“The combination of manual operation and automated functions allows operators to make the most of their experience while benefiting from the precision of the control system,” explains Andreas Hessling, Technical Sales Manager at EMAG Weiss, in an interview. The hydraulic-free W 11-EVO cylindrical grinding machine addresses key customer requirements: minimized energy costs thanks to servo-electric axes, highest precision thanks to scraped V-flat guides and an intuitive touch control for quick machine settings. The sophisticated operating concept shows its strengths particularly in the economical production of prototypes and individual parts. The operator retains direct control over the sanding process thanks to handwheels, while the servo-controlled axes ensure precision positioning and reproducible results.
Mr. Hessling, many companies are faced with the challenge of manufacturing individual parts and prototypes economically. What possibilities does the W 11-EVO offer for this situation?
In single part and prototype manufacturing, the programming effort for pure CNC machines is often uneconomically high. The W 11-EVO allows the operator to contribute his experience directly, while still benefiting from the precision of a modern control system. The operator can observe the grinding process directly and intervene immediately if necessary. This saves time and increases process reliability, especially for valuable individual pieces.
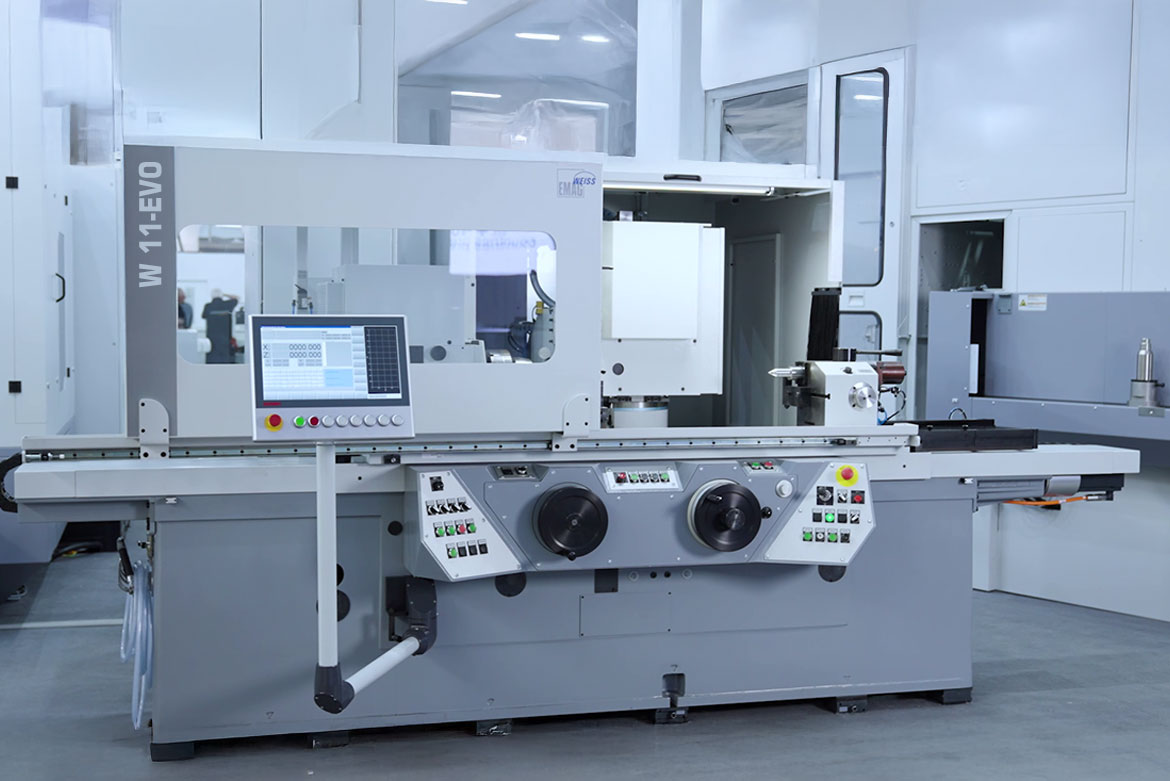
Thanks to its open design, the W 11-EVO offers the operator an optimal view of the sanding process. The ergonomic arrangement of the operating elements enables direct intervention when machining valuable individual pieces.
Energy and maintenance costs are an important issue. How does the W 11-EVO address these aspects?
A key advantage is the complete elimination of hydraulics. Instead, we rely on servo-electric axes. This not only significantly reduces energy consumption, but also eliminates high-maintenance components. No hydraulics also means no oil changes, no seals that can wear out and no costly disposal of hydraulic oil. In addition, the typical problems with vibrations and heat generation are eliminated, which has a positive effect on component quality.
How does the machine support the operator in their daily work?
Operation is designed so that the operator can work quickly and flexibly. On the one hand, he has the usual manual control via handwheels, but at the same time sees all relevant positions digitally on the display. The manual B-axis with “air cushion” support makes it particularly practical to switch quickly between different sanding operations.
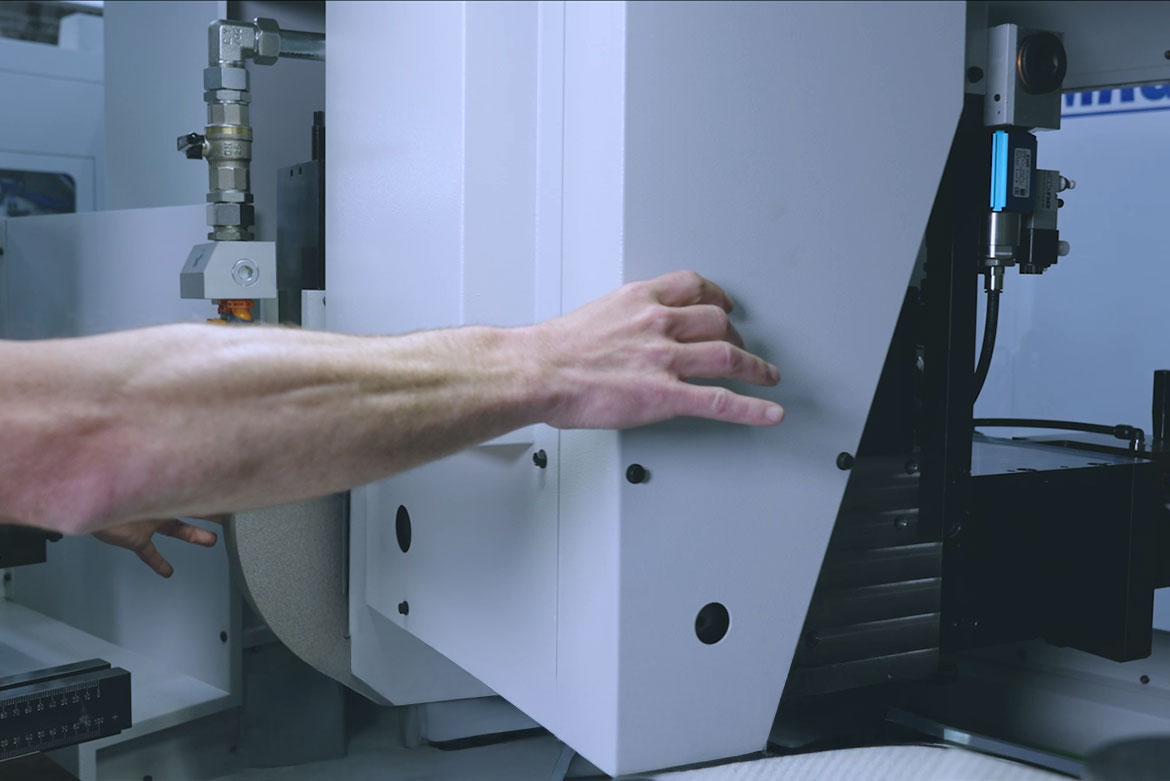
The swiveling B-axis of the W 11-EVO enables quick changes between external, internal and face-grinding. Thanks to the integrated encoder, the control unit recognizes the corresponding grinding operations and provides the interface for entering the technology parameters on the display. This significantly reduces set-up times.
Machine accuracy is crucial for component quality. What solutions do you offer here?
We achieve concentricity accuracies of 1 µm and less on the workpiece headstock. This is mainly due to the high-precision spindle bearing. The scraped V-flat guides also make a significant contribution to the high quality. These are still shaven by hand and then coated – a time-consuming process, but one that pays off in terms of the precision that can be achieved. The long-term stability of this solution can be seen in the many old Karstens machines that still work with precision today.
How flexible is the W 11-EVO for different machining requirements?
The machine covers the complete spectrum from external to internal and face-grinding. The workpiece headstock enables motor speeds from 1 to 650 rpm, which allows optimum adaptation to different workpieces. We can machine workpieces up to 1,500 mm in length between centers. Thanks to the various spindle adapters, the machine is very flexible when it comes to holding workpieces. This reduces capital investments, as one machine can cover many tasks.

The generously dimensioned work area of the W 11-EVO enables the machining of workpieces up to 1,500 mm in length. The machine is designed for external, internal and face-grinding and offers maximum flexibility thanks to various spindle adapters.
How does the control system support process reliability?
The touch interface makes entering technology parameters very clear. The operator is guided through the setup step by step.
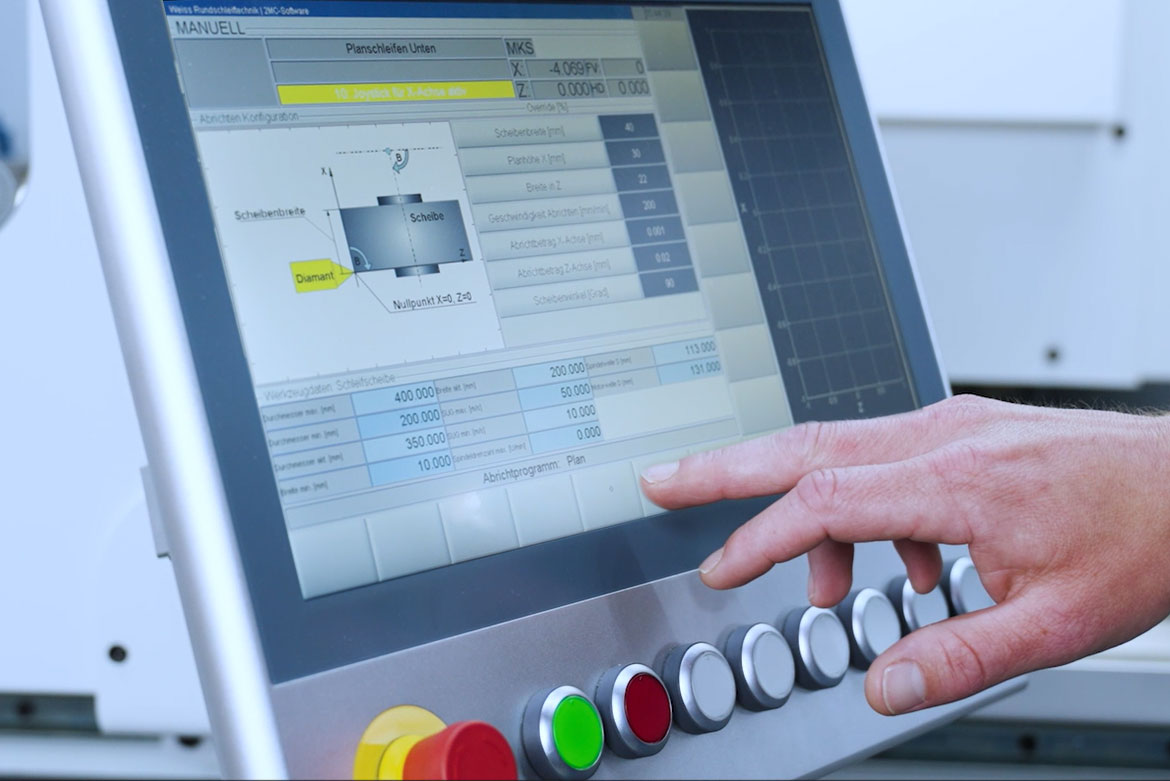
The control unit of the W 11-EVO clearly displays all relevant process parameters. The digital position display and touch operation enable precision control of the grinding operations.
The W 11-EVO is also often used in training, why is that?
The combination of manual operation and modern controls makes the machine the ideal training tool. Trainees learn and understand the basic interrelationships involved in manual grinding, but at the same time they are also familiarized with modern control technology. This creates an excellent basis for later work on fully automatic CNC machines. Especially in times of a shortage of skilled workers, this practical training is an important aspect.