Mit EDNA verfügt EMAG über ein vollständiges Ökosystem für die Digitalisierung der industriellen Produktion. Dabei war die Entwicklung echtes Teamwork über Firmengrenzen hinweg – neben den EMAG Tochterunternehmen waren diverse externe Digitalisierungsspezialisten beteiligt. Insofern war für uns klar: Für dieses Gespräch brauchen wir mehrere Beteiligte: Peter Strohm, Business Development Manager IoT bei EMAG, sowie Ricarda Schuhmann und Lukas Siegele vom Partner intuity berichten hier über den Entwicklungsprozess, die Möglichkeiten von EDNA und warum sie sich über einen besonderen Preis sehr freuen.
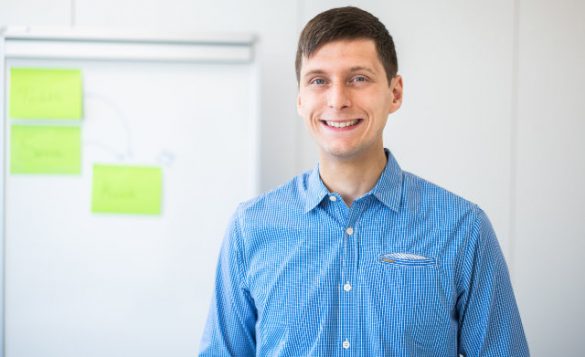
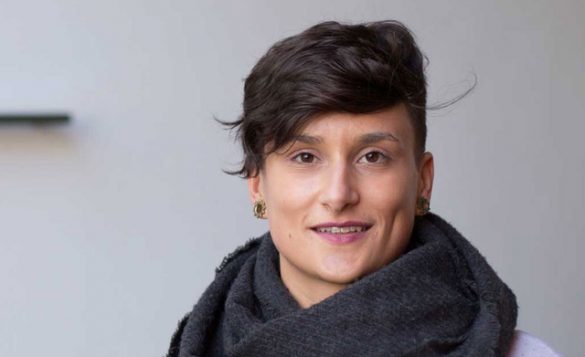
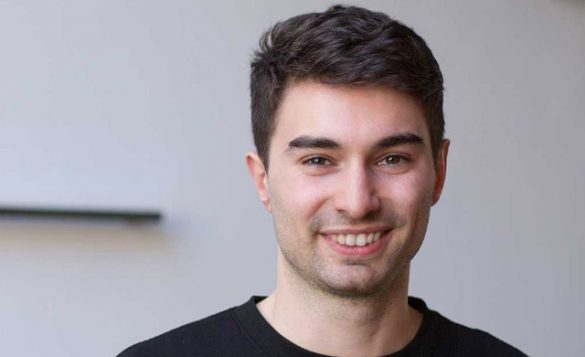
Herr Strohm, fangen wir mit der Vorgeschichte an – wie startet man ein Megaprojekt wie EDNA?
Peter Strohm: Das ist tatsächlich eine Herausforderung. Schauen Sie sich dazu einfach die beeindruckende Struktur und Leistungsfähigkeit von EMAG an: Wir entwickeln Turn-Key-Fertigungslösungen auf höchstem Niveau. Dazu greifen wir auf die Erfahrung von diversen Tochterunternehmen zu, die dann jeweils ihr Wissen einbringen. Es ist ja klar, dass ein Ökosystem für die Digitalisierung der industriellen Produktion in allen Maschinen und Produktionslösungen von EMAG zum Einsatz kommen muss. Wir haben deshalb in sehr vielen Workshops mit den Experten unserer Tochterunternehmen die Anforderungen diskutiert und jeden Entwicklungsschritt mit ihnen abgestimmt.
Wie ist es möglich, dass eine solche Lösung sowohl auf einer Drehmaschine, einer induktiven Härtemaschine als auch auf einer ECM-Maschine problemlos läuft?
Peter Strohm: Das Zauberwort ist „Modularität“. Wir haben gewissermaßen ein Baukastensystem erarbeitet, das wir je nach Anwendung und Produktionssystem anpassen. Mit Blick auf das dazugehörige Bedienpanel geht das sehr schnell. Beim eigentlichen IoT-Kern von EDNA – dieses Gehirn der Maschine nennen wir „Cortex“ – ist der Aufwand natürlich etwas größer. Hier müssen wir zum Beispiel die Anbindung an verschiedene Maschinensteuerungen von Siemens, Fanuc oder BWO umsetzen. Alles passiert im Teamwork mit den Entwicklern unserer EMAG Tochterfirmen.
Ist das System bereits bei Kunden im Einsatz?
Peter Strohm: Grundsätzlich können wir EDNA sowohl bei neuen Maschinen und als auch bei laufenden Bestandsmaschinen zum Einsatz bringen. Letzteres ist bereits der Fall und die Kunden zeigen sich mehr als begeistert: Die OEE ihrer Produktionslinien steigt deutlich an. Vor diesem Hintergrund schätzen wir, dass bereits nach rund einem Jahr ein „Return on Invest“ möglich ist – wenn die gewonnenen Daten ausgewertet und für Handlungsableitungen genutzt werden.
Wie schnell vollzieht sich die Nachrüstung – steht die Maschine zum Beispiel lange still?
Peter Strohm: Überhaupt nicht. Ein Großteil der Arbeit erfolgt nicht vor Ort, sondern am Standort von EMAG, wo wir das System passgenau für die gewünschte Lösung konfigurieren. Die eigentliche Nachrüstung an der Maschine vor Ort dauert dann nur rund einen Tag. In der Folge profitiert der Kunde direkt von den gewünschten Funktionalitäten – unser App-Baukasten ist bereits sehr groß. Er reicht von der Prognose der Ausbringungsmengen über laufende Infos zur verbleibenden Werkzeug-Standzeit bis zur detaillierten Aufschlüsselung der aktuellen OEE.
Wo und wie kann man sich diese Daten anschauen?
Ricarda Schuhmann: Diese Frage führt zum zweiten Schwerpunkt unserer Entwicklungsarbeit, denn es genügt ja nicht, Maschinen nur umfassend zu vernetzen beziehungsweise die Daten zu verarbeiten, zu aggregieren und zu analysieren – die daraus folgenden Handlungsableitungen müssen sie auch in der richtigen Weise darstellen und an Menschen weitergeben können. Genau das erreichen wir mit dem dazugehörigen EDNA Lifeline Dashboards. Seine Usability ist in vielfacher Hinsicht an ein modernes Tablet oder Smartphone angelehnt. Die Bediener kennen die dahinterliegende Bedienphilosophie also bereits aus ihrem Alltag und erlernen die Bedienung somit viel schneller.
Lukas Siegele: Außerdem macht sich die Übersichtlichkeit im Produktionsalltag bezahlt: Auf Anomalien, erreichte Werkzeugstandzeiten oder Maschinenverschleiß wird frühzeitig hingewiesen, was übersehene Ausschussteile und ungeplante Stillstände verhindert. Dabei haben Produktionsplaner, Bediener und Co. von überall aus Zugriff auf das Dashboard – beispielsweise per Smartphone.
Mit dem gesamten EDNA-Ökosystem, auf dem die IoT-Lösungen und das neue HMI basieren, haben Sie sich nun sogar beim renommierten Red Dot Award beworben – wie kam es dazu?
Peter Strohm: Wir sind von dieser Lösung wirklich sehr überzeugt und bekommen zudem laufend positive Rückmeldungen. Beispielsweise will einer der Kunden, der das System bereits im Einsatz hat, weitere Maschinen nachrüsten lassen. Insofern fiel die Entscheidung nicht schwer, uns beim Red Dot Award in der Kategorie „Design Concept“ zu bewerben.
Welche Chancen haben Sie sich im Vorfeld ausgerechnet?
Ricarda Schuhmann: Dazu muss man zunächst wissen, dass sich in diesem Jahr 4.200 Unternehmen mit ihren Neuentwicklungen für den Red Dot Award beworben haben. Bei dieser Masse kann man ja nicht von vorneherein davon ausgehen, dass man gewinnt. Umso erfreulicher ist das Endergebnis: Nach der ersten Abstimmungsrunde waren wir unter den 42 „Best of the Best“ und nach der zweiten Runde gehören wir jetzt sogar zu insgesamt fünf Teilnehmern in der Endrunde zum „Luminary Award“. Das ist natürlich ein Riesenerfolg und bestätigt unsere Arbeit.
Wie geht es jetzt weiter?
Strohm: Wir bieten mit EDNA ein umfassendes und zukunftssicheres Industie-4.0-Ökosystem, das sich wie ein Baukasten anpassen lässt – und das ist wichtig. Schließlich gibt es nicht „den einen“ Weg für alle. Jedes Unternehmen muss eigene Lösungen etablieren, die den Anforderungen entsprechen. Und genau darauf sind wir vorbereitet. Das Ganze ist in jeder Hinsicht offen und kann Daten über Protokolle wie MQTT, REST oder perspektivisch OPC-UA übertragen. Auch der Anschluss von zusätzlicher Sensorik und die Integrationsmöglichkeit anderer Maschinenhersteller stellt kein Problem dar. Dazu kommt, dass wir das Angebot von Apps ständig erweitern und die Analyse der anfallenden Daten somit immer umfassender wird. Der Ansatz ist rundum zukunftssicher. Wir freuen uns darauf, EDNA bei immer mehr Kunden zu implementieren.