Vertical pick-up turning machines are indispensable in modern manufacturing. These machines often produce in three-shift operation and are already highly optimized for specific production requirements. But how can additional increases in performance be achieved with such highly developed manufacturing systems? Jürgen Maier, Head of the Turning Business Unit at EMAG, deals with this question. In the following interview, you will learn how productivity can be further increased by direct loading into the work spindle of a vertical turning machine using a robot.
Which types of workpieces suit the robot direct loading most effectively?
The robot direct loading process is particularly suitable for workpieces with short cycle times. We have a decisive advantage here since a pure workpiece changeover time takes just three seconds. That is extremely fast and efficient. In terms of geometry, stable chucked components with a central bore are ideal. Think of gears or other transmission parts. These workpieces benefit particularly from this process. The stability is important for precision handling by the robot, and the hole enables secure holding and positioning in the spindle.

An industrial robot precisely inserts a workpiece into the spindle of an EMAG vertical turning machine.
Are there special requirements for the geometry or tolerances of the workpieces?
Basically, the workpieces have to fit on the machine, of course. A key feature is that they must have a hole. This is crucial for picking up and positioning by the robot. As far as tolerances are concerned, we are quite flexible. Even turned-out jaws are not a problem. This is due to the high positioning accuracy of our robot. We have developed a sophisticated system in which the robot uses a spring assembly to press against. This combination of precision robot control and mechanical fine adjustment enables us to work reliably even with workpieces with tight tolerances.
What are the advantages compared to classic pick-up loading?
The advantages of direct robot loading over classic pick-up loading are manifold. Firstly – and this is the main advantage – we save cycle time. With the traditional method, we have an additional step: the workpiece is first placed on an intermediate station (conveyor belt) and transported from there into the machine. With our process, this intermediate step is completely eliminated. The robot inserts the workpiece directly into the spindle. This not only saves time, but also reduces potential sources of error. Secondly, this method offers us more flexibility in the process sequence. For example, we can blow off the chuck directly on site. This allows us to handle the workpieces even more efficiently. Another important advantage is the possibility of immediate reworking. The components remain clamped in the robot gripper, so that we can clean, mark or measure them immediately. This optimizes the entire production process and increases the quality of the end product.
Are there limits to this procedure?
Of course, as with any technology, there are limits and scenarios when traditional methods still have advantages. Our direct robot loading method is particularly effective for small to medium-sized vertical turning machines, specifically our VL 2 and VL 4 models, where it makes perfect sense as we can utilize the full efficiency of the system. With larger machines that work with very large and heavy components, the system reaches its limits. In such cases, the process often becomes too complex. An oversized robot would have to be used, which would be neither economical nor practical. This is where traditional pick-up automation still offers advantages. With such large components, the time saved in loading and unloading is also less critical for overall efficiency.
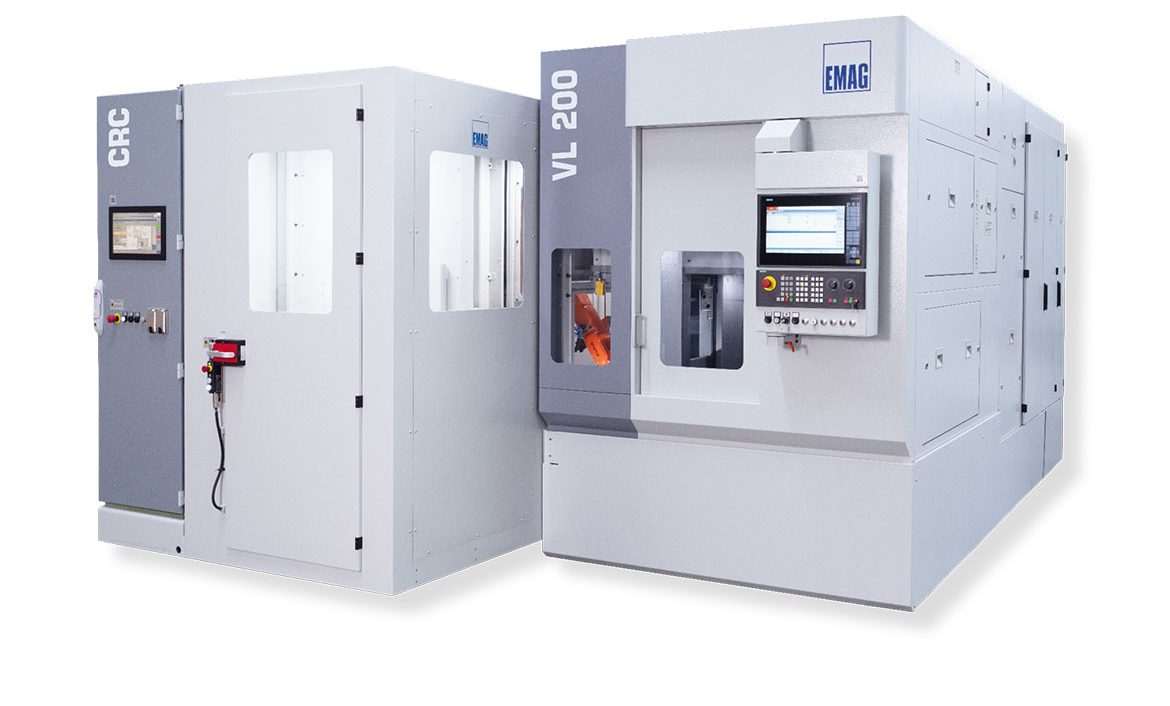
Instead of a conventional conveyor belt, the CRC robot cell is mounted directly on the VL 200. The robot loads the workpiece directly into the spindle and performs the loading and unloading function using a twin-gripper.
We have currently optimized direct loading for part weights up to 3 kg. This covers a large proportion of common applications. We have also worked successfully with larger components, but this must always be assessed on an individual basis. It must match the specific machining requirements and the overall process. Ultimately, it’s about finding the optimum solution for each customer and each application. Sometimes this can be direct robot loading, in other cases a traditional solution or a hybrid solution consisting of robots and pick-up automation may make more sense.
How does the use of robots affect the complexity of the system?
Interestingly, the use of robots actually makes the overall system simpler, not more complex. This may seem contradictory at first glance, but let me explain.
First of all, it is important to understand that modern robots are very user-friendly. Once the robot has been set up, programmed, configured correctly and trained, only a few positions need to be adjusted. This is a one-off effort that quickly pays for itself. The big advantage lies in the flexibility and repeat accuracy of the robot. Once programmed, it performs the movements again and again with the highest precision. This significantly reduces the complexity of daily operation.
The robot also eliminates the need for additional mechanical components, which are often required in traditional loading systems. Each of these components would be a potential source of error and would require servicing. The robot takes over all these functions in one integrated system. The operation of the machine is not made more complicated by using robots. On the contrary, although it is a complex device, in this application, the robot simplifies the overall system, making the system more robust and easier to operate for the worker.
Can you tell us more about the possibility of an unmanned shift with this system?
That’s one of the main advantages of our system with direct robot loading. We can use it to run a complete “ghost shift”, i.e. completely unmanned production over an entire shift. Specifically, we use either a CRC stacking cell or a SCS cell for this. These cells are designed in such a way that they can store a large quantity of raw-parts. The robot then accesses these components independently and carries out the entire loading and unloading process without human intervention.
The result is a significant increase in overall equipment effectiveness (OEE). Just imagine: the machine can run all night, on weekends or public holidays – always, even when there are no operators on site. This increases productivity enormously without increasing personnel costs.
Another advantage is the consistency of production. The robot always works at the same speed and precision, regardless of whether it is 2 a.m. or 2 p.m. This leads to a very consistent quality of the components produced.
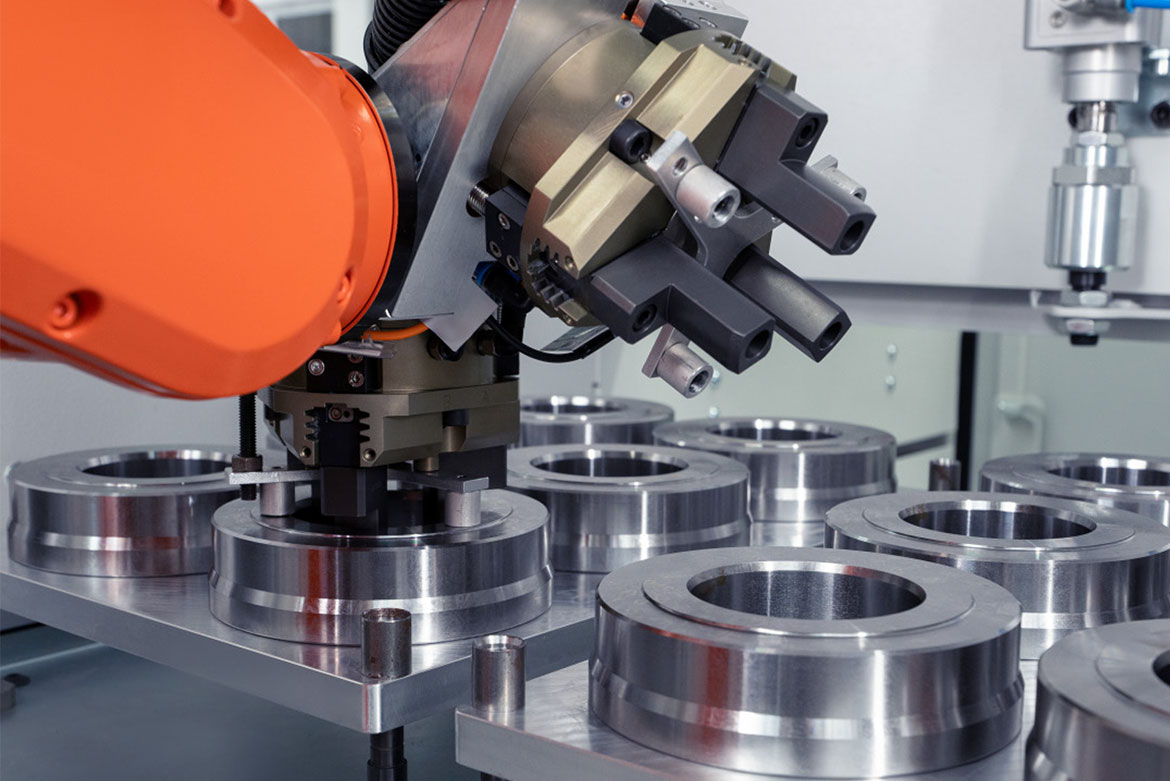
The CRC stacking cell enables fully automated production.
That sounds impressive. But how do you ensure that the tools are sufficient for a complete shift?
That’s a good question, because tool life is often the limiting factor in long, unmanned production runs. This is where our 12-station turret plays a key role in this system.
The 12-station turret gives us the option of working with sister tools. This means that we can insert several identical or very similar tools into the turret. When a tool has reached its service life, the system automatically switches to the next sister tool.
Let me illustrate this with an example. Suppose we have a machining process that requires four different tools. In a conventional system, these four tools would determine the maximum runtime. With our 12-station turret, however, we can load each of these tools three times. This effectively triples our possible runtime without changing tools.
We also use advanced wear monitoring systems. These continuously monitor the condition of the tools and can predict with precision when a tool change will be necessary. In this way, we ensure that we make optimum use of the sister tools and that production is not interrupted due to unexpected tool failure.
This combination of high tool capacity and intelligent tool management enables us to produce a complete shift – whether 8, 10 or even 12 hours – unmanned. This is a decisive factor in developing truly efficient unmanned shifts.
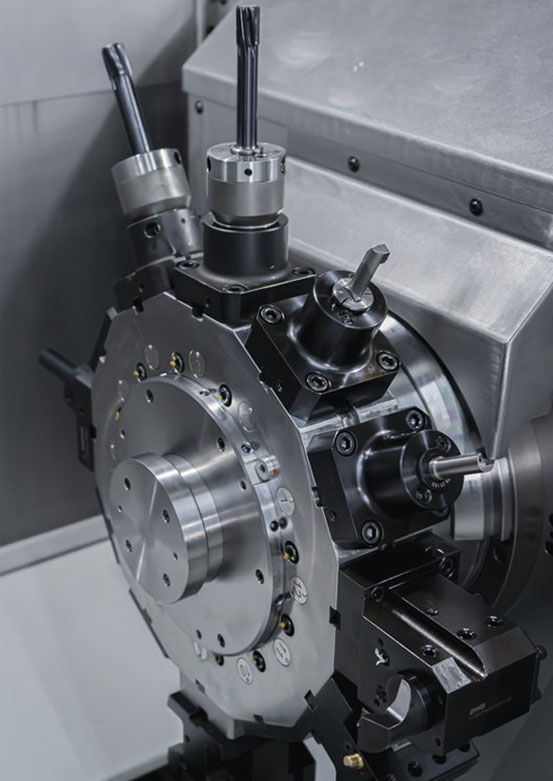
Close-up of the 12-station turret, which holds various tools for unmanned production.
That sounds like a very well thought-out system. What are the advantages for customers?
There are many advantages for our customers:
- Increased productivity: The ability to produce 24/7 enables our customers to significantly increase their capacity utilization and, thus, their overall production.
- Cost efficiency: Unmanned shifts significantly reduce the personnel costs per component produced.
- Flexibility: The system can easily cover night shifts, weekends or public holidays without the need to schedule additional staff.
- Consistent quality: Our machines and the robot always work with the same precision, resulting in very consistent part quality.
- Optimized use of resources: The intelligent use of the 12-station turret and the sister tools ensures that the tool life is optimally utilized.
- Reduced planning effort: Once set up, the system can carry out long production runs without constant monitoring.
- Competitive advantage: The ability to produce flexibly and cost-effectively can represent a decisive competitive advantage in many industries.
In summary, our system enables our customers to optimize their production, reduce costs and at the same time increase their flexibility and responsiveness to market requirements.