The requirements for CNC lathes are clearly defined: maximum process reliability, high machining precision, flexible application options and easy integration into automated production lines. A well-thought-out machine concept is particularly important for workpieces that require machining on both sides as well as additional milling or drilling. The HSC 1 from EMAG has precisely these aspects in mind. In this interview, Peter Gröner, Product Manager of the Turning Business Unit at EMAG, explains the technical features, the range of applications and the design considerations behind this machine.
Mr. Gröner, what was the objective of the HSC 1 lathe?
We wanted to create a compact yet powerful CNC lathe that is ideally suited for two-stage machining processes – i.e. OP 10 and OP 20 – and enables off-the-shelf machining. The focus was on covering all the key requirements of modern turning: high machining accuracy, stable machining, short set-up times and good automation capability. The machine had to be suitable for use in both medium and batch production without compromising on part quality or system availability.
What are the technical features of the machine concept?
At the center is a sturdily designed machine base made of high-quality cast iron. This forms the basis for low-vibration and thermally stable machining. The HSC 1 is also equipped with a main spindle and a counter spindle. Both spindles have a C-axis, which enables rotation-synchronous milling and drilling operations. The spindle bore of 50 mm ensures efficient machining of workpieces made from bar stock. Larger workpieces can be loaded manually.
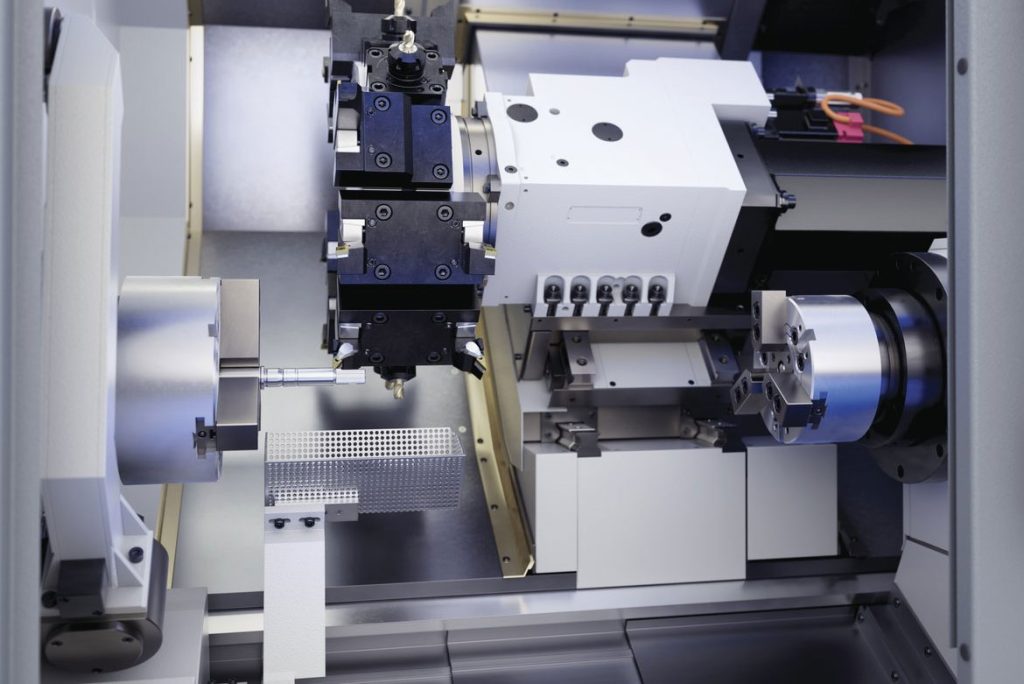
Work area of the HSC 1 with main and counter spindles. The workpiece transfer between the spindles enables continuous OP 10 / OP 20 production.
What is the machine structure like in detail?
The machine has three linear axes (X, Y and Z) and one C-axis each on the main and counter spindles. The X-axis moves 198 mm, the Y-axis ±50 mm and the Z-axis 570 mm. The Y-axis is designed as a linear axis. This allows eccentric contours, flutes, cross holes or flat surfaces to be machined on the lateral surface with high precision. All axes run on preloaded linear guides with ball screws (Ø 32 mm). The rapid traverses are up to 20 m/min in X and Z and 10 m/min in Y.
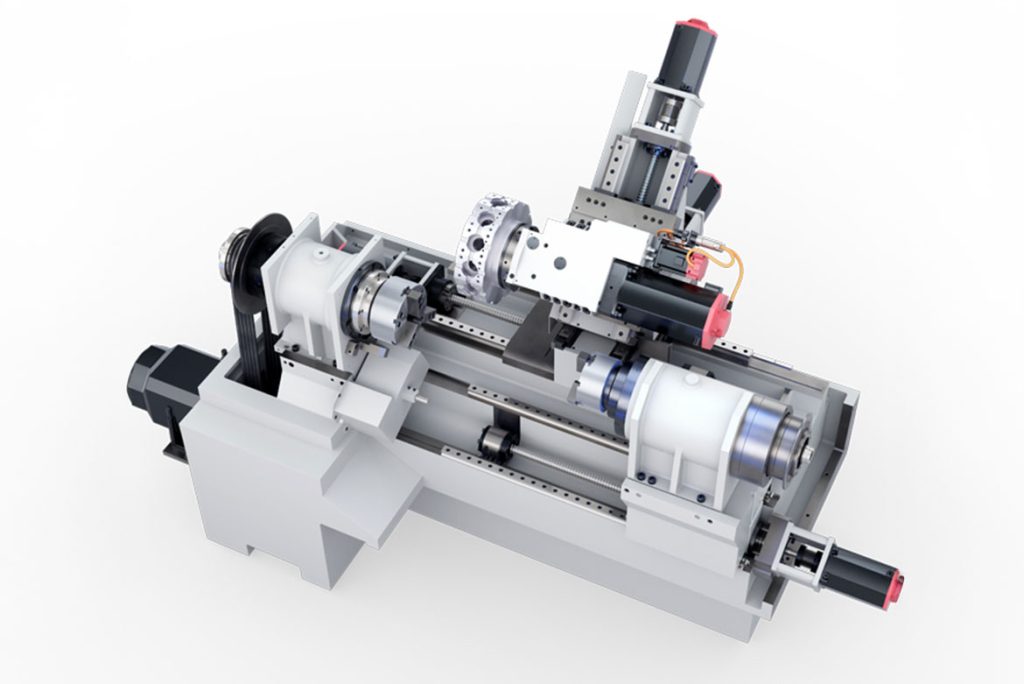
Design of the HSC 1 with three linear axes (X, Y, Z) and one C-axis each on the main and counter spindles. The Y-axis with ±50 mm travel extends the machining spectrum to include off-center milling and drilling operations.
What does spindle technology offer?
The main spindle has an A2-6 nose with a 63 mm bore, suitable for feeding bar stock up to 50 mm. It reaches 4000 min-¹ and is driven by an 11 kW motor (S6, 30 min) or 9 kW continuous power. The counter spindle – also with 4000 min-¹ – has a flange Ø 110 mm and offers 7.5 kW in short-time operation (5.5 kW continuous). Both spindles work irrespective of each other, which enables parallel processes: while a component is being finished on the counter spindle, the main spindle can pick up the next workpiece. The components can be transferred from the main spindle to the counter spindle. This enables machining of the reverse side.
What about the tool technology?
The HSC 1 has a 12-station servo turret in BMT-55 design as standard. All stations can be equipped with driven tools. These provide up to 4.5 kW at 5000 min-¹ and 18 Nm torque – sufficient for typical cross drilling, milling grooves, thread milling or light facing operations. Customers can also choose a 16-station turret as an option – either with VDI-30 or BMT-45. This brings more tools into the system or allows the use of sister tools, which in turn reduces set-up times.
What role does automation play?
The machine concept is fully automatable. The HSC 1 can be combined with a bar loader. A parts catcher is available for removal, which ejects the workpiece from the work area after parting off. The chips are removed via an integrated chip conveyor. Automatic work area doors, a chuck air blast function for chuck cleaning and interfaces for robot linking are available as options. This enables largely unmanned operation – even in shift systems.
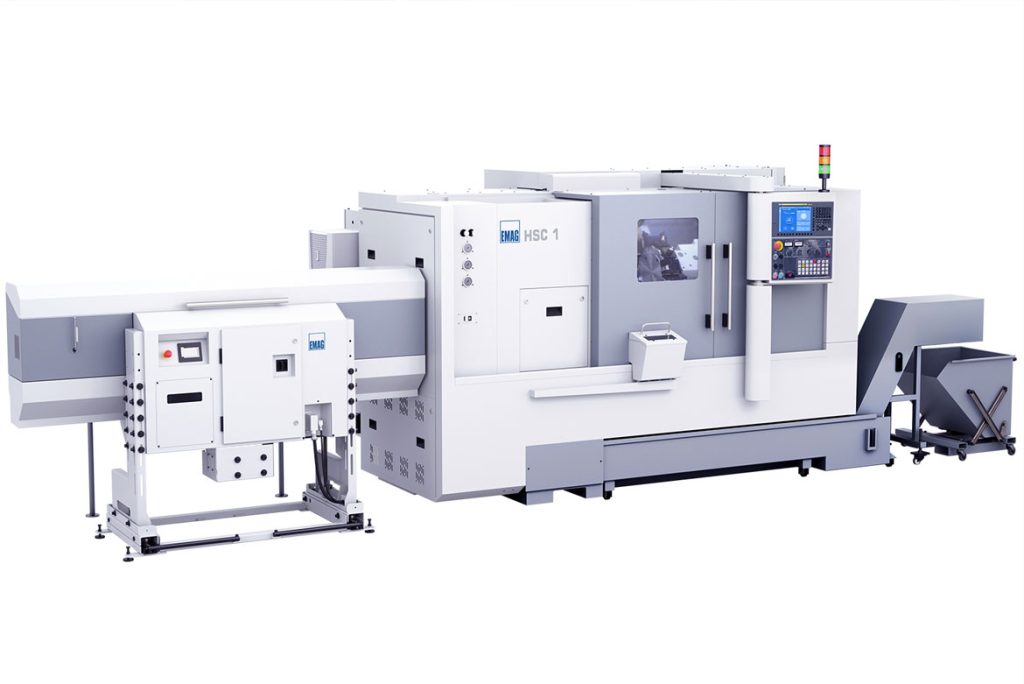
HSC 1 lathe with bar loader and chip conveyor for automated machining.
How do you ensure ease of operation and maintenance?
We pay attention to easy accessibility here: the control panel is mounted on the side and can be swiveled through 90° and the interior is easily visible thanks to large doors and LED lighting. We also have a service door to the counter spindle, a pull-out cooling system and central lubrication. Tool life is monitored via the control system – the Fanuc system offers reliable diagnostics here. Overall, the machine is designed for high availability with reduced maintenance requirements.
For which applications do you see the HSC 1 being typically used?
The component range extends from shafts and gear parts to hydraulic housings, bushings and flanges, as well as components for the medical technology and energy sectors. The machine is particularly advantageous for workpieces that need to be machined on both sides and have milling features. The combination of counter spindle, Y-axis and driven tools covers a wide range of applications, especially for small and medium-sized turned parts with complex geometries.