Whether you’re making transmission shafts, rotor shafts or even gun barrels, the challenges are consistent: high volumes, high precision, limited space and fewer people to get the job done. It can be a lot.
We caught up with David Fitzgerald, EMAG’s Regional Sales Manager, to talk about how the VT 4 vertical turning center is helping manufacturers check all the right boxes.
Q: When you’re talking to shaft manufacturers, what are they struggling with the most?
David: In a word – efficiency. Everyone’s trying to do more with less: fewer machines, fewer operators, smaller footprint, faster cycle times. And they still need top-tier quality. Whether it’s output or transfer shafts, pinions or something more niche like gun barrels, the core need is the same: produce a lot, produce it fast and don’t take up half the shop doing it.
Q: That’s a big ask. How does the VT 4 actually help with all of that?
David: It really boils down to this: The VT 4 does what most machines can’t – all in one setup. It’s got two turrets with live tooling and simultaneous 4-axis machining, so you’re cutting from both sides at once. You can turn, drill, mill, even brush – all in the same machine. Normally you’d need a second machine just for those extra ops. Not here. That consolidation is a big win.
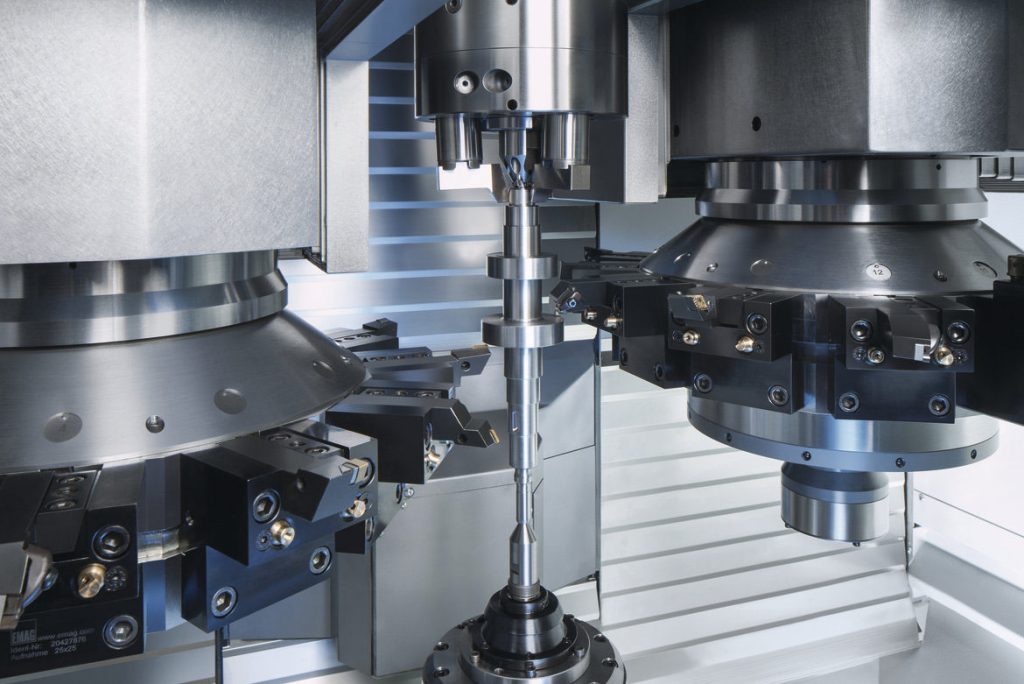
Interior view of the VT 4 showing two tool turrets, each equipped with eleven tool posts (one post per turret used by the gripper). This configuration enable simultaneous machining from both sides for faster cycle times and reduced setups.
Q: So it’s not just about turning. It’s doing secondary operations, too?
David: Exactly. Let’s say you’ve got to mill a slot then drill and brush to deburr the slot. With most machines, you’re handling it off to a second op – extra time, extra tooling, more space. With the VT 4, it’s one and done. The live tooling makes it super versatile.
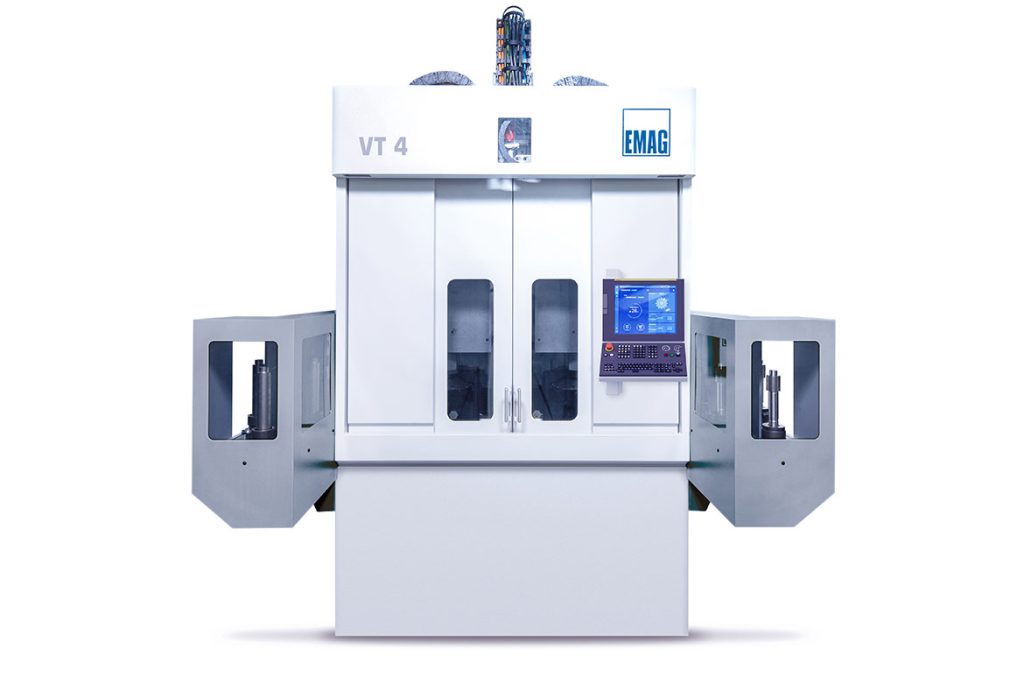
A full exterior view of the EMAG VT 4 vertical turning machine, showcasing its space-saving design and robust enclosure – ideal for automated, high-precision shaft production.
Q: What about quality? Can it keep up with long, high-volume runs without drifting out of spec?
David: Totally. The base is made from Mineralit polymer concrete, which dampens vibration really well – way better than cast iron. Plus, there’s a chiller system that keeps things thermally stable: the base, the turrets, the spindle, all of it. And if you’re really chasing precision, there’s a touch probe on the turret for in-process quality checks. It’s built to stay consistent, even under pressure.

The vertical design arrangement allows gravity-assisted chip flow during machining, preventing chip build-up and maintaining process stability, especially in high-volume operations.
Q: Automation seems like a big deal here. How is it built into the machine?
David: Yeah, and that’s what sets the VT series apart. The automation is fully integrated – not bolted on later. The turrets actually handle loading and unloading using built-in grippers. So once the raw parts are on our built-in conveyer – either by hand or robot – the VT 4 just does its thing. Less operator time, more run time.
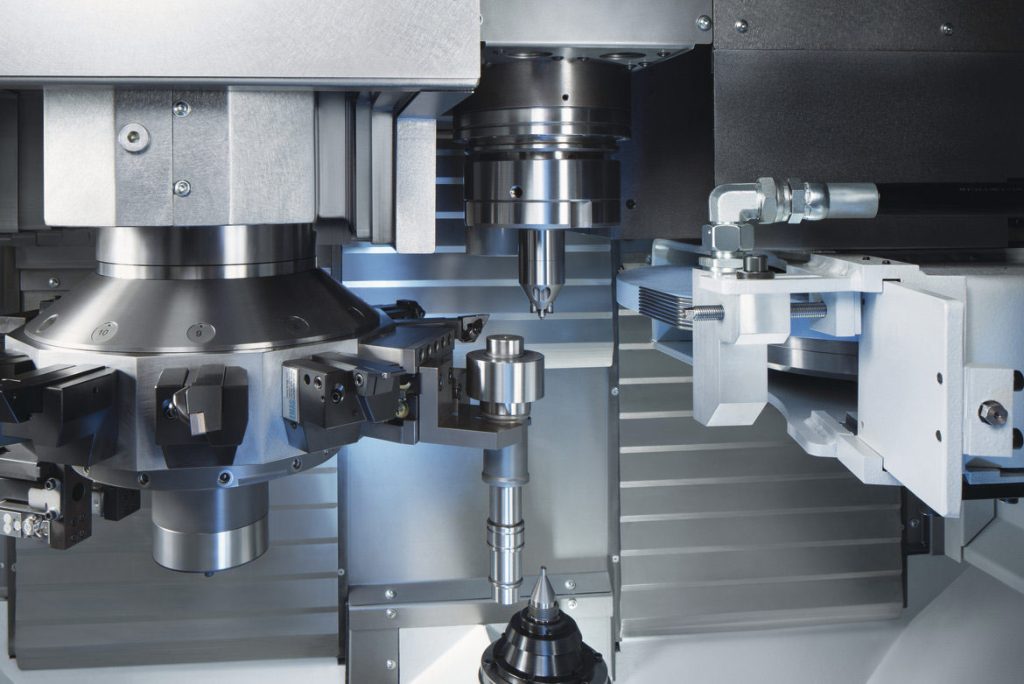
Close-up of the VT 4’s integrated workpiece grippers transferring raw parts into and out of the machining area. The built-in automation reduces handling time, increases throughput and eliminates the need for external loading systems.
Q: If someone already has a production line with other machines, can a VT 4 be added in?
David: Absolutely. Even if your line includes other brands, you can plug the VT 4 into the workflow. We’ll help you figure out how to feed parts in and out – whether that’s conveyors, robots or something custom. Integration isn’t a roadblock.
Q: You mentioned the VT 4. What’s the VT 200?
David: It’s basically the same machine. The only difference is the control system – the VT 4 runs on Fanuc, the VT 200 on Siemens. Everything else – the size, the turrets, the automation – is identical.
Q: Let’s talk dollars. Is this machine competitively priced?
David: Yes. We’ve been very intentional about pricing. When you factor in that you’re eliminating secondary machines and extra setups, the VT 4 often comes out ahead – even compared to the basic 4-axis lathes.
Q: Lead times are always a concern. How quickly can someone get this machine?
David: We’ve got stock machines ready to go, and even custom setups don’t take as long as you’d think. Lead times vary depending on the process, but we’re turning them around fast. Just reach out – we can give you specifics.
Q: What about Industry 4.0? Is this machine IoT-ready?
David: Yep – right out of the box. The VT 4 and VT 200 come equipped with EDNA, our IoT software platform. You can monitor machine health, track performance, even predict maintenance before something breaks. Our customers are seeing productivity bumps over 10% just from using the data. And setup is super straightforward.
Final thoughts:
If you’re in the shaft manufacturing game, and you’re feeling the squeeze – on space, time, people or performance – the VT 4 might be exactly what you need. It’s fast, precise, compact and smart. And it’s ready to get to work.
Contact David, or your regional sales manager for more information on the VT 4 or other EMAG machine tools.