The CLC 200 is a powerful gear hobbing machine that has been specially developed for the machining of gears, gear cutting shafts and worm gears up to module 5. In this interview, Alexander Morhard, Technical Sales Support Manager at EMAG SU, gives an overview of the most important features, advantages and areas of application.
Mr. Morhard, can you start by explaining the main features of this machine?
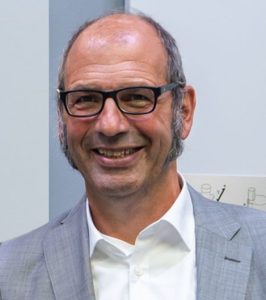
Alexander Morhard, Technical Sales Support Manager at EMAG SU
The CLC 200 is a robust vertical gear hobbing machine. Its stable and heavy construction with a machine weight of over 12 tons dampens vibrations very effectively. At the heart of the machine are the direct drives in both the table and the milling head. These eliminate any gear backlash between the table and milling head and, thus, produce high-quality tooth profiles. The milling head is made of cast steel and has a V-shaped, ground and hand-scraped tangential axis with high rigidity and very good damping. Due to the special design of the milling head, which is made of a high-strength material, allowing large swivel angles.
The milling arbor is mounted with two precision cones that run exactly in relation to each other and ensure very good concentricity of the milling cutter, which is crucial for the gear cutting quality and also enables quick retooling of the milling cutter. An automatically movable counter bearing in the milling head ensures a rigid setup of the tools and also facilitates machine setter. Thanks to this design, we can use not only bore cutters, but also shank hobs with the highest precision, which increases the flexibility of the machine enormously. In addition to the standard milling head, a optional high-speed milling head can also be installed. The directly driven tool table can also be optionally equipped with higher motor speeds.
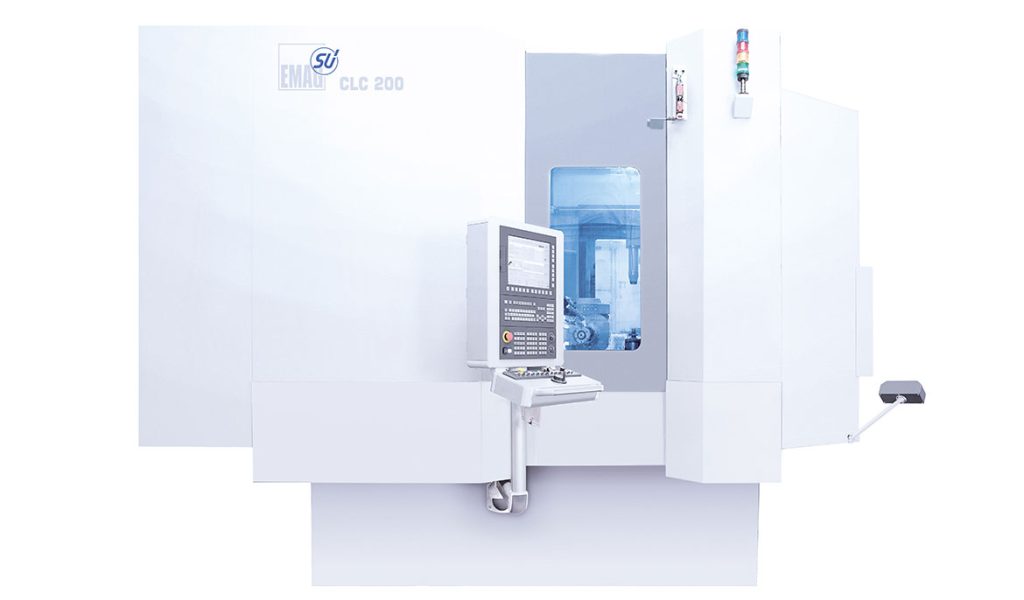
Vertical gear hobbing machine CLC 200 from EMAG with compact design and robust construction.
.
That sounds like a very well thought-out design. What other special features are there?
In addition to the high-precision milling head, the CLC 200 has an automatically movable tailstock. This can optimally support workpieces up to a length of 600 mm and the contact pressure can be adjusted via the NC. This ensures that slim shafts only bend minimally during machining.
Another highlight is the ring loader with two NC axes. Here, the stroke and rotation of the ring loader can be set via the NC control. By automatically moving to the gripping position on the workpiece, the workpieces can be loaded automatically with a minimum number of gripper arms. This drastically shortens the set-up process and of course saves costs, eliminating the need for expensive gripper arms as well as storage for the gripper arms. The machine is also very flexible in terms of coolants. It can be operated with water, emulsion or even dry.
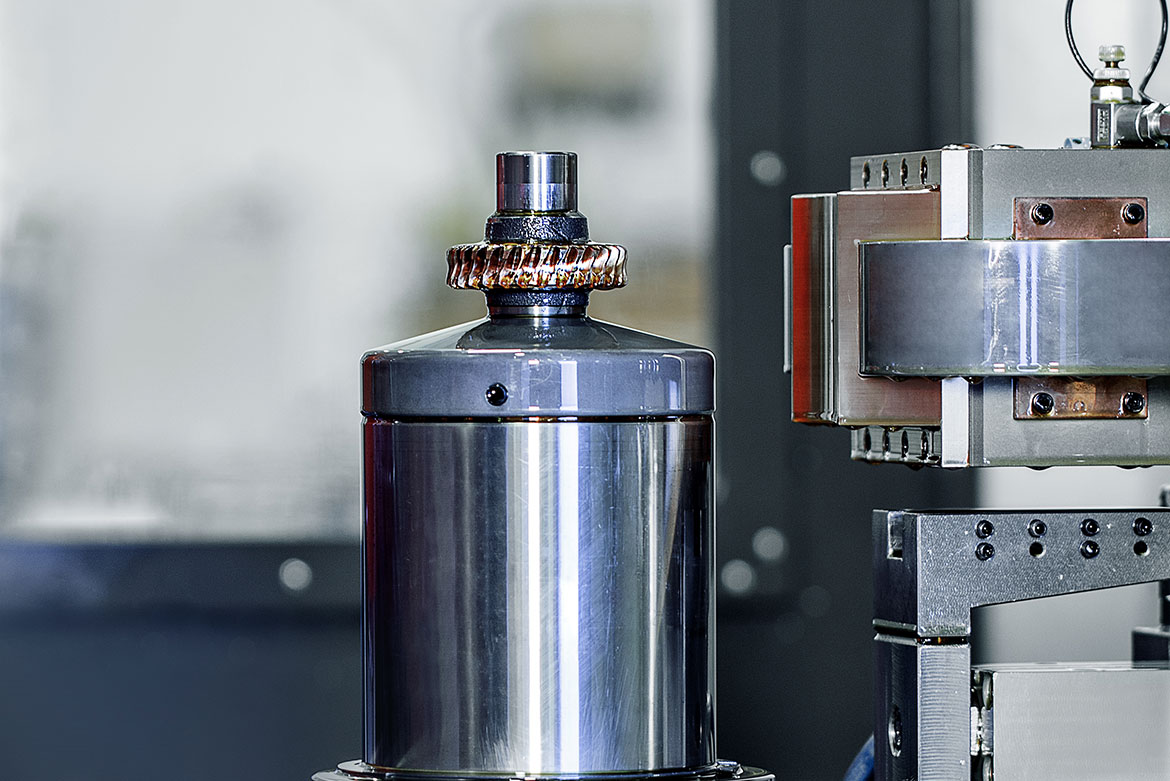
NC ring loader with swivel arms for the use of hobs with small diameters on the CLC 200 gear hobbing machine. This special configuration makes it possible to use hob cutters with a small diameter for precision machining of complex and intricate workpieces.
Which industries and applications in particular suite this gear hobbing machine?
The CLC 200 is a truly a versatile machine. It is ideal for contract gear-cutters, who require a high degree of flexibility. It excels in gear manufacturing thanks to its precision and reliability. The automotive industry particularly appreciates its ability to produce complex tooth profiles in a single operation. Specifically, gears, toothed shafts and worm gears up to module 5 can be machined. The maximum workpiece diameter is 220 mm in diameter and 600 mm in length. Straight and helical gears can be produced. The machine is designed in such a way that it can be used economically for both mass production and single-part production.
How flexible is the CLC 200 with regard to different processing technologies?
The flexibility of the CLC 200 is truly impressive. We can pre-mill tooth profiles for grinding, finish milling, milling with side milling cutters and skiving. Skiving, a hard fine machining technology, requires an optional single-center sensor that can be swiveled in automatically. When milling individual parts, we use the high dynamics of the machine, which means that even complex gear geometries can be produced very economically. Switching between these technologies is extremely simple and requires only very short set-up times.
How are these different processes controlled?
We offer two options: the Fanuc control or optionally the Siemens control with an HMI specially developed for the fast programming of gear hobbing processes. Both systems enable intuitive dialog programming. The EMAG dialog programming offers input masks for all common gear types. The operator only has to enter the workpiece and tool data and the control system automatically calculates all the necessary movements. This reduces training times for new employees and minimizes incorrect entries.
Let’s talk about the CLC 200 ring loader. What advantages does it offer?
The NC-controlled ring loader is a real automation jack-of-all-trades. With its two NC axes, the rotary axis and the lifting axis, almost all loading tasks can be mastered. The rotary axis enables a rotation of 180 degrees, while the lifting axis has a large travel range. This allows us to handle workpieces of different sizes without retooling. A decisive advantage is the reduction in the number of set-up parts. Instead of having special grippers for each workpiece size, we simply move to the appropriate position. This not only saves costs, but also valuable set-up time. The reliability of the system is impressive. Some of our customers have been using the ring loader in three-shift operation for years without any significant downtime.
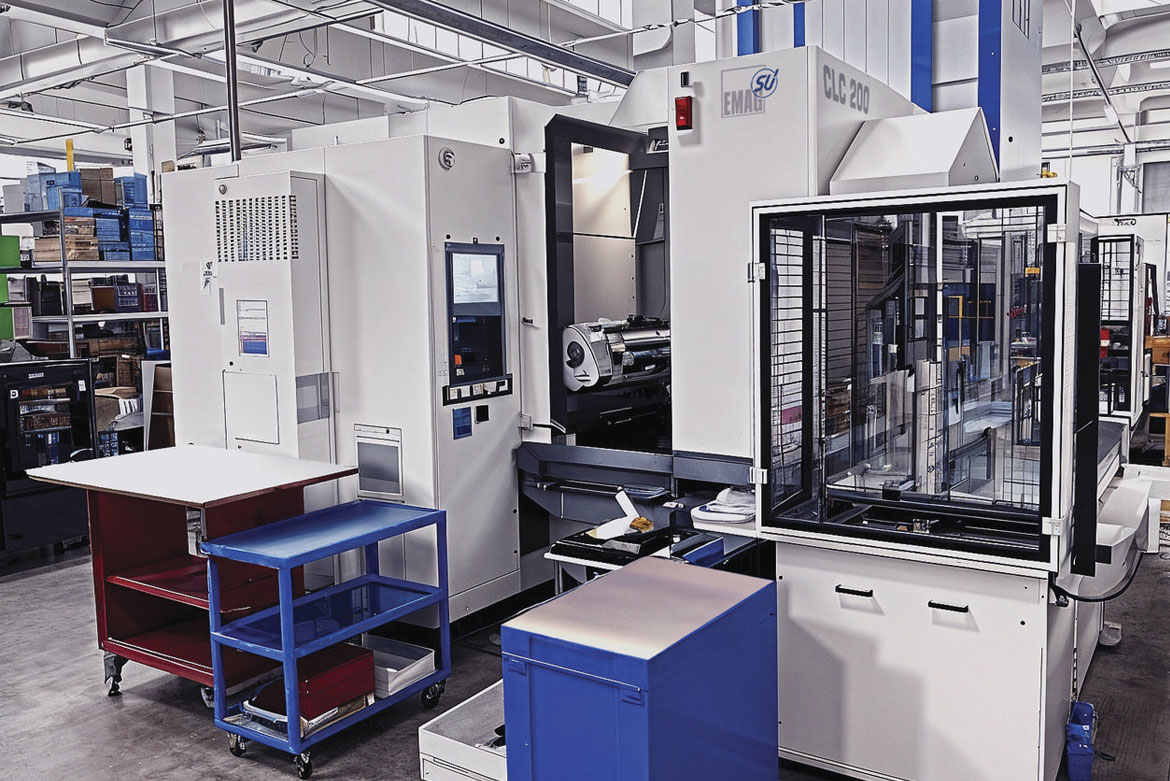
The NC-controlled ring loader of the CLC 200 loading and unloading a workpiece, illustrating the efficiency of the automation.
How easy is it to operate the ring loader?
Operation is very simple and intuitive. The operator simply enters the gripper height and the workpiece diameter into the control unit. The rest is done automatically. Only the workpiece carriers need to be changed on the feed belt, which is done in a few seconds thanks to quick-release fasteners. A special feature is the integrated workpiece recognition. This automatically checks whether the correct workpiece is present and stops the process if there are any deviations. This avoids rejects and increases process reliability enormously.
Are there alternative automation solutions for the CLC 200?
Yes, in addition to the ring loader, we also offer robot loading. A 6-axis robot stands behind the machine and loads directly onto the spindle. The CLC 200 is equipped with an automatic sliding door for this purpose. Although the robot takes a little longer than the ring loader for a complete loading cycle, it is more flexible. For example, it can deburr or clean workpieces in a deburring or cleaning station or inspect them in a measuring station. This is the advantage of the robot, it can also take on other tasks in addition to loading and unloading. For customers with complex workpieces, long running times or frequently changing part families, the robot solution may be the better choice. It always depends on the individual case. The service door can also be opened automatically as an option.

A robot is positioned at the rear of the CLC 200 gear hobbing machine, which loads a workpiece into the machine through an open loading door. This configuration enables efficient and fast production, as the robot can prepare other workpieces in parallel with machining.
How is workpiece control and position orientation achieved with the CLC 200?
The CLC 200 offers a comprehensive package for workpiece control and position orientation. There is a hydraulic cylinder in the table for automatic actuation of the workpiece clamping. The clamping path is digitally monitored to immediately detect errors during setup. We use high-precision inductive sensory equipment for position-oriented milling of flutes, holes or tooth profiles. This determines the exact position of the workpiece and positions the tooth profiles to be milled accordingly. The machine also has an optional integrated measuring system. This can be used both for position-oriented workpieces and for checking the produced tooth profiles. After machining, it carries out a 100% check to ensure that all quality parameters have been met. A special feature is the adaptive process control. Based on the measurement results, the control system can automatically make adjustments to the machining parameters to compensate for fluctuations in material quality or tool wear.
You mentioned the direct drives in the workpiece table and in the milling head. What advantages do these offer?
The direct drives are the heart of the CLC 200 and a decisive advantage. They eliminate any gear backlash in the milling head, resulting in very high precision.
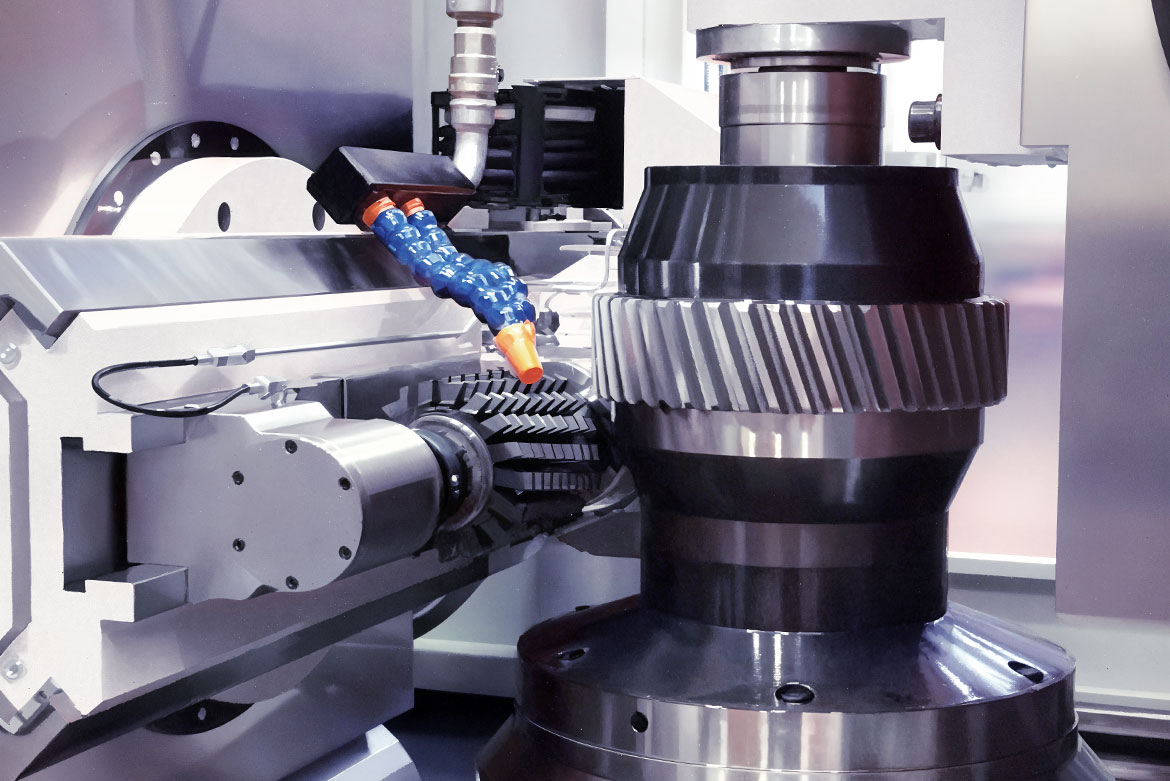
Milling head with direct drive, which ensures maximum precision in gear production.
The direct drive in the workpiece table is available in different speeds and enables high motor speeds with maximum positioning accuracy. This is particularly important in gear hobbing, where perfect synchronization between workpiece and milling cutter is essential. Another advantage is the long service life. Direct drives are virtually no-wear, which drastically reduces maintenance costs and increases machine availability. We have customers who have been using their CLC 200 in three-shift operation for several years without any loss of precision. An often overlooked advantage is energy efficiency. Direct drives have an efficiency of over 90 %, while conventional drives often only achieve 60 to 70 %. This is clearly noticeable in the electricity bill.