VL 시리즈의 모듈형 선반 - 저렴한 단가 보장
생산 성능의 도약을 보장하는 구조: VL 시리즈의 공작 기계는 자동화 장치가 통합된 공간 절약형 수직 선반입니다.
최고의 성능, 저렴한 단가 - 이러한 성능의 기반은 고품질 구성품입니다. 이 공작 기계의 본체는 댐핑 폴리머 콘크리트 MINERALIT®로 구성되어 있고, 자동화 장치는 픽업 작업 스핀들로 X축과 Z축에서 매우 빠르게 이동하며, 공구 리볼버는 짧은 회전 시간을 보장합니다.
또한 이러한 기계에는 복잡한 형태를 가공하기 위해 리볼버에 Y-축이 장착됩니다. 따라서 이 공작 기계의 적용 범위가 대폭 증가합니다.
결과: 기계의 구조가 최소한의 공간을 요구하여 높은 부품 품질과 공정 안전성을 보장합니다.
출고 시 EDNA IoT-READY: VL 시리즈의 선반으로 데이터에 최적화된 제조의 세계로 진입
데이터 분석에 의해, 예컨대 구성품 마모나 최악의 경우 기계 고장에 의한 불필요한 조업 중단 시간을 줄이거나 심지어 이러한 시간을 완전히 방지할 수 있습니다. 여기서는 10% 이상의 생산성 향상이 표준입니다. 고객이 되도록 가장 간단하게 데이터에 최적화된 제조의 세계로 진입할 수 있도록, VL 시리즈의 공작 기계를 즉시 IoT Ready로 제공합니다. 따라서 실제로 기계에서의 데이터 분석을 즉시 시작할 수 있습니다.
IoT Ready에 대한 자세한 정보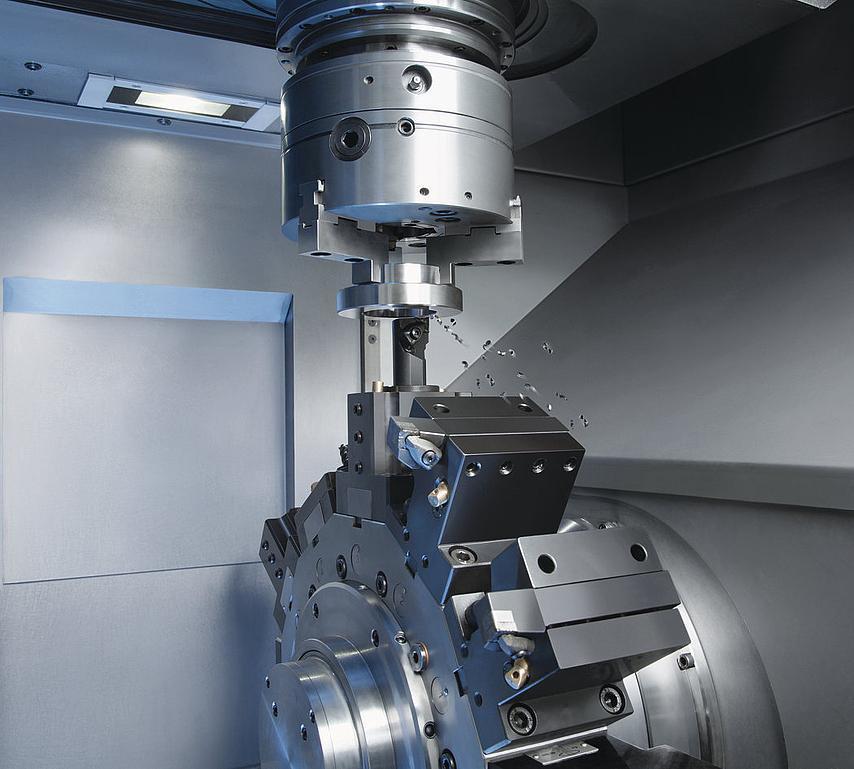
VL 시리즈 모듈형 선반의 하이라이트
- 모듈식 구조의 일관된 수직형 모델 제품군으로 다양한 버전이 가능함
- 특히 중대형 시리즈 생산용으로 적합
- 각 기계마다 완전 자동화 및 조작 기술이 통합되어 있음
- 수동 로딩용으로 설계, 그러나 간단한 자동화도 가능
- 한 사람이 여러 대의 기계 조작 시 특히 이상적
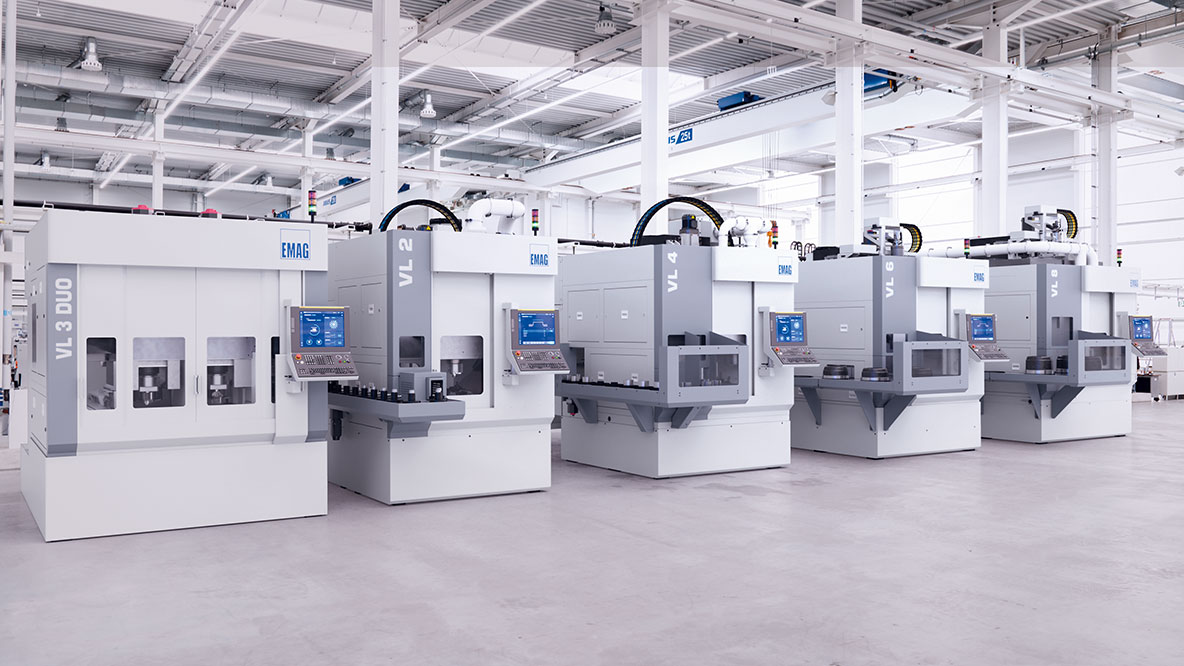
VL 시리즈 모듈형 선반의 장점
- 척 부품 가공 = 일관된 가공 컨셉
- 최소 설치 면적(Chaku-Chaku 또는 선형 배치) = 공간 비용 절감, 장비 배치의 다양한 가능성
- 전환/전향 및 중앙 공급/배출 벨트를 통한 간단한 연결 가능성 = 미래지향적인 유연성, 자동화 비용 절감, 장비의 유휴시간 단축
- 통합된 자동화 = 추가 비용 없음(인터페이스 등)
- 빠른 이송거리로 인해 유휴 시간 단축 = 유휴 시간의 최적화
- 동일 부품 전략, 통일된 예비 부품 비축 = 절감된 유지보수 비용
- 손쉬운 사용(접근이 용이한 작업 공간) = 신속한 셋업
- 높은 에너지 효율 = 낮은 에너지 비용