Mit der neuen Maschine VST 50 nimmt sich EMAG erstmals einer ebenso speziellen wie anspruchsvollen Aufgabe an: der Bearbeitung von Kugelzapfen und Kugelhülsen; in der Lenkung oder Aufhängung von Pkws sind diese Bauteile zum Beispiel unverzichtbar. Was zeichnet die VST 50 im Detail aus und wie lassen sich in diesem Bereich extreme Span-zu-Span-Zeiten von unter zwei Sekunden erreichen? Lesen Sie hier ein Gespräch mit Dr. Mathias Klein, CSO der EMAG Gruppe, über diese Herausforderung.
Herr Dr. Klein, warum hat sich EMAG überhaupt mit der Bearbeitung des Kugelzapfens beschäftigt?
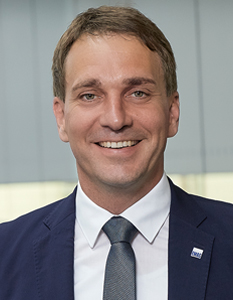
Dr. Mathias Klein
Ein großer Automobilzulieferer kam mit dieser Aufgabe auf uns zu, weil er seine bisherigen Maschinen ersetzen wollte. Diese sind rund 20 Jahre alt und entsprechen somit in verschiedenen Details nicht mehr dem aktuellen Stand der Technik im Maschinenbau. Es stellte sich also die Frage, ob wir diese für uns neue Bearbeitungsaufgabe lösen können – und das mit sinkenden „Costs per Piece“ und mit höherer Prozesssicherheit. Das war der Startpunkt für die Entwicklung der VST 50.
Was ist das Besondere an einem Kugelzapfen?
Zunächst einmal muss man betonen, dass Kugelzapfen tatsächlich sehr häufig in unseren Pkws vorkommen – je nach Modell 8- bis 18-mal, wobei es übrigens keine Rolle spielt, ob es sich dabei um Elektroautos oder Verbrenner handelt. Folglich werden jetzt und in Zukunft sehr viele dieser Bauteile hergestellt und es geht dabei jedes Mal um perfekte Oberflächen sowie extreme Maßgenauigkeiten. Vor diesem Hintergrund kann man sicher von einer typischen EMAG Aufgabe sprechen.
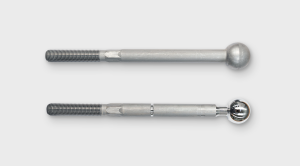
Die neue VST 50 von EMAG sorgt für eine rasante Bearbeitung der Kugelzapfen. Dabei sind hochpräzise Oberflächen im Fokus.
Wie haben Sie die Aufgabe gelöst?
Unsere übergreifende Zielsetzung war es, eine hochautomatisierte Lösung zu entwickeln, die sich einfach bedienen lässt und zugleich mit einer besonderen Prozesssicherheit punktet. Das prägt die VST 50 in vielen Details. Für die eigentliche Drehbearbeitung von Kugel und Hals des Kugelzapfens – hauptsächlich um diesen Bereich geht es hier – gibt es im Arbeitsraum zwei hängende Werkstückspindeln, die sich kombiniert verfahren lassen. Folglich können wir eine Spindel be- und entladen, während die andere beim Bearbeitungsprozess im Einsatz ist. Der dazugehörige Kreuzschlitten mit den Werkzeugen ist gewissermaßen zweigeteilt: Die Werkzeuge für die Kugel und für das finale Glätten lassen sich per B-Achse für die Kugeloberfläche drehen und per U-Achse zustellen. Daneben befinden sich die Werkzeuge für den Hals.
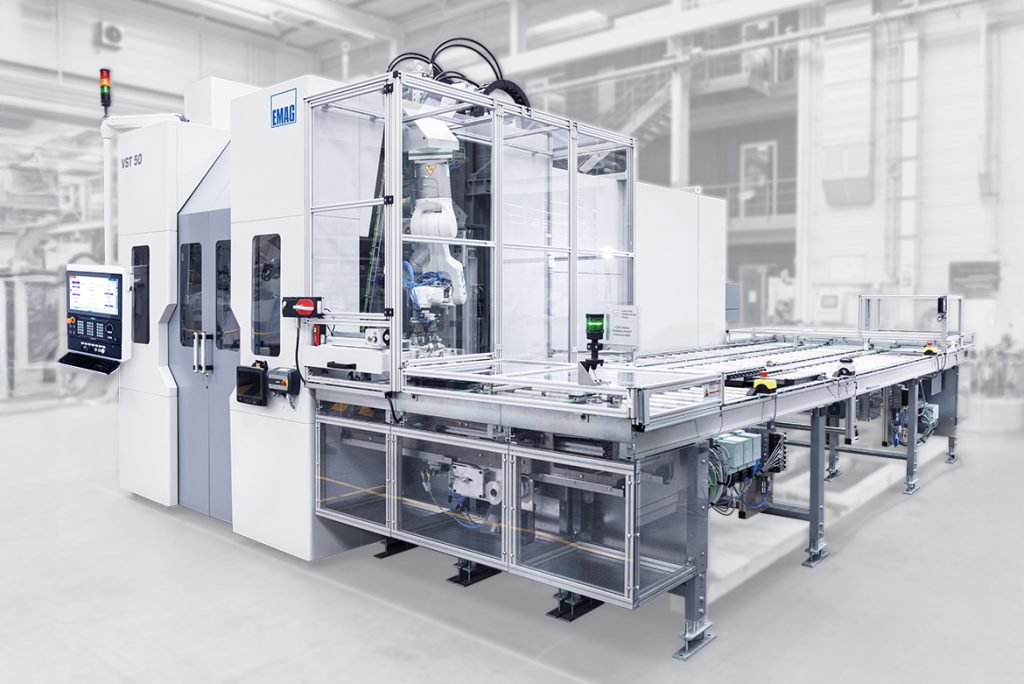
Inklusive Automation ist die VST 50 für die hochproduktive Fertigung ausgelegt.
Auf welche Weise kommen die Werkstücke nun in den Arbeitsraum?
Das ist das zweite Herzstück unserer Lösung, bei der wir auf drei parallel angeordnete Roboter setzen – jeder übernimmt einen anderen Teilprozess im Werkstückfluss: Der linke Roboter transportiert die Werkstücke von der Übergabestation zur linken Werkstückspindel, der mittlere erledigt das Gleiche an der rechten Werkstückspindel und der rechte Roboter transportiert die Werkstücke von der Übergabestation nach außen.
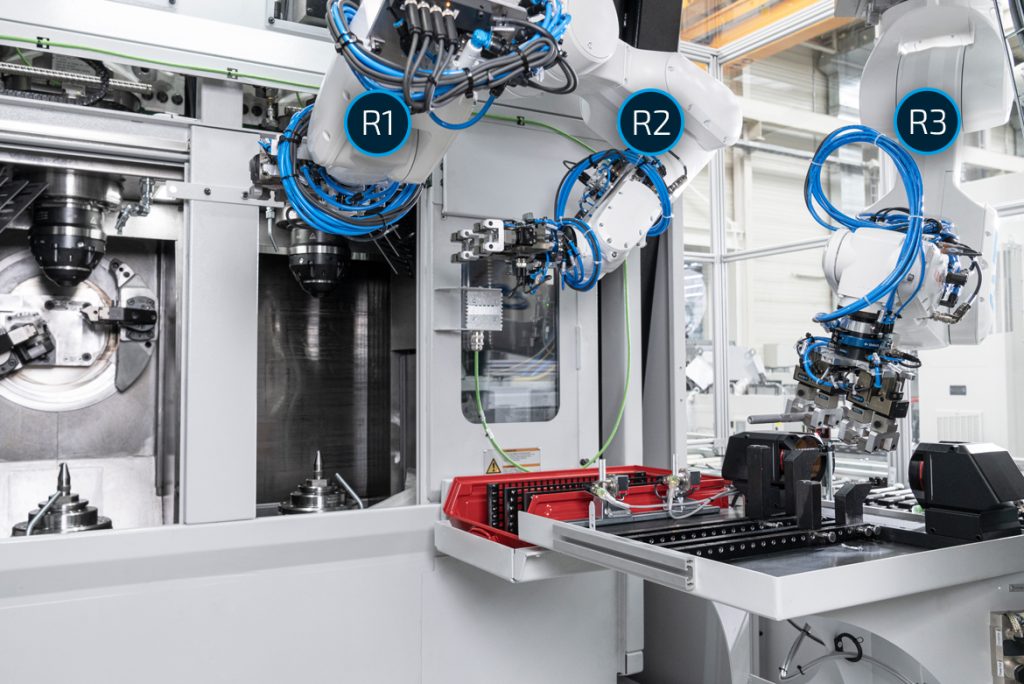
Drei parallel angeordnete Roboter sorgen in der VST 50 für das Teilehandling inklusive Werkzeugwechsel und Qualitätskontrolle.
Könnte diese Aufgabe nicht auch von nur einem Roboter ausgeführt werden?
Das wäre möglich, allerdings würden wir somit die angestrebten extrem kurzen Taktzeiten nicht erreichen. Unsere Lösung sorgt dafür, dass alle sieben Sekunden ein fertiges Werkstück die Maschine verlässt und die Span-zu-Span-Zeit weniger als zwei Sekunden beträgt. Außerdem erfolgt das gesamte Handling „definiert“. Die Teile werden also nicht in irgendeiner Weise abgeworfen und dabei beschädigt.
Wie vollzieht sich der Werkzeugwechsel?
Zunächst ist es wichtig, dass die VST 50 eine Vorhersage zum Werkzeugwechsel auf ihrem Panel macht. Hier sieht der Bediener also, ob der nächste Wechsel bereits ansteht. Wenn das der Fall ist, drückt er einfach eine Taste und eines der Werkzeugmagazine schwenkt für den Tausch nach außen. Die Panel-Anzeige verdeutlicht dabei per Farbe, welche Werkzeuge konkret verschlissen sind; so wird eine Fehlbedienung verhindert. Nach dem Austausch schwenkt das Magazin zurück in seine Ausgangsposition und den Rest erledigt der Roboter: Dazu legt er zunächst seinen Werkstückgreifer ab und nimmt einen Werkzeuggreifer auf. Anschließend entnimmt er das verschlissene Werkzeug aus dem Innenraum der Maschine und tauscht es gegen ein neues, das er aus dem befüllten Magazin entnimmt. Der gesamte Werkzeugwechsel per Roboter vollzieht sich dabei in weniger als 90 Sekunden.
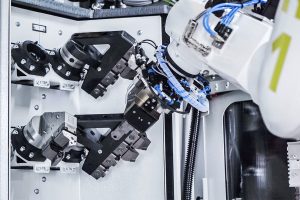
Die Roboter be- und entladen nicht nur die
Maschine (hier im Bild), sondern sorgen auch
für den Werkzeugwechsel.
Was für eine Rolle spielt die Prozesssicherheit bei Ihrer Lösung?
Das ist ein entscheidender wirtschaftlicher Faktor. Auf der einen Seite gibt es deshalb ein Lichtband-Mikrometer, das die finalen Kugel- und Halsdurchmesser bestimmt und zugleich etwaige Späne detektiert. Alle fertigen Bauteile durchlaufen diese Messung. Fehlteile werden sofort entfernt. Auf der anderen Seite befinden sich Prozess-Kameras vor den Ladeluken. Mit ihrer Hilfe kann der Bediener den Bearbeitungsprozess per Bedienpanel beobachten – das Live-Kamerabild wird hier auf Wunsch eingeblendet. Darüber hinaus haben wir sogar noch eine Teileerkennung am Förderband integriert.
Welche Marktchancen hat diese Lösung aus Ihrer Sicht?
Wir sind überzeugt davon, dass wir mit der VST 50 die Bearbeitung von Kugel und Hals am Kugelzapfen auf ein neues Level heben, denn die Lösung ist doppelt so schnell wie hergebrachte Produktionslösungen, was letztlich für deutlich sinkende Stückkosten sorgt. Darüber hinaus ist die Messung außerhalb des Arbeitsraums außergewöhnlich genau und umfassend, der Werkzeugwechsel erfolgt vollautomatisch und nicht zuletzt ermöglichen unsere EDNA Apps eine weitgehend intuitive Bedienung, was die Nutzung der Maschinen vereinfacht. Lassen Sie es mich so zusammenfassen: Wir heben die Produktion des Kugelzapfens auf ein neues Niveau.