When it comes to cylindrical grinding, there’s no shortage of strong options – and a few persistent myths. At its core, cylindrical grinding is one of the most precise and consistent methods of finishing round parts. Yet, many manufacturers hesitate to explore it further, often due to outdated assumptions or misconceptions. Let’s take a closer look at some of the most common myths and why they don’t hold up today – especially with machines like EMAG’s WPG 7 on the market.
“CNC is Always better Than Manual Grinding”
There’s no doubt that CNC grinding brings repeatability and automation to the table – but that doesn’t mean manual grinding is obsolete. In fact, experienced machinists can often achieve impressive results with manual machines, especially for low-volume work or one-off components that demand hands-on finesse. Manual grinding offers flexibility and tactile control that some applications still require.
The real takeaway? It’s not about choosing between CNC or manual – it’s about having the right tool for the job. A machine like the WPG 7 is built with this in mind: while fully CNC-controlled, it’s designed to offer easy operator access and intuitive setup, making it ideal for both seasoned manual grinders and shops ready to transition to more automated processes.
“Automation is Only for High Volume”
This myth is especially common in small to mid-sized shops, where automation is often seen as costly or overkill. But with today’s modular grinding platforms, automation isn’t an all-or-nothing commitment. It can start with something simple as programmable workholding or automated part loading.
The WPG 7 is a prime example – it’s and OD cylindrical grinding machine that can be equipped with automation options, but it also performs great as a stand-alone unit. Shops can start manual and scale up when the workflow demands it. In many cases, even limited automation can significantly reduce cycle times and free up skilled labor for more critical tasks.
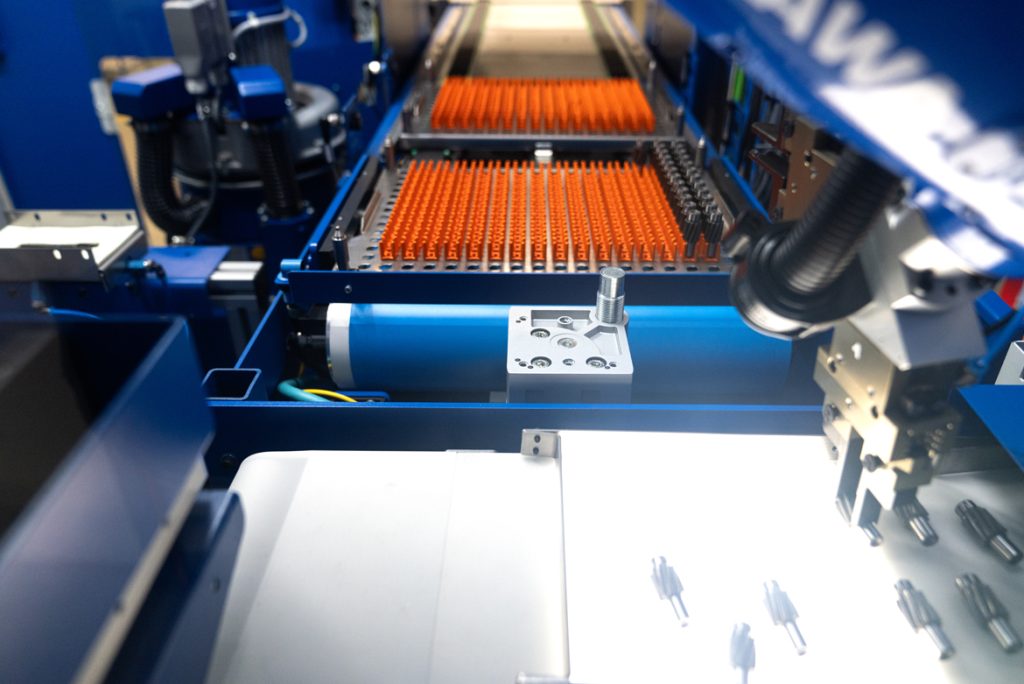
The WPG 7 cylindrical grinding machine offers modular automation options – from simple loading to full robotic integration – ideal for growing shops.
“Grinding Machines Take Too Long to Set Up”
While it’s true that traditional grinding setups could be time-consuming, modern cylindrical grinding technology has come a long way. Machines like the WPG 7 are engineered for fast changeovers, with a compact footprint and intelligent controls that make setup more intuitive than ever.
Thanks to features like quick-change tooling, user-friendly interfaces and minimal mechanical adjustments, shops can move from part to part without excessive downtime. For job shops or OEMs that handle multiple part families, this can mean the difference between a profitable run and wasted hours.
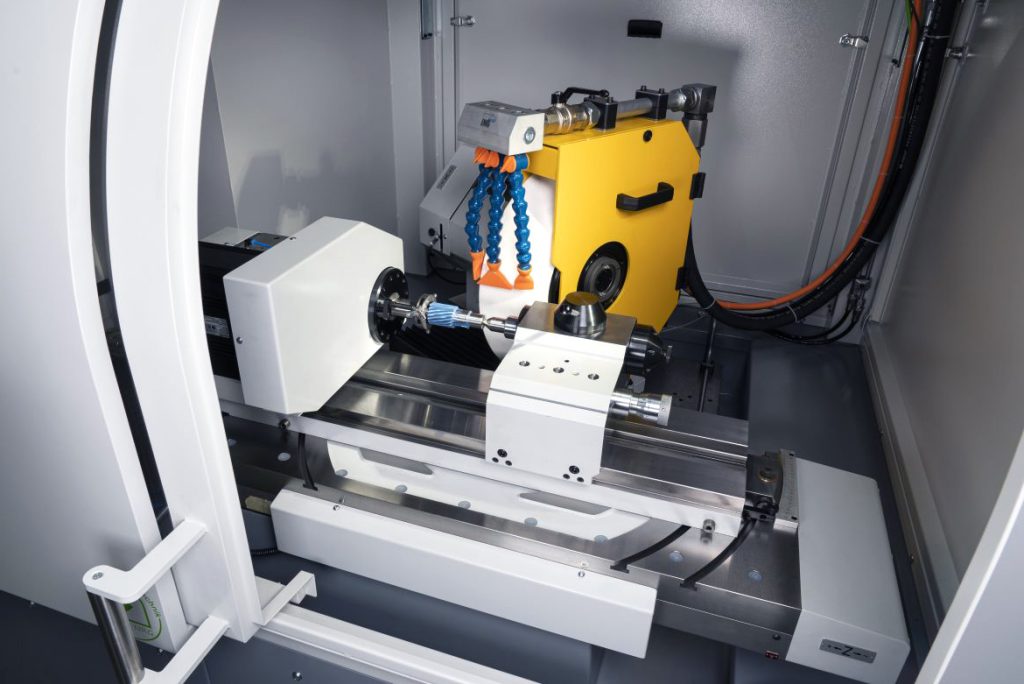
The WPG 7 grinding machine features a large front door, supporting fast changeovers and intuitive operator access.
Clearing the Air – and Grinding Smarter
Cylindrical grinding doesn’t have to be intimidating, expensive or inefficient. By challenging outdated assumptions, manufacturers can unlock new efficiencies and capabilities – whether they’re producing hundreds of parts or just a handful.
The bottom line? The right grinding machine doesn’t just cut – it fits. And with machines like the WPG 7 offering a blend of flexibility, automation-readiness and quick setup, there’s never been a better time to rethink what cylindrical grinding can do for your shop.
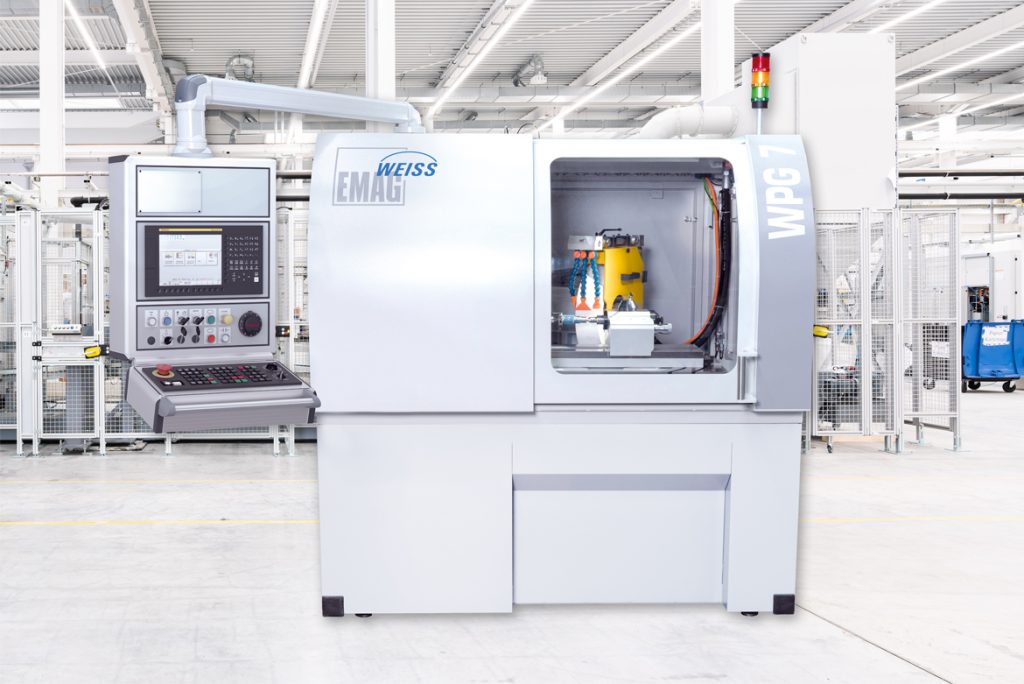
WPG 7 cylindrical grinding machine designed for flexible, efficient machining – ideal for both small batches and high-mix production.