At EMAG, we know that the manufacturing market on the East Coast is an important one and with that in mind, we decided to plunge into EASTEC 2017 – and we’re so happy we did!
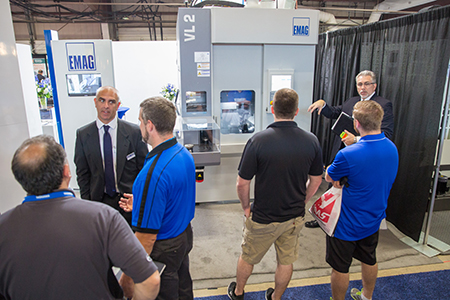
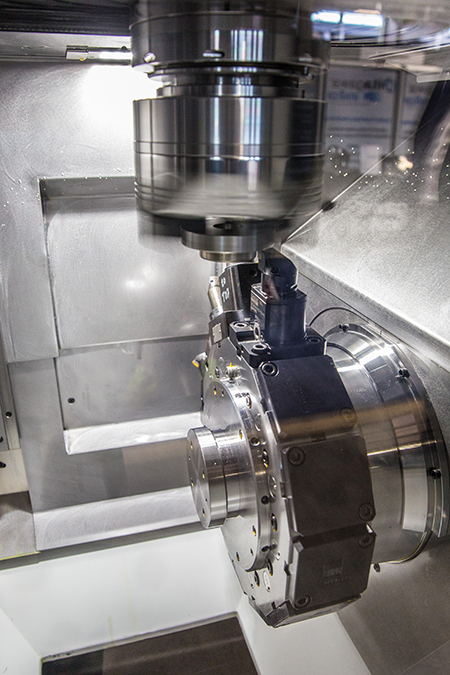
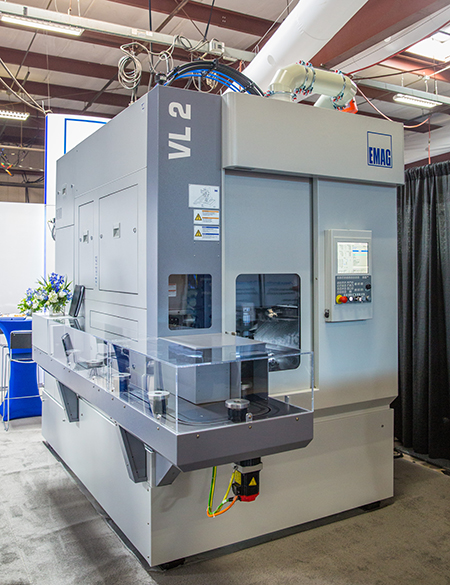
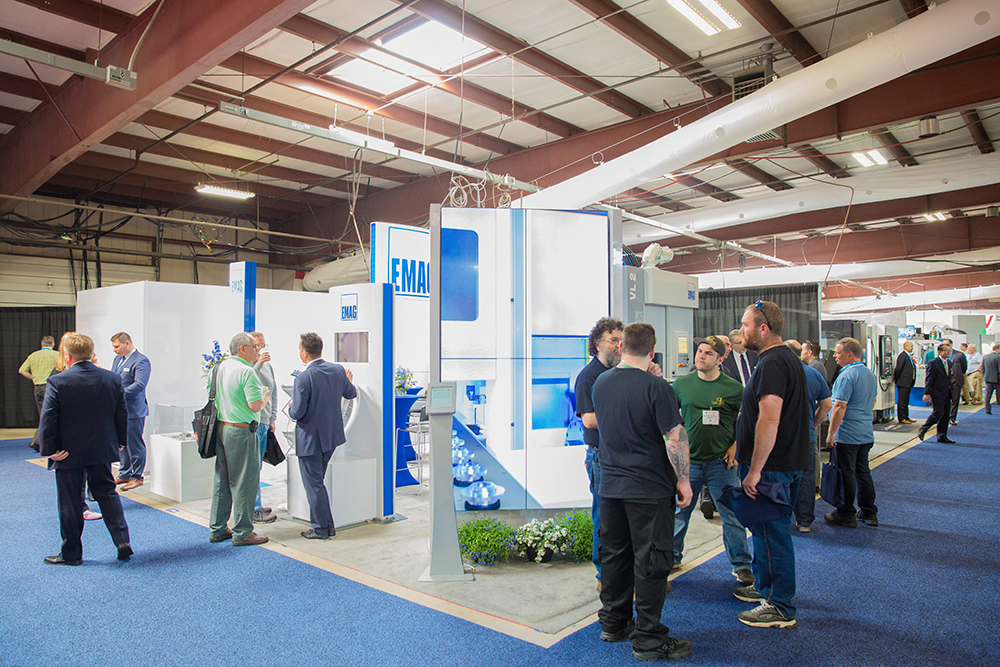
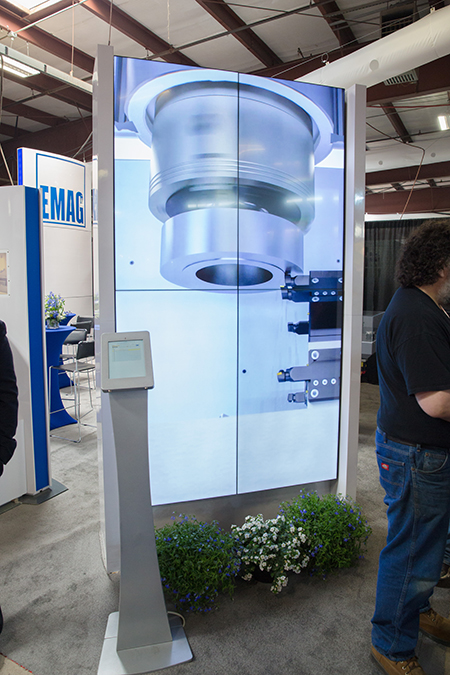
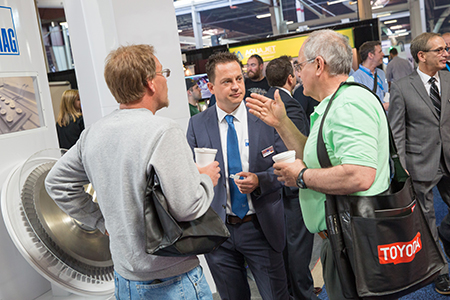
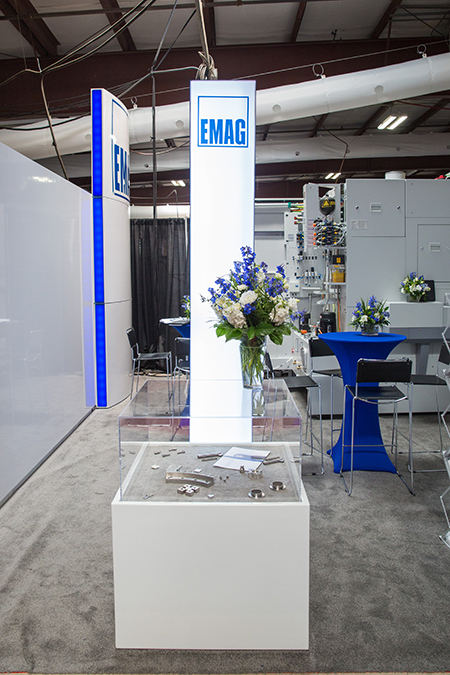
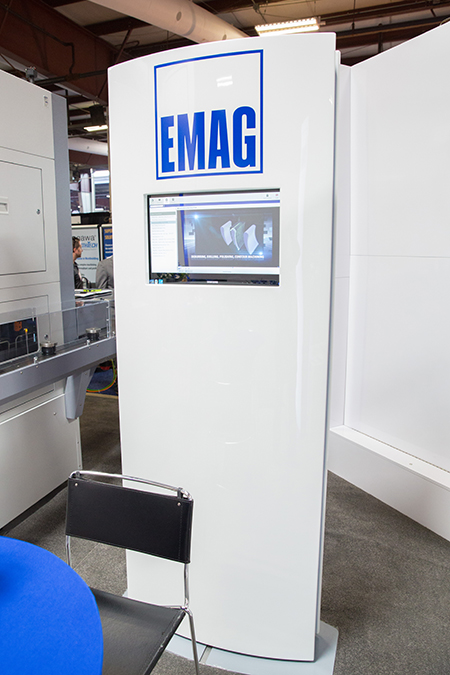
At EMAG, we know that the manufacturing market on the East Coast is an important one and with that in mind, we decided to plunge into EASTEC 2017 – and we’re so happy we did!
Today’s competitive talent marketplace requires small and medium contract manufacturers and OEM’s to make the most of the talent they have. Skilled, experienced machinists are hard to find and having them tied up hand-loading parts into a lathe is seldom the best use of talent. So – how does a successful small to mid-sized shop meet their customers’ production requirements with the existing talent pool?
Electro-chemical machining (ECM) is a fascinating production method, because the technology involves virtually no workpiece contact: A direct current, or pulse, is used to polarize the workpiece positively, to create an anode, and the tool negatively, for the cathode. An electrolyte solution flows between the two, and metal ions detach from the workpiece. The components are not exposed to any mechanical or thermal stress during the process.
EMAG’s Standard Modular Vertical Turning Solutions for chucked and shaft like components continue to gain market share within North America.
For years EMAG has continued to develop and invest in new technologies that make them the leading OEM of Manufacturing Systems for Precision Metal Components. We’ve become known world-wide for our Vertical Turning technology along with our ability to provide complete process chains to the world’s leading Automotive OEM. We’ve become the prominent leader in gear box, engines, and chassis solutions within the automotive industry but can also provide solutions within Energy, Aerospace, Agriculture, Construction and Oil Field.
Increasing cost pressure, high demands on part quality and frequent change of batches – the manufacturing of car brake discs is a difficult field. Particularly in the spare parts market, where users must request individual machining solutions that can be retooled for new workpieces without long downtimes.
EMAG ELC 250 helps with mass reduction with the laser welding of differential parts.
EMAG had seen that the world automobile market was pushing suppliers to decrease mass and reduce the overall size of driveline systems, specifically differentials. More of todays automobiles are offering an all-wheel drive or on demand four wheel drive system that require an added differential.
I continue to be amazed by the depth of product offerings that EMAG has in its arsenal – even though I have full access to all of the marketing material. However, unless one specifically seeks information on various process step combinations, these can be quickly overseen. Even our larger and more sophisticated customers often miss the opportunity to take advantage of EMAG’s unique solutions to manufacturing processes.