der Spannfutter und der Geometrie der gesamten Maschine.
Was für eine Rolle spielt das jeweilige Einsatzszenario der Maschine?
Das fließt natürlich in die Wartungsplanung mit ein, denn es treten ja zum Beispiel unterschiedlich hohe Bearbeitungskräfte auf und die Maschinen sind unterschiedlich lange pro Jahr bei den Kunden im Einsatz. Allerdings kennen wir immer vergleichbare Anwendungen und schlagen auf dieser Basis zielgenaue Wartungszyklen und -strategien vor.
Kann man seine Maschine auch in einem kleinen Rahmen nur prüfen lassen?
Natürlich, dafür bieten wir verschiedene Inspektions-Pakete an. Es gibt zum Beispiel den Quick-Check für eine optische und mechanische Prüfung der Maschine. Die Ergebnisse geben Aufschluss über die wesentlichen Komponenten. Im Rahmen des etwas ausführlicheren Fitness-Checks kommt eine vordefinierte Checkliste zum Einsatz. Anschließend kann man gegebenenfalls Reparaturen und Instandhaltungsmaßnahmen einleiten.
Wie wichtig ist im Kontext von Wartung und Inspektion das Thema „IoT“?
Das Thema ist sehr wichtig – wir haben immer mehr Kunden, die auf unser umfangreiches EDNA-System zurückgreifen, weil es mit einem datenbasierten Health Check für sinkende Kosten sorgt. Basis der Lösung ist der EDNA IoT-Core – ein Industrie-PC, der an die Steuerung der Maschine angeschlossen wird und mit Hilfe der Software „EDNA Cortex“ Fertigungs- und Sensordaten empfängt und aufzeichnet. Für den Health Check erfolgen nun regelmäßige Vibrationsmessungen per Sensor. Dabei fährt das Messprogramm verschiedene Achsen und Komponenten in der Maschine ab und ermittelt ihre Schwingungsdaten. Sie werden in der EDNA Cloud verarbeitet und per KI analysiert. Insgesamt ist das KI-Modell so gut trainiert, dass es für den Gesundheitszustand der Maschine einen Trend bestimmen kann.
Was für einen wirtschaftlichen Effekt hat dieser Ansatz?
In der Praxis führt das System zu erstaunlichen Kostenvorteilen, wie aktuelle Anwendungsbeispiele von EMAG deutlich machen. Es lässt sich ein Großteil der ungeplanten Stillstände erkennen und die Wartezeiten für Ersatzteile und Servicetechniker gehen radikal zurück – zum Beispiel, weil Ersatzteile frühzeitig vorliegen und der Serviceeinsatz ebenso frühzeitig geplant wird. Auf dieser Basis erreicht man eine Produktivitätssteigerung von rund drei Prozent.
Wie würden Sie abschließend die Bedeutung von Wartung in der Zukunft beurteilen?
Wir sind überzeugt davon, dass die Bedeutung des Services im Maschinenbau in den nächsten Jahren weiter zunehmen wird. Höhere Anforderungen an Bauteilqualität und Just-in-Time-Produktionsprozesse geben hier die Richtung vor. In diesem Kontext sind wir mit unserem Angebot optimal aufgestellt.