The requirements for shaft machining have changed significantly in recent years. Increasing variant diversity combined with decreasing batches present manufacturing companies with new challenges. With the VTC 100 GT EMAG is presenting a machine in which the turning, grinding, drilling and milling processes using a combined lifetool. In the following interview, Marina Manger, Technical Sales at the Grinding business unit, explains how this technology integration makes production more efficient and what concrete benefits users can derive from it.
Ms. Manger, the VTC 100 GT combines various manufacturing processes. What specific advantages does this combination offer the user and can you give us some examples?
The VTC 100 GT enables complete machining in a single setup. This means that we can perform turning, grinding, drilling etc., in one work area. Allowances can be reduced under certain circumstances, as no reclamping errors have to be taken into account. Technological limits are avoided.
A very good example is the machining of rotor shafts. These are the heart of the electric drive and place high demands on the machining process. Bearing and sealing ring seats, the rotor, ring grooves and face shoulders are machined in a single setup. A grinding process is often prescribed for the hard machining of the bearing seats. This is pre-turned to achieve a constant grinding allowance. The adjacent face shoulders do not require a grinding process, but are turned. The sealing ring seat is also pre-turned and then ground. A swirl-free Rz of 1–3 µm is often required here. The rotor is also turned first and then ground. The required drawing tolerances are IT6. Compliance with the tolerances can be ensured using the in-process measuring head.
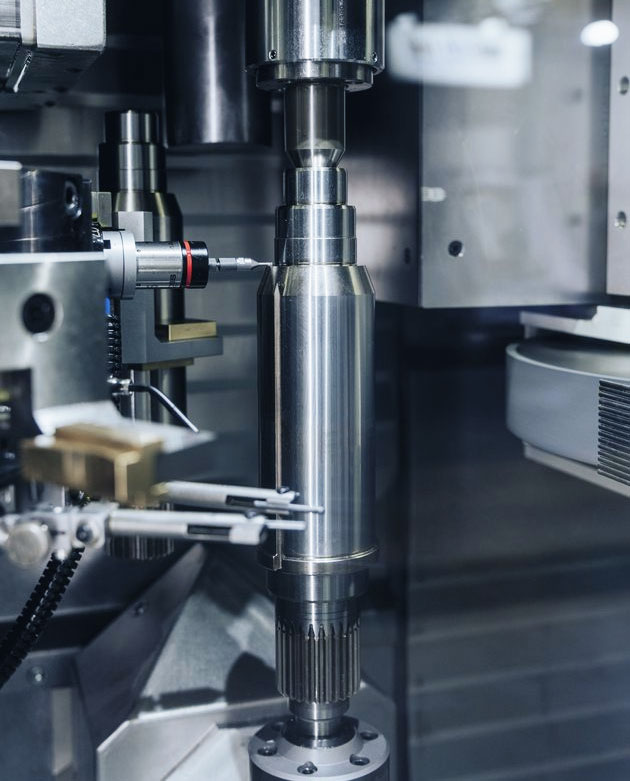
Vertical work area of the VTC 100 GT with clamped E-rotor shaft. The vertical arrangement enables optimum chip fall. The picture shows the measuring head for probing the axial position of the rotor shaft and the in-process measuring head.
The following is a completely different example: Joint housings are to be turned and ground. The machining requirements are similar to those presented for the rotor shaft.
The annual quantity of 500,000 workpieces requires a rethink. Machining processes must be completed in parallel. This was solved with a VT 100 as a pure turning machine, which was connected to a VTC 100 GT via Track Motion. The turret of the VTC 100 GT was equipped with two grippers for this purpose. This enables a quick change between raw and finished parts in the machine.
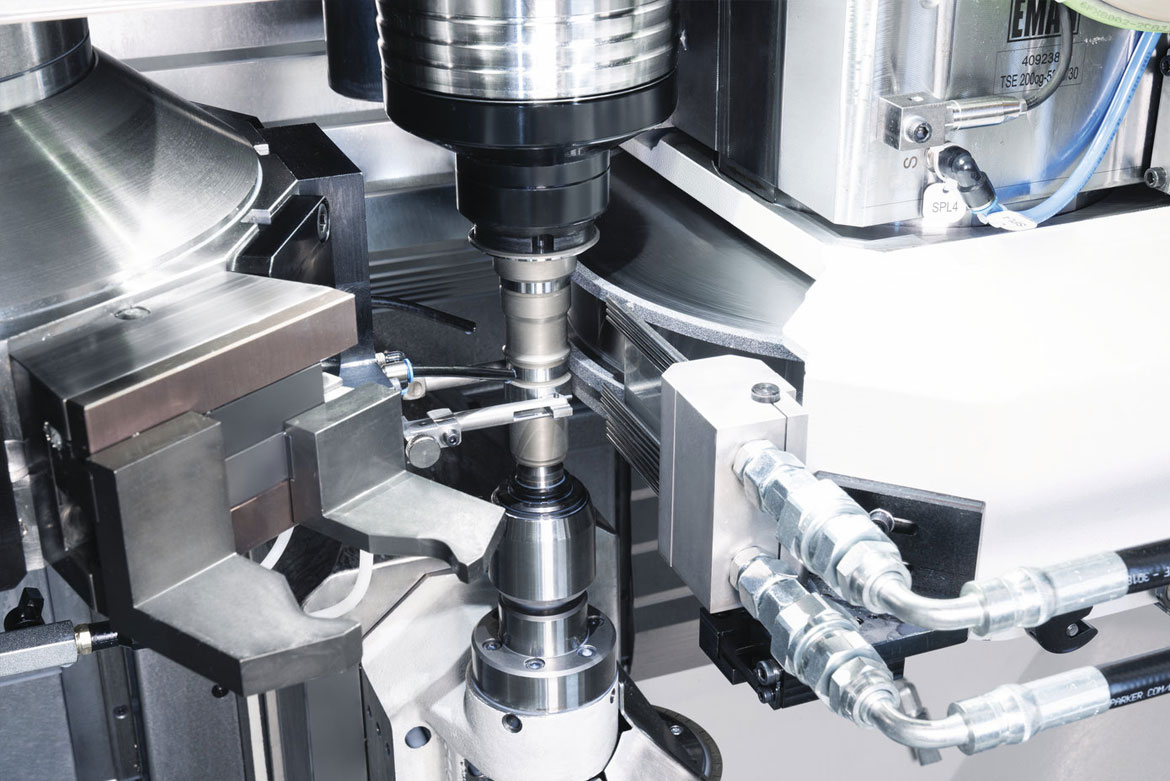
Joint housing on the VTC 100 GT: The machine achieves a cycle time of 36 seconds with two grinding operations, one of which is twist-free. A coaxiality of the two seats of ≤ 0.005 mm with a center roughness value of Ra 0.2 – 0.6 µm.
Productivity plays a central role in manufacturing processes. How does the VTC 100 GT address this aspect?
Automated loading and unloading via the turret is a key productivity factor. The machine also has integrated raw and finished part storage. The vertical design ensures optimum chip fall, which increases process reliability and minimizes downtimes.

The turret of the VTC 100 GT performs the loading and unloading function as well as the tool receptor. The gripper system transports the workpieces between the integrated storage and the working position, eliminating the need for additional handling systems.
How does the machine support users with frequently changing machining requirements?
The machine has been consistently designed for short set-up times. Thanks to the excellent accessibility, tool changes and set-up processes can be carried out quickly. This enables our customers to manufacture economically even with small batches and to react flexibly to new machining requirements.
Many production halls have limited floor space. How does the VTC 100 GT fit in here?
A big advantage of the VTC 100 GT is its small footprint. Despite its extensive functionality and integrated workpiece storage, the VTC 100 GT has a very compact design. Connections to additional automation is trouble-free.
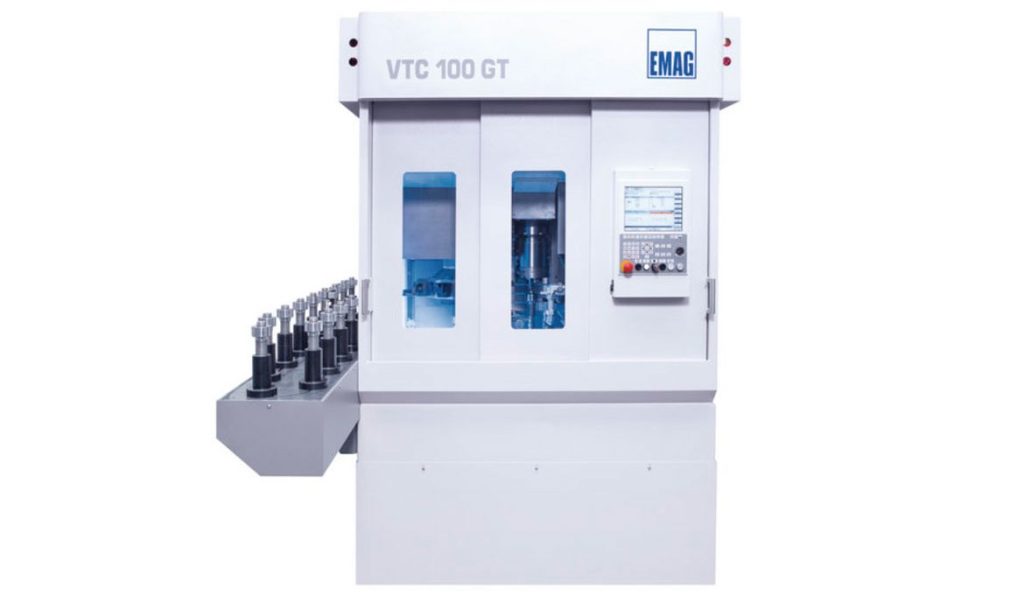
The VTC 100 GT combines grinding, hard turning and skiving in one compact unit. The vertical design and integrated storage systems minimize the footprint in production, while providing optimum accessibility for set-up processes.