09/01/2024 - Oliver Hagenlocher - Stampa
Soluzioni di rettifica di EMAG SU: Finitura superficiale estrema per la mobilità elettrica
Particolare precisione e affidabilità dei processi hanno caratterizzato l'ingegneria automobilistica per molti decenni. Con l'affermarsi della mobilità elettrica, tuttavia, queste esigenze stanno aumentando ancora una volta, perché molti componenti dei motori elettrici devono essere prodotti in modo ancora più "perfetto": Ciò richiede la massima finitura superficiale nell'ordine dei micrometri, in modo che non si verifichino rumori di marcia sui componenti degli ingranaggi. In questo contesto, la tecnologia di EMAG SU è attualmente al centro dell'attenzione di molti pianificatori di produzione: tra le altre cose, gli specialisti stanno sviluppando soluzioni ad alte prestazioni per la rettifica di ingranaggi, tra cui tempi brevi da truciolo a truciolo, concetti di assi intelligenti, stabilità termica e meccanica e un elevato grado di facilità d'uso. Su quali macchine e processi si concentra l'attenzione?
Immagini
Tra le soluzioni attuali per il settore della rettifica degli ingranaggi vi sono la macchina G 250 da un lato e la G 160 dall'altro. La G 160 viene utilizzata per componenti fino al modulo tre e con un diametro esterno massimo di 160 millimetri. In questo campo di applicazione, è la macchina più veloce sul mercato, grazie a due tavole portapezzo parallele che si muovono alternativamente ad alta velocità rispetto alla mola. Così, mentre un componente è in fase di lavorazione, il robot di carico inserisce un pezzo grezzo nell'altro mandrino o scarica il componente finito. Inoltre, il concetto degli assi garantisce le superfici perfette che sono così importanti nella mobilità elettrica. Il fattore decisivo è che la G 160 non ha un asse tangenziale, ma gli assi Y e Z esistenti creano un asse tangenziale "virtuale" attraverso un movimento simultaneo. Di conseguenza, la distanza tra l'asse A e il punto di contatto dell'utensile è molto ridotta, il che impedisce le cosiddette "frequenze fantasma" sulla superficie del componente. Le possibilità offerte da questo approccio per la mobilità elettrica sono dimostrate dall'esempio di un "albero intermedio" con 21 denti e un modulo normale, per il quale si è ottenuto un tempo da terra a terra di soli 33 secondi (compresa la compensazione di svergolamento e il tempo di ravvivatura proporzionale) e un tempo di rettifica di soli 25 secondi. Valori di prestazione simili sono mostrati per un albero di ingresso con 26 denti e un modulo di 1,6 millimetri. In questo caso, il tempo di rettifica puro è di soli 28 secondi.
Tempi terra-terra minimi
La macchina più grande, G 250, si distingue anche per la precisione, i tempi minimi da truciolo a truciolo, i brevi tempi di capacità di cambio formato per i componenti con una lunghezza massima di 550 millimetri. La macchina dispone anch'essa di una doppia tavola (come la G 160). Le operazioni di carico e scarico e la misurazione dei componenti vengono così eseguite in parallelo alla lavorazione. Interessante anche il fatto che il mandrino di rettifica possa ospitare mole di diametro diverso e che l'intera struttura sia molto rigida. La rettifica per generazione e la rettifica per profilo avvengono sul mandrino principale, quindi la macchina non ha un percorso termico. Inoltre, può essere riattrezzata per l'altro processo in pochi minuti. Nel campo della mobilità elettrica, ad esempio, questo approccio viene utilizzato per la rettifica delle ruote motrici degli assi. Il tempo terra-terra è di soli 69 secondi (compresa la compensazione di svergolamento e il tempo di ravvivatura proporzionale), mentre il tempo di rettifica effettivo è di soli 58 secondi. La G 250 raggiunge una produttività altrettanto elevata nella lavorazione di pignoni con una forte bombatura nel profilo del fianco del dente e una bombatura normale nella linea del fianco. Il tempo terra-terra è di 33 secondi e il tempo di rettifica pura di 28 secondi. È stata raggiunta una qualità DIN 3962 pari a 4.
Sky Grind: Riduzione massiccia dei costi
EMAG SU illustra inoltre quale potrebbe essere il futuro generale della rettifica degli ingranaggi con la creazione del nuovo processo "Sky Grind". In questo caso, la rettifica finale degli ingranaggi avviene completamente a secco, con grandi vantaggi economici per l'utente, perché non sono più necessari sistemi di filtraggio e di raffreddamento (normalmente necessari per la rettifica a umido), riducendo così i costi di investimento iniziali. Inoltre, il consumo energetico si riduce notevolmente. Il tutto è reso possibile da un sistema a doppio utensile con due mandrini diversi nella macchina: uno per l'operazione di finitura tramite dentatura e l'altro per l'operazione di finitura tramite rettifica. Ciò significa che, ad esempio, nel caso di una classica ruota di commutazione per autoveicoli con una tolleranza di 100 µm per fianco, 90 micrometri vengono rimossi con la dentatura e solo 10 micrometri con la rettifica di generazione con il processo Sky-Grind. In definitiva, i tempi ciclo della rettifica convenzionale e del processo Sky-Grind sono molto simili, ma i costi molto diversi.
Come si può riassumere il know-how e l'offerta di EMAG SU? "Si può certamente dire che garantiamo ai nostri clienti vantaggi competitivi e un rapido ritorno dell'investimento", risponde Alexander Morhard di EMAG SU. "Per raggiungere questo obiettivo, investiamo continuamente in ricerca e sviluppo per aumentare ulteriormente l'efficienza e la compatibilità ambientale delle macchine. Il risultato è quello di avere perfette soluzioni per la produzione di diversi tipi di ingranaggi che richiedono lavorazioni ultra fini".
Referenti
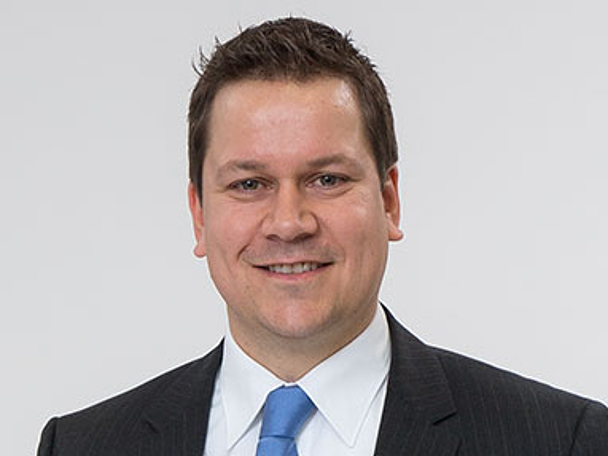