Eine besondere Herausforderung beim Bearbeitungsprozess rund um homokinetische Gelenke stellt das Induktivhärten ihrer Achszapfen dar: Bislang kamen dafür sehr große und schwer bedienbare Linearmaschinen zum Einsatz, die mithilfe vieler einzelner Prozessschritte das komplexe Bauteil bearbeiteten – ein wenig stabiler Gesamtprozess mit Fehlerquellen. Vor diesem Hintergrund stellt die induktive Härtemaschine VLC 100 IH eine kleine Revolution für die Produktion von homokinetischen Gelenken dar. Mit ihr erfolgt das Induktivhärten nicht nur auf einer viel kleineren Maschinen-Stellfläche, sondern auch deutlich schlanker und somit letztlich prozesssicherer.
Den Härteprozess für Gelenkwellen radikal verschlanken
Immer komplexere Bauteile mit zunehmend schlankeren Prozessen produzieren – was zunächst paradox klingt, ist im Automobilbau seit Jahren einer der vorherrschenden Trends. Ein globalisierter Wettbewerb gibt hier den „Takt“ vor: Viele Abläufe müssen flexibler, einfacher und letztlich stabiler werden.
So rückt der für den Härteprozess verantwortliche Maschinenbau aktuell in den Fokus der Produktionsplaner, die auf der Suche nach schlankeren Lösungen sind. Das gilt vor allem, wenn die eingesetzte Technologie – wie bei der Bearbeitung des Achszapfens – komplex ist und dabei (zu) viel Stellplatz beansprucht.
So entwickelte eldec aufgrund einer Anfrage eines OEMs einen komplett neuen Prozess für das Induktivhärten des Achszapfens. Der gesamte Ablauf wird auf Basis der Pick-Up-Technologie massiv vereinfacht und deutlich schlanker.
Induktivhärten von Achszapfen in nur drei Takten
Einfacher und schlanker – tatsächlich scheint bereits der erste Blick auf die VLC 100 IH dieses Urteil zu bestätigen, denn die Härtemaschine beansprucht zunächst einmal eine viel kleinere Stellfläche als herkömmliche Linearanlagen. Zudem benötigt der komplette Prozess nur noch drei statt vorher acht Takte und vollzieht sich komplett innerhalb einer Aufspannung. Vieles erinnert in seiner Einfachheit an die Prozesse in anderen EMAG-Maschinen: Der einzelne Achszapfen wird zunächst per Pick-Up-Spindel aufgenommen, direkt in den Arbeitsraum transportiert und hochgenau positioniert. Die Spannung erfolgt am äußeren Bereich der Glocke mit einer denkbar kleinen Kontaktfläche, um eine unerwünschte Wärmeleitung am Bauteil zu vermeiden.
Genauso präzise erfolgt anschließend die Zustellbewegung jenes Induktors, der für das Induktivhärten des Schafts am Achszapfen verantwortlich ist. Er befindet sich deutlich über der Arbeitsspindel auf einer neu konstruierten Z-Achse und wird mithilfe eines Antriebsschlittens von oben auf das vorliegende Bauteil herabgefahren. Der zweite Induktor für die Glocke ist hingegen fest unterhalb der Arbeitsspindel angeordnet. Auf dieser Konstruktionsbasis kann das Härten aller relevanten Bauteilbereiche problemlos innerhalb eines Taktes erfolgen. Ein Wenden des Bauteils ist nicht nötig. Nach dem Abschrecken durch eine integrierte Abschreckbrause transportiert die Spindel das fertige Bauteil einfach wieder aus der Maschine heraus. Bauteildurchmesser bis zu 120 Millimeter und eine Bauteillänge bis 200 Millimeter sind möglich. Der entscheidende Vorteil ist bei diesem Härteprozess, dass mithilfe der zwei Induktoren der Schaft und die Glocke des Achszapfens in einer Erwärmungsstation gehärtet werden.
80 Prozent weniger Komponenten für den gleichen Prozess
So benötigt die kompakte Härtemaschine bis zu 80 Prozent weniger Komponenten, Aktoren und Sensoren als herkömmliche Linearsysteme.
Das ganze System ist im Übrigen zugänglicher für den Bediener. Alle Serviceprozesse erfolgen schneller und sicherer. Ein ähnlicher Konstruktionsvorteil zeigt sich auch beim Antrieb, denn alle Prozesse innerhalb der VLC 100 IH laufen elektromechanisch ab – in vielen Linearmaschinen kommen hingegen pneumatische Einheiten zum Einsatz. Auf diese Weise ist das eldec-System deutlich energieeffizienter und weniger fehleranfällig.
Und nicht zuletzt lässt sich diese Technologie, die über eine eigene Automation verfügt, perfekt in ganzheitliche Produktionslinien integrieren.
Der Ansatz lässt sich natürlich auf weitere Bauteile übertragen. Viele Anwender für das Härten des Achszapfens nutzen immer noch eine letztlich unproduktive Lösung. eldec bietet hierfür eine robuste Alternative mit deutlich dynamischeren und sicheren Produktionsprozessen. Das ist für ein Automotive-Bauteil, das hochpräzise und in sehr großen Stückzahlen entstehen muss, eine unverzichtbare Qualität.
Vertikale Härtemaschine VLC 100 IH für die Serienfertigung
Die von der EMAG eldec Induction GmbH entwickelte vertikale Pick-up-Härtemaschine VLC 100 IH überträgt das induktive Härten auf den modularen Maschinentyp von EMAG.
Weitere Infos…
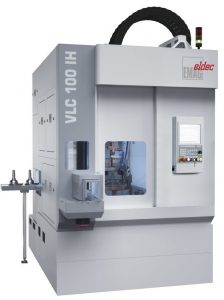
Die vertikale Pick-up-Härtemaschine VLC 100 IH überträgt das Induktivhärten auf den modularen Maschinentyp von EMAG.