At its core, cylindrical grinding is all about precision. This process involves machining the external or internal surface of a cylindrical workpiece using grinding machines equipped with rotating wheels. These machines remove material through abrasion, delivering exact dimensions and smooth finishes. Whether it’s external or internal grinding – or even a mix of both – this technique plays a pivotal role in producing high-quality parts for industries like automotive, aerospace and more.
In today’s fast-paced manufacturing world, having the right CNC cylindrical grinder can make all the difference. The right machine saves time, reduces costs, and improves product quality – whether you’re handling small batch production runs, mass production or a variety of tasks. But with so many options out there, how do you decide which one is best for your needs? This guide will walk you through the key factors to consider.
1. Size Matters: Compact vs. Full-Scale Solutions
One of the first considerations is the machine’s size and footprint. For facilities with limited floor space, compact solutions like the WPG 7 external cylindrical grinder offer a high degree of functionality without consuming excessive space. These machines integrate all critical components, including the electrical cabinet, cooling system, and lubrication system, within the housing for a streamlined design. Compact grinders are ideal for the external machining of smaller components, delivering precision without sacrificing valuable workspace.
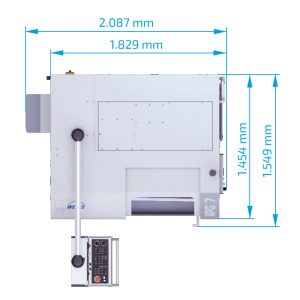
Dimensions of the machine at a glance
2. Flexibility in Loading: Automation vs. Manual Operation
The choice between automated and manual loading depends on your production requirements.
- Manual Loading: Ideal for smaller batches and prototype. These setups allow operators to quickly adjust and fine-tune processes, offering greater control over one-off parts.
- Automated Loading: Best for medium to large production runs. Machines with integrated gantry systems, such as those developed by EMAG, streamline operations by reducing cycle times and ensuring consistent part handling. Automated systems can be customized to connect with chain conveyors, pallet circulators, or robots, enhancing productivity and scalability.
3. Grinding Configurations: Straight vs. Angular Plunge-Cut
OD grinders typically offer configurations for straight or angular plunge-cut grinding. It’s essential to select the appropriate configuration based on your production needs:
- Straight Plunge-Cut Grinding: Suitable for components requiring linear grinding operations.
- Angular Plunge-Cut Grinding: Allows for angled profiles and more complex geometries. This setup often involves a fixed grinding head and specific profiling of grinding wheels to match the task.
Understanding your product’s geometry and surface finish requirements will help you decide on the right configuration.
4. Advanced Monitoring and Control Systems
Modern grinding machines come equipped with advanced monitoring and control systems that ensure process reliability and precision. Look for features like:
- In-Process Measurement System: Continuous diameter monitoring ensures consistent tolerances, even during high-speed operations.
- GAP and Crash Control: These features prevent damage to both the machine and the workpiece by detecting potential collisions early.
- Automatic Balancing System: Ensure vibration-free operations for improved surface quality and machine longevity.
These features not only enhance the quality of your output but also reduce downtime and maintenance needs.
5. Ease of Operation: Simplify Precision, CNC Control and Programming
User-friendly interfaces and intuitive programming are essential, especially when transitions between different parts or tasks. Machines with CNC control, such as those featuring FANUC technology, simplify the input of grinding parameters and allow operators to switch between cycles quickly. Dialog-based programming interfaces reduce the learning curve, enabling operators to achieve optimal results with minimal training.
Tailored Solutions for Unique Tasks
If your production involves specialized tasks, look for grinders that offer customizable options. Features like profiling capabilities for grinding wheels, adjustable head angles, and modular designs can significantly enhance the machine’s adaptability. The ability to tailor your machine to specific tasks ensures it remains versatile enough to handle evolving production demands.
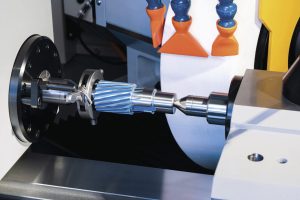
WPG 7 Workarea
6. Durability and Heat Management
Grinding machines endure intense mechanical and thermal stresses, so their design must support long-term reliability. Key factors include:
- Rigid Machine Construction: Ensures stability during operations minimizing vibrations and inaccuracies.
- Heat Dissipation: Effective heat transfer mechanisms reduce thermal distortion, maintaining micrometer-level precision over extended periods.
7. Quick Installation and Setup
Time is money in manufacturing, so machines that offer rapid setup and minimal downtime are a significant advantage. Compact solutions like the WPG 7 can be installed in under four hours, requiring only power and compressed air connections. This plug-and-play capability minimizes disruption to your operations. It’s easy to deploy and easy to integrate into new or existing processes.
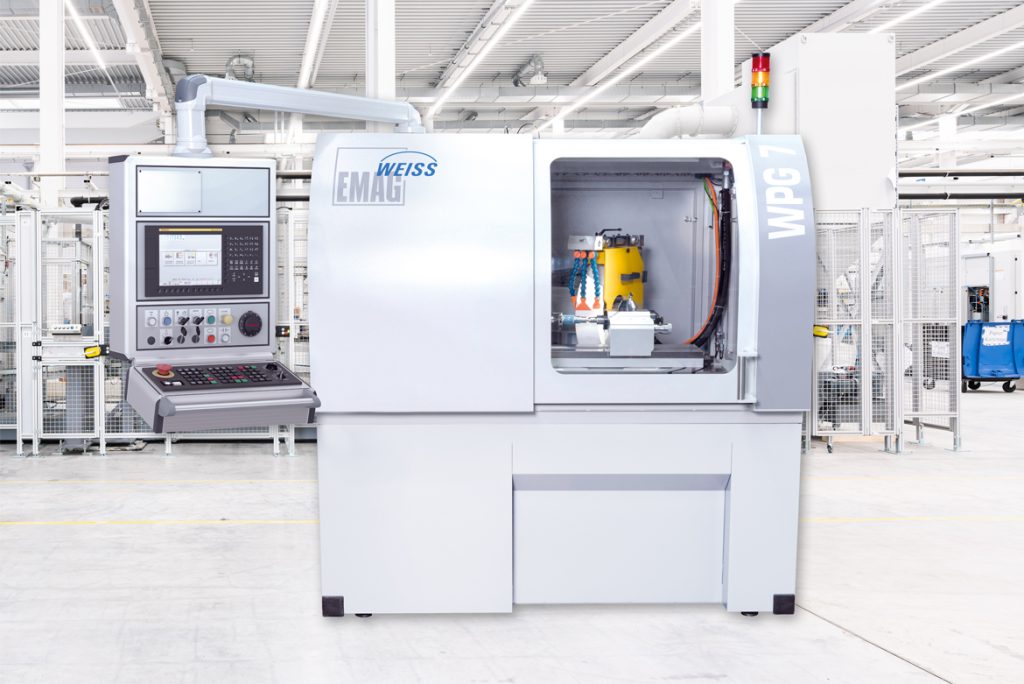
O.D. Cylindrical Grinding Machine
Conclusion: Investing in the Right Cylindrical CNC Grinder
Choosing the right CNC grinder isn’t just about meeting immediate needs; it’s about future-proofing your operations. Compact designs, automation options, advanced control systems, and tailored configurations make OD grinders indispensable in today’s manufacturing landscape. Whether you’re producing small batches or scaling up to mass production, investing in the right machine will enhance your efficiency, precision, and adaptability for years to come.
Take the time to evaluate your specific requirements and remember that the right grinder isn’t just a machine – it’s a strategic asset for your manufacturing business.