Wenn Container von LKWs angehoben, große Baggerschaufeln geschwenkt oder schwere Behälter in Produktionsbetrieben gekippt werden, sind sie häufig unverzichtbar: leistungsstarke Dreh-Antriebe. Die Reihe von Anwendungsbeispielen für diese Technologie ließe sich sehr lange fortsetzen. Als Marktführer in diesem Bereich setzt die HKS Dreh-Antriebe GmbH mit Hauptsitz im hessischen Wächtersbach auf vertikale Wälzfräsmaschinen von EMAG Richardon – mit ihrer Hilfe entsteht eine zentrale Verzahnung. Aktuell haben die Spezialisten eine neue Maschine dieses Typs für ihren Produktionsstandort im sächsischen Neukirch angeschafft. Im nachfolgenden Interview erklärt HKS-Produktionsleiter Mario Vogt, was den Ausschlag für diese Investitionsentscheidung gab und welche technologischen Herausforderungen den Prozess prägen.
Herr Vogt, wie würden Sie allgemein die Herausforderungen bei der Produktion von Dreh-Antrieben umreißen?
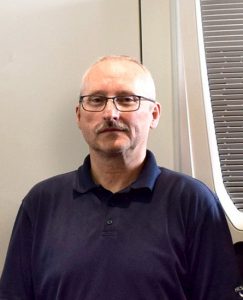
HKS-Produktionsleiter Mario Vogt
Mario Vogt: Zunächst einmal muss man wissen, dass unser Produkt in vielen Anwendungsbereichen eine zentrale Rolle spielt. Dreh-Antriebe kommen überall zum Einsatz, wo eine Masse beschleunigt, abgebremst und präzise positioniert werden muss. Konkret werden dabei zum Beispiel die massiven Seitenwände von LKWs, Arbeitsbühnen oder sehr schwere Baggerschaufeln bewegt. Außerdem benötigt man unsere Technologie an vielen Stellen im Maschinenbau, in der Robotik, im Schiffsbau, in der Bergbauindustrie oder in Kraftwerken. Dabei handelt es sich zumeist nicht um Standardlösungen – im Gegenteil: Wir entwickeln und produzieren individuelle Lösungen mit unterschiedlichen Konstruktionsprinzipien und Leistungswerten. Sie passen perfekt zur jeweiligen Aufgabenstellung. Für unsere Produktionsbereiche heißt das im Gegenzug, dass wir viele verschiedene Bauteile herstellen müssen und die Losgrößen stark variieren. Flexibilität wird bei uns großgeschrieben. Zum Beispiel die Umrüstprozesse müssen deshalb sehr schnell ablaufen.
Was für eine Rolle spielt der Faktor „Qualität“?
Das ist eine entscheidende Kategorie. Unsere Dreh-Antriebe kommen zum Beispiel auch auf Baustellen oder innerhalb von Offshore-Anlagen zum Einsatz. Die Belastung durch raue Umgebungen ist also groß. Außerdem wirken sehr große Kräfte auf die Getriebe. Unsere Produktion muss deshalb sicherstellen, dass alle Verzahnungen sehr genau gefertigt werden, stabile Oberflächen und keinerlei Fehler aufweisen. Das garantieren wir letztlich mit einer hohen Fertigungstiefe an den drei Standorten in Hessen und Sachsen. Sehr viele verschiedene Verfahren vom Drehen, Fräsen und Schleifen über das Verzahnen bis zum Räumen und Stoßen kommen bei uns zum Einsatz.
Aktuell haben Sie für den Standort in Neukirch eine vertikale Wälzfräsmaschine R 300 von EMAG Richardon angeschafft. Wie kam es zu dieser Investitionsentscheidung?
Dreh-Antriebe sind auf dem Vormarsch – es kommen immer neue Anwendungen hinzu. Aktuell setzen zum Beispiel viele Hersteller von Forstmaschinen auf unsere Technologie. Hier sorgen sie für die Greifer-Bewegung von riesigen Baumfäll-Maschinen. Vor diesem Hintergrund steigen natürlich auch die Stückzahlen in unserer Produktion an. In Neukirch kamen zuletzt ältere Maschinen zum Einsatz, die für höhere Ausbringungsmengen nicht mehr geeignet sind. Folglich wurde die Investition in eine moderne Wälzfräsmaschine notwendig. Dass wir dabei auf eine Maschine von EMAG Richardon setzen, liegt nahe. Schließlich sind zwei Wälzfräsmaschinen dieses Typs bereits seit längerer Zeit an unserem hessischen Standort mit großem Erfolg im Einsatz.
Was genau wird mit der neuen Maschine bearbeitet?
In Dreh-Antrieben befindet sich ein Kolben mit einem Steilgewinde, das wir mithilfe der R 300 herstellen. Dieses zentrale Verzahnungselement wandelt die Linearbewegung des Kolbens in eine summierte Drehbewegung um – und nur eine sehr präzise Verzahnungsfertigung garantiert, dass dieser Prozess stabil abläuft. Auf der vertikalen Wälzfräsmaschine werden dabei sehr unterschiedliche Kolben mit Modul-3-Außenverzahnungen und einer Breite von 90 bis 350 Millimetern bearbeitet. Die Bauteile sind zwischen 200 und 500 Millimetern lang und zwischen 2 und 200 Kilo schwer.
Wie genau vollzieht sich der Prozess in der Produktion?
Nach dem Einrichten fahren wir die Maschine zunächst mit einem Musterteil ein. Die benötigten Einstellungen kann der Bediener sehr einfach im Steuerungssystem aufrufen. Die R 300 wird entweder per Hand oder per Kran beladen – je nach Größe und Gewicht des Bauteils. Nach Fertigstellung des Musterteils startet der Verzahnungsprozess am ersten „richtigen“ Bauteil. Abschließend erfolgt noch ein Härteprozess.
Haben sich die Prozesse mit Inbetriebnahme der R 300 verändert?
Wir sind viel schneller geworden. Der eigentliche Umrüstprozess – ohne Einfahren – dauert zumeist nur noch wenige Minuten und der Verzahnungsprozess zwischen 2 und maximal 30 Minuten. In der Vergangenheit benötigten wir hierfür bis zu drei Stunden! Insgesamt sind wir also fünf- bis sechsmal schneller, weil wir viel höherer Schnittwerte fahren. Deutlich größere Stückzahlen in einem vergleichbaren Zeitraum sind die Folge.
Sind Sie zufrieden mit der Bearbeitungsqualität?
Die Ergebnisse entsprechen in jeder Hinsicht unseren hohen Anforderungen. Es ist offensichtlich, dass die schwingungsarme Gesamtkonstruktion der Maschine sich positiv auf die Präzision auswirkt. Übrigens punktet die Maschine auch mit Blick auf die Werkzeug-Standzeiten. Sie sind im Vergleich zu den älteren Maschinen um rund 30 Prozent angestiegen.
Wie viele Bauteile werden auf der Maschine gefertigt?
Insgesamt fertigen wir sehr unterschiedliche Kolben und Verzahnungen auf der R 300. Dazu nur eine Zahl: Allein für die diversen Baumaschinen werden etwa 60 verschiedene Dreh-Antriebe benötigt – und das ist nur einer von vielen verschiedenen Anwendungsbereichen. Dabei schwanken unsere Losgrößen zwischen eins und 50. Folglich müssen wir die Wälzfräsmaschine praktisch täglich umrüsten. Angesichts der guten Zugänglichkeit des großen Arbeitsraums und der einfachen Steuerungssoftware ist das aber kein Problem. Unsere Bediener wurden nur zwei Tage lang geschult. Seitdem gibt es keinerlei Probleme.
Die Maschine ist seit einigen Monaten im Einsatz. Was für ein Fazit ziehen Sie?
Der ganze Prozess vom ersten Meeting mit EMAG bis zur Auslieferung und Inbetriebnahme der Maschine vollzog sich völlig reibungslos. Es kam zu überhaupt keinen Problemen. Zudem ist die Maschine schnell, präzise und robust. Unsere Investitionsentscheidung wurde in der Praxis bestätigt.
Mehr zur R 300 finden Sie hier…