Alexander Morhard, Technical Sales Support Manager at EMAG SU, talks in an interview about the G 160 gear generating grinding machine, the fastest machine of its kind for gear production. He provides insights into the innovative axis concept, the high gear quality and the wide range of possible applications in gear manufacturing and electromobility.
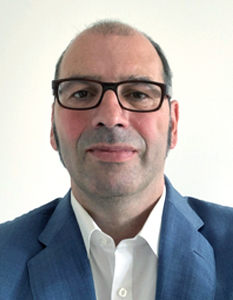
Alexander Morhard
Mr. Morhard, you are Technical Sales Support Manager for the new G 160 gear generating grinding machine. What makes this machine so special?
The G 160 is indeed one of the fastest gear generating grinding machines on the market. What makes it special is its innovative axis concept and the outstanding gear quality it delivers.
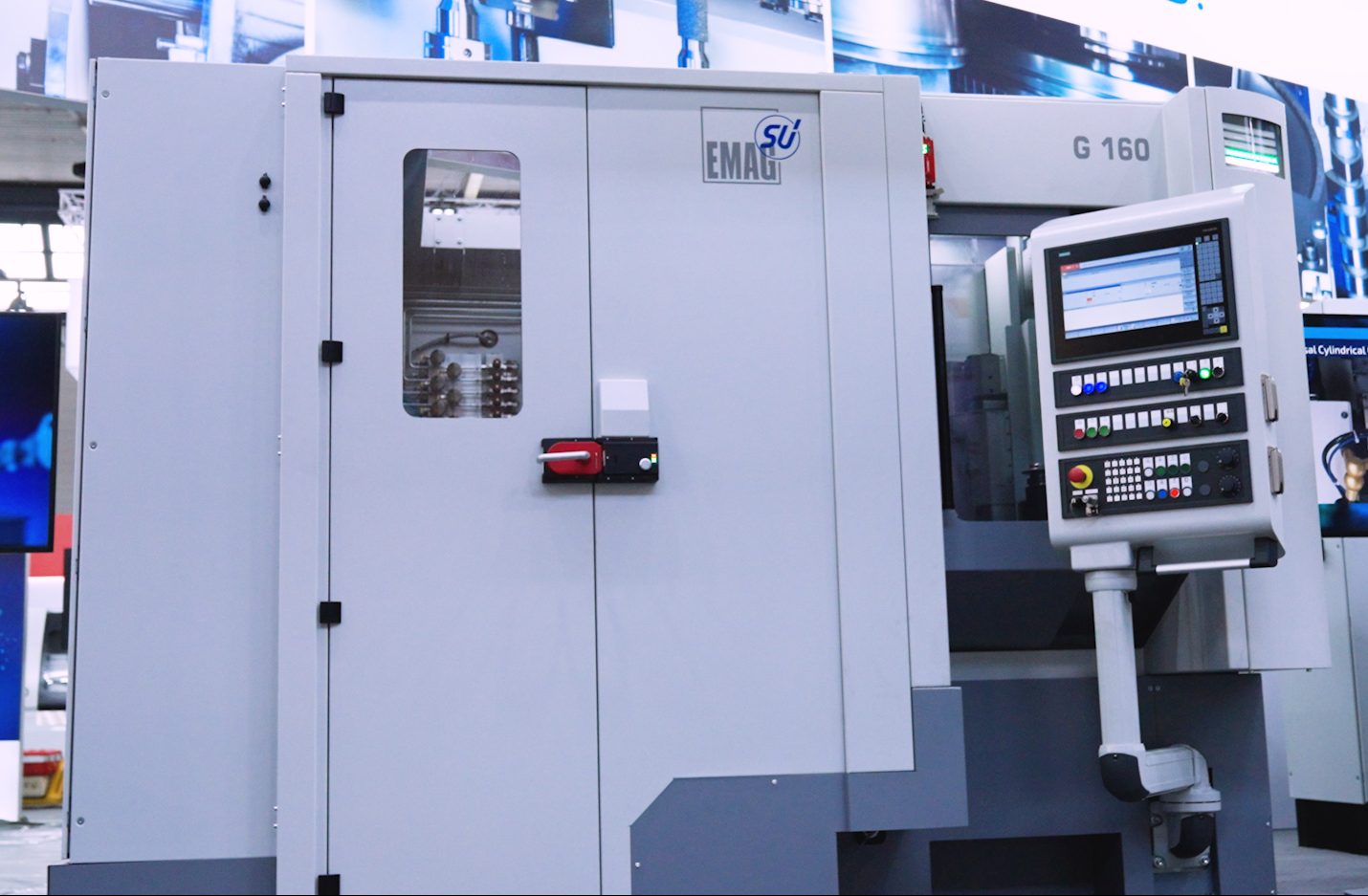
The G 160 gear generating grinding machine from EMAG SU in the production of gears.
Can you tell us more about this innovative axle concept?
With pleasure. Instead of a conventional turret, we use two parallel table slides with direct-driven spindles. These are driven by linear motors, which enables extremely fast positioning of the workpiece. This is particularly advantageous for small planetary gears and gears.

The G 160 gear generating grinding machine from EMAG SU features an innovative axis concept with two parallel table groups driven by linear motors. This configuration enables short chip-to-chip times of just 1.6 seconds.
How does this affect the processing time?
The effects are impressive. By moving all axes simultaneously, we achieve a chip-to-chip time of less than 2 seconds. To be precise, it is 1.6 seconds. That’s around 2.5 seconds faster than our competitors.
That sounds like a considerable time saving. How does this affect overall production?
The effects are greater than you might initially think. These 2.5 seconds saved per cycle add up to several additional production shifts over the course of a year. That is an enormous gain in productivity.
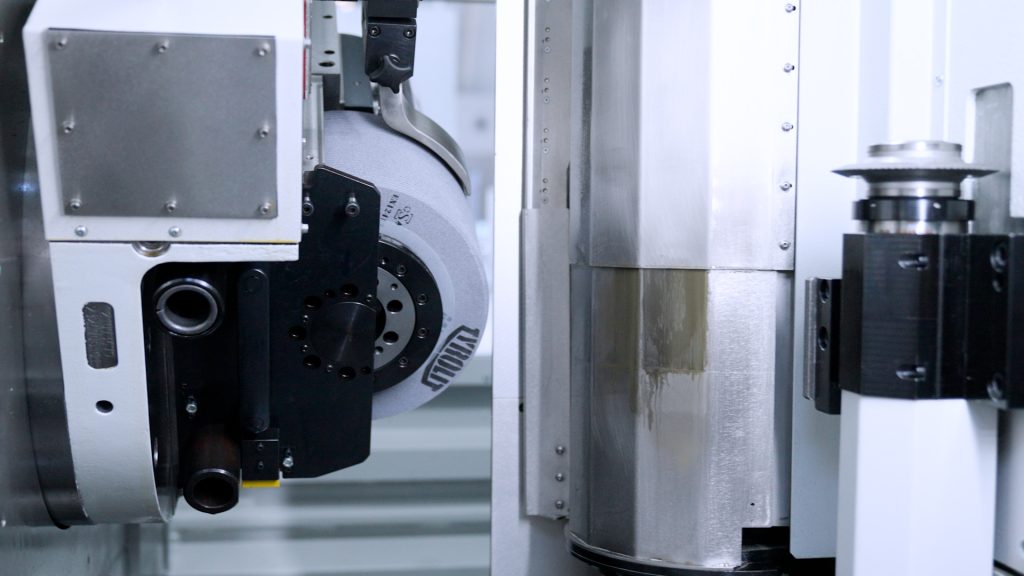
The G 160 gear generating grinding machine from EMAG SU is characterized by its quick and easy retooling. The grinding wheel can be moved into an ergonomically favorable position and the quick-change clamping devices enable rapid retooling.
Impressive. What about the quality of the machined components?
The quality is outstanding. We generally achieve a waviness (FF-Alpha) of less than two micrometers on the surface during gear generating grinding. This is an excellent result and meets the highest requirements in gear manufacturing.
What special grinding processes does the G 160 offer?
We offer a wide range of processes: topological grinding, fine grinding and polishing grinding. Particularly noteworthy are our grinding processes for noise-reduced surfaces, which were specially developed for transmission parts in electric cars.

The G 160 gear generating grinding machine from EMAG SU enables a variety of grinding processes, including topological grinding, polishing grinding, fine grinding and the production of noise-optimized tooth profiles. This flexibility ensures the highest precision and quality in gear production.
What about servicing and wear and tear on the machine?
We have placed great emphasis on ease of maintenance and durability in the design. There are no cables or open guideways in the work area. This reduces wear considerably, especially when you consider that cables are very susceptible to wear in combination with abrasion and oil.
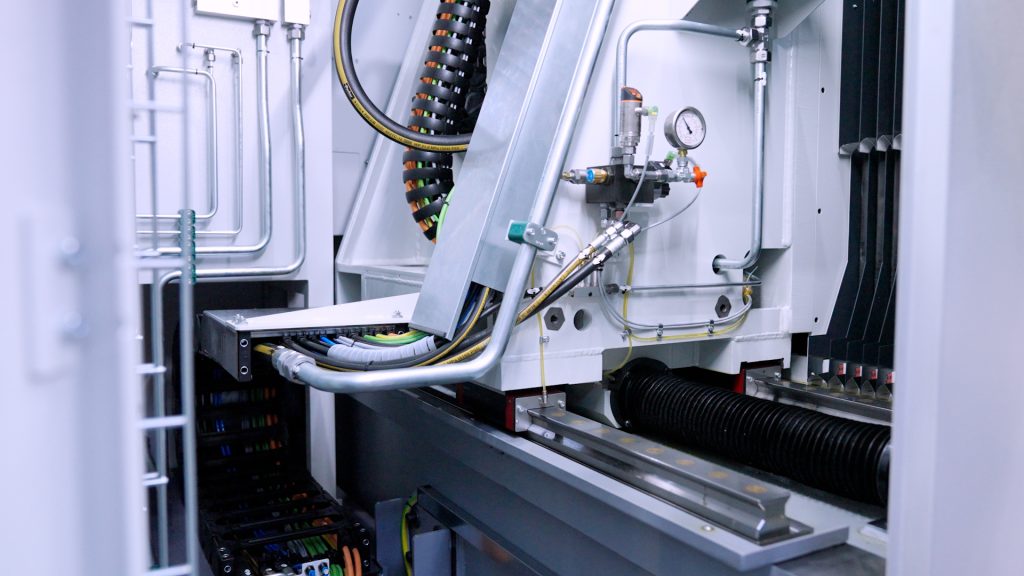
The quality-determining components such as guides and drives are located in the background, separate from the work area. This arrangement protects the important components from chips and coolant and increases the service life and precision of the machine.
Finally, one more question: How fast can the G 160 produce a gears?
For small planetary gears, we achieve lead times of just 13 seconds. This includes the entire process from inserting the blank to removing the finished gears. To our knowledge, this makes the G 160 the fastest machine of its kind on the market.