06.08.2019 - Oliver Hagenlocher - Noticias
EMO 2019 – Soluciones de línea con la VL 1 TWIN: enorme reducción de costes por pieza para engranajes planetarios o cónicos
La presión generada por los costes, las altas exigencias de calidad y, también en gran medida, las enormes cantidades de piezas requeridas afectan enormemente a la fabricación de cajas de cambios para turismos. Además, se espera que los volúmenes de producción aumenten en los próximos años. Los autores de los actuales "Escenarios de Shell para automóviles de turismo" estiman que la flota mundial de turismos podría más que duplicarse hasta alcanzar los 2500 millones de vehículos en 2050. Casi inevitablemente, el coste por pieza se coloca en el punto de mira de los planificadores de producción: ¿cómo es posible fabricar en grandes series y de forma más eficiente componentes típicos de cajas de cambio, como engranajes planetarios o cónicos? El Grupo EMAG ofrece una respuesta a la medida de esta pregunta con el desarrollo del centro de torneado pickup de dos husillos VL 1 TWIN. Este torno mecaniza simultáneamente dos componentes idénticos en un mismo espacio de trabajo. Esta base técnica ofrece posibilidades de gran alcance: si se conectan dos máquinas en línea, el engranaje planetario puede mecanizarse por ambos lados, y esto con tiempos de ciclo cortos. ¿Cómo es exactamente la solución de línea para engranajes planetarios o cónicos?
Imágenes
No es nada raro que en determinados centros de producción se fabriquen cada año hasta un millón de ruedas de engranajes planetarios. Para entender esto basta con echarle un vistazo a una transmisión automática con convertidor: el correspondiente engranaje planetario consta, por lo general, de cuatro juegos de ruedas dentadas, cada uno de ellos con tres piñones planeta y una rueda solar. Puede haber un total de 16 ruedas dentadas. Además, es interesante observar cómo la transmisión automática con convertidor está adquiriendo una renovada importancia en la actualidad. Por un lado se sigue considerando que es una solución cómoda, compacta y robusta para una caja de cambios. Por otro, algunos fabricantes también apuestan por esta tecnología para el diseño de motores híbridos modernos. "En este contexto es posible explicar el desarrollo del VL 1 TWIN. La reducción de costes en la fabricación de engranajes planetarios y cónicos era una prioridad en nuestra agenda", explica Björn Svatek, Sales & Marketing Director Modular Solutions de EMAG. "Por este motivo, en esta máquina de doble husillo hemos apostado por el mecanizado simultáneo de dos componentes idénticos en un mismo espacio de trabajo. Esto tiene como resultado grandes volúmenes de producción en tiempos muy cortos. Por otro lado, hemos reducido significativamente el precio por husillo mediante un control de costes consecuente. Esto contribuye al bajo coste por pieza".
Engranajes planetarios: dos piezas terminadas cada 20 segundos
¿Qué aspecto tiene exactamente una solución de línea VL-1 TWIN para el mecanizado blando de estos engranajes planetarios? En principio, el proceso tiene lugar en dos máquinas que están conectadas entre sí por un sistema de automatización TrackMotion. El correspondiente TransLift (un carro de elevación y volteo con pinza eléctrica) retira simultáneamente dos piezas brutas de la cinta de alimentación y las transporta a la primera máquina. Aquí, los dos husillos pickup del VL 1 TWIN se encargan de llevar los componentes a la zona de trabajo. A continuación se realiza el torneado del primer lado del diámetro interior y exterior (OP 10 – OP 10). El diámetro y la longitud (dirección X/Z) de ambos componentes se pueden corregir por separado, ya que los cabezales fijos pueden desplazarse de forma independiente. Esto es especialmente importante después de un cambio de herramienta, para compensar desviaciones (por ejemplo, después de cambiar las placas volteadoras). Después de extraídas las piezas del espacio de mecanizado, el TransLift vuelve a tomar el relevo: gira 180 grados los dos componentes semiterminados y los transporta al otro VL 1 TWIN. Aquí se refrenta la segunda cara del diámetro exterior (OP 20 – OP 20). Finalmente, el TrackMotion deposita el componente terminado en la cinta de almacenamiento, la cual puede alojar hasta 400 piezas terminadas en las unidades de apilado integradas. Todo el proceso tiene lugar con un tiempo de ciclo de unos 20 segundos para dos componentes. El tiempo medio entre sujeciones es de apenas 5 segundos. Una serie de detalles técnicos de equipamiento hacen posible esta enorme velocidad: los dos husillos pickup ofrecen altos valores de accionamiento de 9,9 kW y 136 Nm con un funcionamiento al 40 %. Al mismo tiempo, el motor lineal sin desgaste en el eje X (en combinación con sistemas de medición directa de posiciones) tiene una elevada aceleración de 8 m/s2, alta precisión continua inclusive. Esto significa que los ajustes H6 del taladro principal, requeridos con frecuencia, pueden realizarse de forma fiable.
Engranajes cónicos: taladrado, desbastado y acabado en una máquina
Debido a la creciente presión de los costes en la fabricación de engranajes cónicos, todos los procesos deben llevarse a cabo con alta eficiencia. Para ello, la fabricación mediante proceso de forja ofrece ventajas: los engranajes cónicos fabricados con procesos modernos suelen salir de la forja con un dentado ya acabado. En este caso solo se necesita un proceso de torneado en una sujeción. Con el VL 1 TWIN, EMAG ofrece la solución ideal para el mecanizado blando en paralelo de dos piezas brutas de engranajes cónicos (OP 10 – OP 10). En la máquina se llevan a cabo cuatro pasos de mecanizado sucesivos y el tiempo de ciclo es de solo unos 25 segundos: tras la alimentación mediante TrackMotion o husillo pickup, el taladro central del componente se realiza "en macizo" mediante un proceso de taladrado, tras el cual se inicia el desbastado del casquete esférico. En el tercer y cuarto paso tienen lugar el acabado del taladro y del casquete. Una solución de sujeción especial reproduce negativamente el dentado del componente y lo mantiene en una posición estable todo el tiempo. En relación con el proceso de taladrado macizo, la bancada de Mineralit® desempeña un papel especial, ya que el hormigón polímero reduce las vibraciones durante el proceso de taladrado, lo que proporciona una precisión adicional. Un sistema opcional de medición de piezas entre el espacio de trabajo y las estaciones pickup incrementa la fiabilidad del proceso. En principio, también es posible conectar dos VL 1 TWIN con un único sistema TrackMotion y llevar luego a cabo el mismo proceso en las máquinas (OP 10 – OP 10, OP 10 – OP 10). El factor decisivo es que la pinza TrackMotion se mueve con una velocidad de hasta 150 metros por minuto, lo que garantiza el transporte de entrada y salida en las máquinas TWIN que funcionan en paralelo.
Solución perfecta para la fabricación de cajas de cambios
En general, el concepto TWIN permite grandes incrementos de productividad para una gama completa de componentes adicionales, desde árboles de levas y pistas de rodamientos hasta bridas. Dependiendo de las necesidades se crean líneas de producción multitecnológicas, como fresadoras por generación y desbarbadoras EMAG. "Estamos convencidos de que el VL 1 TWIN es la solución perfecta para las crecientes cantidades de piezas y la competencia cada vez mayor en la fabricación de cajas de cambios", afirma Björn Svatek. "Los usuarios se benefician de unos costes por pieza más bajos, tiempos de ciclo cortos y una alta fiabilidad del proceso. Estas son las ventajas que deseamos defender en el mercado con mayor energía".
El VL 1 TWIN en vivo en la EMO 2019
Persona de contacto
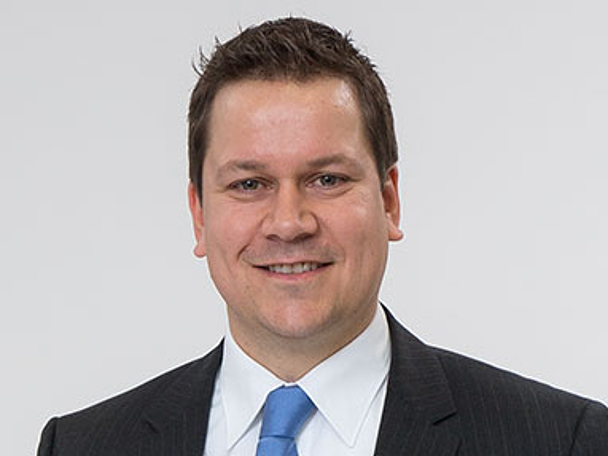
Oliver Hagenlocher
Área
Press and Communication