Mit dem Health Check bietet EMAG seinen Kunden ein IoT-Tool für die Gesundheitsbewertung von Vorschubachsen und Spindeln, um deren Wartungszeiträume besser planen zu können. Darüber hinaus entwickelt EMAG diese Lösung immer weiter, wie Patrick Kaiser, Data Scientist bei EMAG, im Gespräch betont: „Die Erfahrungen und unser Service fließen hier gezielt ein“.
Herr Kaiser, welche Rolle spielen IoT-Lösungen grundsätzlich für EMAG?
Sie werden immer wichtiger – auch und gerade weil man mit ihnen echte Mehrwerte schaffen sowie neue Optimierungspotenziale erschließen kann. Und genau das ist immer unser Ziel als Maschinenbauer. Folglich nutzen wir die Datenanalyse und die Vernetzung der Maschinen, um zum Beispiel den Service effektiver zu machen.
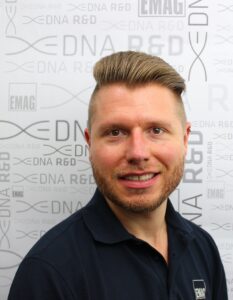
Patrick Kaiser, Data Scientist
Ist die Implementierung dieser Lösungen nicht immer ein großer Aufwand?
Wir haben in den letzten Jahren sehr gezielt daran gearbeitet, diesen Aufwand massiv zu reduzieren – mit der Entwicklung von EDNA. Das ist unser Software-Ökosystem für die Entwicklung von IoT-Anwendungen, wobei der manuelle Aufwand bei deren Implementierung schrumpft. Darauf setzt jetzt auch der Health Check – eine halb-automatische Gesundheitsbewertung sowie ein Frühwarnsystem für Vorschubachsen und Spindeln von Drehmaschinen.
Den Begriff „vorausschauende Wartung“ hört man seit Jahren sehr häufig. Was zeichnet hier den Ansatz von EMAG aus?
Zunächst muss man betonen, dass der Health Check zukünftig eine Kombination von verschiedenen Techniken ist – die Entwicklung dazu läuft gerade. Es gibt zukünftig Elemente der vorausschauenden Wartung als auch der zustandsbasierten Wartung und des Zustandsmonitorings. Bei ersterem wird der Zustand der Maschine anhand von Modellen ermittelt. Die zustandsbasierte Wartung startet hingegen immer, sobald ein Schwellenwert überschritten wird. Beim Zustandsmonitoring werden bestimmte Zustände dokumentiert und visualisiert, was wiederum für die Organisation der Wartung eine Basis bildet. Wir führen das alles in einer Lösung zusammen.
Wie sieht die praktische Umsetzung aus?
Am Anfang stehen 3D-Beschleunigungssensoren, mit deren Hilfe wir Schwingungen messen, sowie ein Industrie-PC, der an die Steuerung der Maschine angeschlossen wird. Er zeichnet mithilfe der Software EDNA Cortex diese Fertigungs- und Sensordaten auf. Das ist die technische Basis für den Health Check. Je nach Variante dieser Lösung stehen unterschiedliche Apps für Anwender zur Verfügung, denn es gibt gewissermaßen eine Vollversion, die wir einfach Health Check nennen, sowie den Health Check Lite.
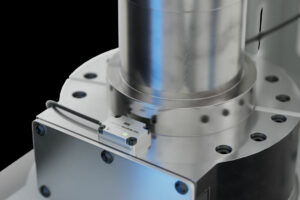
Mithilfe von 3D-Beschleunigungssensoren werden Schwingungen aufgezeichnet.
Was unterscheidet die beiden Versionen?
Bei der Vollversion werden die angesprochenen Messungen automatisch ausgeführt und an EMAG transferiert, wo direkt eine Gesundheitsbewertung auf Basis von Modellen erfolgt, die wiederum auf Erfahrungswissen basieren. Das Ergebnis wird innerhalb weniger Minuten auf Dashboards angezeigt und kann von den Nutzern über eine App eingesehen werden. Auf Kundenwunsch erfolgt zusätzlich eine manuelle Bewertung durch Experten von EMAG.
Beim Health Check Lite vollzieht sich der Prozess nicht automatisch. Hier startet der Anwender das Programm manuell, um Schwingungen aufzuzeichnen. Die Ergebnisse sendet er per Mail zur detaillierten Analyse an EMAG. Der Health Check Lite hat also keinen direkten Zugang zur Analyse-Software im EMAG Netzwerk. Die anschließende Bewertung erfolgt aber ebenso auf Basis von Modellen.
Wie kann man sich die Ergebnisse vorstellen?
Die Gesundheitswerte der Vorschubachsen und Spindeln werden in Form von Prognose-Charts angezeigt – ein Liniendiagramm mit einzelnen Punkten, wobei jeder Punkt für eine Messung steht. Für die Berechnung der finalen Gesundheitswerte glätten wir die Ergebnisse, damit man sich nicht unnötig auf Ausreißer konzentriert. Der Kunde sieht am Ende einen Trend, dessen Tendenz leicht abzulesen ist. So entsteht ein wertvolles Frühwarnsystem für die Wartung – denn die interpretierten Schwingungen können etwa auf Lagerspiel und -schaden, Spindelvibrationen im Stillstand oder andere Störfrequenzen hinweisen.
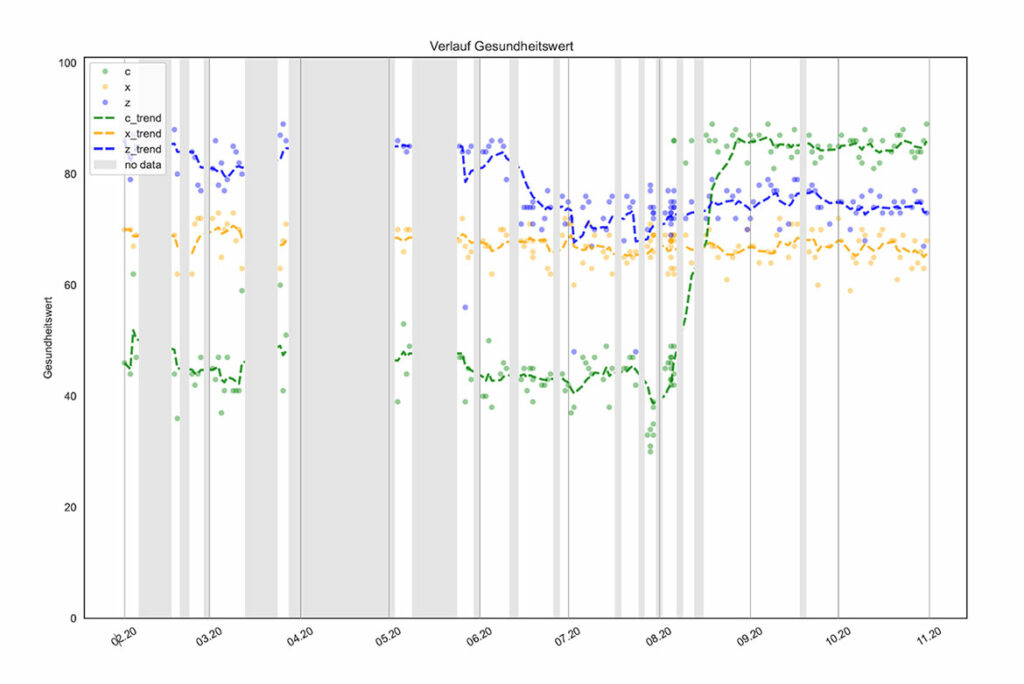
Beispiel für einen Prognose-Chart im EMAG Health Check
Bleibt am Ende die Frage nach den aktuellen Entwicklungen: Was gibt es Neues rund um den Health Check?
Grundsätzlich optimieren wir diese Lösung kontinuierlich. Erfahrungen des Service und weitere Erkenntnisse aus der laufenden Nutzung des Health Checks fließen mit ein. Aktuell haben wir etwa einen mobilen Health Check auf der Roadmap, bei dem der EMAG Service verschiedene Sensoren verwendet, um vor Ort bei den Anwendern Daten zu erheben und direkt per KI auszuwerten. Auf diese Weise lassen sich zukünftig auch Maschinen überprüfen, die noch nicht „IoT Ready“ sind.
Außerdem arbeiten wir aktuell an einem Health Check Messkoffer. Er könnte zukünftig zum Einsatz kommen, wenn an einer Maschine bestimmte Probleme regelmäßig auftreten. Man kann dann einfach mithilfe eines mobilen IPC Messungen über einen bestimmten Zeitraum dokumentieren – ohne dass der Techniker immer vor Ort ist. Anschließend werden die erhobenen Daten analysiert und gegebenenfalls die Ursache behoben.
Weitere Information zum EMAG Health Check