In der Welt der Hochpräzisionsantriebe ist Zoerkler ein Name, der für Innovation, Qualität und technische Exzellenz steht. In seiner fast 120-jährigen Geschichte hat sich das Unternehmen von einer bescheidenen mechanischen Werkstatt zu einem führenden Anbieter von Antriebssystemen für die Automobil- und Luftfahrtindustrie entwickelt. Im Interview gibt Geschäftsführer Bernhard Wagner Einblicke in die faszinierende Welt der Präzisionsfertigung, innovative Fertigungstechnologien und die Zukunftsvisionen der Zoerkler Gears GmbH & Co KG.
Werfen wir zunächst einen Blick zurück. Können Sie die Entstehungsgeschichte und die Entwicklung Ihres Unternehmens kurz skizzieren?
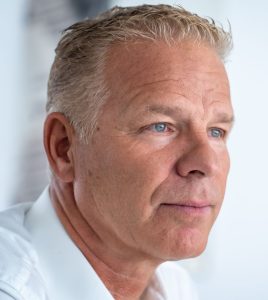
Bernhard Wagner, Geschäftsführer von Zoerkler
Gerne. Unser Unternehmen blickt auf eine fast 120-jährige Geschichte zurück. Angefangen hat es als bescheidener Familienbetrieb – eine kleine mechanische Werkstatt. Mein Großvater legte den Grundstein mit der Fertigung einfacher Ersatzteile. Im Laufe der Zeit spezialisierten wir uns immer mehr auf die Verzahnungstechnik, insbesondere für Baumaschinen.
In den folgenden Jahrzehnten expandierten wir kontinuierlich. An unserem alten Standort in Wien begannen wir auf einer Fläche von rund 1.800 Quadratmetern bereits mit der Produktion von hochwertigen Antriebssystemen und Zahnrädern. Der große Sprung gelang uns 2008 mit der Übersiedlung ins Burgenland. Hier verfügen wir über eine Produktionsfläche von 8.000 Quadratmetern, die es uns ermöglicht, hochwertige Antriebssysteme und Präzisionsteile auf höchstem Niveau zu fertigen.
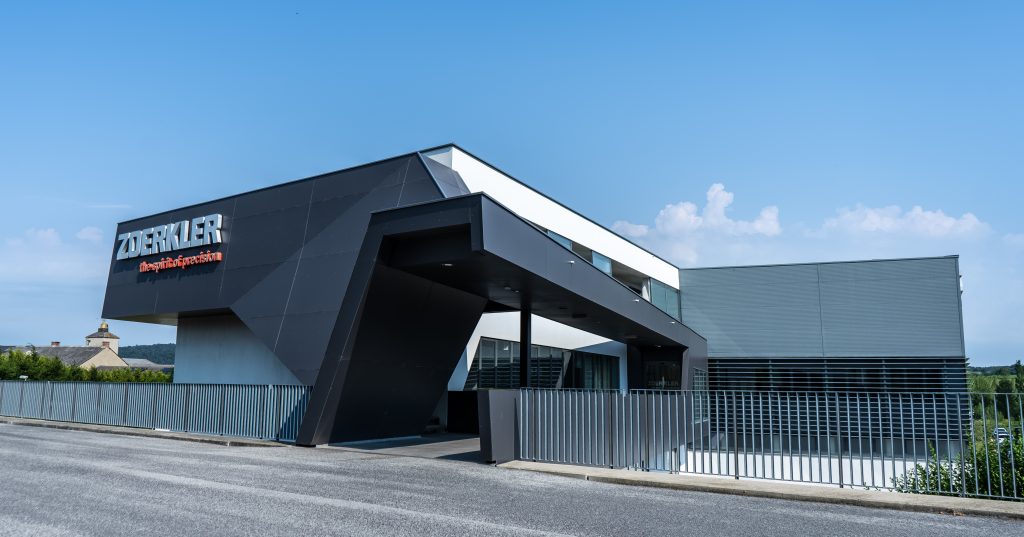
Der hohe Qualitätsanspruch spiegelt sich auch in der modernen Gestaltung der Produktionshalle wider.
Eine beeindruckende Entwicklung. Wie viele Mitarbeiterinnen und Mitarbeiter beschäftigen Sie derzeit am Standort?
Unser Team umfasst derzeit 100 Mitarbeiterinnen und Mitarbeiter. Darunter sind acht Auszubildende, was unser Engagement für die Ausbildung junger Fachkräfte unterstreicht. Etwa 15 unserer Mitarbeiterinnen und Mitarbeiter sind hochqualifizierte Konstrukteure, die in unserem Entwicklungsteam arbeiten. Der größte Teil unserer Belegschaft, nämlich 77 Mitarbeiterinnen und Mitarbeiter, ist in der Produktion tätig, wo sie ihr Wissen und Können in die Fertigung unserer Präzisionsteile einbringen.
Können Sie uns einen tieferen Einblick in Ihr Kerngeschäft geben? Sie sprachen von Präzision und hochwertigen Getrieben.
Unser Kerngeschäft ist die Entwicklung, Herstellung und Erprobung von Hochleistungs-Antriebssystemen. Dabei haben wir uns auf zwei Hauptbranchen spezialisiert: die Automobil- und die Luftfahrtindustrie. Hier sind die Anforderungen an Präzision und Zuverlässigkeit besonders hoch.
Unsere Antriebssysteme finden sich in Hochleistungsfahrzeugen, die zur absoluten Topklasse der Automobilindustrie gehören. In der Luftfahrt rüsten wir Hubschrauber und Flugzeuge mit unseren Systemen aus. Die extremen Einsatzbedingungen erfordern höchste Qualität und Zuverlässigkeit. Darüber hinaus bedienen wir auch die Schienenfahrzeug- und Landmaschinenindustrie, wo unsere Antriebssysteme ebenfalls zum Einsatz kommen. Unser Hauptfokus liegt jedoch eindeutig auf Präzisionsantriebssystemen für anspruchsvollste Anwendungen in der Automobil- und Luftfahrtindustrie.
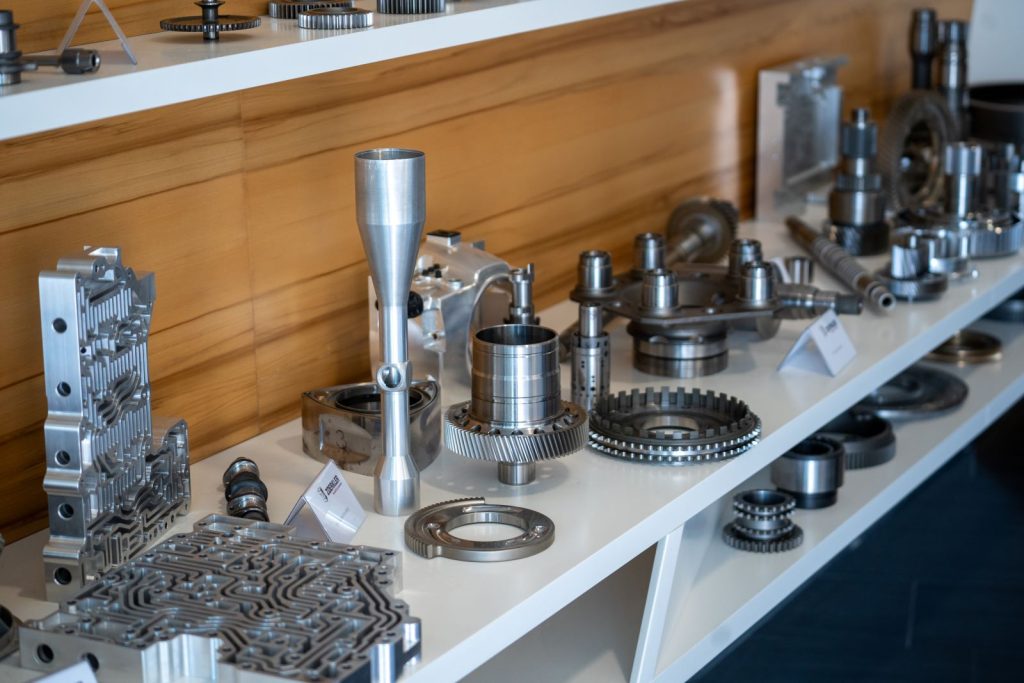
Eine Auswahl verschiedener von Zoerkler gefertigter Präzisionsteile. Die Teile variieren in Größe und Form, von kleinen Zahnrädern bis hin zu komplexen Getriebeteilen.
Auf Ihrer Website erwähnen Sie, dass Sie Antriebssysteme von der Entwicklung über die Berechnung bis hin zur Fertigung von Prototypen oder bis zur Serienreife anbieten. Können Sie diesen Prozess näher erläutern?
Selbstverständlich. Viele unserer Aufträge sind zukunftsorientierte „Built-to-Spec“-Projekte. Das heißt, wir erhalten vom Kunden detaillierte Anforderungen und Spezifikationen. Auf dieser Basis übernehmen wir den gesamten Entwicklungsprozess.
Zunächst erstellen wir ein umfassendes Layout. Unsere Ingenieure entwickeln, konstruieren und fertigen das Antriebssystem bis ins kleinste Detail. Nach Abschluss der Planungsphase beginnt die Produktion. Alle Komponenten werden im eigenen Haus gefertigt und anschließend von unseren Spezialisten montiert. Ein besonderer Mehrwert für unsere Kunden ist unser hauseigenes Prüffeld. Auf Wunsch führen wir umfangreiche Tests bis hin zur kompletten Zertifizierung des Systems durch. So ist sichergestellt, dass jedes Produkt, das unser Haus verlässt, höchsten Qualitätsstandards entspricht und für den jeweiligen Einsatzzweck optimal geeignet ist.
Das klingt nach einem sehr umfassenden Ansatz. Was ist das Besondere an einem Zoerkler-Getriebe? Was sind die Stärken Ihrer Komponenten?
Das Besondere an unseren Getrieben ist die Kombination aus höchster Qualität der Einzelkomponenten und deren perfektes Zusammenspiel im Gesamtsystem. Bei jedem einzelnen Teil legen wir größten Wert auf Präzision. Wenn diese Präzisionsteile dann zu einem System zusammengefügt werden, entsteht eine Gesamtleistung, die in puncto Zuverlässigkeit und Qualität ihresgleichen sucht. Ein wesentlicher Vorteil unseres Ansatzes ist die vollständige Integration aller Prozessschritte – vom Engineering bis zum Test – unter einem Dach. Dadurch können wir die Entwicklungszeit deutlich verkürzen. Bereits in der Engineering-Phase können wir mit großer Sicherheit sagen, dass die auf der Zeichnung angegebenen Toleranzen in der Produktion eingehalten werden.
Für unsere Kunden bedeutet dieser ganzheitliche Ansatz einen enormen Vorteil an Transparenz und Kontrolle. Sie haben die Möglichkeit, mit ihrem Team zu uns zu kommen und den gesamten Prozess vor Ort zu verfolgen – von der Konstruktion am Computer über die Fertigung und Montage bis hin zum Prüfstand. Diese Offenheit und direkte Einbindung des Kunden in den Entwicklungs- und Fertigungsprozess ist ein Alleinstellungsmerkmal, das unsere Kunden sehr schätzen.
Das ist in der Tat ein beeindruckender Ansatz. Welche Stückzahlen und Losgrößen stellen Sie typischerweise her?
Unsere Produktion ist sehr flexibel und kundenorientiert. Unsere Aufträge bewegen sich typischerweise in Losgrößen zwischen 50 und 100 Stück. So können wir jedes Produkt mit höchster Sorgfalt und Präzision fertigen, ohne Kompromisse bei der Qualität einzugehen.
Wir haben aber auch einige Serienaufträge in unserem Portfolio, bei denen wir deutlich größere Stückzahlen produzieren. In diesen Fällen liefern wir mitunter 800 bis 900 Stück pro Woche. Diese Bandbreite zeigt, dass wir in der Lage sind, sowohl Kleinserien als auch größere Produktionsvolumina effizient abzuwickeln. Ein wichtiger Aspekt unserer Produktion ist, dass wir ausschließlich kundenspezifische Lösungen herstellen. Wir haben keine Lagerware, jedes Teil wird nach den individuellen Anforderungen unserer Kunden gefertigt. Reine Lohnfertigung betreiben wir nur in sehr geringem Umfang, da unsere Aufträge in der Regel ein hohes Maß an spezifischem Know-how erfordern.
Besonders geschätzt wird von unseren Kunden auch unser Engagement in der Prototypenentwicklung. Auch wenn die Entwicklung nicht von uns stammt, unterstützen wir die Entwicklungsabteilungen der OEMs mit unserem umfangreichen Fertigungs-Know-how bei der Herstellung von Prototypen. Diese Fähigkeit, flexibel auf unterschiedliche Kundenanforderungen zu reagieren und dabei stets höchste Qualität zu liefern, ist einer der Gründe, warum unsere Kunden uns als wertvollen Partner schätzen.
Können Sie uns einen Einblick in die Technologien und Prozessschritte geben, die Sie hier bei der Getriebefertigung einsetzen?
Sehr gerne. Wir sind stolz darauf, dass wir nahezu alle Prozessschritte der Getriebefertigung im eigenen Haus durchführen können. Unsere Fertigungskette beginnt beim Rohmaterialeinkauf und umfasst alle wesentlichen Bearbeitungsschritte. Für die Grundbearbeitung setzen wir modernste Dreh- und Fräsmaschinen ein. Danach kommen unsere hochpräzisen Schleifverfahren, sowohl Rundschleifen als auch Koordinatenschleifen, zum Einsatz, um die geforderten engen Toleranzen zu erreichen.
Ein besonderer Schwerpunkt liegt natürlich in der Verzahnungstechnik. Hier verfügen wir über ein breites Spektrum an Möglichkeiten. Wir können Innenverzahnungen schrägstoßen und -schleifen, was besonders bei Kompaktgetrieben von Vorteil ist. Auch die Herstellung von Zahnkränzen und Ringverzahnungen gehört zu unserem Repertoire, selbst bei kleinsten Abmessungen.

Detailansicht eines Präzisionszahnrads
Eine unserer Spezialitäten sind Kegelradverzahnungen für Hubschrauber, insbesondere solche mit Winkel ungleich 90 Grad. Hier haben wir uns als absolute Spezialisten etabliert.
Für die Automobilindustrie ist das Thema NVH (Noise, Vibration, Harshness) von großer Bedeutung. Auch in diesem Bereich haben wir eine besondere Kompetenz entwickelt, insbesondere bei der Optimierung des Schwingungsverhaltens und der Mikrogeometrie. Diese Aspekte untersuchen wir sorgfältig auf eigenen Prüfständen. Diese Vielfalt an Technologien und unser tiefes Verständnis jedes einzelnen Prozessschrittes ermöglichen es uns, selbst komplexeste Antriebssysteme in höchster Qualität zu fertigen.
Dieses breite Technologiespektrum stellt sicher hohe Anforderungen an Ihr Team. Können Sie näher darauf eingehen, wie Sie diese Herausforderung meistern?
Unser Team ist zweifellos unser wertvollstes Kapital. Wir haben zwar hochmoderne Maschinen, aber es sind unsere hervorragend ausgebildeten Mitarbeiterinnen und Mitarbeiter, die diese Technologie mit Leben füllen und ihr volles Potenzial ausschöpfen. Wir legen großen Wert auf die Ausbildung unseres Nachwuchses. Jedes Jahr stellen wir 2 bis 4 Lehrlinge ein und bieten ihnen neben einer fundierten Berufsausbildung auch die Möglichkeit, die Matura zu absolvieren. Diese jungen Fachkräfte sind unsere Zukunft – viele von ihnen entwickeln sich zu unseren zukünftigen Führungskräften und Teamleitern.
Die wahre Stärke unseres 100-köpfigen Teams liegt in der Kombination aus umfassender Ausbildung, dem großen Können jedes Einzelnen und dem perfekten Zusammenspiel. Ich vergleiche unser Team gerne mit Spezialeinheiten – jeder Einzelne ist hoch qualifiziert, aber die wahre Stärke entfaltet sich im Zusammenspiel. Diese Mischung aus Fachwissen, Erfahrung und Teamgeist ermöglicht es uns, auch komplexe Herausforderungen zu meistern und innovative Lösungen zu entwickeln. Unsere Mitarbeiterinnen und Mitarbeiter sind nicht nur Experten in ihrem jeweiligen Fachgebiet, sondern verstehen auch die Zusammenhänge im Gesamtprozess. Das macht uns besonders und befähigt uns zu Spitzenleistungen.
Sprechen wir über Ihre EMAG Maschine. Warum haben Sie sich entschieden, Kleinserien und häufig wechselnde Teile auf einer Pick-up-Vertikaldrehmaschine und nicht auf einer klassischen Horizontalmaschine zu fertigen?
Die Entscheidung für die EMAG Maschine basierte auf mehreren ausschlaggebenden Faktoren. Der Hauptgrund war, dass wir eine Lösung für die automatisierte Bearbeitung von schwereren Werkstücken bei gleichzeitig höchster Genauigkeit und Zuverlässigkeit benötigten.
Die vertikale Bauweise der EMAG VL 6 bietet uns hier entscheidende Vorteile. Trotz häufigem Umrüsten – wir wechseln mehrmals pro Woche die zu fertigenden Teile – sind wir mit der gleichbleibend hohen Maßhaltigkeit sehr zufrieden. Das ist bei unseren Präzisionsteilen besonders wichtig.
Ein weiterer wichtiger Aspekt sind die vielfältigen Bearbeitungsmöglichkeiten. Wir nutzen sowohl das Hartdrehen als auch die integrierten Fräsbearbeitungen intensiv. Diese Multifunktionalität ermöglicht es uns, komplexe Teile in einer Aufspannung zu bearbeiten, was die Genauigkeit erhöht und die Durchlaufzeiten verkürzt.
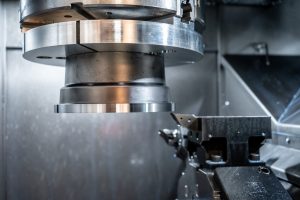
Vertikaler Arbeitsraum der Drehmaschine EMAG VL 6 mit eingespanntem Getriebegehäuse während der Bearbeitung.
Letztlich hat uns die Kombination aus der Komplexität der Bearbeitungsmöglichkeiten, der erreichbaren Genauigkeit, der hohen Verfügbarkeit der Maschine und nicht zuletzt der hervorragende Service von EMAG überzeugt. Diese Maschine passt perfekt zu unseren Anforderungen an Flexibilität und Präzision in der Kleinserienfertigung.
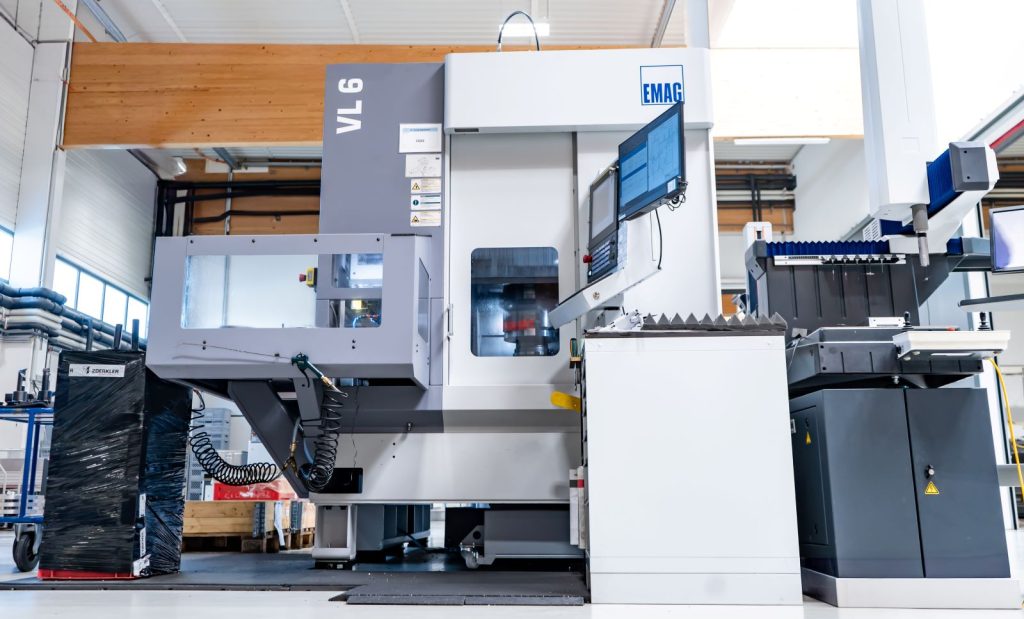
Moderne Fertigungshalle mit der vertikalen Pick-up-Drehmaschinen VL 6 von EMAG bei Zoerkler.
Welchen Einfluss hat das Automatisierungssystem von EMAG auf Ihre Produktionsprozesse?
Der Einfluss des Automatisierungssystems ist beträchtlich, aber es ist wichtig zu betonen, dass es seine volle Wirkung erst im Zusammenspiel mit der hervorragenden Maßhaltigkeit und Qualität der gesamten Anlage entfaltet. Ein konkretes Beispiel: Wir nutzen die Möglichkeit, die Maschine in der zweiten und dritten Schicht häufig autonom laufen zu lassen. Dies wäre ohne die außerordentliche Stabilität und Präzision der Anlage nicht möglich. Die Kombination aus zuverlässiger Automatisierung und konstanter Genauigkeit ermöglicht es uns, rund um die Uhr effizient zu produzieren, ohne Abstriche bei der Qualität machen zu müssen. Das ist für uns von unschätzbarem Wert. Er erhöht nicht nur unsere Produktivität, sondern gibt uns auch die Flexibilität, auf wechselnde Auftragslagen schnell und effizient zu reagieren.
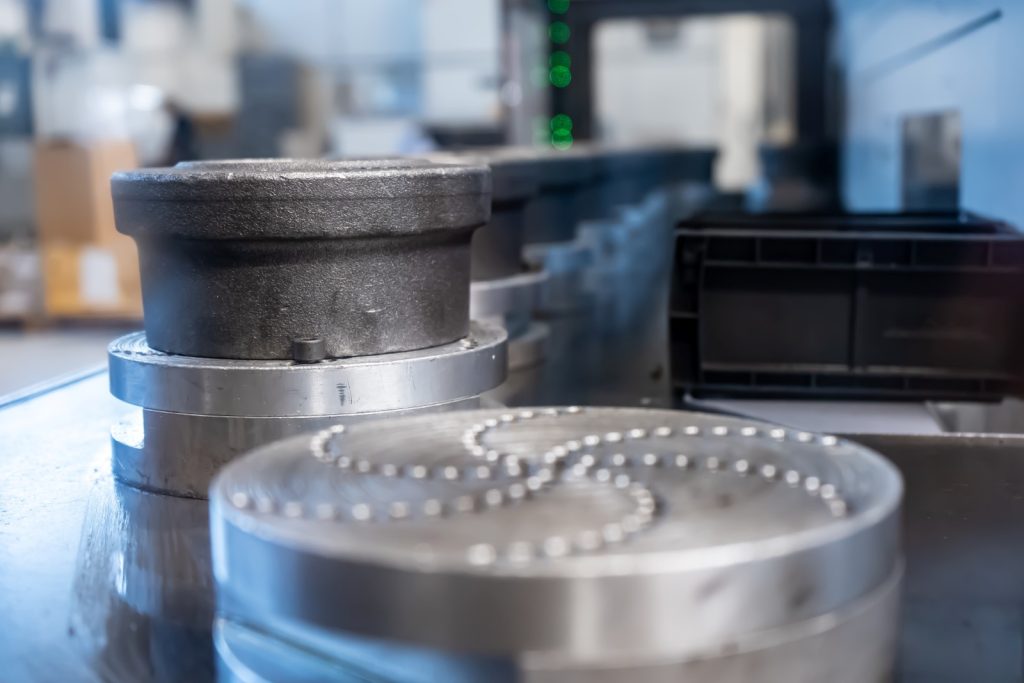
Automationsband der EMAG VL 6 mit mehreren Werkstücken in Reihe zur automatisierten Bearbeitung. Das Band transportiert die Werkstücke zur Pick-up-Station und ermöglicht so einen kontinuierlichen und effizienten Produktionsfluss.
Qualitätssicherung ist zweifellos ein kritischer Aspekt, insbesondere bei Ihren Luftfahrtaufträgen mit ihren strengen Dokumentationsanforderungen. Wie stellen Sie sicher, dass Sie diese hohen Standards erfüllen?
Qualitätssicherung hat für uns oberste Priorität. Wir haben ein ausgeklügeltes QS-System implementiert, das alle Bereiche unserer Fertigung abdeckt. Speziell für die EMAG Maschine haben wir eine hochpräzise Messmaschine direkt neben der Anlage installiert. Diese ermöglicht kontinuierliche Zwischenprüfungen während des Fertigungsprozesses. Alle Messergebnisse werden automatisch elektronisch erfasst und dokumentiert, sodass eine lückenlose Rückverfolgbarkeit gewährleistet ist.
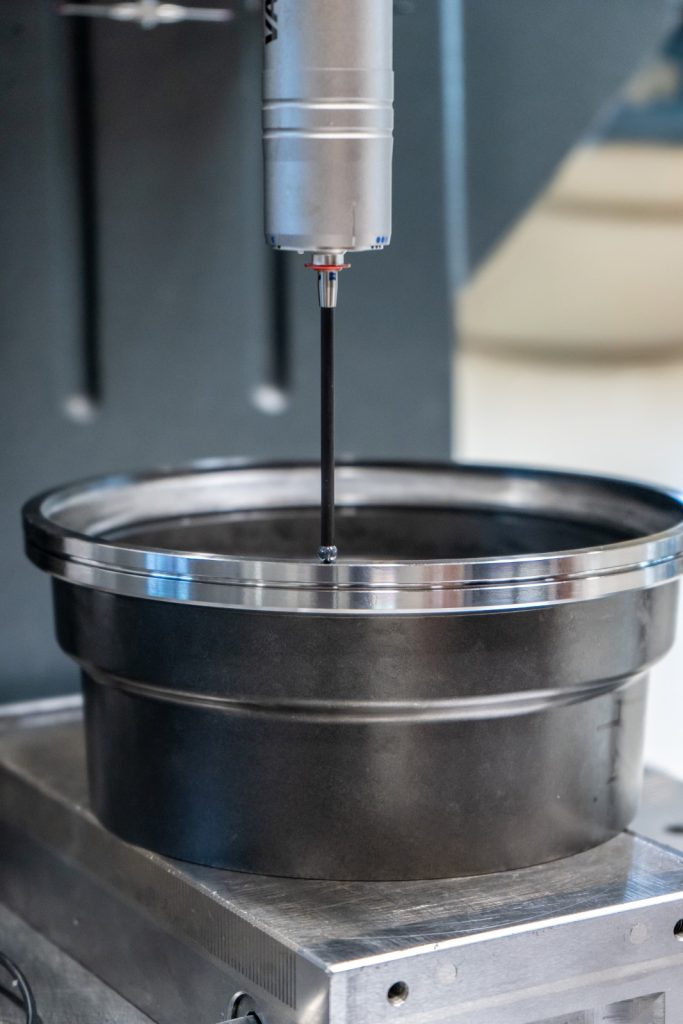
Hochpräzise Messmaschine bei der Prüfung eines Getriebegehäuses.
Unser Qualitätssicherungssystem geht jedoch weit darüber hinaus. Wir verfolgen einen ganzheitlichen Ansatz, bei dem jedes Teil chargenbezogen verwaltet wird. Für jede Charge erstellen wir einen umfassenden Dokumentationsbericht, der die gesamte Produktionshistorie abbildet – von der Herkunft des Rohmaterials bis hin zu jedem einzelnen Bearbeitungsschritt.
Für die Luftfahrtindustrie ist die lückenlose Dokumentation aller Prozesse besonders wichtig. Dazu gehören nicht nur technische Daten, sondern auch Informationen über die beteiligten Mitarbeiterinnen und Mitarbeiter und die eingesetzten Technologien. Diese Daten werden sozusagen „eingefroren“ und archiviert, um jederzeit eine lückenlose Rückverfolgbarkeit zu gewährleisten. Dieser umfassende Ansatz zur Qualitätssicherung und Dokumentation ist nicht nur eine Notwendigkeit in der Luftfahrtindustrie, sondern auch ein wesentlicher Bestandteil unserer Unternehmensphilosophie. Sie ermöglicht es uns, gleichbleibend hochwertige Produkte zu liefern und das Vertrauen unserer Kunden zu rechtfertigen.
Der Wechsel von der horizontalen zur vertikalen Bauweise bei der VL 6 war sicherlich eine Umstellung. Wie sind Ihre Mitarbeiter mit diesem Konzeptwechsel umgegangen?
Die Umstellung auf die vertikale Bauweise der VL 6 war in der Tat eine große Veränderung, aber ich bin stolz darauf, wie gut unser Team diese Herausforderung gemeistert hat. Die Vorteile der vertikalen Bauweise, insbesondere in Kombination mit der Automatisierung und dem Pick-up-System, lagen für uns auf der Hand. Wir erreichen deutlich höhere Genauigkeiten beim Spannen und Wenden der Werkstücke, was direkt zur Qualität unserer Produkte beiträgt.
Was die Umstellung für unsere Mitarbeiter betrifft, hatte ich volles Vertrauen in ihr Können und ihre Anpassungsfähigkeit. Die 90-Grad-Drehung in der Bearbeitungslogik war zwar anfangs eine Herausforderung, aber unsere Techniker und Ingenieure haben sie mit Begeisterung und Professionalität und mit der Unterstützung der EMAG Techniker gemeistert. Wir haben die Umstellung mit umfangreichen Schulungen und einer schrittweisen Einführung begleitet. So konnten sich unsere Mitarbeiterinnen und Mitarbeiter mit dem neuen Konzept vertraut machen und ihre Erfahrungen in die Umsetzung einbringen.
In der Praxis hat sich gezeigt, dass mein Vertrauen in unser Team voll gerechtfertigt war. Sie haben sich nicht nur schnell an die neue Technologie gewöhnt, sondern auch innovative Wege gefunden, das Potenzial der Maschine voll auszuschöpfen. Heute arbeiten unsere Mitarbeiter mit der Vertikalmaschine genauso selbstverständlich und effizient wie zuvor mit den Horizontalmaschinen. Diese erfolgreiche Umstellung unterstreicht einmal mehr die Kompetenz und Flexibilität unseres Teams – Eigenschaften, die in unserer schnelllebigen und technologiegetriebenen Branche von unschätzbarem Wert sind.
Ein faszinierender Aspekt Ihres Unternehmens, über den wir noch nicht ausführlich gesprochen haben, sind Ihre Teststände. Können Sie uns mehr darüber erzählen?
Sehr gerne. Unsere Teststände sind in der Tat ein wesentlicher Bestandteil unseres Leistungsspektrums und ein wichtiger Faktor für unseren Erfolg. Wir verfügen über ein große Bandbreite an hochmodernen Testeinrichtungen, mit denen wir unsere Produkte unter realistischen und oft extremen Bedingungen prüfen können. Ein Highlight ist unser Hochleistungs-Hubschraubergetriebeprüfstand. Dieser kann Leistungen von bis zu 2 x 4 Megawatt, Drehzahlen von bis zu 26.000 Umdrehungen pro Minute und Drehmomente von bis zu 180.000 Newtonmetern bewältigen. Damit können wir selbst die anspruchsvollsten Zertifizierungstests für Hubschraubergetriebe durchführen.
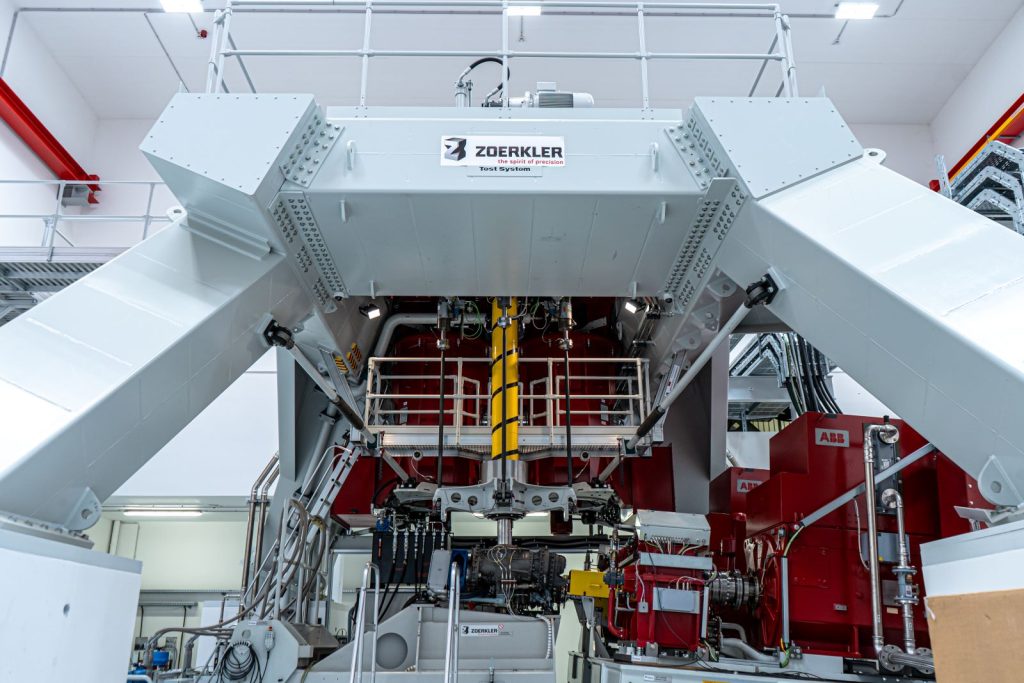
Kraft unter Kontrolle: Der beeindruckende Hubschrauber-Getriebeprüfstand von Zoerkler.
Im Bereich der Elektromobilität haben wir spezielle Prüfstände mit Batteriesimulation entwickelt. Damit können wir E-Antriebe sowohl elektrisch über den Inverter als auch mechanisch testen. Ein besonderer Schwerpunkt liegt dabei auf NVH-Analysen (Noise, Vibration, Harshness), die für den Fahrkomfort und die Effizienz von Elektrofahrzeugen entscheidend sind. Für die Automobilindustrie bieten wir umfassende Dienstleistungen an, die von der kompletten Serienentwicklung bis zur Erprobung von Getrieben und Elektroantrieben reichen. Darüber hinaus sind wir beratend tätig, insbesondere wenn es um die Optimierung von Getrieben geht. Ein typisches Szenario ist zum Beispiel die Behebung von Geräuschproblemen bei bestimmten Drehzahlen. Hier setzen wir hochsensible Schwingungs- und Geräuschsensoren ein, um eine genaue Analyse und darauf aufbauend eine Getriebeoptimierung durchzuführen.
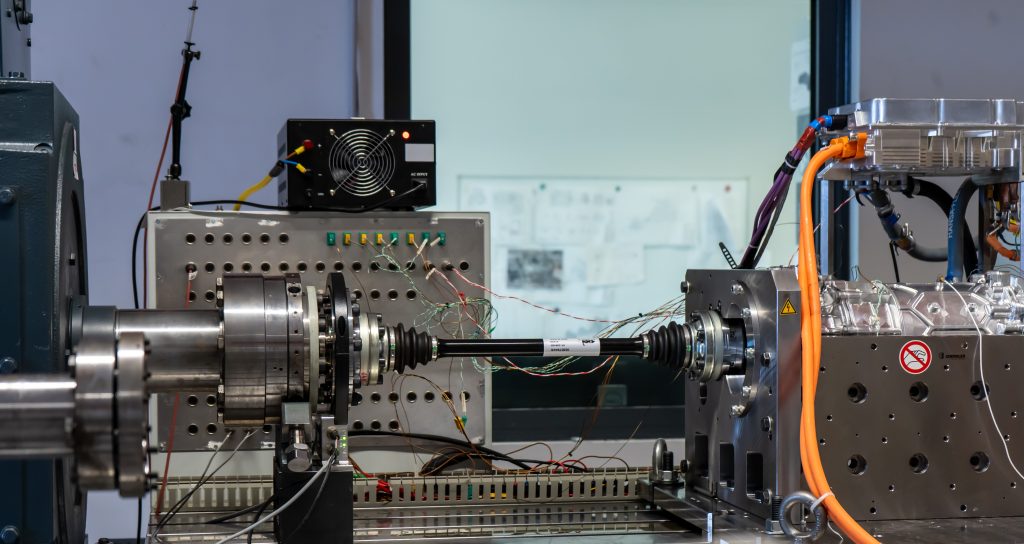
Zukunft der Mobilität: Der E-Antriebsprüfstand von Zoerkler
Diese Teststände sind nicht nur ein wichtiges Instrument zur Qualitätssicherung, sondern auch ein wesentlicher Bestandteil unseres Entwicklungsprozesses. Sie ermöglichen es uns, innovative Lösungen zu entwickeln und zu validieren, bevor sie in Serie gehen. Das reduziert nicht nur Risiken, sondern beschleunigt den Entwicklungsprozess erheblich.
Zum Schluss möchte ich noch einen Blick in die Zukunft werfen. Wo sehen Sie das Unternehmen Zoerkler in den nächsten Jahren? Welche strategischen Ziele verfolgen Sie?
Unsere Vision für die Zukunft ist klar und ehrgeizig: Wir wollen die Marke Zoerkler als einen der führenden Namen in der Automobil- und Luftfahrtindustrie etablieren. Konkret bedeutet dies, dass wir bei zukünftigen Entwicklungsprojekten in Schlüsselbranchen wie Helikopter, Jet und Supercar eine noch bedeutendere Rolle spielen wollen. Wir verstehen uns als Innovationstreiber und wollen unsere Position als bevorzugter Partner für hochkomplexe Antriebslösungen weiter ausbauen.
Ein wichtiger Aspekt unserer Strategie ist die kontinuierliche Investition in Forschung und Entwicklung. Wir beobachten Trends wie Elektrifizierung, autonomes Fliegen und neue Werkstoffe sehr genau und arbeiten daran, unsere Kompetenzen in diesen Bereichen weiter auszubauen.
Nachhaltigkeit ist ein weiteres zentrales Thema für uns. Wir arbeiten intensiv daran, unsere Produkte und Prozesse noch umweltfreundlicher zu gestalten, ohne Kompromisse bei der Leistungsfähigkeit einzugehen. Wir sehen dies nicht nur als ethische Verpflichtung, sondern auch als Wettbewerbsvorteil in einem zunehmend umweltbewussten Markt.
Nicht zuletzt setzen wir weiterhin auf unser wichtigstes Kapital: unsere Mitarbeiterinnen und Mitarbeiter. Wir werden weiterhin in die Aus- und Weiterbildung unserer Mitarbeiterinnen und Mitarbeiter investieren und ein Arbeitsumfeld schaffen, das Innovation und Spitzenleistungen fördert.
Unser Ziel ist es, unsere Position als Technologieführer und verlässlicher Partner in unseren Kernmärkten weiter zu stärken und gleichzeitig neue Märkte zu erschließen. Wir sind überzeugt, dass wir mit unserem Know-how, unserer Innovationskraft und unserem engagierten Team für diese Herausforderungen bestens gerüstet sind. Wir freuen uns mit EMAG einen verlässlichen Partner für unsere ehrgeizigen Zukunftsziele gefunden haben.