Geht es um die Präzision in der Elektrochemischen Metallbearbeitung, spielt die verwendete Werkzeugkathode eine besondere Rolle: Ihre Form gibt den Materialabtrag am Bauteil vor – folglich ist ihre Konstruktion und präzise Produktion eine enorm wichtige Bearbeitungsaufgabe im Mikrometerbereich. Für ihre Entwicklung verfügt EMAG ECM deshalb über einen umfangreichen Entwicklungsbereich mit weitgehend digitalem Workflow.
In drei Schritten zum BLISK-Werkzeug
Aktuell vollziehen die Spezialisten mit Sitz in Gaildorf bei Schwäbisch Hall in diesem Zusammenhang einen wichtigen Schritt: Die Berechnung der Kathodenform für BLISK, DISK, Diffusor und Co. erfolgt zukünftig mithilfe der eigenentwickelten Software „EMAG Tool Designer“. Der Werkzeugbau vollzieht sich somit zukünftig in drei Schritten: Zunächst erfolgt mithilfe des „EMAG Tool Designers“ eine erste Vorausberechnung (IT0) der Kathode anhand der 3-D-Geometriedaten des Bauteils. Nach der Fertigstellung der Kathode startet ein erster Bearbeitungsprozess in der PECM-Maschine. Anschließend erfolgt eine optische 3-D-Vermessung am fertigen Bauteil. Die Messergebnisse fließen erneut in den „Tool Designer“ ein. Das Programm errechnet die notwendigen Korrekturen an der Kathode.
Präzision für den Turbinenbau
Das korrigierte Werkzeug wird dann erneut getestet bzw. das fertige Bauteil vermessen, Wenn die Werte stimmen, ist der Entwicklungsprozess abgeschlossen. Am Ende stellen die Spezialisten ihren Kunden immer ein hochpräzises Werkzeug zur Verfügung – Grundbedingung für genaue Produktionsprozesse während des PECM-Verfahrens im Turbinenbau.
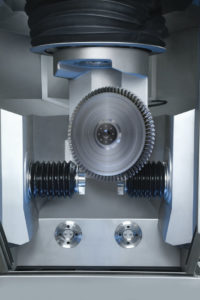
PECM im Turbinenbau
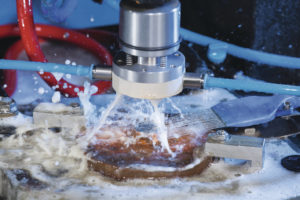
PECM im Turbinenbau
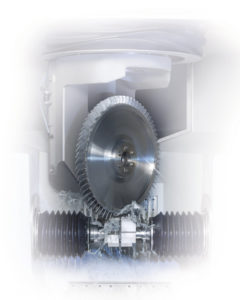
PECM im Turbinenbau
PECM im Turbinenbau