09/20/2021 - Oliver Hagenlocher - Customer Stories
Supplier ZLKL establishes high-end manufacturing processes with EMAG
It is an impressive success story: Since its foundation in 1993, the Czech supplier company ZLKL has shown constant growth - most recently around 15 percent per year. Today, more than 200 employees work at three locations. They produce sophisticated components for the electrical and automotive industries. According to those responsible, a decisive success factor is the continuous investment in advanced production technology with automation components, and EMAG solutions play a major role in this. Aproximately 25 machines from the southern German machine manufacturer are in operation at ZLKL's Czech sites. Why do the people in charge at ZLKL keep putting their trust in EMAG?
"We rely on high-end manufacturing technologies to develop high-end manufacturing processes," says Karel Zeman, Senior Manager Machining at ZLKL, summing up his company's formula for success. "This creates high-volume production that satisfies very demanding customers from the automotive and other industries." Regular investments in manufacturing technologies have shaped ZLKL's development in this regard, and a current emphasis on electromobility has earned them several orders. "In addition, we are continuously strengthening our position as a Tier 1 supplier. Our vast experience of central components is paying off here," adds Zeman.
Productivity increases significantly with vertical turning
The company started investing in EMAG technology about ten years ago. Two factors changed the direction of general development. Firstly, the product portfolio contained more and more chuck parts ideally suited for vertical pick-up turning. Secondly, the conventional turning technology previously used no longer produced the desired results. "We very quickly realized that vertical turning significantly increases productivity. In addition, with many EMAG machines it is possible to integrate further operations such as drilling or milling. This provides an added performance plus for complex components," explains Zeman. "Incidentally, we benefit from the high reliability of EMAG machines in continuous operation. Last but not least, we have a competent partner for establishing new production processes."
High volumes - maximum quality
ZLKL currently has around 25 EMAG machines in operation - including the modular pick-up machines VL 3, VL 3 Duo, VL 4, VL 5, VL 7 and VL 8; the turning center VM9; the vertical machine VTC for multi-axis shaft machining; and, at the end of this year, a first VL2. This technological base is used to produce roughly 300,000 powertrain components per month for electric and combustion engines, such as flanges, hubs, housings and shafts. Since ZLKL's products are subject to high mechanical stress in later use, producing quality parts is as important as the number of components. "So, it is particularly important that the quality is right. Each component must be very stable and manufactured with high precision to guarantee the function of the powertrain in the long term," says Zeman.
In this context, the technical details of the EMAG’s VL machines show potential possibilities.
Despite their integrated pick-up automation and integrated parts storage, they have a small footprint. The pick-up spindle moves very quickly in the X and Z axes, and the mold turret guarantees short swivel times. In addition, the machines can be equipped with a Y axis in the turret for complex geometries. The VL 3 DUO, for example, which is also in use at ZLKL, ensures even greater productivity. It has two separate workspaces for OP 10 and OP 20. Each workspace is equipped with a powerful pick-up spindle and a tool turret with 12 tool stations. The integrated automation system not only ensures fast parts transport between the parts storage and work areas, but also turns the parts between OP 10 and OP 20.
Ensuring a smooth production flow
Optimum integration of the machines into the production flow is greatly important to ZLKL. Here, the Czech production planners benefit from the flexibility of EMAG technology. There are independent production cells, machines arranged in parallel for larger output quantities, and complete production lines including EMAG machines. Many solutions feature a high degree of automation and in-process measurements and other control procedures, which in turn provide the indispensable process reliability and efficiency. "Every new process is designed so that we can meet high customer expectations in terms of unit costs and quality. We are talking here about customer-specific components that are produced in large quantities for many years. Consequently, we do not make any compromises on key factors – and in my experience, this is exactly the requirement we can ensure with EMAG", Zeman summarizes.
이미지
다운로드
담당자
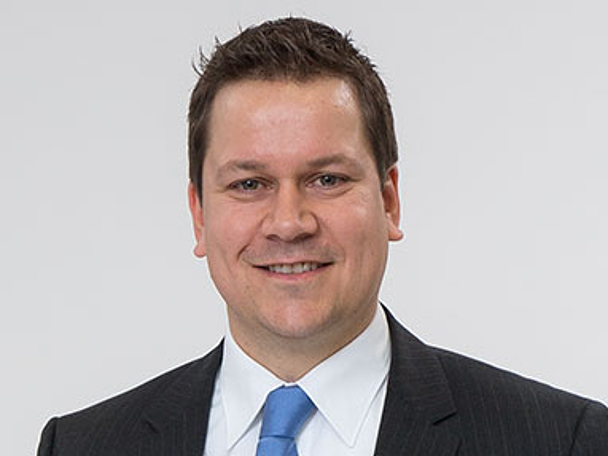