In the rapidly developing world of electromobility, precision and efficiency play a decisive role in production technology. The HLC 150 H high-performance gear cutting machine from EMAG KOEPFER represents a revolutionary solution in this context. This machine, which is characterized by its universality, precision and performance, was specially designed for the demanding task of machining tooth profiles in electric car components. With the increasing demand for quiet and efficient electric vehicles, the requirements for the machining quality of the components are also increasing. The HLC 150 H meets these challenges with advanced technology and an impressive range of machining options. In this blog post, we take a look at the special features and technical innovations of this machine and shed light on how it is driving production in the e-car sector.
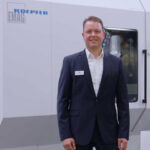
Jörg Lohmann, Head of Technology & Project Management at EMAG KOEPFER
Mr. Lohmann, what is so special about the HLC 150 H?
The HLC 150 H is characterized by its universality, precision and performance. It is suitable for a wide range of workpieces and enables the efficient machining of various types of gears such as spur and helical gears, shafts and worms. The machine offers a wide range of technological possibilities and is particularly suitable for high-precision tasks such as the machining of components for electric cars.
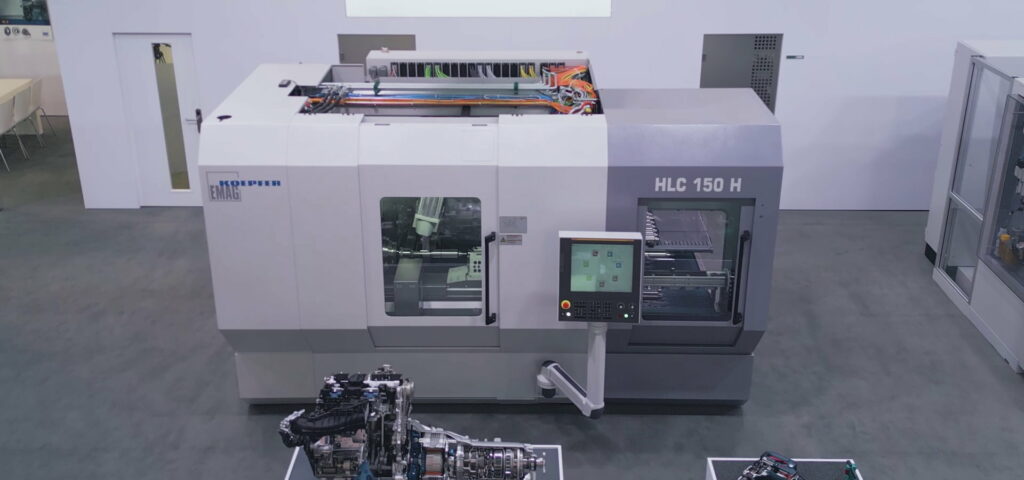
The HLC 150 H: A high-performance gear cutting machine for a wide range of applications
How does the absence of an internal combustion engine affect the requirements for components in electric cars?
As electric cars lack the masking noise of a combustion engine, the requirements for the noise emission of components are increasing. Higher gearing qualities and surface finishes are required to avoid disturbing running noises. This applies not only to the hard finishing of shafts, but also to soft machining.
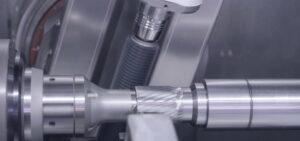
Adaptation to e-mobility: machining of rotor shafts, higher gear qualities for lower noise emissions.
What role does the HLC 150 H play in production for e-mobility?
With a view to the growing e-mobility market, the HLC 150 H offers a solution for increasing quantities. With its high degree of automation and process stability, it is ideal for mass production. Various automation solutions, from manual loading to integration into manufacturing systems, make it a versatile gear cutting machine in e-car production.
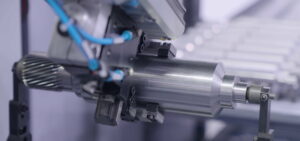
Automation meets process stability: solutions for increasing volumes in e-mobility.
What are the special features of the HLC 150 H gear hobbing machine for the gear cutting of rotor shafts?
The HLC 150 H ensures high productivity in the machining of rotor shafts, a key component in electric cars. It enables short cycle times and achieves a gear cutting quality of DIN 7. Its design ensures stable and process-reliable hobbing and prevents the formation of chip clusters, resulting in higher efficiency and quality. EMAG KOEPFER has extensive experience in mechanical engineering and offers a broad portfolio of technologies for the machining of various components. With the HLC 150 H and K 160 machines, we are well positioned to meet the growing demand for high-precision and efficient machining solutions for the e-car boom. Our concept of seamless integration into the production process is particularly interesting for the mass production of e-car components such as rotor shafts.
How important is the automation capability of the machines?
The HLC 150 H is designed for a high degree of automation, which makes it ideal for modern production environments. Particularly noteworthy is the integrated high-speed gantry loader, which enables workpieces to be handled quickly and efficiently. This adaptability to different levels of automation makes the HLC 150 H a key tool for efficient and scalable mass production, especially in areas such as e-mobility, where high quantities and consistent quality are required.
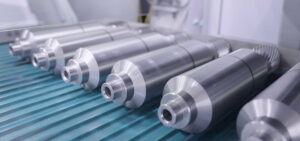
Flexible loading options: from manual loading to complete integration into manufacturing systems.