EMAG recently introduced the USC 850 CNC universal turning machine – a precision and powerful turning machine for large workpieces. In the following interview, Bernd Scheschy, Technical Sales in the Turning Business Unit, explains the technical features of this machine.
Mr. Scheschy, the EMAG USC 850 has been announced as a new CNC universal turning machine. What characterizes this machine and for which areas of application was it developed?
The USC 850 is a universal lathe that has been specially developed for the precision and efficient machining of large turned parts. We are talking about a machine that impresses with its robust design, state-of-the-art CNC control technology and excellent machining accuracy. In concrete terms, this means that with a maximum turning diameter of 600 mm and a turning length of 1,850 mm, the USC 850 offers exceptional machining flexibility. Even workpieces weighing up to 3,000 kg can be securely clamped and machined with the help of the tailstock. The manufacturing accuracy is in the IT6 tolerance range and thus meets the highest demands for dimensional accuracy and surface finish. The machine was developed primarily for users in demanding industries: Automotive suppliers, aerospace or general mechanical engineering – wherever large rotationally symmetrical precision parts need to be produced economically. In short: The USC 850 combines high precision and productivity when machining large workpieces.
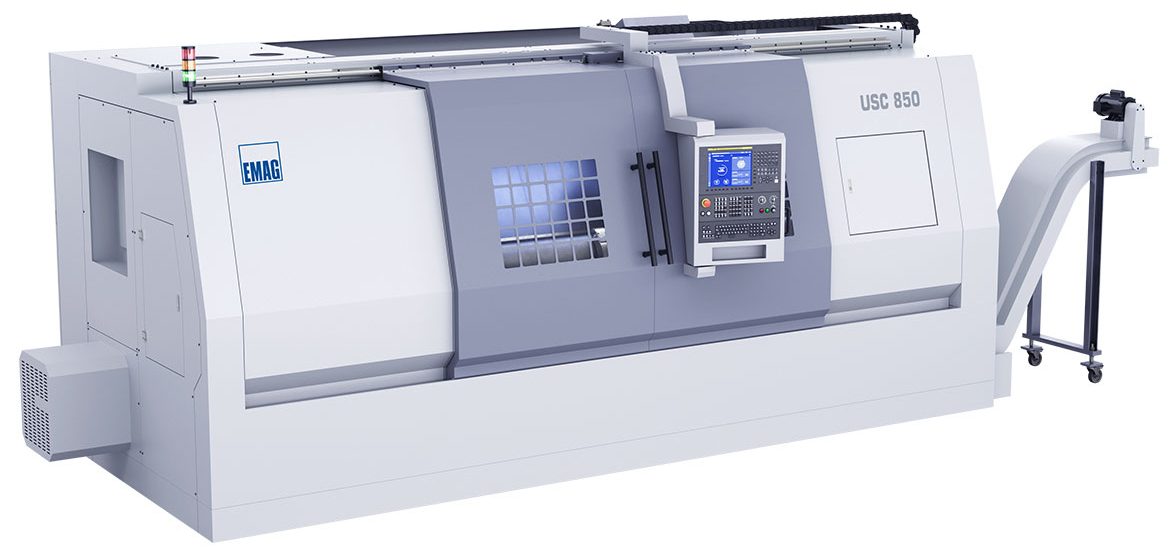
Exterior view of the USC 850 universal lathe with closed housing, CNC control panel and stable machine structure for demanding machining tasks.
Can you tell us something about the machine design of the USC 850? How does the design ensure that even very large workpieces can be machined with precision?
A key feature of the USC 850 is the particularly stable machine design. The machine base has a 60° inclined bed design. This inclined bed design – together with the solid substructure – ensures exceptionally high static and dynamic rigidity and optimal vibration damping. Vibrations during machining are thus reduced to a minimum, which is extremely important for consistently high production quality. We also use high-quality cast iron. The bed, carriage and other load-bearing components are made of cast iron that has been stress-relieved twice. The double stress-relief annealing of the cast iron virtually eliminates material-related deformations, so that the machine remains dimensionally accurate over the long term. Another point concerns the guideways: Hardened flat guides with large contact surfaces are used instead of roller guides. These flat guides direct the axes with precision and virtually no-wear, even under high loads. The overall result is a rigid and robustly damped base body. For the user, this means that the machine remains smooth even with heavy workpieces and demanding cuts and guarantees maximum precision.
Keyword main spindle – what features does the spindle of the USC 850 have and what does this mean for the cutting performance?
The main spindle is another decisive factor in the performance of the USC 850. We have installed a high-performance spindle unit here that sets standards in terms of both performance and precision. Specifically, the spindle delivers a continuous output of 30 kW and can even deliver 37 kW for short periods (30 minutes). This means that even difficult-to-machine materials can be machined efficiently. The spindle is driven by a belt drive with a two-stage transmission. This means that there are two speed ranges: a lower gear from 10 to 850 min-¹ and an upper gear from 30 to 1,500 min-¹. This means that a very high torque is available in the lower range, while the speed required for smaller diameters can be achieved in the upper range – all in all, an optimal adaptation to different machining requirements. The spindle bearing is also important: We use a combination of precision angular contact ball bearings and double-row cylindrical roller bearings. This bearing combination gives the spindle excellent rigidity and ensures precision concentricity even under the highest loads. The entire spindle unit is assembled with the utmost care, finely balanced and subjected to an optimized running-in process – resulting in concentricity accuracies in the micrometre range. In practice, this means that the workpiece runs in the spindle with minimal runout, which is crucial for the dimensional accuracy of precision sleeves or bearings, for example. The large spindle clearance of 135 mm is also worth mentioning. This means that even long bar stock can be clamped through the spindle. To summarize, the main spindle of the USC 850 offers high-performance in two speed ranges while guaranteeing maximum running accuracy – a basic requirement for the efficient machining of large workpieces.
The name universal lathe already indicates flexible machining options. What role does the turret play in the USC 850 and what additional machining is possible with it?
The turret is indeed a key to the flexibility of the USC 850. We use a BMT65 turret with twelve stations. This means that it can hold up to 12 tools and all stations are designed for driven tools. The driven tools – i.e. milling or drilling tools in the turret – reach motor speeds of up to 3,000 min-¹ and are powered by their own drive with 3.7 kW (5.5 kW for a short time). This makes it possible to perform a variety of milling and drilling operations in one setup in addition to pure turning operations. For example, cross bores, grooves, face shoulders or threads can be machined directly on the lathe without having to clamp the workpiece in a milling machine. The tool receptors in the turret are very generously dimensioned: We can use turning tools with a shank cross-section of up to 25×25 mm and boring bars or drilling tools up to Ø 50 mm. This covers a wide range of cutting tools. The internal coolant supply through the turret is particularly noteworthy. The coolant is fed directly through the turret and the tool to the cutting edge. This ensures a targeted cooling system directly at the interfaces and significantly improves both the service life of the tools and the surface finish of the workpieces. In addition, the turret has an extremely robust design and precision indexing. Even rough-machining and finishing operations can be carried out with a high degree of dimensional accuracy. A hydraulic clamping system holds the turret securely in position during machining, even with high cutting forces. Not to forget: The USC 850 has a C-axis on the spindle, which enables sensitive positioning of workpieces. The C-axis is CNC-controlled and enables exact alignment of the workpiece for milling and drilling work – it achieves a positioning accuracy of around 0.0175°. For example, surfaces or drill holes can be positioned with high angular accuracy on the circumference of a workpiece. In summary, the turret in combination with the C-axis enables complete-machining: turning, drilling, milling – all in one machine and in one setup. This saves set-up time, avoids positioning inaccuracies due to re-clamping processes and significantly increases process accuracy and cost-effectiveness.
Large and long workpieces place special demands on clamping and stability during machining. What features does the USC 850 offer for precision machining of very long or thin-walled workpieces?
For workpieces, especially if they are long and relatively thin-walled, the machine must ensure stable support to avoid vibrations or deformation. The USC 850 is ideally equipped for this. Firstly, it has a robust hydraulic tailstock. This tailstock is used to support the free end of long workpieces. The quill has a diameter of 150 mm and a stroke of 150 mm. There is an MK6 centering cone in the quill, onto which a centering tip or a rotating center punch can be placed to center the workpiece end precisely. The tailstock quill is positioned and clamped hydraulically and can be moved either via a CNC program or manually using a foot pedal. On the other hand, the machine can be equipped with a hydraulic steady rest, especially for very long or thin-walled workpieces. The steady rest is attached to the machine base and usually supports the workpiece in the middle or at a suitable point across the diameter. Our steady rests cover clamping ranges from Ø 30 mm to 245 mm.
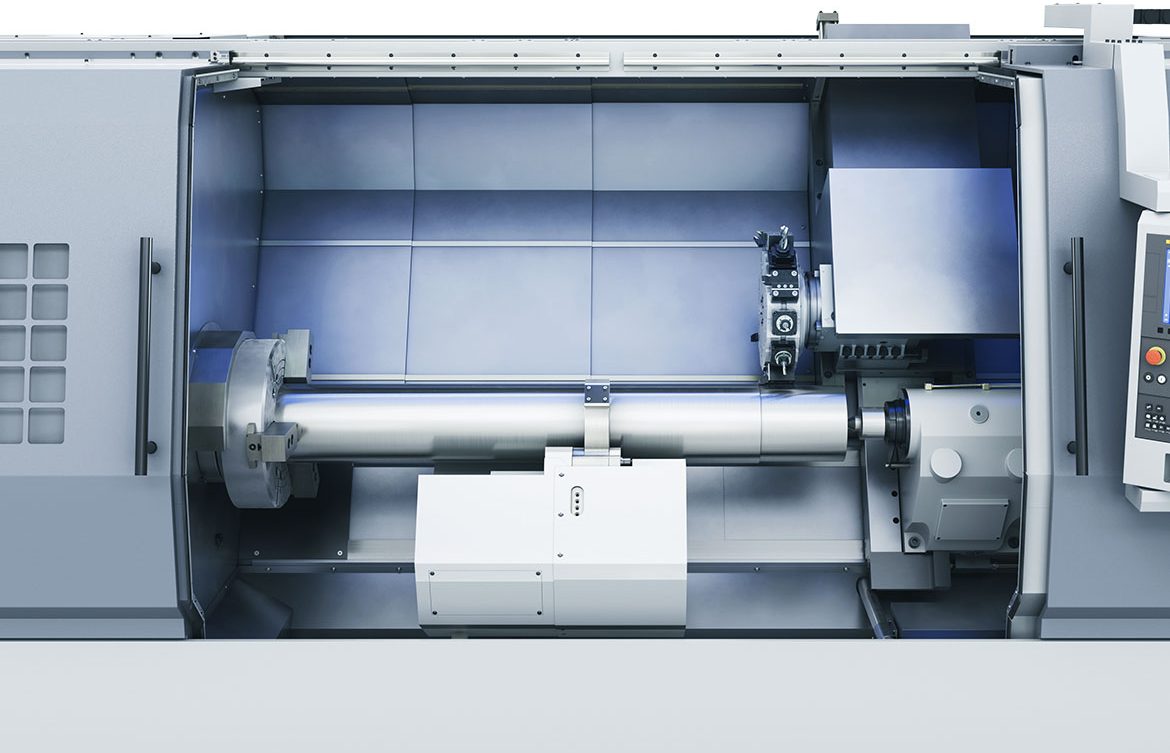
Work area of the USC 850 with robust 60° inclined bed, BMT65 turret and hydraulic tailstock for large workpieces.
Can you give us an example of a typical workpiece for which the USC 850 is particularly well suited?
One workpiece that is currently in high demand is sleeves with a diameter of 155 mm. We have developed special processes and machining technologies for this, both for external and internal machining. A 155 mm artillery shell casing is typically a relatively long, cylindrical workpiece with a comparatively thin wall thickness. Without support, such a case could vibrate under the tool pressure or bend slightly, which would impair the dimensional accuracy. By using the tailstock in combination with the steady rests, however, the workpiece is held securely at both ends (and in the middle if necessary). Vibrations are suppressed and the shape remains stable. This allows us to turn, drill and, if necessary, mill with constant precision over the entire length of the sleeve without risking ovalities or wall thickness deviations, for example. Practical experience has shown that the USC 850 really comes into its own with such tasks: Long bullet sleeves or similar components can be finish machined with high precision in one or two setups. The hydraulic clamping forces of the steady rests can be sensitively adjusted and are digitally displayed so that the contact pressure is always under control – important for clamping the workpiece firmly without deforming it.
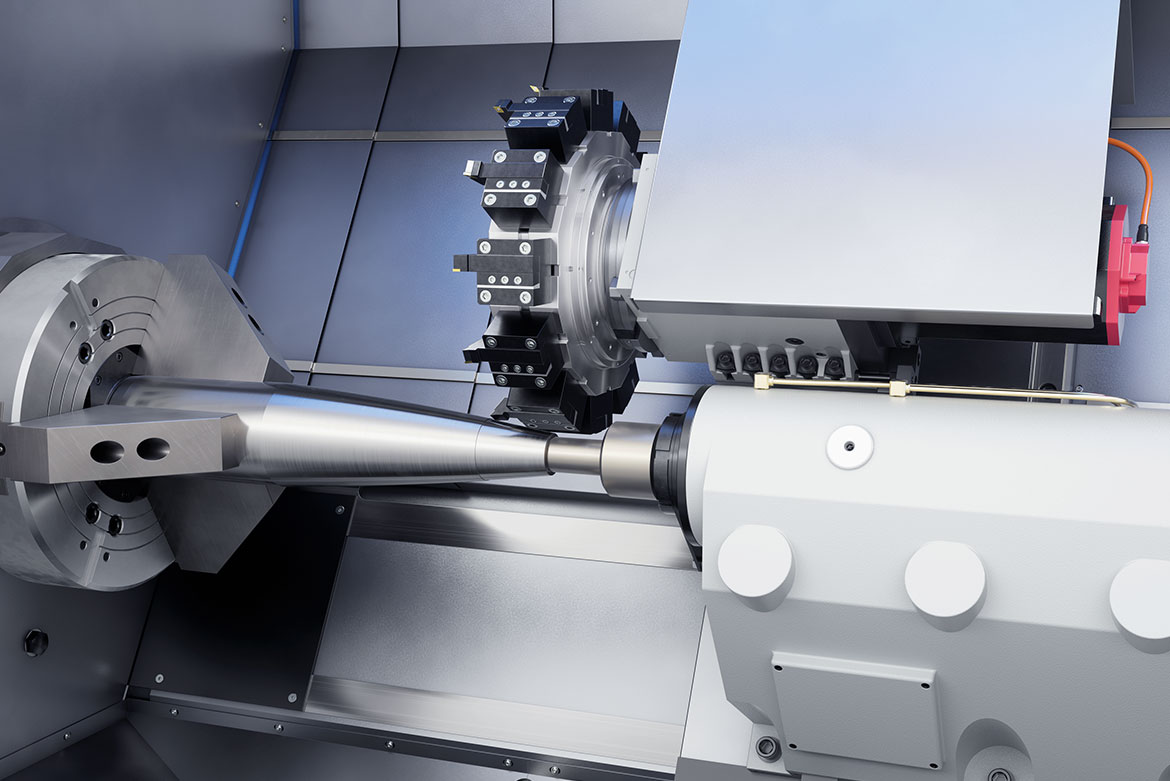
Work area of the USC 850 universal lathe with a clamped 155 mm artillery shell sleeve, supported by a hydraulic tailstock, for vibration-free precision machining.
A word about the control system and operation: Which CNC control system is used in the USC 850 and what advantages does it offer the user?
For the control system, we rely on a proven system from FANUC. Specifically, the USC 850 is equipped with the FANUC 0i-TF CNC control. This control offers all the necessary functions for the complex multi-axis machining required for this machine. For the operator, this means that he has a powerful and at the same time familiar CNC system in front of him, which enables simple programming and reliable sequence control. The FANUC 0i series is used in many workshops around the world, which speaks for its reliability and also means that operators hardly need any training time – an advantage in practice. Another important aspect is the longevity of the electronic components. We have housed all the electronics in an air-conditioned electrical cabinet with IP54 protection. This means that temperature fluctuations, dust or oil mist cannot harm the control electronics. Even in harsh production environments, the electrics work at a constant temperature and are protected from dirt – this significantly increases operational reliability. From the operator’s point of view, the control system offers programmability via G-code as well as convenient features such as cycles for turning and milling operations, graphic support and the like – we have made sure that daily processes can run efficiently.