02.12.2019 - Oliver Hagenlocher - Presse
Produktionssystem von EMAG: Leichte Rotorwelle entsteht mit ganzheitlichen Produktionssystemen
Zahlreiche Studien prognostizieren der Elektromobilität ein rasantes Wachstum. Auch die aktuellen Umsatzzahlen deuten den Wandel an: So ist laut Center of Automotive Management der Absatz von Elektroautos im letzten Jahr in China oder den USA massiv angestiegen. In Deutschland verdoppelte sich der Marktanteil auf niedrigem Niveau. Dem Maschinenbau kommt bei dieser Entwicklung eine zentrale Rolle zu: Er muss die Produktionstechnologie entwickeln, mit der sich zentrale Komponenten des Elektroantriebs sicher und präzise herstellen lassen – bei viel größeren Stückzahlen als bisher. Die Rotorwelle ist eine solche Komponente: Sie muss das hohe Drehmoment des Elektromotors präzise und stabil übertragen. Gleichzeitig sollte die Kombination aus Rotorblechpaket und -welle möglichst leicht sein, damit die Reichweite des E-Autos ansteigt. Aber wie lässt sich eine komplexe Rotorwelle effizient produzieren? Die Maschinenbauer von EMAG entwickeln hierfür unterschiedliche Lösungen, die perfekt an Bauteilgeometrie und Produktionsplanung angepasst werden – vom perfekt automatisierten Produktionssystem bis zur kundenspezifischen Einzelmaschine.
Der Leichtbau ist seit Jahrzehnten einer der zentralen Aufgabenstellungen im Automobilbau: Jede Komponente vom Getrieberad über Antriebswellen bis zu diversen Gehäusen soll leichter und kleiner werden, damit der Verbrauch der Pkws zurückgeht. Interessanterweise wird das Thema bei E-Autos fast noch wichtiger, weil sie mit weniger Gewicht längere Strecken ohne Nachladen des Akkus bewältigen. Daher bleibt bis auf weiteres das Thema „Reichweite“ eine der zentralen Entwicklungsaufgaben innerhalb der Elektromobilität. In diesem Zusammenhang passen massive und somit schwere Elektromotorenwellen, auf denen sich relativ große Rotorblechpakete befinden, nicht ins Bild. Wie sich gewichtsoptimierte Rotorwellen (und damit gewichtsoptimierte Elektromotoren) in Großserie fertigen lassen, zeigt aktuell EMAG: Die Spezialisten für ganzheitliche Produktionssysteme haben eine Linie konzipiert, in der Weichbearbeitung, Härten und Hartbearbeitung an einer hohlen und somit leichten Welle direkt hintereinander ablaufen. „Insgesamt ist die Produktion eines solchen Bauteils in jedem Fall eine ideale Aufgabenstellung für EMAG“, erklärt Ulrich Heiermann, Manager Technical Application bei EMAG. „Wir verfügen über das notwendige Anwendungs-Know-how, das vom Drehen, Bohren und Fräsen über das Härten bis zum Schleifen reicht. Außerdem entwickeln wir seit Jahrzehnten die dazugehörigen Automationssysteme. Folglich kommt die komplette Linie und Prozessentwicklung aus einer Hand. Auf der anderen Seite liefern wir für zentrale Teilprozesse wie das Drehen oder Schleifen kundenspezifische Einzellösungen, die dann zum Beispiel per Hand beladen werden und bei der Installation von Einzelmaschinen auch den Start für einen späteren Ausbau zu einer kompletten automatischen Linie bilden können. In beiden Fällen kommen flexible Baukastenlösungen zum Einsatz. Aus unterschiedlichen Technologiemodulen konfigurieren wir passgenaue Maschinen. Wir sind auf jede Anforderung vorbereitet.“
Gebaute Welle mit großen Vorteilen
Aktuell ist die „gebaute“ Rotorwelle ein beeindruckendes Beispiel für den flexiblen Ansatz: Gemäß Anfrage sollte EMAG ein mehrstufiges Produktionssystem entwickeln, das Weichbearbeitung, Laserschweißen, Härten und Hartbearbeitung zusammenführt. Außerdem wird die Welle während des Prozesses aus zwei unterschiedlichen Endstücken zusammengebaut – ein Grundprinzip, wie man es zum Beispiel von gebauten Nockenwellen kennt. So lässt sich der Ablauf in kurze und zum Teil parallel ablaufende Teilprozesse zerlegen. Außerdem eröffnet der Ansatz den Bauteilentwicklern häufig größere Freiheiten. Die Endfertigung dieser Welle erfolgt innerhalb des EMAG Systems perfekt getaktet: In den ersten beiden Operationen (10 und 20) werden die beiden unterschiedlichen Rohteile innen wie außen bearbeitet, wobei auch die hohle Innengeometrie entsteht. Zum Einsatz kommen vier EMAG Pick-Up-Maschinen des Typs VL 4. Nach einem Reinigungsprozess (OP 30) werden die Endstücke in einer ELC 250 von EMAG per Laserschweißen miteinander verbunden (OP 40) – ein extrem schnelles und sicheres Verfahren. Die exakt dosierbare, konzentrierte Energie des Laserstrahls erlaubt eine hohe Schweißgeschwindigkeit und minimale Verzüge am geschweißten Bauteil. Anschließend erfolgt das sekundenschnelle und hochpräzise Härten der Lagersitze in der induktiven Härtemaschine MIND 750 von EMAG eldec (OP 50). Die Hartbearbeitung der Welle startet mit dem Außendrehen in der EMAG Pick-Up-Maschine VT 4-4 (OP 60) und dem Innendrehen in der modularen VL-Baureihe (OP 70). In OP 80 und 90 erhält die Welle eine Verzahnung und verschiedene Schultern werden außen fertiggedreht. Für die Finishbearbeitung mit engen Toleranzen und hohen Forderungen an die Oberflächenqualität sorgt der abschließende Schleifprozess auf einer vertikalen Wellenschleifmaschine der VTC-Baureihe (OP 100).
Anschließend ist die Welle vorbereitet für das Fügen mit dem dazugehörigen Blechpaket. Bei der Automationstechnologie, die den Transport zwischen den Maschinen sicherstellt, passt sich EMAG den Vorstellungen der Kunden an. Es kommen zum Beispiel Linienportale, Stapelzellen, Stauförderbänder oder das EMAG eigene TrackMotion-System zum Einsatz – in jedem Fall profitiert das System von der Einheitlichkeit der eingesetzten Maschinen mit ihren optimierten Schnittstellen und nicht zuletzt von der Komplettlösung für den Kunden mit einem Gesamtsystem und EMAG als einzigen erforderlichen Ansprechpartner während der Planung, Umsetzung und im Servicefall. Außerdem sorgt die EMAG eigene Pick-Up-Technologie für Tempo im Prozessablauf: Die Welle (bzw. die beiden Einzelteile zu Beginn) werden mit einer verfahrbaren Werkstückspindel in den Arbeitsraum hinein- und heraustransportiert. Anschließend vollzieht sich der vertikale Dreh- und Fräsprozess mit hohen Schnittgeschwindigkeiten und einem optimiertem Spänefall.
Schnelle Lösung aus einer Hand
Etwa alle 45 Sekunden verlässt eine fertige Rotorwelle diese Linie. Unerwünschte Nebenzeiten, in denen eine Maschine stillsteht, sind auf ein Minimum reduziert. „Die Qualität eines solchen Produktionsprozesses entscheidet sich bereits in einer frühen Konzeptphase. Hier bringt EMAG sein komplettes Wissen ein – über die unterschiedlichen Werkzeuganwendungen, die Konzeption von multifunktionalen Werkzeugmaschinen, ihre Steuerung und Verkettung. Im Mittelpunkt steht immer das Ziel, ein optimales Bauteil in der vom Kunden geforderten Taktzeit und Qualität zu produzieren. Ob dies in einer ganzheitlichen Linie bei hohen Jahresstückzahlen oder zum Beispiel mit handbeladenen Einzellösungen bei geringeren Stückzahlen und dafür mit mehr Flexibilität erfolgt, entscheidet letztlich der Kunde“, so Ulrich Heiermann.
Weitere Informationen über Gebaute Rotorwellen für gewichtsoptimierte Elektromotoren finden Sie hier...
Bilder
Downloads
Ansprechpartner
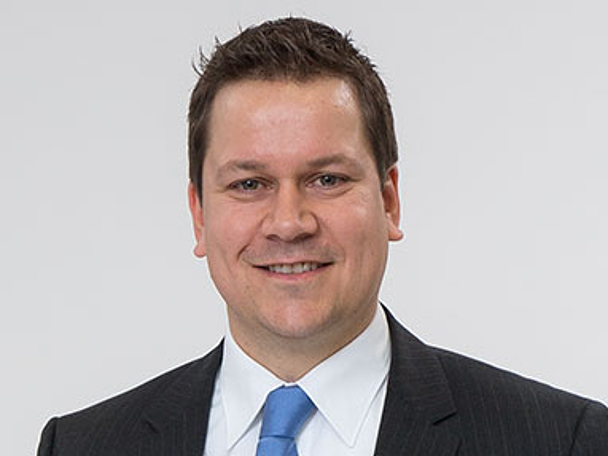
Oliver Hagenlocher
Bereich
Presse und Kommunikation