30.09.2020 - Oliver Hagenlocher - Presse
Wie man mit Schäldrehen die Fertigung von Rotorwellen optimieren kann
Durch den Wandel in der Automobilindustrie gewinnen nicht nur neue Bauteile, sondern auch neue Fertigungsmethoden für Produktionsplaner an Bedeutung. Die steigende Nachfrage nach Elektrofahrzeugen sorgt eben auch für steigende Produktionskapazitäten. Damit einhergehend stellt sich die Frage, wie sich diese Produktion möglichst effizient gestalten lässt.
Ein zentrales Bauteil ist dabei sicher der Elektromotor selbst. Für dessen Hauptbestandteil, nämlich die Rotorwelle mit Blechpaket, hat EMAG ein hocheffizientes Bearbeitungsverfahren entwickelt, das in puncto Geschwindigkeit und Qualität praktisch konkurrenzlos ist.
Bilder
Schon seit einiger Zeit gibt es Projekte bei denen die Blechpakete von Rotorwellen überdreht und nicht geschliffen werden. Da EMAG neben den vertikalen Drehmaschinen auch Schleifmaschinen herstellt, entschied man bei den Anfragen, neben der Kundenpräferenz, immer je nach Oberflächenanforderungen, ob mit Technologie Schleifen oder Drehen angeboten wird. Bei der Drehbearbeitung gibt es noch den Vorteil der Trockenbearbeitung des Blechpakets. Bei Oberflächenanforderungen unter Rz 6,3 Mikrometern, dauert konventionelles Längsdrehen wiederum entsprechend lange. So fing man bei EMAG damit an, mit der Schäldrehtechnologie zu experimentieren. Da diese Technologie bei EMAG schon länger eingesetzt und konstant weiterentwickelt wird, kennt man ihr großes Potenzial, das sich in Kombination mit der Leistungsfähigkeit der vertikalen Drehmaschinen zeigt.
Drallfreie Oberflächen und schnelle Vorschübe
Beim Schäldrehen wird eine schräg gestellte Schneide am rotierenden Werkstück vorbei geschwenkt. Der Schneideneingriffspunkt wandert dabei entlang der Schneide kontinuierlich weiter. So kommt die gesamte Schneidkante zum Einsatz und sorgt für bessere Standzeiten der Werkzeuge. Die Technologie bietet den Vorteil von sehr kurzen Zykluszeiten (bis zu 10-fach schneller als Schleifen bzw Längsdrehen).
Das Schäldrehen bietet dem Anwender mehrere Vorteile:
- die Möglichkeit, bei der Hartbearbeitung drallfreie Oberflächen zu erzeugen
- sehr kurze Zykluszeiten, die durch einen höheren Vorschub pro Umdrehung ermöglicht werden
- besseren Standzeiten der Werkzeuge, die durch den Einsatz der gesamten Schneidkante erreicht werden
Diese Vorteile galt es nun auf die Bearbeitung von Rotorwellen bzw. die Bearbeitung von Blechpaketen zu übertragen, was auch tatsächlich gelang. Dabei hat sich gezeigt, dass sich vor allem die Oberflächenqualitäten Rz < 6,3 µm mit höchsten Vorschüben bis 1mm/U mit dieser Bearbeitungstechnologie umsetzen lassen. Durch den schichtweisen Aufbau der Blechpakete bricht der Span je nach Dicke des Bleches und Vorschubwert nach 1 bis 1,5 Umdrehungen. So entstehen keine Späneknäuel, wie es sonst durch das Aufwickeln von langen Bandspänen bei der konventionellen Drehbearbeitung mit niedrigem Vorschub üblich ist.
Sinkende Kosten bei der Bearbeitung von Rotorwellen
Dass sich die Vorteile des Schäldrehens zwangsläufig auch positiv auf die Stückkosten auswirken, liegt auf der Hand. Denn aufgrund der kürzeren Zykluszeiten sinken die Maschinenkosten und die Werkzeugkosten und Werkzeugwechselkosten sinken aufgrund der längeren Standzeiten (bedingt durch die kurze Eingriffszeit jedes Bereichs der ganzen Schneide).
Allerdings ist der Fertigungsprozess mittels Schäldrehen anspruchsvoll und bedarf einer entsprechenden Maschinenbasis und des dazugehörigen Know-hows. Genau hier kann EMAG mit dem Gesamtpaket punkten.
4-achsige Bearbeitung von Rotorwellen
Die vertikalen 4-achsigen Wellendrehmaschinen der VT-Baureihe sind ideal für die Fertigung von Rotorwellen. Bei der Bearbeitung von Bauteilen mit einer maximalen Länge von 630 Millimetern und einem maximalen Durchmesser von 200 Millimetern können die Maschinen ihre Qualitäten voll ausspielen:
- Simultan: Der Bearbeitungsprozess erfolgt vierachsig, und zwar simultan von zwei Seiten. Dafür ist die Maschine mit zwei Werkzeugrevolvern mit jeweils zwölf Plätzen ausgestattet, wovon 11 mit Drehwerkzeugen oder angetriebenen Werkzeugen bestückbar sind; ein Platz ist jeweils durch einen Werkstückgreifer belegt.
- Automatisiert: Die Werkstückgreifer sorgen für eine parallele Be- und Entladung der Maschine. Während der eine Greifer ein neues Rohteil in die Spannposition bringt, transportiert der andere das fertige Teil hinaus auf das Werkstückband. Dafür ist die VT-Baureihe auf beiden Seiten mit umlaufenden Teilespeichern ausgestattet, in die die Rohteile bzw. Fertigteile aufgenommen werden können. Mit dem TrackMotion Automationssystem lassen sich mehrere VT-Maschinen sehr einfach und kostengünstig miteinander verketten.
Schäldrehen auf VT-Maschinen
Aufgrund der jahrelangen Erfahrung bei EMAG ist die Schäldrehtechnologie bereits optimal für den Serieneinsatz ausgelegt. Selbiges gilt für die eingesetzten Maschinen, die durch die Erkenntnisse aus vielen Anwendungen und Versuchen perfekt für diese Technologie ausgerichtet wurden. Beispielsweise wurde der Drehrevolver der VT-Baureihe an die speziellen Anforderungen des Schäldrehens angepasst. Dies betrifft sowohl die Mechanik als auch die Parametrierung der Schwenkachse und deren regelungstechnische Einstellung. Auch softwareseitig steht dem Einsatz der Schäldrehtechnologie auf den vertikalen Wellendrehmaschinen nichts im Wege. Entsprechende Programme auf der Steuerung machen das Einrichten der Maschine ebenso leicht wie bei einer konventionellen Drehbearbeitung.
Weitere Informationen:
In dieser Animation wird die Verkettung am Beispiel der Rotorwellenbearbeitung gezeigt: https://www.youtube.com/watch?v=B9pywqiPg-s
Downloads
Ansprechpartner
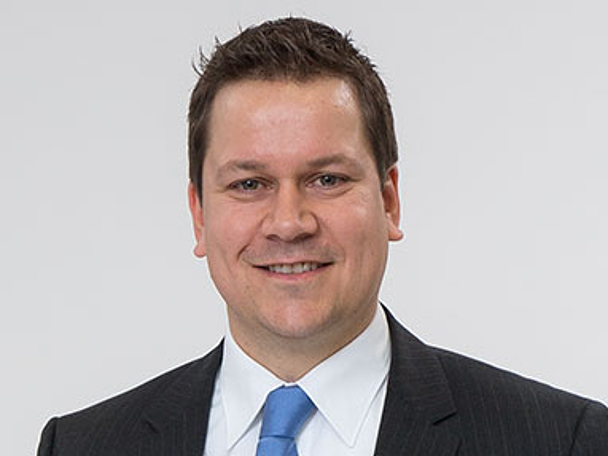
Oliver Hagenlocher
Bereich
Presse und Kommunikation