Whenever containers are lifted by trucks, large excavator shovels are swiveled or heavy containers are tilted at production plants, powerful rotary drives are to thank! The number of application examples for this technology is almost unlimited. As market leader in this sector, HKS Dreh-Antriebe GmbH with headquarters in Wächtersbach, Hesse relies on vertical hobbing machines from EMAG Richardon – major gearing is created with their help. These specialists have recently acquired a new machine of this type for their production site in Neukirch, Saxony. In the following interview, HKS Production Manager Mario Vogt explains why they made this investment decision and what technological challenges stand out in this process.
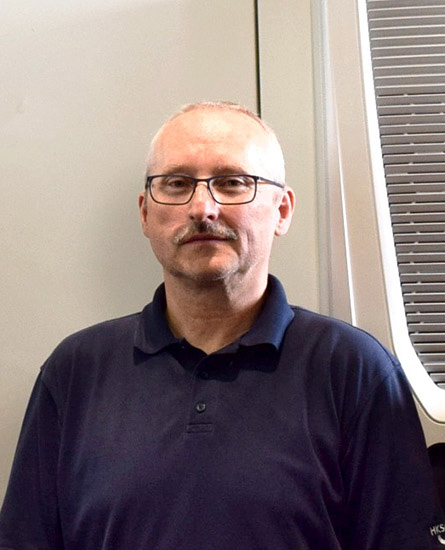
HKS Production Manager Mario Vogt
Mr. Vogt, how would you describe the challenges in the production of rotary drives?
Mario Vogt: First of all, you need to know that our product plays a major role in numerous areas of application. Rotary drives are used wherever a mass has to be accelerated, braked and precisely positioned. In concrete, for example, this means moving massive side walls of trucks, working platforms or very heavy excavator shovels. Our technology is also required in many areas of mechanical engineering, robotics, shipbuilding, the mining industry and power stations. These are usually not standard solutions – On the contrary: we develop and produce individual solutions with different design principles and performance values. They are customized perfectly to the respective task. For our production this means that we have to produce many different components and the batch sizes vary considerably. Flexibility is a top priority for us. For example, the re-tooling processes must be executed very quickly.
What role does quality play?
It is a significant factor. Our rotary drives are used, for example, on construction sites or within offshore plants. This means that the stress caused by these harsh environments is enormous and a large amount of force is exerted on the gears. Therefore, our production must ensure that all gearings are precisely manufactured, have stable surfaces and no defects. We must guarantee this is achieved at our three production sites in Hesse and Saxony. We use many different processes, from turning, milling and grinding up to gearing, broaching and butting.
You have recently acquired an R 300 vertical hobbing machine from EMAG Richardon for the production site in Neukirch. How did you make the decision on this investment?
Rotary drives are continuing to advance – new applications are constantly being added. For example, many manufacturers of forestry machines rely on our technology. They are responsible for the gripper movement of huge tree cutting machines. Against this background, our production quantities are also increasing of course. Old machines that are no longer suitable for high output quantities were being used in Neukirch. This made the investment in a state-of-the-art hobbing machine necessary. The obvious choice was a machine from EMAG Richardon. After all, two of these hobbing machines have been successfully operating at our production site in Hesse for a long time.
What exactly is produced with the new machine?
In rotary drives, there is a piston with a helical thread, which we produce using the R 300. This central gearing element converts the linear movement of the piston into a cumulative rotary movement – and only very precise gearing production guarantees that this process runs smoothly. Very different pistons with module 3 external gearings and a width of 90 to 350 millimeters (4 to 14 inches) are machined on the vertical hobbing machine. The components are between 200 and 500 millimeters (8 and 20 inches) long and weigh between 2 and 200 kilograms (4 and 441 lbs).
How exactly does the process take place in production?
After setting up the machine, we first run it in with a sample part. The operator can very easily pull up the required settings in the control panel. The R 300 is loaded either by hand or by crane – depending on the size and weight of the component. After completing the sample part, the gearing process starts with the first “correct” component. Finally, a hardening process takes place.
Have the processes been changed by putting the R 300 into service?
We have become a great deal quicker. The actual re-tooling process – without running-in – usually takes only a few minutes and the gearing process takes between 2 and a maximum of 30 minutes. In the past, we needed up to three hours! All in all, we are five to six times faster because we can achieve much higher cutting values. Considerably larger quantities in a comparable period of time are the result.
Are you happy with the machining quality?
The finished product meets our high demands in every respect. It is obvious that the low-vibration overall design of the machine positively effects the precision. The machine also provides good results in terms of the tool life. Compared to old machines, it has been increased by about 30 percent.
How many components are produced on the machine?
All in all, we manufacture very different pistons and gearings on the R 300. About 60 different rotary drives are required for the various construction machines alone – and that is only one of many different application areas. Our batch sizes vary between one and 50, which means we have to re-tool the hobbing machine almost daily. However, this is no problem because of the easy accessibility, large machining area and the simple to control software. Our operators were trained on how to completely turn over the machine in just two days. Since then there have been no problems at all.
The machine has been operating for a couple months now, what are your thoughts?
The entire process from the first meeting with EMAG, to the delivery and start-up of the machine was very smooth. There were no problems at all. The machine is fast, precise and sturdy – after seeing the performance of the machine, we are very happy with our decision.
More Information about the EMAG Richardon R 300 here…