Whether for the development of new oil fields or the reliable extraction of natural gas, pipes and couplings are among the most critical components in the drilling process. They carry immense loads, transmit high torques and must remain permanently sealed.
But what makes a perfect threaded connection? What challenges are involved in manufacturing OCTG components – and why are specially designed machine tools so essential? We explore these questions with Udo Lauer, OCTG specialist at EMAG, who shares his insights into the technical world of pipe and coupling machining.
Mr. Lauer, can you start by explaining what OCTG components are and their role in drilling operations?
OCTG stands for “Oil Country Tubular Goods”. This refers to pipes and couplings specially manufactured for use in oil and gas drilling operations. These components join together to form a pipe string that is used to drill the well or later serve for stabilization and production. OCTG components are essential to the safety and efficiency of any drilling operation.
Why are threaded connections so important for OCTG components?
Threaded connections must withstand extreme mechanical stress. They support the entire weight of the pipe string, transmit torque and must endure high pressures and sometimes corrosive environments. Even the smallest inaccuracies during production can cause failures – with significant consequences. This is why our focus at EMAG is on ultra-precise thread machining.
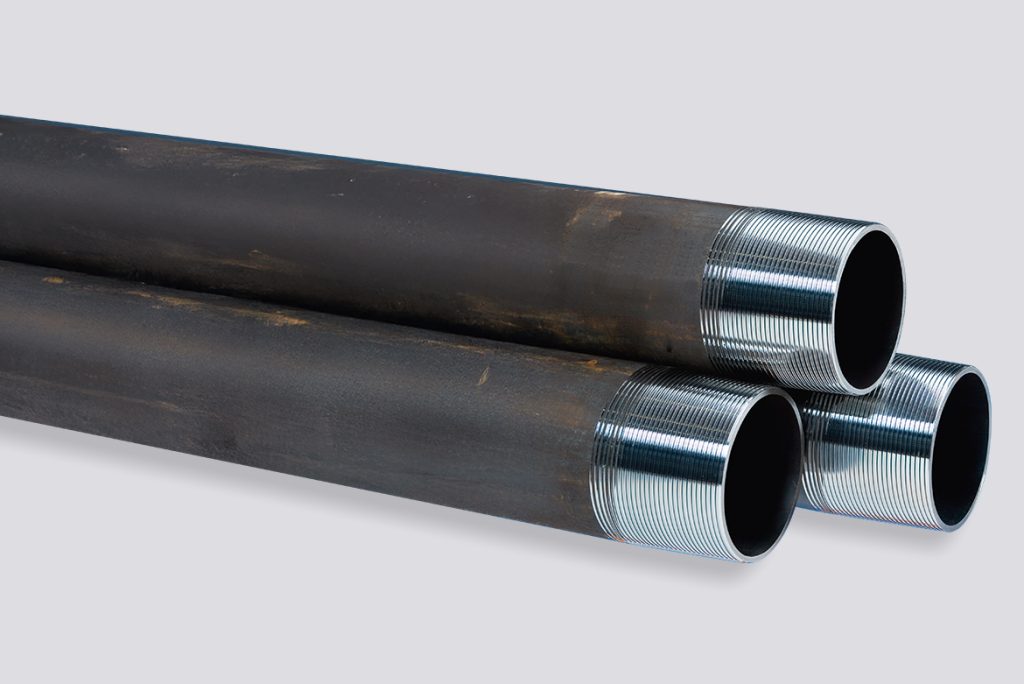
Tube ends with precision machined threaded connections – ideal for API, GOST integral and premium threads
What role do EMAG machines play in the production of pipes and couplings?
EMAG machines such as the USC 21 and VSC 500 are specially enigneered for these applications. The USC 21 enables complete-machining of tube ends – from standard API and GOST threads to complex integral and premium threads. The VSC series is tailored for machining couplings that connect the individual pipes. Both machines offer exceptional stability, integrated automation and excellent process reliability.
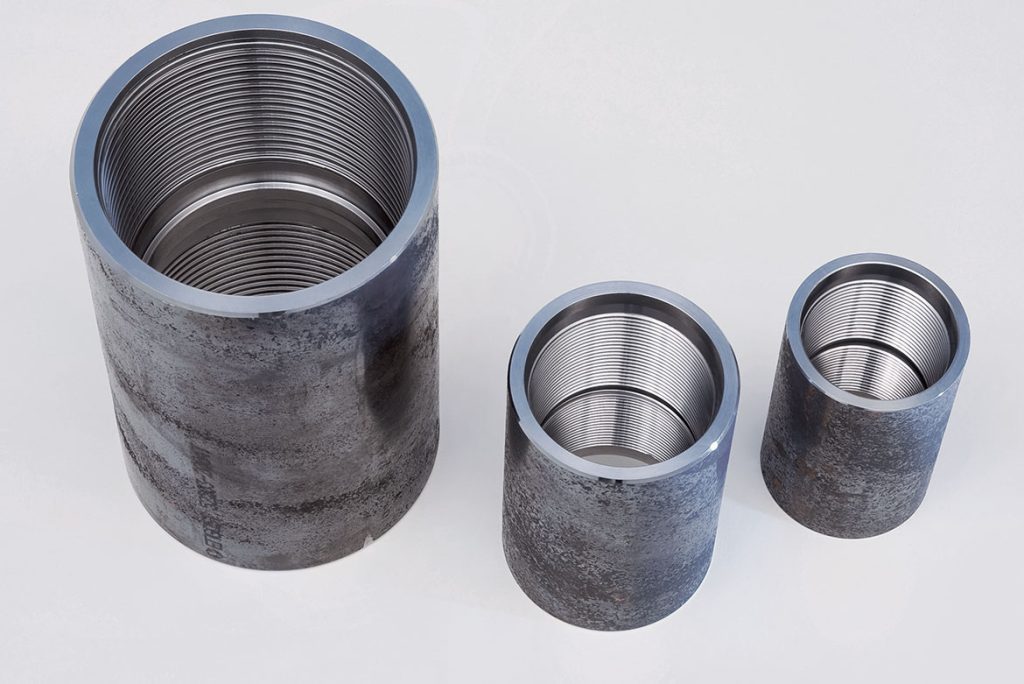
OCTG couplings with high-precision threaded connections, manufactured on EMAG VSC vertical turning machines
What are the specific advantages of a machine like the USC 21?
The USC 21 is both highly flexible and extremely productive. It supports simultaneous machining with up to six axes and features powerful direct drives, delivering maximum accuracy. Its modular design reduces cycle times and boosts productivity. For our customers, this means considerable advantages in quality, reliability and cost-efficiency.
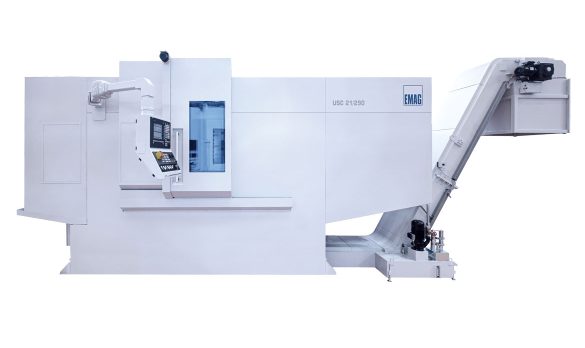
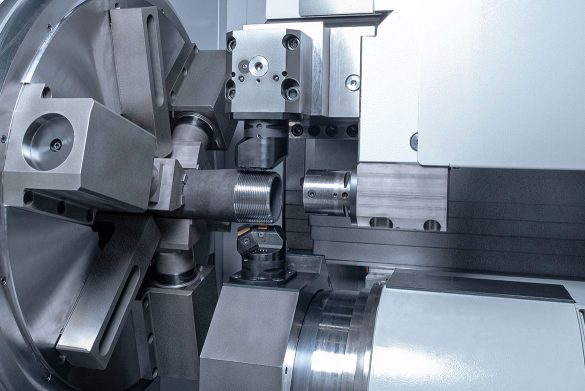
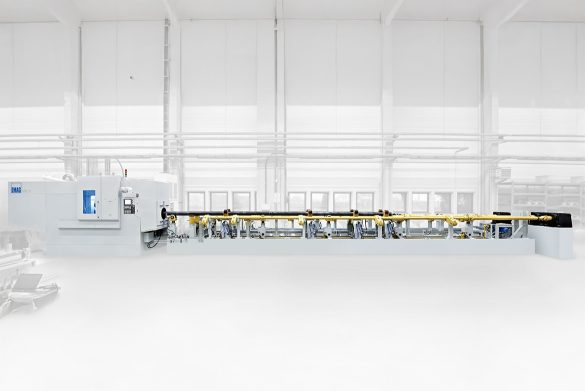
What does a typical manufacturing system that EMAG supplies for couplings look like?
We offer complete manufacturing systems from a single source, including the link-up of several machines if required – for example, socket production systems with VSC machines. These systems include automated feeding systems, integrated quality controls and cleaning processes.
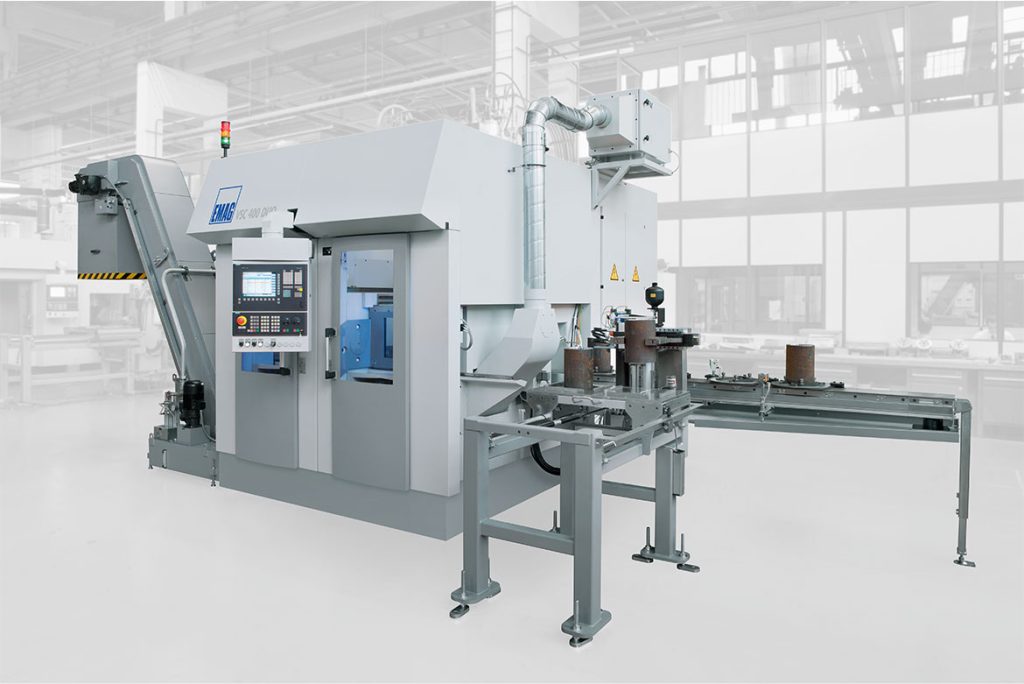
Fully automatic production system based on VSC vertical turning machines for the complete-machining of couplings
Mr. Lauer, what advice would you give to customers considering OCTG production?
When investing in OCTG production, it’s essential to prioritize long-term process reliability and quality. Requirements for integral and premium connections are particularly demanding. I always recommend choosing machines and solutions that are purpose-built for OCTG manufacturing, as ours are at EMAG. The true value isn’t just in the machine – it’s the tailored system solution, we provide to meet each customer’s unique production needs.