For over 30 years, Bäringhaus & Hunger, based in Grünhainichen near Chemnitz, have been active in the part manufacturing industry – experiencing growing success with the production of high-precision turned and milled parts. About 90 percent of orders received at Bäringhaus & Hunger come directly from suppliers in the automotive industry. From almost the very beginning, EMAG has played an important role in this as a mechanical engineering partner, and currently have over 20 machines on the Bäringhaus & Hunger shop floor. How did this partnership develop and why is it still so important today? We spoke with partners, Matthias and Sebastian Hunger, the second generation of the family to run the company, about the secret to their company’s success.
Mr. Hunger, how would you describe your company’s market position?
Matthias Hunger: We are active as a system supplier for a well-known automobile manufacturer, and for them we process up to 1,000,000 parts per year. We are also responsible for the mechanical processing of a large variety of parts that we produce between 1 and 200,000 of per year. This range extends from turned parts such as gearshift wheels, axle journals and joints to milled parts such as steering knuckles and aluminum housing parts. Overall, over 30 years we have developed into a successful company that provides jobs for about 120 employees.
Sebastian Hunger: It is extremely important to us that we ensure very precise and error-free results for our customers, and that we can react quickly and flexibly to new inquiries. In some cases, we are able to present sample parts to a customer just one week after inquiry. That is our benchmark. Customers know that if they come to us, they will be offered the perfect production solution as quickly as possible, provided of course that the inquiry matches our area of work.
How do you ensure fast response times?
Sebastian Hunger: First, it is important that we have a lot of experience with a specific range of parts. In some cases, we have been working with the associated production processes for decades. That is why we already know how to configure the associated machines. For example, we develop the workpiece pallets for the circulating conveyor belts in-house. The same applies to the processing of the machines. As a result, the desired production solution is available, quickly! Additionally, almost the entire vertical turning process is performed in-house using a uniform technology. This allows us the capability to quickly changeover additional machines and create the desired quantities within a specific delivery window.
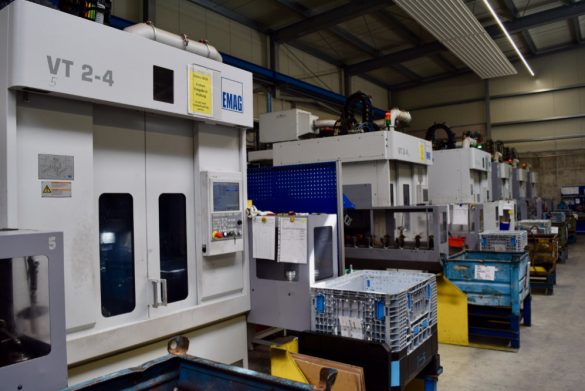
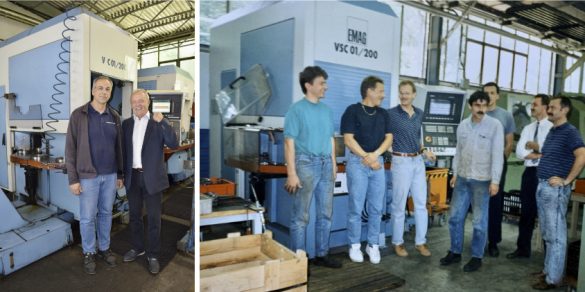
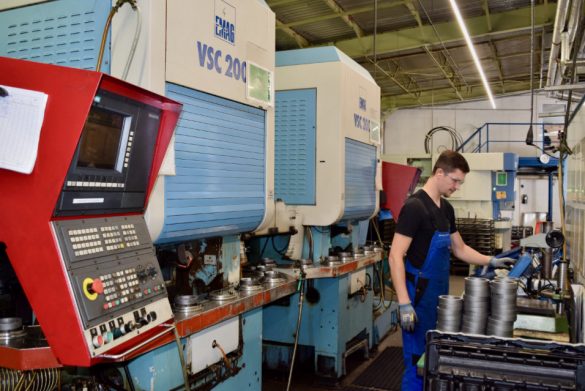
Over the years, what experience have you gained with EMAG’s pick-up technology?
Matthias Hunger: We have had a very good experience with these machines, and they have certainly contributed to our success. The company’s first EMAG solution was a new VSC in 1993, before that we had only invested in used machines that required labor-intensive hand loading. The pick-up technology on the VSC changed the whole process because the operator simply had to place the blank on the conveyor belt, and then remove them when the part was finished. The machine – significantly improving speed right from the start, did everything else. The price-performance ratio was also very good – after all, we did not have to invest in an external automation solution. All of these benefits are still applicable for us today!
How did additional investments in EMAG technology come about?
Matthias Hunger: We continued to experience a rapid increase in success with our approach, and of course when we started producing larger part quantities and receiving new orders, we had to look at investing regularly in new production technology. Solutions from EMAG continued to play a role in our success. For example, in 1995 we purchased two interlinked VSC machines for the double-sided machining of joints, then in 2001 we invested in the standard VL 3 and VL 5 machines for the machining of ball hubs and with the purchase of a VT 2-4 in 2015 we started machining shafts. Incidentally, space was also a factor in many of these investment decisions, as we did not have to plan for additional blank and finished part dispensers and automation solutions. So, we loved that EMAG’s solutions have a very compact design.
Are you planning to continue using pick-up technology in the future?
Sebastian Hunger: Yes, that is what we are envisioning. The standardization of our turning processes is the base of a perfectly designed and efficient production process – the latter is extremely important when discussing the growing price pressure in vehicle manufacturing. Some time ago, I had a conversation with a customer who confirmed that we could even keep up with competition from the Far East in terms of unit costs. This would be almost impossible without the extensive automation of the turning process using a pick-up spindle.
At the end of the day, the question of the first VSC machine remains with you – where is the machine today?
It is actually still in use. We use it today for preliminary processes such as turning forging skin. But it does that flawlessly.