06.09.2021 - Oliver Hagenlocher - Noticias
Laser Metal Deposition: EMAG desarrolla una solución de producción para discos de freno recubiertos
El disco de freno de los automóviles del futuro es resistente al desgaste... y dura tanto como el propio vehículo. Esto se consigue gracias a un recubrimiento con dos capas de material duro que se aplican sobre el disco mediante un procedimiento de soldadura láser. La solución de máquina correspondiente está siendo desarrollada por EMAG LaserTec y se denomina ELC 450 LMD. Esta máquina integra la llamada Laser Metal Deposition en un proceso totalmente eficiente cuya calidad está asegurada. ¿Qué detalles distinguen esta solución de producto de EMAG?
Los sistemas de freno actuales siempre han generado muchas (incluso demasiadas) partículas de polvo fino. A ello se suma un nuevo reto: en los automóviles eléctricos, los frenos se utilizan poco porque durante la recuperación del motor ya se produce una acción de frenado suficiente. En algunos casos, debido a esta prolongada falta de uso, el disco de freno puede empezar a oxidarse. Ante esta situación, los constructores de automóviles están cambiando la tecnología de frenado. Los frenos de tambor, por ejemplo, podrían llegar a resurgir ya que, con ellos, el proceso de frenado no despide polvo fino hacia el medio ambiente. Una alternativa interesante a estos frenos son los discos de freno recubiertos de material duro, que son resistentes al desgaste y a la corrosión. Con ellos, por lo menos el disco no genera polvo fino y su vida útil es la del propio automóvil.
El foco puesto en una tecnología de recubrimiento eficiente
Sin embargo, hoy en día el recubrimiento de los discos con carburo de wolframio u otros materiales similares sigue constituyendo un especial desafío. Ello se debe a que, hasta ahora, lo más utilizado ha sido la proyección con llama a alta velocidad (HVOF), que consiste en "disparar" el recubrimiento a altas velocidades sobre el componente y causa grandes pérdidas de material. ¿Existe una alternativa más eficiente cuyo proceso resulte más seguro? "Con esta pregunta nos contactaron hace tiempo algunos proveedores de componentes, dado que nuestros conocimientos sobre láser ofrecen una base general ideal para desarrollar procedimientos de recubrimiento con láser", explica el Dr. Andreas Mootz, director general de EMAG LaserTec, con sede en Heubach, cerca de Aalen. "Además, tenemos muchísima experiencia en todo lo relacionado con el desarrollo de procesos integrales. Hemos combinado estas dos cualidades para desarrollar la nueva máquina ELC 450 LMD, cuyos procesos discurren con absoluta seguridad gracias a la llamada Laser Metal Deposition. Esta operación consiste en aplicar sobre el disco de freno una capa adherente y, encima, una capa de metal duro mediante sendos procesos de soldadura láser. Casi no se pierde nada de material".
Este proceso es posible imaginarlo con exactitud examinando los detalles de la máquina. Esta contiene una mesa circular con cinco estaciones por las que cada componente pasa en total cuatro veces (dos por cada lado debido a las dos capas de recubrimiento).
- Pesaje: en la primera estación se pesa el componente aún sin recubrir. El valor obtenido sirve de referencia para luego determinar el peso de la capa en el siguiente pesaje, después de una pasada. El resultado permitirá saber si sobre el disco se ha aplicado la cantidad de material correcta.
- Limpieza láser: en la siguiente estación se limpian las sustancias de trabajo y la suciedad que haya en la pieza bruta. Para ello se aplican sobre la superficie unos impulsos de radiación láser que evaporan súbitamente el material.
- Precalentamiento: en la tercera estación, la tecnología de inducción de EMAG eldec hace que el componente alcance la temperatura de mecanizado ideal.
- Laser-Cladding: ahora, mediante un procedimiento con láser, se inicia el recubrimiento propiamente dicho. En cada pasada se aplica una capa: primero una capa adherente y luego el recubrimiento de carburo. El proceso entero se beneficia del avanzado diseño de la herramienta láser, que suministra el polvo de material a través de un canal. Este polvo se fusiona con la superficie del disco en el punto de fusión del proceso de soldadura.
- Estación volteadora/medidora: por último, la mesa circular contiene una estación de medición y volteo. Esta se utiliza cuando el primer lado del componente ya ha atravesado dos pasadas de recubrimiento y, por tanto, queda pendiente el segundo lado.
Soluciones integrales de EMAG
En conjunto, el desarrollo de esta nueva tecnología de recubrimiento aún no ha concluido del todo, tal como confirma el Sr Mootz: "Seguimos realizando ensayos de recubrimiento en colaboración con nuestros clientes. Pero ya vemos que, en un futuro, podremos ofrecerles una solución muy eficiente. La combinación de tecnología de recubrimiento láser de alta precisión con otros procedimientos, como la limpieza y el precalentamiento, y con medidas de aseguramiento de la calidad como el pesaje garantiza la seguridad de proceso indispensable para producir gran cantidad de piezas destinadas a la construcción de automóviles". A ello se suma una ventaja característica de EMAG: para los procesos previos de torneado del disco y los procesos finales de rectificado del disco recubierto, esta empresa constructora de maquinaria también desarrolla la tecnología de producción adecuada. Por deseo de los clientes, la solución completa para la fabricación de la siguiente generación de discos de freno también será de EMAG. "Partiendo de nuestra larga experiencia y nuestros amplios conocimientos, apostamos en muchos campos de aplicación por las soluciones integrales de un único proveedor. En poco tiempo, los discos de freno recubiertos también serán un ejemplo de ello", resume el Sr. Mootz para terminar.
Imágenes
Persona de contacto
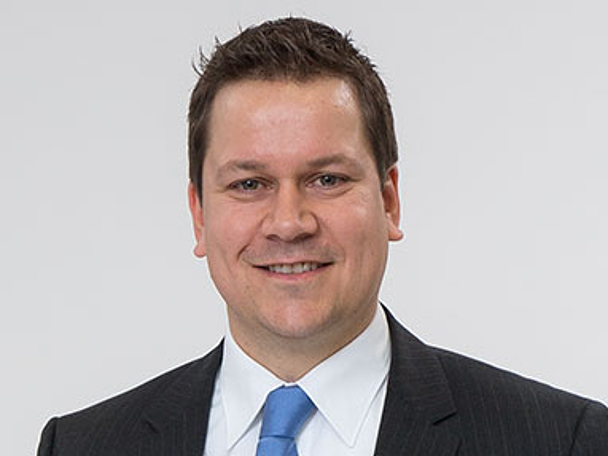
Oliver Hagenlocher
Área
Press and Communication