09.01.2024 - Oliver Hagenlocher - Noticias
Soluciones de rectificado de EMAG SU: Calidad de superficie extrema para la e-movilidad
La precisión especial y la fiabilidad de los procesos han caracterizado a la ingeniería automovilística durante muchas décadas. Sin embargo, con la implantación de la e-movilidad, estas exigencias vuelven a aumentar, ya que muchos componentes de los motores eléctricos deben fabricarse de forma aún más "perfecta": Esto suele implicar la máxima calidad superficial en el rango de los micrómetros, para que no se produzcan ruidos de los engranajes, por ejemplo, que, en vista del silencioso motor eléctrico, serían audibles. En este contexto, la tecnología de EMAG SU se encuentra actualmente en el punto de mira de muchos planificadores de producción: entre otras cosas, los especialistas están desarrollando soluciones de alto rendimiento para el rectificado de engranajes, que incluyen tiempos cortos entre virutas, conceptos de ejes inteligentes, estabilidad térmica y mecánica, así como un alto grado de facilidad de uso. ¿En qué máquinas y procesos nos centramos?
Imágenes
Entre las soluciones más destacadas para el campo de la rectificación de engranajes se encuentran, por un lado, la máquina G 250 y, por otro, la G 160. La G 160 se utiliza para componentes de hasta módulo tres y con un diámetro exterior máximo de 160 milímetros. En este campo de aplicación, es la máquina más rápida del mercado, lo que es posible gracias a dos mesas de piezas paralelas que se mueven alternativamente a gran velocidad a la muela. Así, mientras se mecaniza un componente, el robot de carga interna introduce una pieza en bruto en el otro husillo o descarga previamente el componente acabado. Además, el concepto de eje garantiza las superficies perfectas, tan importantes en la e-movilidad. El factor decisivo aquí es que el G 160 no tiene eje tangencial, pero los ejes Y y Z existentes crean un eje tangencial "virtual" mediante un movimiento simultáneo. Como resultado, la distancia entre el eje A y el punto de contacto de la herramienta es muy pequeña, lo que a su vez evita las llamadas "frecuencias fantasma" en la superficie del componente. Las posibilidades que abre este enfoque para la e-mobility se muestran, por ejemplo, con el ejemplo de un "eje intermedio" con 21 dientes y un módulo normal, con el que se consigue un tiempo de suelo a suelo de sólo 33 segundos (incluyendo la compensación de entrelazado y el tiempo de reavivado proporcional) y un tiempo de rectificado de sólo 25 segundos. Se muestran valores de rendimiento similares con un eje de entrada con 26 dientes y un módulo de 1,6 milímetros. En este caso, el tiempo de rectificado puro es de sólo 28 segundos.
Tiempos mínimos entre el suelo y el suelo
La máquina G 250, de mayor tamaño, también destaca por su precisión, tiempos mínimos de viruta a viruta, tiempos cortos de preparación y fiabilidad para componentes con una longitud máxima de 550 milímetros. La máquina también dispone de una mesa doble (como la G 160). De este modo, los procesos de carga y descarga, así como la medición de componentes, se realizan en paralelo al mecanizado. También es interesante: el husillo de rectificado puede alojar muelas de diferentes diámetros y toda la construcción es muy rígida. El rectificado por generación y el rectificado de perfiles tienen lugar en el husillo de rectificado principal, por lo que la máquina no tiene dilatación térmica. Además, puede reconvertirse para el otro proceso en sólo unos minutos. En el campo de la e-movilidad, por ejemplo, este enfoque se utiliza para rectificar las piñones motrices de los ejes. En este caso, el tiempo entre el suelo y el suelo es de sólo 69 segundos (incluida la compensación de entrelazado y el tiempo de reavivado proporcional), mientras que el tiempo de rectificado real es de sólo 58 segundos. La G 250 alcanza una productividad comparativamente alta al mecanizar piñones con un fuerte abombamiento en el perfil del flanco del diente y un abombamiento normal en la línea del flanco. El tiempo de fondo a fondo es de 33 y el tiempo de rectificado puro de 28 segundos. Se alcanza una calidad DIN 3962 de 4.
Sky Grind: Reducción masiva de los costes
Además, EMAG SU ilustra cómo podría ser el futuro general del rectificado de engranajes con el establecimiento del nuevo proceso "Sky Grind". En él, el rectificado final del engranaje se realiza completamente en seco, lo que supone grandes ventajas económicas para el usuario, ya que no se necesitan sistemas de filtrado, refrigeradores y similares (que normalmente son necesarios para el rectificado en húmedo), lo que reduce los costes de inversión iniciales. Además, el consumo de energía se reduce enormemente. Todo ello es posible gracias a un sistema de doble herramienta con dos husillos portaherramientas diferentes en la máquina: uno para el desbaste por fresa madre y otro para el acabado por rectificado. En la práctica, esto significa: por ejemplo, en el caso de una rueda dentada clásica de automoción con una tolerancia de 100 µm por flanco, se eliminan 90 micrómetros mediante tallado con fresa madre y sólo 10 micrómetros mediante rectificado generador con el proceso Sky-Grind. Al final, los tiempos de ciclo del rectificado húmedo convencional de engranajes y del proceso Sky-Grind son muy similares, pero los costes son muy diferentes.
¿Cómo se pueden resumir los conocimientos técnicos y la oferta de EMAG SU? "Podría decirse que garantizamos a nuestros clientes ventajas competitivas y un rápido "retorno de la inversión"", responde Alexander Morhard, de EMAG SU. "Para conseguirlo, invertimos continuamente en investigación y desarrollo para seguir aumentando la eficiencia y el respeto medioambiental de las máquinas. Al final, disponemos de soluciones perfectas para la producción de superficies ultrafinas con diferentes contornos."
Persona de contacto
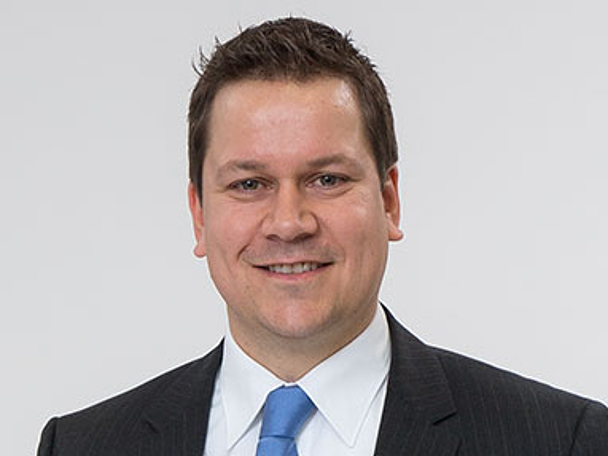
Oliver Hagenlocher
Área
Press and Communication