Lightweight construction in the automotive industry is a fight for every pound. Every single part is investigated for whether it could be made even lighter. This is typically accomplished by using new materials of changing part geometries. Laser welding offers a surprisingly simple strategy, e.g. by enabling a stable connection between differential gear and ring gear. This saves screw connections and reduces weight by 1.2 kg – quite an accomplishment by the standards of the field.
The entire process chain at a glance
It is critical that laser welding is integrated in an end-to-end process that begins with cleaning and brushing and finishes with a final inspection. Developing systems for such processes is a specialty of EMAG Automation. Over the last several years, the company has sold more than a hundred laser welding systems. As systems suppliers, the engineers at EMAG familiarize themselves with the production process and develop the process chain. This drastically simplifies the planning on the customer side.
In-depth experience with components
Customers of EMAG LaserTec also benefit from its in-depth experience with components: Various
control gears, differential housings or clutch bodies are
machined using production lines from Heubach, near Schwäbisch Gmünd, Germany, even today. The process is always planned around the component – based on EMAG’s proven modular engineering concept. This is why the systems are unusually stable and efficient in every detail.
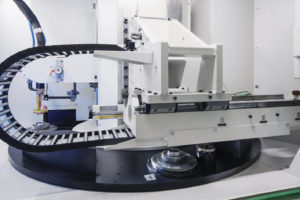
Integrating laser welding perfectly
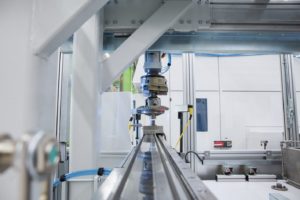
Integrating laser welding perfectly