Die Rotorwelle in einer vollautomatisierten Linie fertigstellen
EMAG konzipiert und konstruiert komplette Produktionslinien für einteilige oder zweiteilige Rotorwellen, in denen alle Bearbeitungsprozesse perfekt verzahnt hintereinander ablaufen. Technologie, Automatisierung und Prozessentwicklung kommen dabei aus einer Hand – ideale Lösungen für die schnell steigenden Stückzahlen im Bereich der Elektromobilität.
"One face to the customer"
Die Zusammenarbeit beginnt oft in einer frühen Phase: Kunden können im Vorfeld die Konstruktionszeichnungen des Bauteils mit EMAG abklären, um einen möglichst schlanken und sicheren Produktionsprozess zu ermöglichen. Am Ende verfügen die Unternehmen über ein perfektes Produktionssystem, das mit Blick auf die Taktzeiten Benchmarks setzt, gleichzeitig aber eine hohe Stabilität und Produktionssicherheit aufweist.
Dabei gilt immer das Prinzip „One Face to the Customer“: Ein erfahrener Ansprechpartner bei EMAG bespricht die Anforderungen der gesamten Produktionslösung mit dem Kunden – dazu gehören beispielsweise auch die Maschinen, die nicht von EMAG stammen, aber zur kompletten Prozesskette gehören. EMAG kümmert sich um jede einzelne Komponente der Fertigungslösung und definiert ihre Spezifikationen. Und das heißt: Kunden sparen sehr viel Kapazität in der Angebotsphase – und haben einen zentralen Ansprechpartner in der späteren Auftragsabwicklung.
Lösungsbeispiel für zweiteilige Rotorwelle
Im Endergebnis zeigen sich beeindruckende Prozesse – wie beispielsweise in der nachfolgenden, komplett automatisierten Produktionslinie für eine zweiteilige Rotorwelle. Ihre Produktionsleistung beträgt rund 360.000 Bauteile pro Jahr. Insgesamt vollziehen sich acht Operationen, die komplett von EMAG Maschinen realisiert werden. Die Automatisierung und Verkettung der einzelnen Maschinen und Stationen erfolgt mit Robotern, Ladeportalen und Palettenbändern sowie dem EMAG eigenen TrackMotion-System.
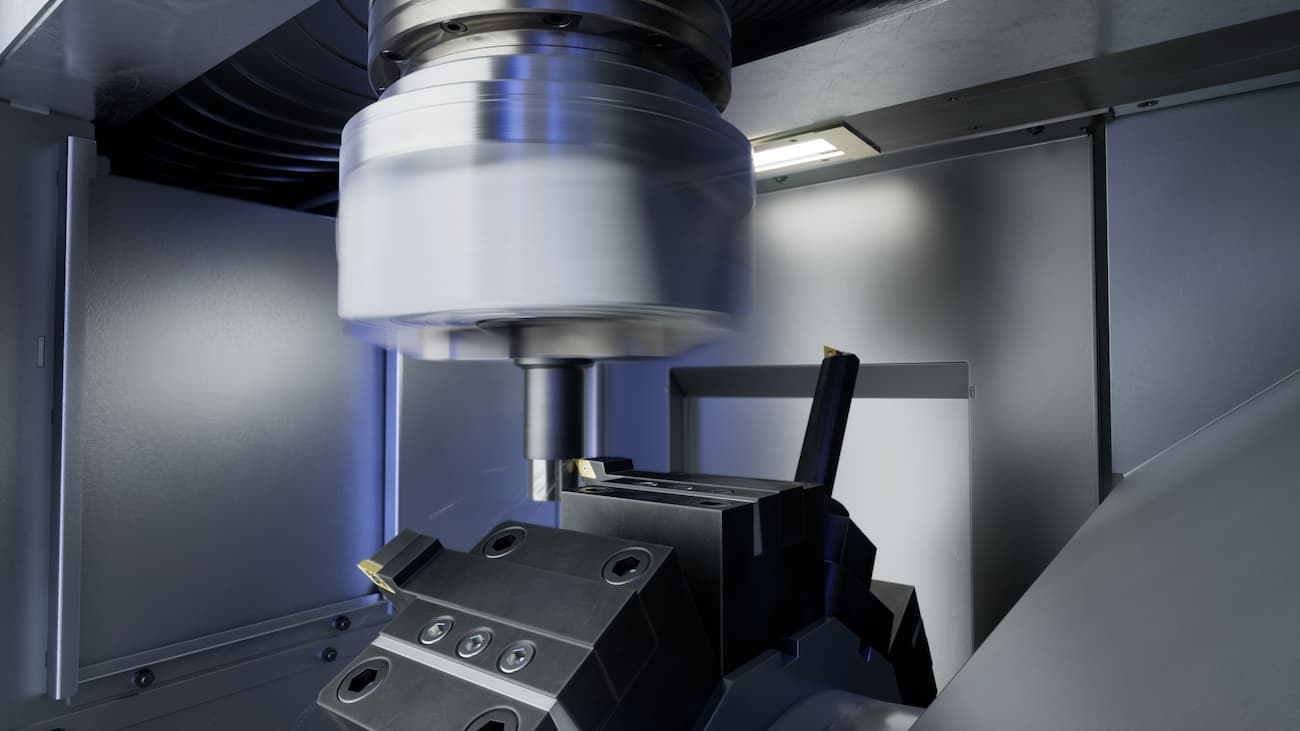
OP 10/OP 20: Drehen der Endstücke der Rotorwelle
Nach der Rohteilzuführung startet das Vordrehen der beiden Endstücke auf insgesamt vier VLC 200 Maschinen von EMAG (OP 10 und OP 20). Jedes Bauteil durchläuft dabei zwei Maschinen – nach der Bearbeitung der ersten Seite wird es durch das eingesetzte EMAG TrackMotion gewendet. Dann startet der Drehprozess an der zweiten Seite.
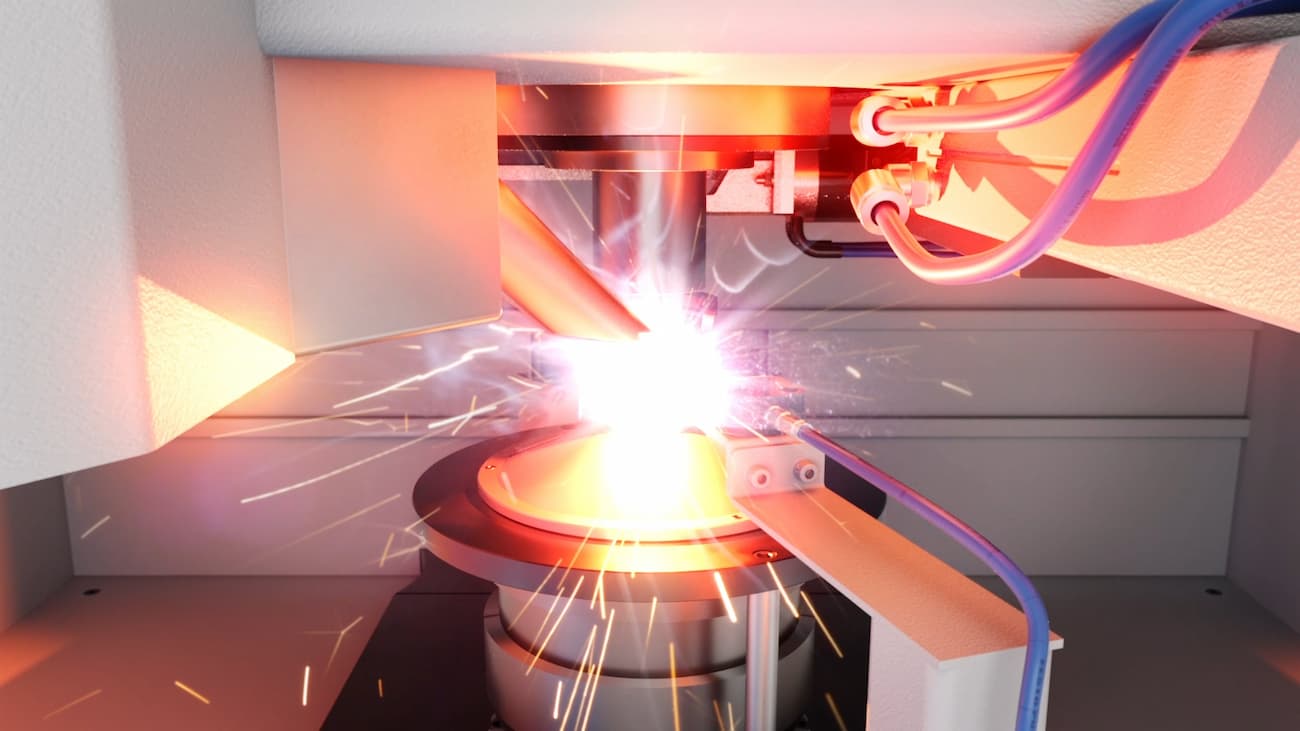
OP 30: Laserreinigen & Laserschweißen
Anschließend erfolgt in OP 30 zunächst das Laserreinigen der Fügenaht.
Nach dem Laserreinigen werden die beiden Endstücke (Flansch und Rohr) über ein Ladeportal der Laserschweißmaschine ELC 6 von EMAG LaserTec zugeführt. Hier werden die Teile zunächst gefügt und dann verschweißt (OP40).
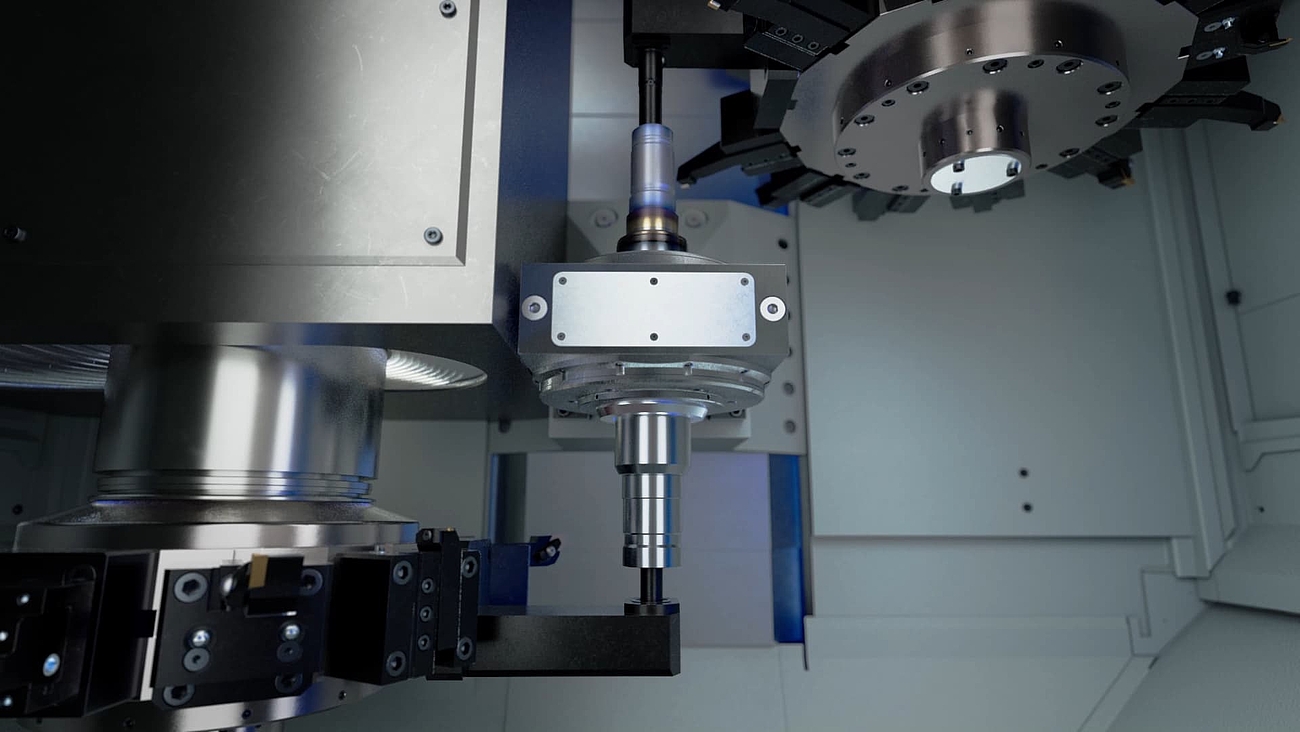
OP 50: Hartdrehen der Rotorwelle
Beim anschließenden Hartdrehen (OP 50) in einer VTC 200 CD (Mittenantrieb) werden Zentrierungen an der Welle fertiggestellt.
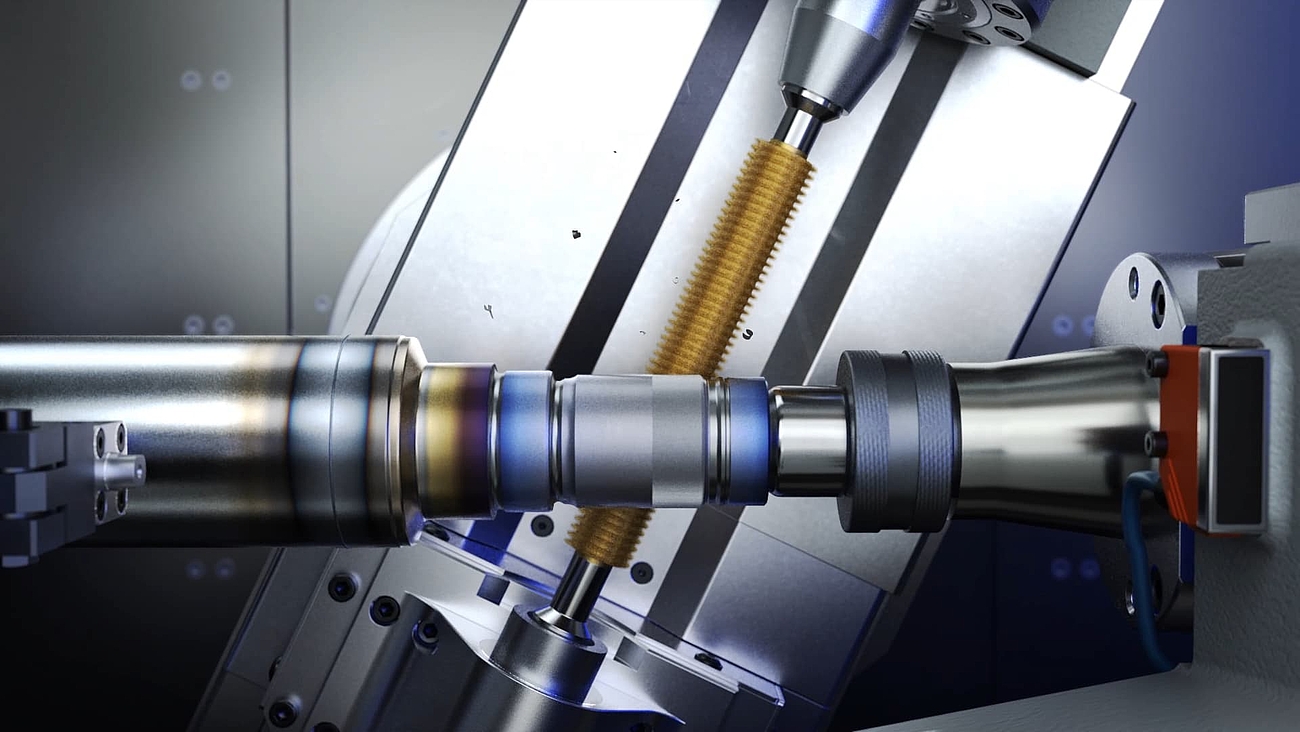
OP 60: Verzahnen
In OP 60 wird mithilfe der Wälzfräsmaschine HLC 150 H von EMAG Koepfer eine Steckverzahnung gefräst. Be- und Entladen der Maschine erfolgen erneut über das Ladeportal. Die Zuführung in den Arbeitsraum erledigt die interne Automation der HLC 150.
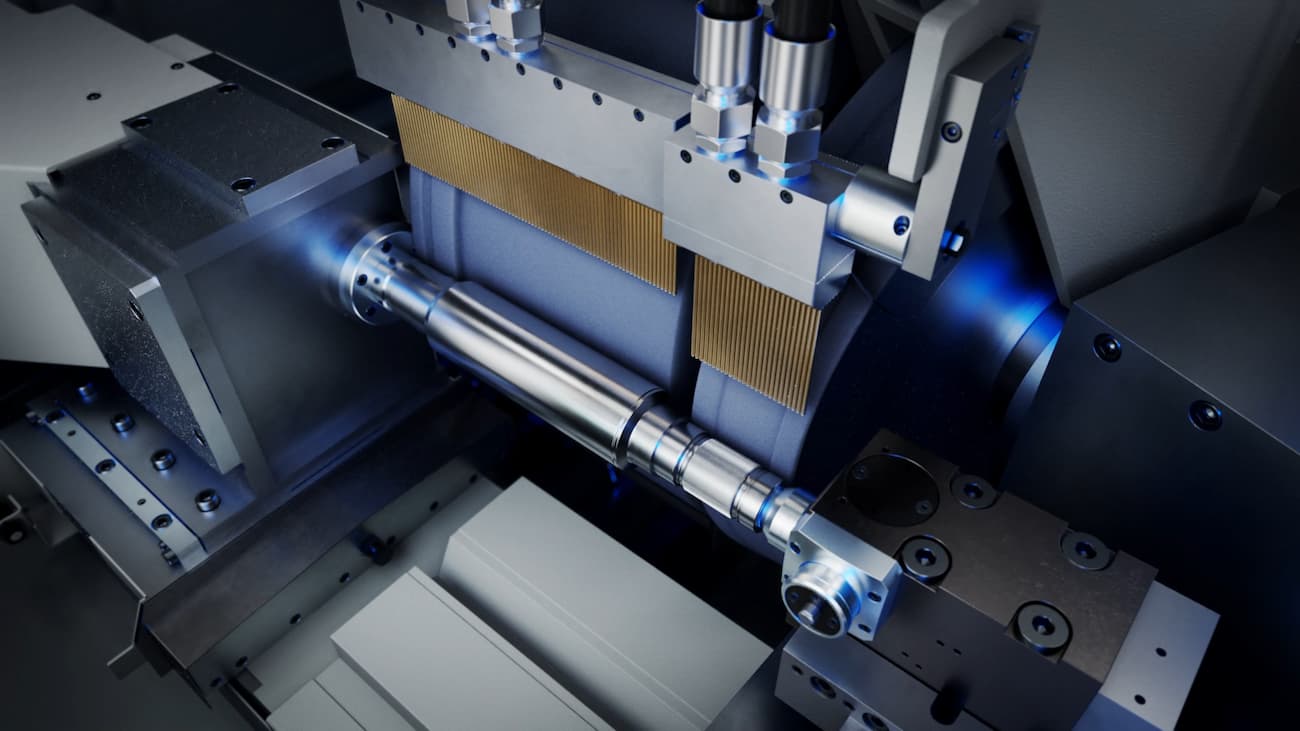
OP 70: Schleifen der Rotorwelle
Die Schleifprozesse an Lagersitzen, Planschultern und der Lauffläche des Wellendichtrings beschließen den Produktionsprozess an der Rotorwelle. Zum Einsatz kommen dabei zwei EMAG Maschinen des Typs HG 310.
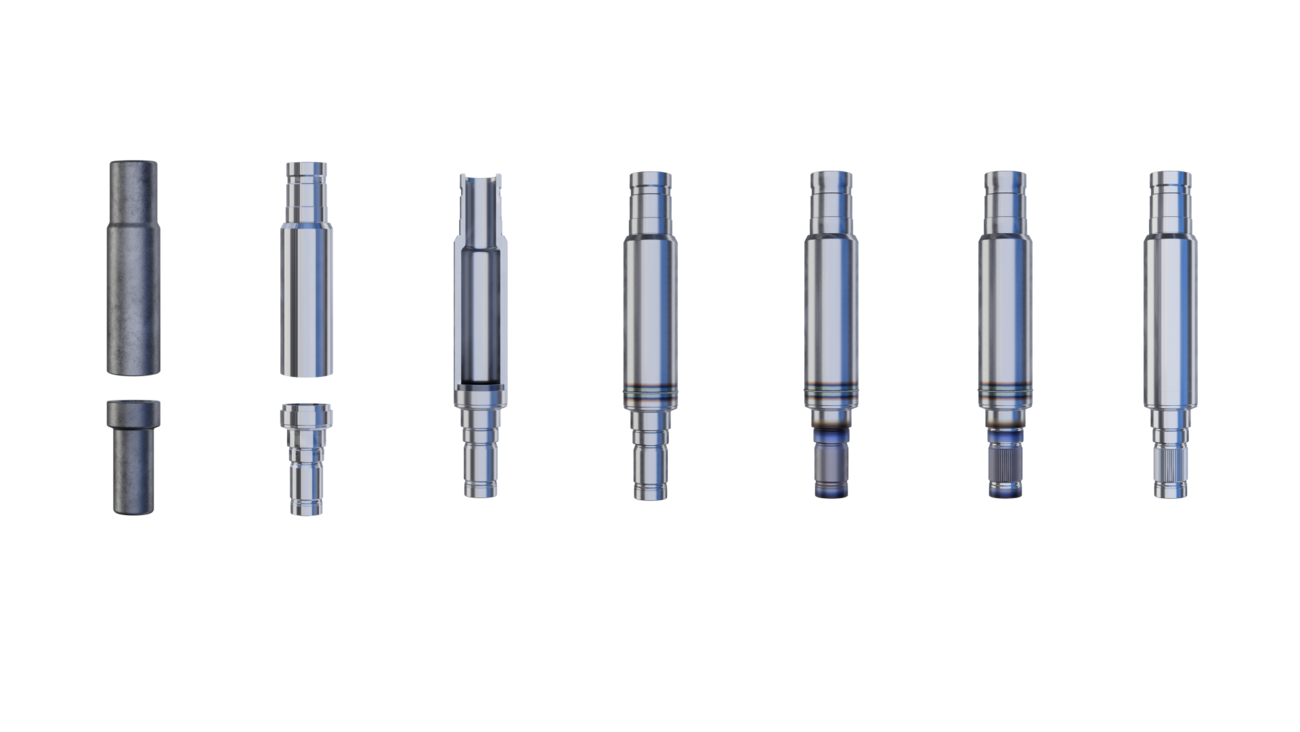
Vorteile dieser kompletten Fertigungslinie für Rotorwellen
- Technologie, Automatisierung und Prozessentwicklung kommen aus einer Hand – kurze Lieferzeiten und schneller Produktionsstart stehen dabei immer im Fokus.
- Alle Maschinen und die Automation werden optimal aufeinander abgestimmt.
- Einfache Automationssysteme, optimierte Schnittstellen und kurze Wege sichern rasante Produktionsprozesse.
- Das Fertigungssystem punktet mit kurzen Umrüst- und Wartungszeiten.
- „One Face to the Customer“: Ein erfahrener Ansprechpartner bei EMAG bespricht die Anforderungen der gesamten Produktionslösung mit dem Kunden.
Whitepaper
Elektromobilität
Erfahren Sie in diesem Whitepaper wie hocheffiziente Produktionslösungen für Rotoren, Statorgehäuse und Getriebeteile aussehen können. Sie können das Whitepaper in unserer Mediathek herunterladen.
MediathekTechnologien
Komplexe Fertigungssysteme aus einer Hand dank einer hohen Bandbreite an Technologien
Die Laserreinigung ist ein schnelles und platzsparendes Verfahren, das in vielen Anwendungsfällen konventionelle Waschmaschinen ersetzen kann. Eine…
Laserschweißen ist die Voraussetzung für kompakte, gewichtsoptimierte Bauteile und damit für energieeffiziente Fahrzeuge. Die exakt dosierbare,…
Das Vertikaldrehen ist ein zerspanendes Fertigungsverfahren für Metalle. EMAG war einer der ersten Werkzeugmaschinenhersteller, der das Vertikaldrehen…