Precision plays a decisive role in the manufacture of weapons. One technique that contributes significantly to the precision of firearms is rifling – the insertion of helical flutes into the barrel of a weapon. The rifling ensures that the bullet rotates when fired and hits its target with precision. Traditionally, rifling used to be produced by mechanical processes such as hammering. Or button broaching. However, with the further development of technology, electrochemical machining (ECM) is establishing itself as a superior alternative that enables much greater precision.
ECM Rifling is an electrochemical process for shaping the internal geometry of rifle and pistol barrels. The special feature of ECM Rifling is the high quality of the process.
ECM rifling technology offers various advantages over traditional methods:
- Precision: The precision of the weapons is significantly improved by the even and precise pull that is applied to the barrel.
- Reproducibility: Every weapon machined using this technique has the same exact characteristics.
- Adaptability: The ECM machines make it possible not only to produce standard straight pulls, but also to produce special shapes and tapers in the range of 10-20 µm, which further optimizes ballistic performance.
With the PI machines, EMAG offers a powerful ECM rifling solution that can be configured to customer specifications. These machines have a rifling module that is integrated into the PI machines. The module can machine up to eight barrels with a length of 50 to 800 mm in parallel.
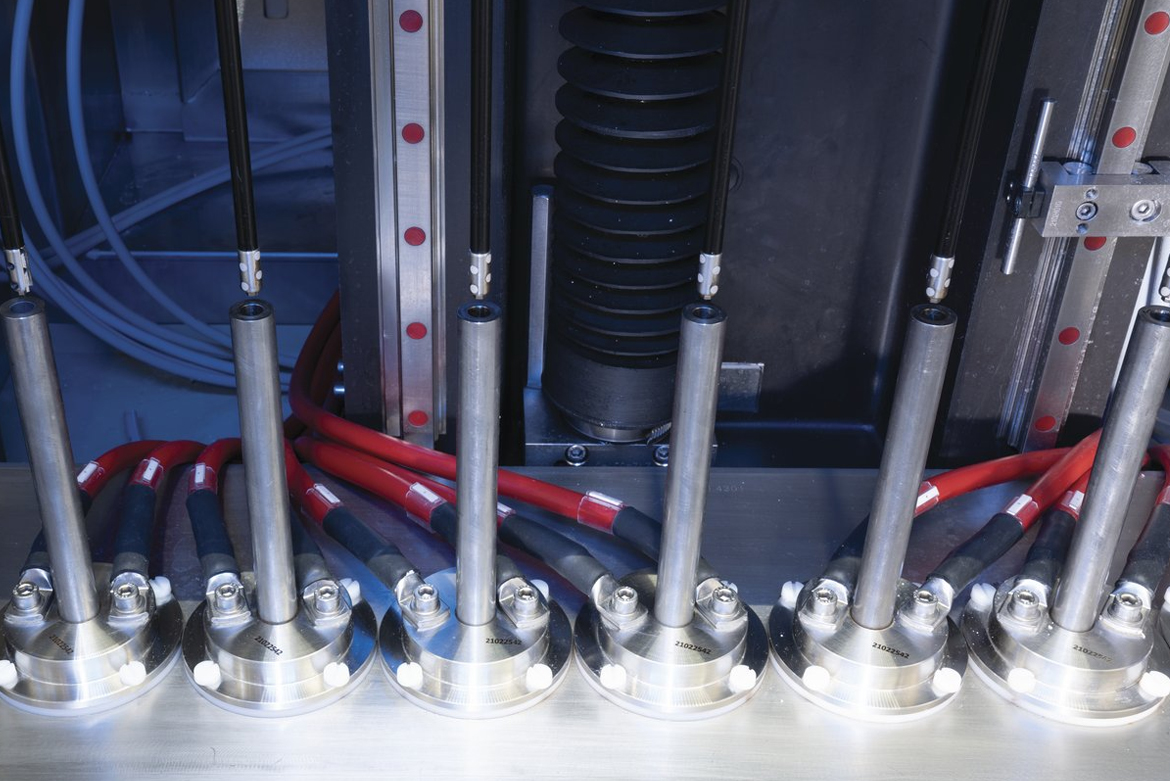
Detailed view of EMAG’s ECM rifling technology, which introduces helical geometries into a gun barrel.
ECM Rifling from standard to customized
With the EMAG ECM Rifling, not only classic rifling geometries with conventional rifling trains can be acheived, but also multi-radial rifling geometries can be produced. This alternative geometry complements the performance spectrum for barrel design and optimization of ballistics.
In addition, EMAG offers the option of incorporating complex internal geometries such as hexagonal or hexagonal profiles into the barrels. Such profiles are particularly in demand for special applications where tailor-made accuracy of fit and unique functionality are required.
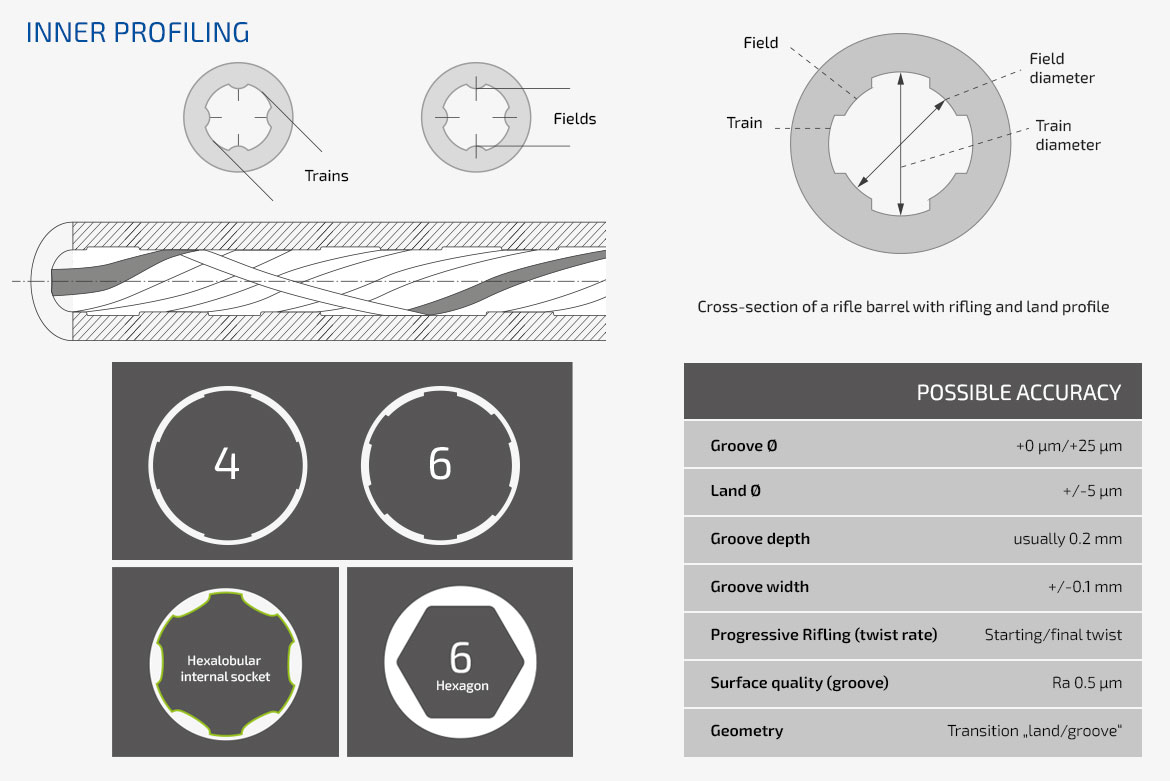
The EMAG ECM rifling process offers exceptional customization options from classic to multiradial rifling geometries. Complex internal hexagonal and hexagonal profiles are also possible to precisely meet customer-specific requirements.
The EMAG ECM rifling process can be individually adapted to the specific requirements of each customer. This enables a high degree of flexibility in production and ensures that each gun barrel corresponds exactly to the technical specifications. This allows manufacturers to develop unique weapon systems that are tailored to the respective area of application.
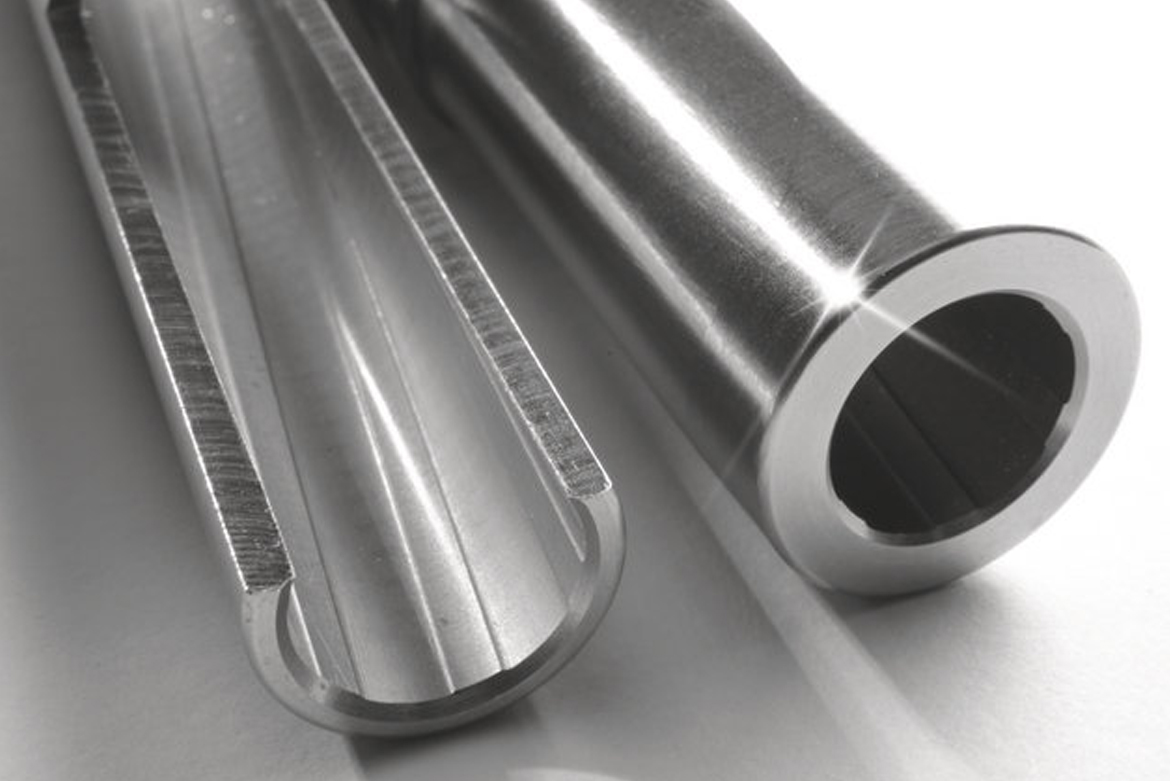
Close-up of a rifle barrel being machined using ECM rifling from EMAG, with spiral grooves visible.