02/12/2019 - Oliver Hagenlocher - Stampa
Sistema di produzione EMAG: Realizzazione di un albero di rotore leggero con sistemi di produzione globali
Numerosi studi stimano una rapida crescita della mobilità elettrica. Anche le cifre sul volume di affari attuale indicano un cambiamento in questa direzione: secondo i dati forniti dal Center of Automotive Management, lo scorso anno la vendita di auto elettriche è aumentata notevolmente in Cina e negli Stati Uniti. In Germania la quota di mercato è raddoppiata nei segmenti più bassi. L'industria meccanica riveste un ruolo chiave nell'ambito di questo sviluppo, poiché deve sviluppare la tecnologia di produzione che consente di produrre i componenti centrali dei motori elettrici in modo rapido e sicuro – con volumi produttivi molto maggiori rispetto al passato. Uno di questi componenti è l'albero del rotore, la cui funzione è trasmettere in modo preciso e stabile la coppia elevata del motore elettrico. Allo stesso tempo la combinazione di pacco di lamierini e albero del rotore deve essere il più possibile leggera, per far aumentare l'autonomia delle auto elettriche. Com'è possibile produrre in modo efficiente un componente complesso come l'albero del rotore? Per far ciò i costruttori EMAG sviluppano numerose soluzioni che vengono adattate perfettamente alla geometria del componente e alla pianificazione della produzione – da sistemi di produzione perfettamente automatizzati a macchine singole customizzate.
La realizzazione di strutture leggere è da decenni una delle sfide centrali dell'industria automobilistica: componenti come ingranaggi del cambio, alberi motore e diversi tipi di alloggiamenti devono essere sempre più compatti e leggeri, in modo da ridurre i consumi dei veicoli. È interessante constatare come questa questione abbia una centralità ancora maggiore nelle auto elettriche, che con un peso inferiore riescono a percorrere tratti più lunghi senza ricarica dell'accumulatore. Ecco perché il tema "autonomia" rimane tuttora uno degli obiettivi di sviluppo più importanti nell'ambito della mobilità elettrica. In questo contesto alberi per motori elettrici pieni e quindi pesanti, sui quali si trovano pacchi di lamierini relativamente grandi, si dimostrano essere inadeguati. EMAG dimostra come sia possibile produrre in grandi serie alberi di rotore (e quindi motori elettrici) con un peso ottimale: gli specialisti di sistemi di produzione globali hanno concepito una linea dove lavorazione su non temprato, tempra e lavorazione su temprato di un albero cavo e quindi leggero vengono eseguite direttamente in successione. "Nel complesso, la produzione di un componente come questo rappresenta in ogni caso una sfida ideale per EMAG", spiega Ulrich Heiermann, Manager Technical Application presso EMAG. "Disponiamo del know-how applicativo necessario che include tornitura, alesatura, fresatura, tempra e rettifica. Inoltre, da decenni sviluppiamo i relativi sistemi di automazione. Ne consegue che la linea completa e lo sviluppo del processo vengono forniti da un'unica fonte. D'altro canto, per i sottoprocessi centrali come la tornitura o la rettifica offriamo soluzioni su misura, con macchine che possono ad esempio essere caricate a mano e, in caso di installazione di singole macchine, possono costituire anche il punto di partenza per la successiva trasformazione in una linea automatica completa. In entrambi i casi vengono utilizzate soluzioni modulari flessibili. Partendo da moduli tecnologici diversi configuriamo macchine su misura. Siamo preparati a ogni necessità del cliente."
Albero composto con notevoli vantaggi
Attualmente l'albero di rotore "composto" rappresenta un eccezionale esempio di approccio flessibile: su richiesta EMAG ha dovuto sviluppare un sistema di produzione in più fasi nel quale sono state combinate lavorazione su non temprato, saldatura laser, tempra e lavorazione su temprato. Inoltre durante il processo l'albero viene assemblato da due diverse estremità – un principio di base noto ad esempio per gli alberi a camme composti. In questo modo il processo può essere scomposto in sottoprocessi brevi e in alcuni casi eseguiti parallelamente. Questo approccio garantisce inoltre spesso ampia libertà agli sviluppatori dei componenti. La finitura di questo albero viene eseguita in modo perfettamente temporizzato all'interno del sistema EMAG: nelle prime due operazioni (10 e 20) i due diversi pezzi grezzi vengono lavorati all'interno e all'esterno e viene realizzata anche la geometria cava interna. Vengono utilizzate quattro macchine pick-up EMAG di tipo VL 4. Dopo un processo di pulizia (OP 30) le estremità vengono saldate tra di loro (OP 40) in una ELC 250 di EMAG mediante saldatura laser – un processo estremamente rapido e sicuro. L'energia concentrata e dosabile con precisione del raggio laser permette una elevata velocità di saldatura e ritardi minimi nel componente saldato. Nell'arco di pochi secondi viene quindi eseguita la tempra di precisione della sede dei cuscinetti nella macchina per tempra induttiva MIND 750 di EMAG eldec (OP 50). La lavorazione su temprato dell'albero ha inizio con la tornitura esterna nella macchina pick-up EMAG VT 4-4 (OP 60) e con la tornitura interna nella serie VL modulare (OP 70). Nella OP 80 e 90 viene eseguita una dentatura sull'albero e la tornitura esterna di finitura di diversi spallamenti. Il processo di rettifica finale, eseguito sulla rettificatrice verticale per alberi della serie VTC (OP 100) garantisce una lavorazione di finitura con tolleranze ridotte ed esigenze elevate di qualità delle superfici.
A questo punto l'albero è pronto per la giunzione con il relativo pacco di lamierini. Per quanto riguarda la tecnologia di automazione che garantisce il trasporto tra le macchine, EMAG si adatta alle esigenze dei clienti. Vengono ad esempio utilizzati portali di linea, celle impilatrici, nastri trasportatori ad accumulo oppure il sistema TrackMotion proprietario EMAG. In tutti i casi il sistema può beneficiare di macchine con una struttura unitaria e interfacce ottimizzate e, tra l'altro, di una soluzione completa per il cliente, con un sistema completo ed EMAG come unico partner di riferimento durante le fasi di pianificazione, realizzazione e assistenza. Inoltre la tecnologia pick-up EMAG garantisce un processo rapido: l'albero (o i due pezzi singoli inizialmente) viene trasportato all’interno e all’esterno della zona di lavoro con un mandrino portapezzo traslabile. Infine, viene completato il processo di tornitura e fresatura verticale a velocità di taglio elevate con una caduta di trucioli ottimizzata.
Una soluzione rapida da un'unica fonte
Ogni circa 45 secondi un albero di rotore finito esce dalla linea. Gli indesiderati tempi di fermo macchina sono ridotti al minimo. "La qualità di questo processo di produzione risulta cruciale già nella prima fase di progettazione. Qui EMAG fa leva su tutte le sue conoscenze – le svariate applicazioni per utensili, la progettazione di macchine utensili multifunzionali, il loro controllo e la concatenazione. Al centro c'è sempre l'obiettivo di produrre un componente ottimale, con il tempo ciclo e la qualità richiesti dal cliente. Se questo obiettivo viene realizzato in una linea completa con volumi produttivi annui elevati oppure ad esempio con soluzioni su misura caricate a mano per la produzione in piccole quantità e quindi con maggiore flessibilità, è il cliente a deciderlo", conclude Ulrich Heiermann.
More information about Assembled Rotor Shafts for Weight-Optimized Electric Motors you will find here...
Immagini
Download
Referenti
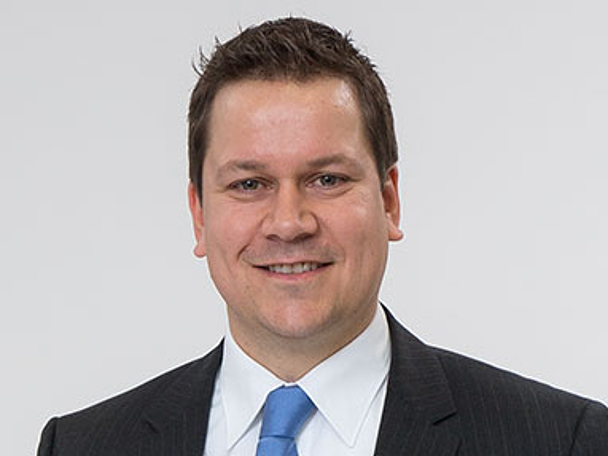
Oliver Hagenlocher
Zona
Press and Communication