The integration of robot technology into manufacturing processes is playing an increasingly important role in the modern industrial landscape. Jan Gotthold, Product Manager at EMAG Maschinenfabrik, provides an exciting insight into this area. Using EMAG’s drive shaft production line as an example, he demonstrates the key benefits of this technology.
The integration of robots into manufacturing processes is a hot topic in the industry. Mr. Gotthold, can you explain the main advantages using the EMAG manufacturing system for drive shafts as an example?
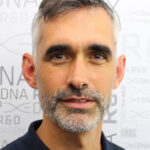
Jan Gotthold, Product Manager at EMAG Maschinenfabrik
Jan Gotthold: Of course, robot-assisted production, as developed by EMAG for drive shafts, offers immense advantages. Firstly, we achieve economical production through optimal machine utilization, which saves costs. Secondly, the high autonomy of the system enables a reduction in worker involvement, which increases flexibility. Thirdly, we achieve high buffer volumes in a small area and fourthly, the capital investments are comparatively low.
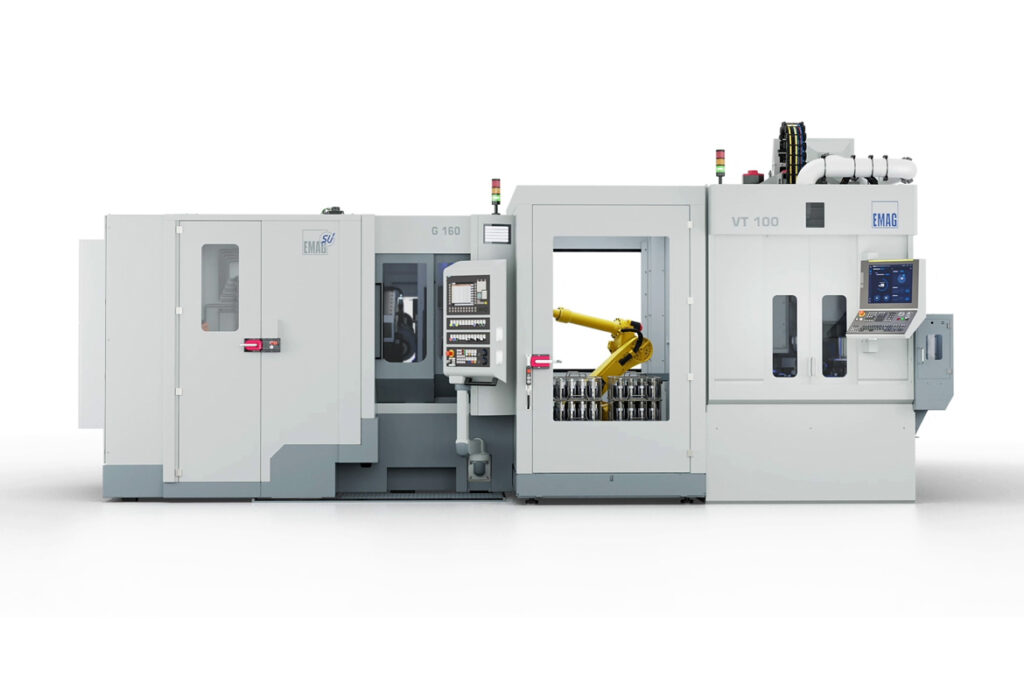
Production system for drive shafts interlinked using robot technology.
How does this system actually work and which machines are involved?
Jan Gotthold: At its core, the system consists of the VTC 100 vertical turning machine for 4-axis turning and the G 160 gear grinding machine for grinding. The VTC 100 is characterized by short paths and a powerful main spindle, which makes it ideal for high quantities.
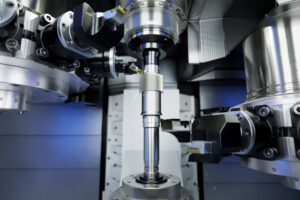
The VTC 100 vertical turning machine is ideal for 4-axis turning of drive shafts. It is characterized by short travel distances and a powerful main spindle, which makes it ideal for high quantities.
The G 160, on the other hand, can boast extremely short chip-to-chip times of less than 2 seconds thanks to its axis concept, making it one of the fastest gear generating grinding machines on the market.
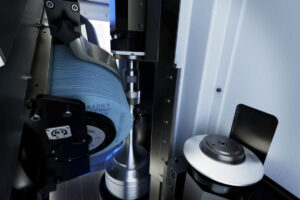
The G 160 gear generating grinding machine is one of the fastest gear grinding machines on the market. It is ideal for grinding drive shafts as it enables extremely short chip-to-chip times of less than 2 seconds.
The two machines are connected by a robot cell, which ensures fast and efficient processes.
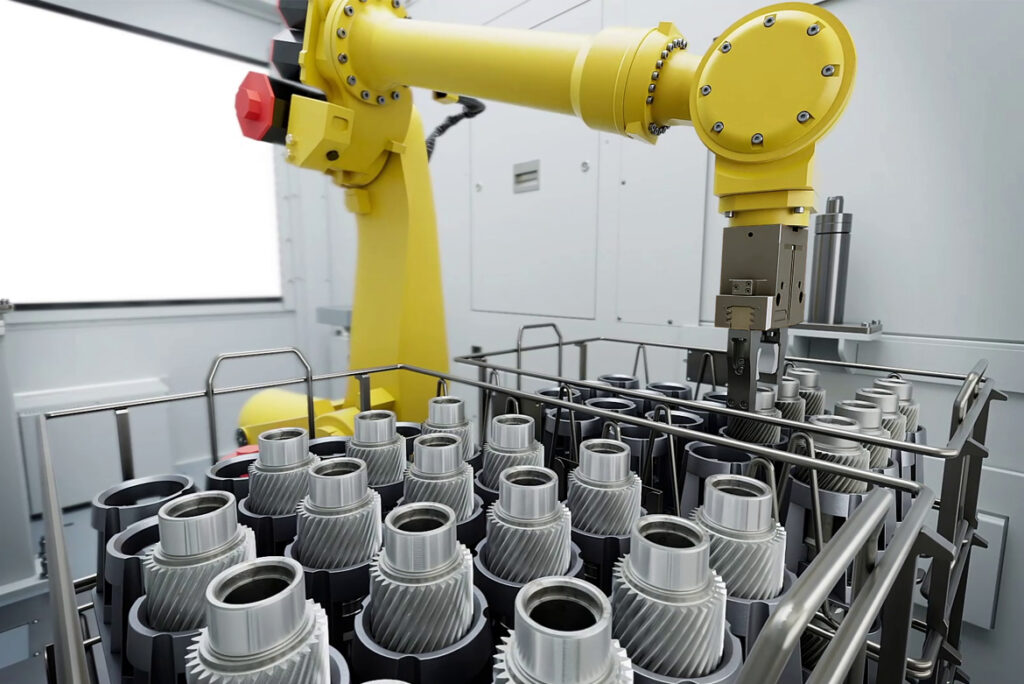
The robot cell is responsible for the fast and efficient handling of the drive shafts between the two machines. The direct link-up increases both process reliability and production efficiency.
How does this technology affect safety and efficiency in production?
Jan Gotthold: In addition to efficiency and user-friendliness, occupational safety is our top priority, which is why our machines and automation solutions meet the highest safety requirements.
Efficiency is increased by the reduced use of personnel and high availability alone. This means that less time is required for loading and unloading as well as for the machining processes, which leads to higher output.