Modern production systems are a key factor for the competitiveness of manufacturing companies. For high-quality cylindrical grinding machines, a comprehensive modernization of existing systems can be an economically interesting alternative to purchasing new equipment. CNC-Technik Weiss GmbH, part of the EMAG Group since 2019, specializes in retrofitting Karstens cylindrical grinding machines. The Neckartailfingen–based company has decades of experience in overhauling and modernizing these precision machines. In an interview with Andreas Holstein, Plant Manager at EMAG Weiss, we were able to talk about the technical possibilities and economic aspects of retrofitting.
How do you define the term retrofit in the context of machine tools?
By retrofit, we mean the modernization or retooling of older machines that are no longer in production. This includes both mechanical and control technology components. This is to be distinguished from upgrades, where existing systems are expanded in terms of functionality or safety technology.
What are the main reasons for a retrofit?
One of the main reasons is often outdated control and drive technology for which spare parts are no longer available. Added to this are worn mechanical components such as guides or inadequate machine geometry. An important economic aspect is that the investment for a retrofit is around 15 to 30 percent lower than the cost of a comparable new machine. In addition, the safety of the machine is improved and brought up to leading edge technology. All retrofitted machines are also CE-compliant.
How does the retrofit process actually work?
First, we carry out a detailed inventory of the machine at the customer’s premises. Based on this, we discuss the options for reworking the individual assemblies and prepare a scalable, transparent quotation. Depending on the scope, the conversion is carried out at our premises or at the customer’s facility. The modernized components of the overhauled machine reach the level of a new machine.
What accuracy do you achieve after a retrofit?
We are guided by DIN 8630 for cylindrical grinding machines. For example, we achieve concentricity of 0.5 micrometers or better for workpiece spindles. After the retrofit, the machine geometry and accuracy correspond to the level of a new machine.
How long does a typical retrofit project take?
Usually between 12 and 16 weeks, depending on the scope. As we have over 60 basic machines of all Karstens series in stock, we can often use an identical machine as a foundation. The customer can then continue production on their old machine until it is replaced. This reduces the downtime to around two days.
How important is energy efficiency in retrofitting?
We use energy-efficient components throughout. The grinding spindle motors comply with efficiency class IE4 and are operated with regenerative frequency converters. For machine cooling, we use room-controlled air conditioning units that only regulate by a delta to the room temperature. Hydraulic pumps work with an accumulator charging circuit and, therefore, do not run permanently. Machines with hydraulics are retooled to servomotors and are then free of hydraulics.
Can you introduce us to various retrofit projects from your portfolio?
One very impressive example is the previously mentioned retrofit of a Karstens K33 for an automotive supplier. The machine makes steering pinions for electric power steering systems. With the addition of an integrated gantry loader, we achieve a chip-to-chip time of just 19 seconds – faster than comparable new machines on the market.
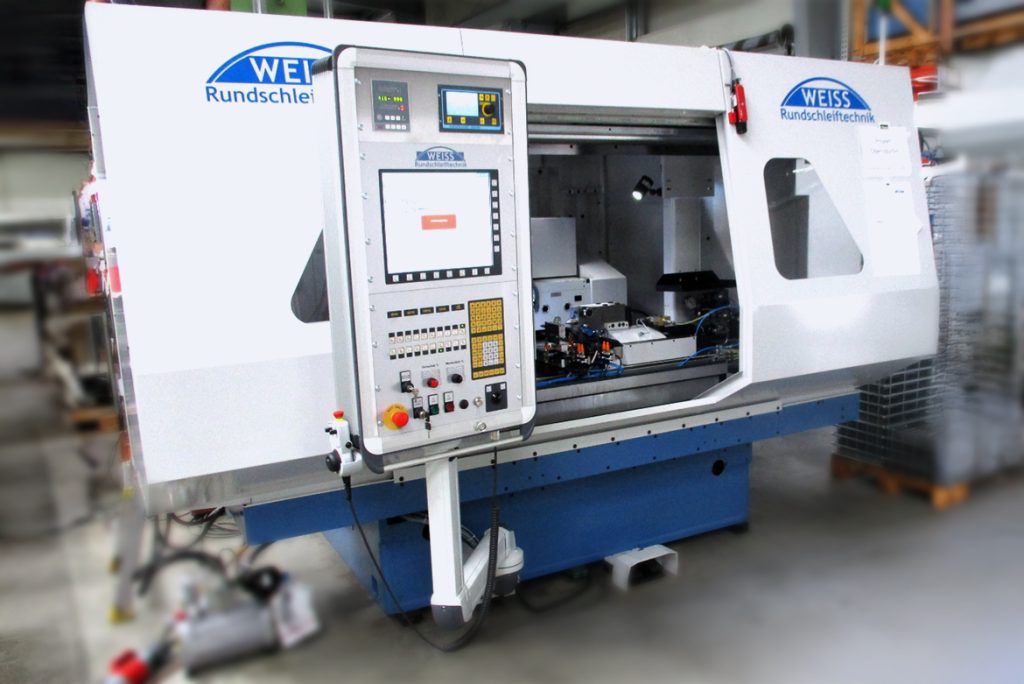
Karstens K33 cylindrical grinding machine after complete retrofit: Equipped with modern CNC control, full enclosure and integrated loading system.
Another interesting project was the complete retrofit of a Karstens K11. Here we upgraded the machine to a W 11-Advanced, with ball screw drive in the Z-axis, modern motion control and touch operation. The micrometer-precise infeed and automatic Z-axis free movement were particularly important in this case.
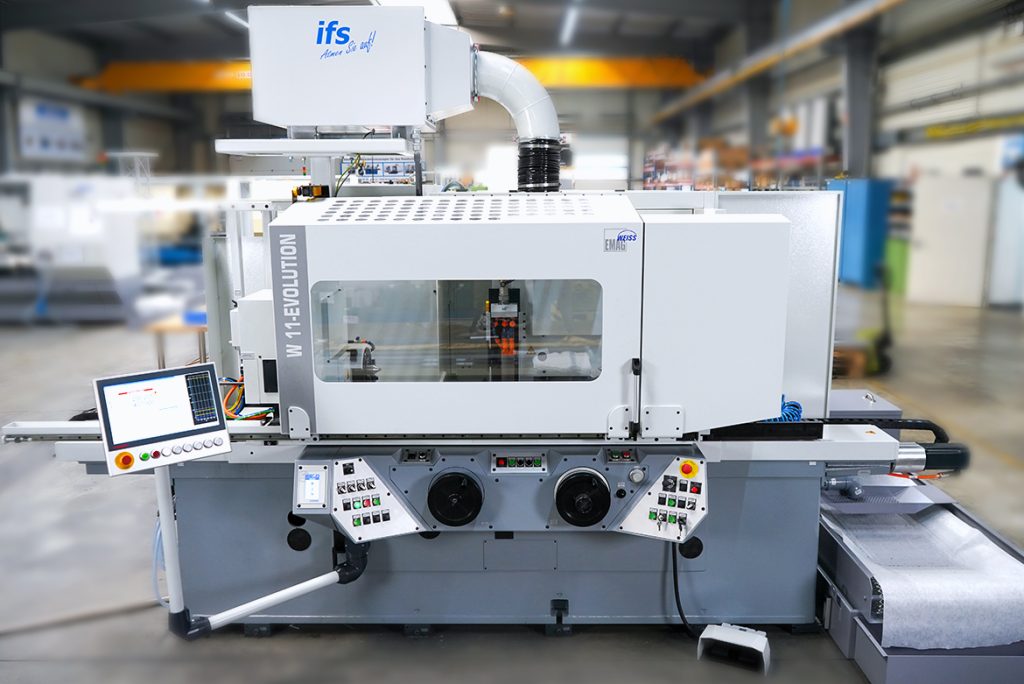
Retrofit universal cylindrical grinding machine K 11 with state-of-the-art control technology: Precision infeed thanks to ball screw drive in the Z-axis and user-friendly touch operation.
We carried out an extensive upgrade on a Karstens K19. The machine was equipped with a stepless B-axis and active longitudinal positioning on the grinding head. By converting the X and Z axes with servo motors and ball screws, external and internal grinding, including taper grinding, is now possible in a single setup.
Are there also more cost-effective retrofit variants?
Yes, a good example is the retrofit of a Karstens K56. Here we had a machine that was still mechanically very good but had control problems. In such cases, we offer a “light retrofit” in which we concentrated on replacing the control system and overhauling the most important mechanical assemblies. This is a very interesting economic option for customers whose machines are still in good mechanical condition.
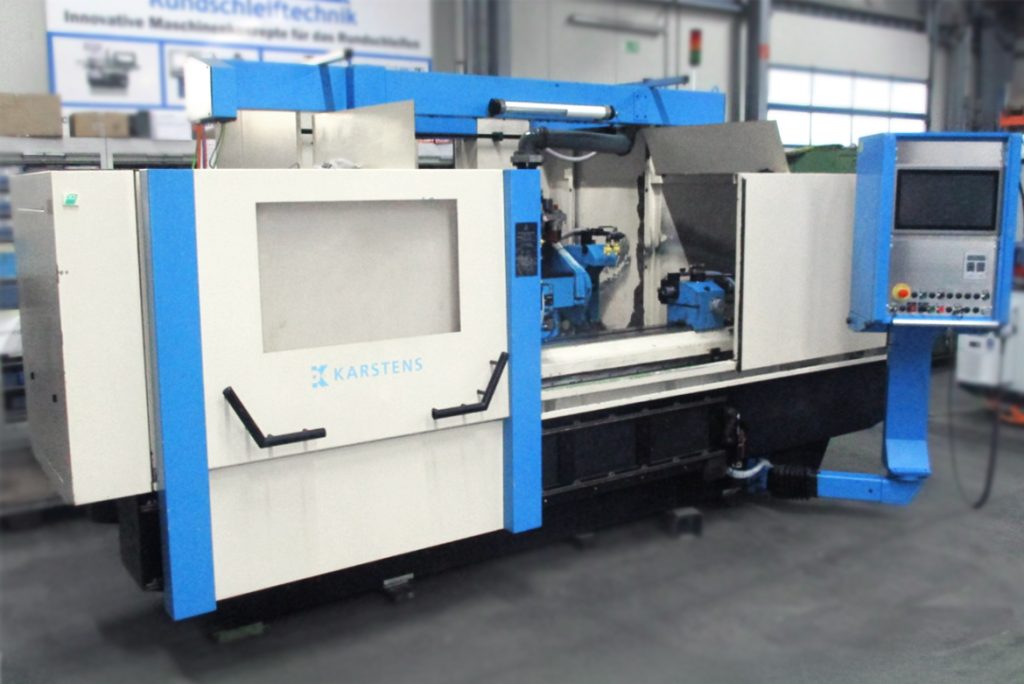
Cost-efficient modernization of a Karstens K56: The machine in good mechanical condition received a new control system and a targeted overhaul of the core components.
What about the supply of spare parts for retrofit machines?
The supply of spare parts for retrofit machines is generally guaranteed in the long term, as outdated control and drive components are replaced with modern, current technology as part of the retrofit. In addition, we offer comprehensive service and still have spare parts in stock even for very old machines. In this way, we ensure that your machine can be operated reliably over its entire service life.