Turning balls, especially in safety-critical areas such as the automotive industry, places the highest demands on precision, repeatability and cycle time. Components such as ball pins in ball joints play a central role in steering and chassis. Their production requires state-of-the-art turning technology – especially when it comes to large quantities and economical processes.
Technical requirements for ball turning
Ball turning is a special process in machining technology in which not only an exact ball shape but also a uniform, high-precision surface must be produced. This is necessary to ensure smooth movement in the joint and prevent premature wear. Depending on the size of the component, ball diameters between 16 and 40 mm with tolerances in the micrometre range must be achieved.
Challenges in batch production
In large-scale production, the challenge is to combine this precision with short cycle times. A reliable solution must not only offer high repeatability and process reliability, but also minimize tool wear and be easy to automate. In addition, all quality requirements must be verifiable inline.
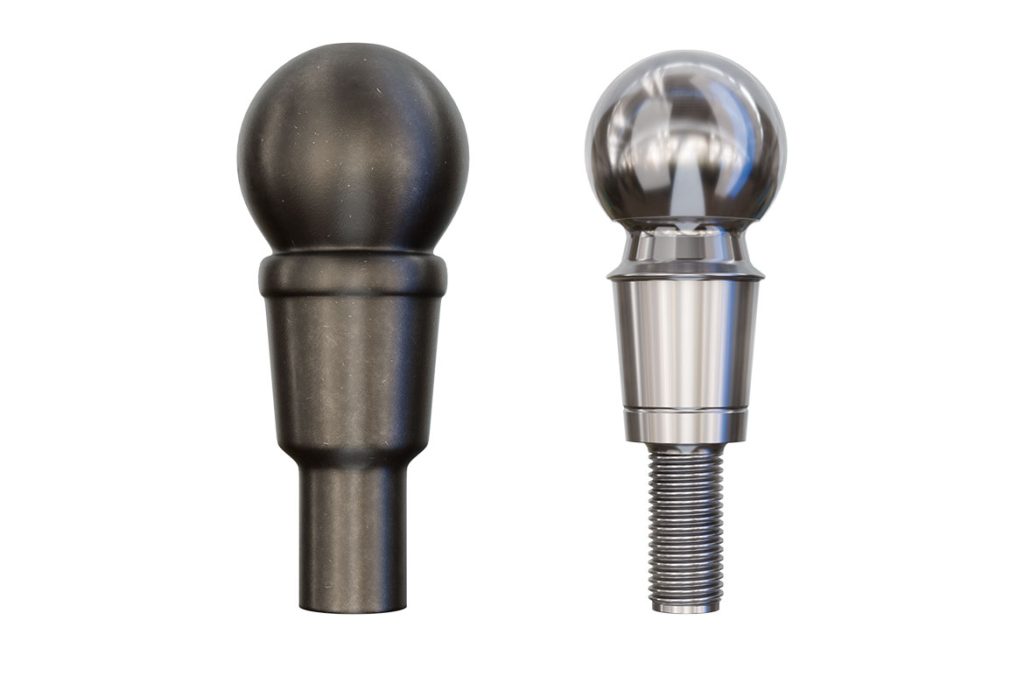
On the left an unmachined blank, on the right a finished turned ball pin with. The component on the right shows the precision contour and smoothing of the ball.
The EMAG VST 50: Customized solution for ball turning
With the VST 50, EMAG offers a machine specially developed for turning ball pins. The turning machine combines two irrespective movable workpiece spindles with a two-part compound slides, which is optimized for both the ball and the neck part of the journal.
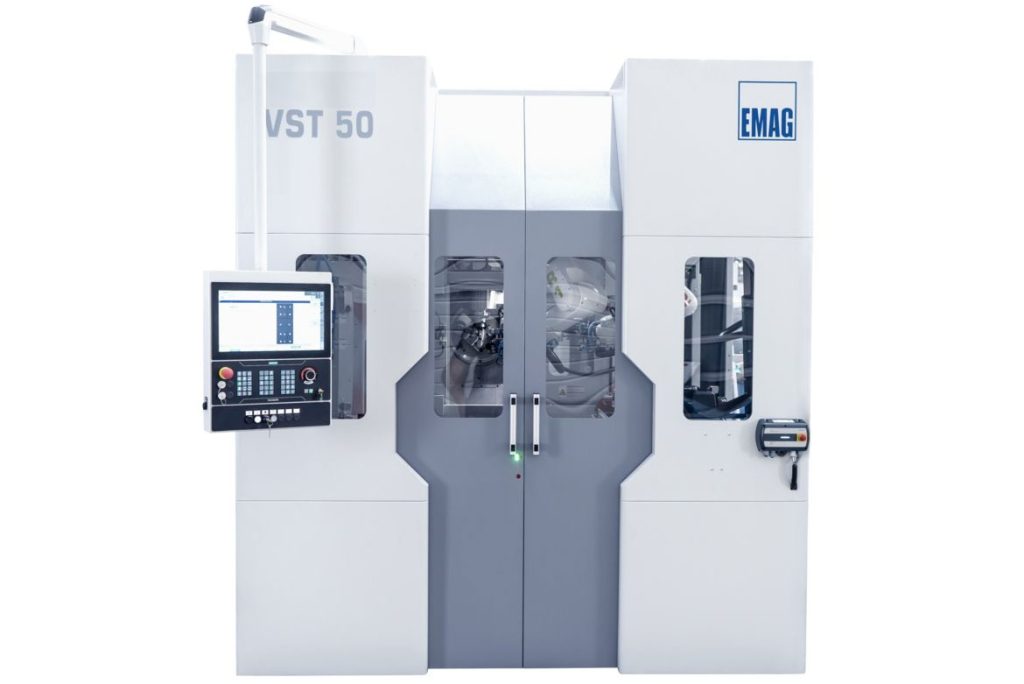
The VST 50 turning machine from EMAG is designed for high-precision ball turning in series production.
Key features at a glance:
- Two workpiece spindles enable parallel loading, unloading and turning – one spindle is machining while the other is loading.
- Rotative B-axis for precision ball machining, including smoothing process.
- Linear U-axis for setting the ball diameter and shape (polarity).
- Integrated process measurement technology using a light-band micrometer for 100% inspection of each component.
- Automated loading and unloading with three robots, optimized for the shortest cycle times.
- Tool change during operation, supported by RFID-coded tools and robot handling.
Productivity and quality in balance
Thanks to the combination of robust mechanical engineers, intelligent software (EDNA apps) and sophisticated automation, the VST 50 achieves a cycle time of just seven seconds per workpiece. At the same time, process reliability remains at the highest level thanks to comprehensive measurement technology and integrated camera monitoring. The tool change time is less than 90 seconds – without manually interrupting production.
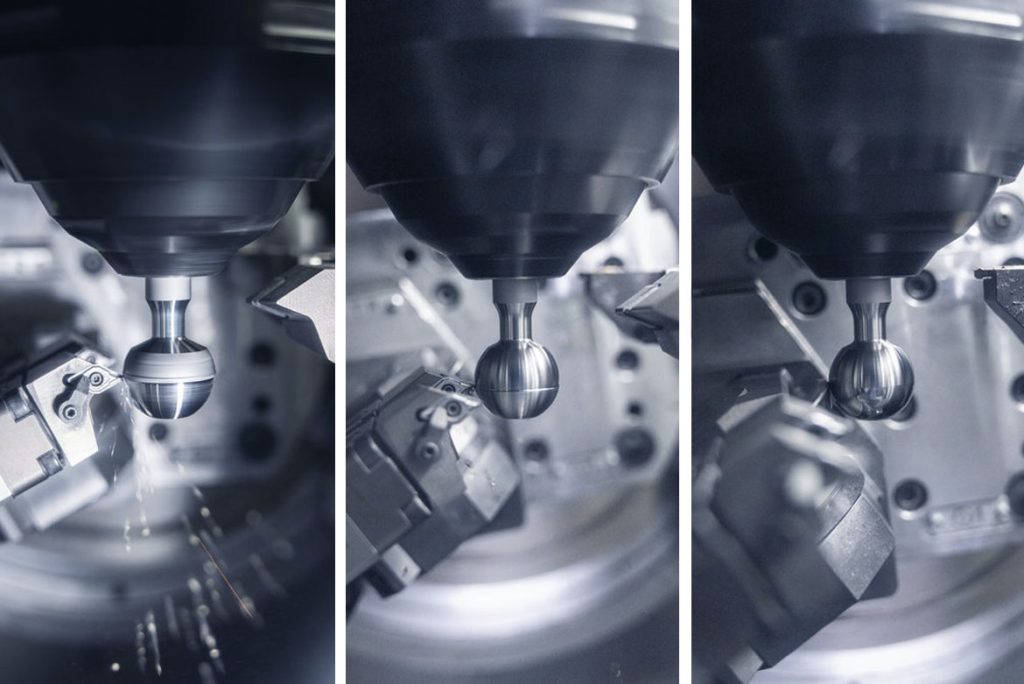
The work area of the VST 50 shows the precision turning of a ball pin. The rotary B-axis allows the ball to be shaped precisely. The tool and component are optimally coordinated to achieve the highest surface finish.
Range of applications and flexibility
The machine is designed for:
- Short ball pins (Ø 16-40 mm, length 50-150 mm)
- Long ball pins (Ø 22-35 mm, length 150-455 mm)
- Machining of ball sleeves
Thanks to its flexible equipment, the VST 50 can also be used for other rotationally symmetrical components where the precision turning of spherical shapes is required.
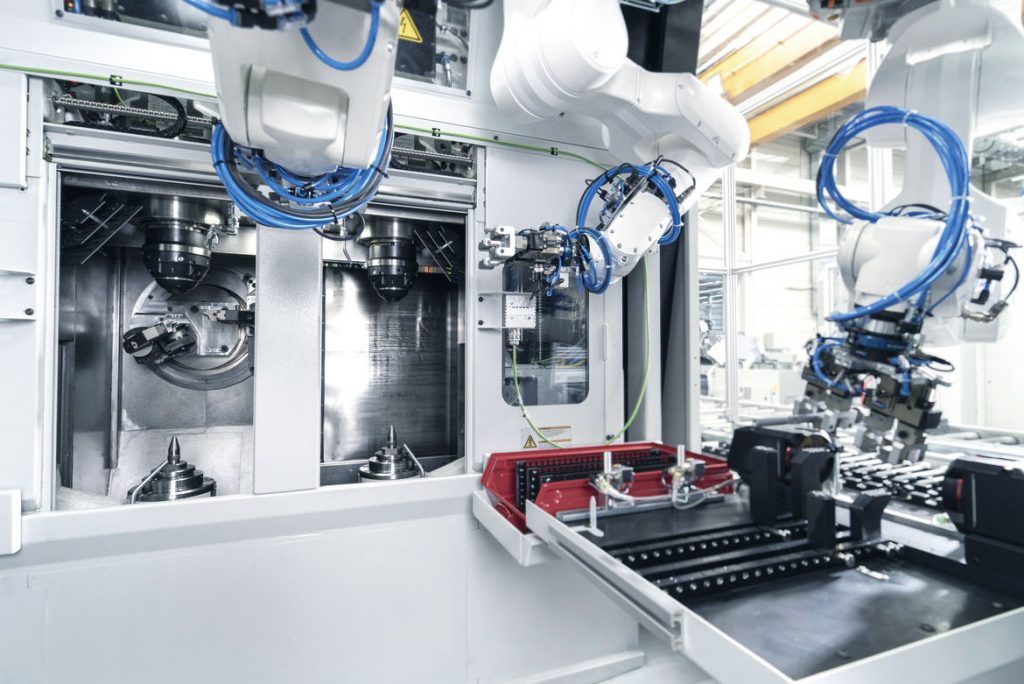
Three cooperating robots ensure a fast and precise material flow in the VST 50. They take over the loading and unloading of the spindles as well as the transfer to external automation modules. The system is designed for maximum cycle times and process reliability.
Turning balls at top industrial level
Turning balls is a high-precision machining process that can only be efficiently implemented in safety-critical applications such as the automotive industry with specially designed machines. The EMAG VST 50 offers a sophisticated solution for the batch production of ball pins – with short cycle times, comprehensive measuring technology and a high level of user-friendliness. If you want to turn balls economically, this machine is the practical answer to today’s production requirements.