Mit Einführung der EURO-7-Norm müssen sich die Bremssysteme im Auto massiv verändern. Zum ersten Mal werden darin die Feinstaub-Emissionen geregelt – und viele aktuelle Modelle halten mit ihren Bremsen diese Vorgaben nicht ein. Was bedeutet das konkret für die Automobilproduktion, welche Rolle spielen beschichtete Bremsscheiben und warum ist die neue Laser-Metal-Deposition-Technologie von EMAG hierbei der Königsweg? Ein Gespräch mit Dominic Grimminger, Experte für das Bremsscheibenbeschichten bei EMAG.
Warum ist das Thema „Bremsscheiben-Beschichtung“ überhaupt so wichtig?
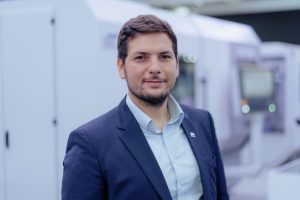
Dominic Grimminger, Spezialist bei EMAG für die Bearbeitung von Bremsscheiben
Das hängt im Wesentlichen mit der EURO-7-Norm zusammen. Hier werden zum ersten Mal nicht nur Abgaswerte des Verbrennungsmotors, sondern auch die Feinstaub-Emissionen von Reifen und Bremsen reguliert. Für Letzteres gilt dann ein Wert von nur noch 7 Milligramm Feinstaub je Kilometer – und das für alle Modelle. Zum Vergleich: Aktuell beträgt dieser Wert je nach Modell zwischen 5 und 40 Milligramm! Gerade bei größeren Fahrzeugen mit höheren Feinstaub-Emissionen muss also ein Weg gefunden werden, den Ausstoß massiv zu reduzieren. Das ist mit beschichteten Bremsscheiben in Kombination mit einem darauf abgestimmten Bremsbelag möglich. Konstruktive Veränderungen am Fahrzeug sind dabei nicht notwendig.
Gäbe es Alternativen, um die Feinstaub-Emissionen des Bremssystems zu reduzieren?
Häufig werden in der Medien Absaugsysteme genannt, die sich in der Nähe der Bremsen befinden und den Feinstaub dort absorbieren sollen. Allerdings wird dabei nur ein Teil der Emissionen abgesaugt. Zudem müssten die Hersteller zusätzlichen Bauraum einplanen, höhere ungefederte Massen in Kauf nehmen – und somit größere konstruktive Änderungen am Fahrzeug vornehmen, was den Gesamtaufwand enorm erhöht. Eine weitere Möglichkeit ist der Einsatz von sogenannten NAO-Bremsbelägen (Non-Asbestos Organic). Tatsächlich nehmen so die Feinstaub-Emissionen ab. Allerdings gilt das nur bei fabrikneuen Bremsscheiben. Nach kurzer Zeit im Einsatz steigen sie wieder auf das heutige Niveau an.
Welche Herausforderungen gibt es beim Beschichten der Scheiben?
Grundsätzlich ist die Idee, Bremsscheiben zu beschichten, nicht neu. Allerdings waren die Produktionskosten bislang häufig zu hoch sowie der Prozess auf Basis von thermischen Spritzverfahren oder Galvanisieren zu kompliziert. Hier sind aufwendige Vorbearbeitungen für die Anbindung der Schicht notwendig. Außerdem sind die Schichten (zu) dick und der Wärmeeintrag ist hoch. Vor diesem Hintergrund stellt die Neuentwicklung von EMAG auf dem Gebiet des Laserauftragschweißens von Bremsscheiben einen großen Fortschritt für diese Aufgabenstellung dar. Die neue Produktionslösung ist wirtschaftlich, großserienfähig, prozesssicher – und variabel, denn es kann eine Vielzahl von Materialkombinationen zum Einsatz kommen.
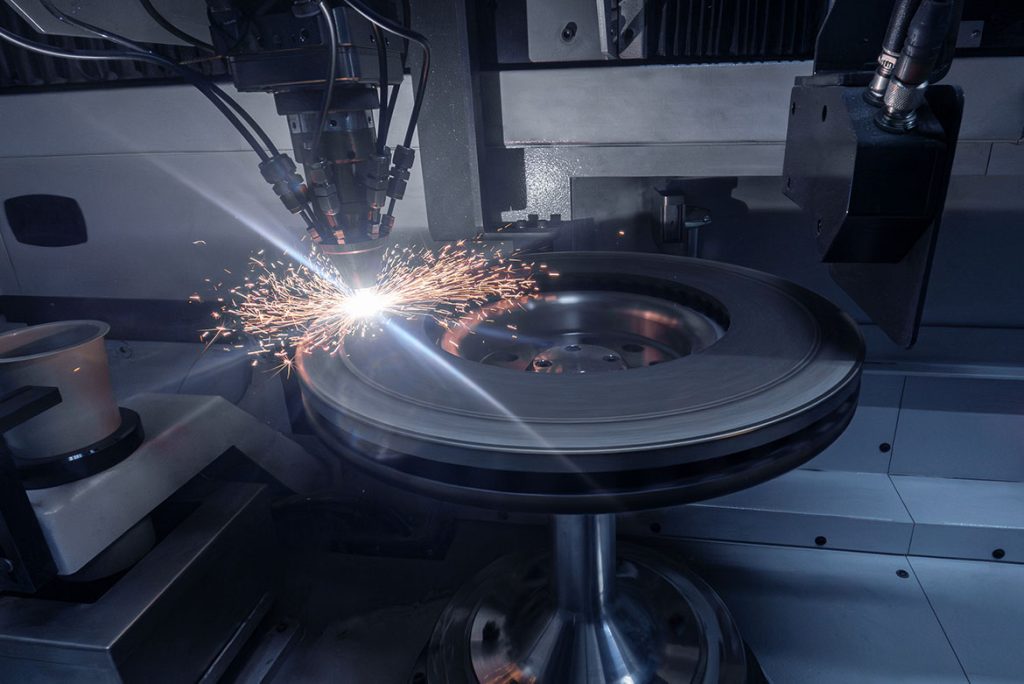
Per Laserauftragschweißen wird eine zweilagige Beschichtung aufgebracht, die Bremsscheiben vor Korrosion und Verschleiß schützt.
Was zeichnet diese Lösung im Detail aus?
Im Mittelpunkt steht die bekannte Laser-Metal-Deposition-Technologie. Hierbei wird Werkstoffpulver durch einen Kanal einem Laserwerkzeug zugeführt. Anschließend verschmilzt es mit der Oberfläche der Scheibe im Schmelzpunkt des Schweißprozesses. Diesen Ansatz hat EMAG mit seiner Laserbeschichtungstechnologie optimiert. So sorgt das Verfahren dafür, dass die Flächenrate jeweils sehr hoch, die Schichtdicke minimal und die Oberflächen besonders glatt sind – und das bei kleiner Rauheit. Hierzu nur zwei Zahlen zur Verdeutlichung: Beim EMAG Laserbeschichtungsprozess werden Flächenauftragsleistungen von 2.500 cm²/min erzielt; das ist ein Vielfaches höher als beim konventionellen Laserauftragschweißen. Und während die Schichtdicke beim konventionellen Laserauftragschweißen typischerweise rund 0,5 mm beträgt, können wir hier Werte von unter 0,01 mm erreichen. Auf dieser Basis ist das Verfahren großserienfähig.
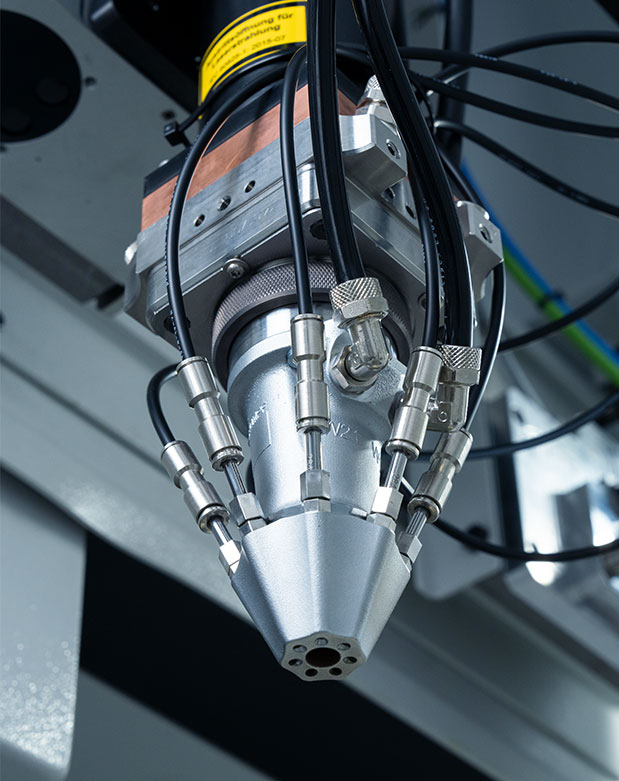
Aufbau des Laserwerkzeugs: Der Beschichtungswerkstoff wird als Pulver zugeführt und per Laserprozess mit der Bauteiloberfläche verschmolzen.
Welche Rolle spielt der Maschinenbau?
EMAG stellt mit seinem großen Prozess-Know-how rund um die Laserbearbeitung und das Doppelseiten-Planschleifen – beide Verfahren spielen hier eine Rolle – sicher, dass Anwender auf Wunsch Turnkey-Lösungen für die gesamte Prozesskette bekommen. So gibt es etwa bereits ein ausgefeiltes Maschinenkonzept für das Laserauftragschweißen von Bremsscheiben mit drei Rundtischen in einer Maschine. Auf dem ersten vollzieht sich das Aufbringen der Grundschicht, was ungefähr doppelt so schnell vonstattengeht als das Aufbringen der darüber befindlichen Hartstoff-Schicht parallel auf zwei Bauteilen auf den zwei nachfolgenden Rundtischen.
Die EMAG Lösung für das Doppelseiten-Planschleifen der beschichteten Bremsscheibe profitiert von hoher Steifigkeit und einem intelligenten Abdeckungskonzept an den Schleifscheiben. Beide Schleifspindeln sind dabei parallel angeordnet, wobei die Bremsscheibe per Kreuzschliff bearbeitet wird. Die Schleifscheiben schärfen sich von selbst.
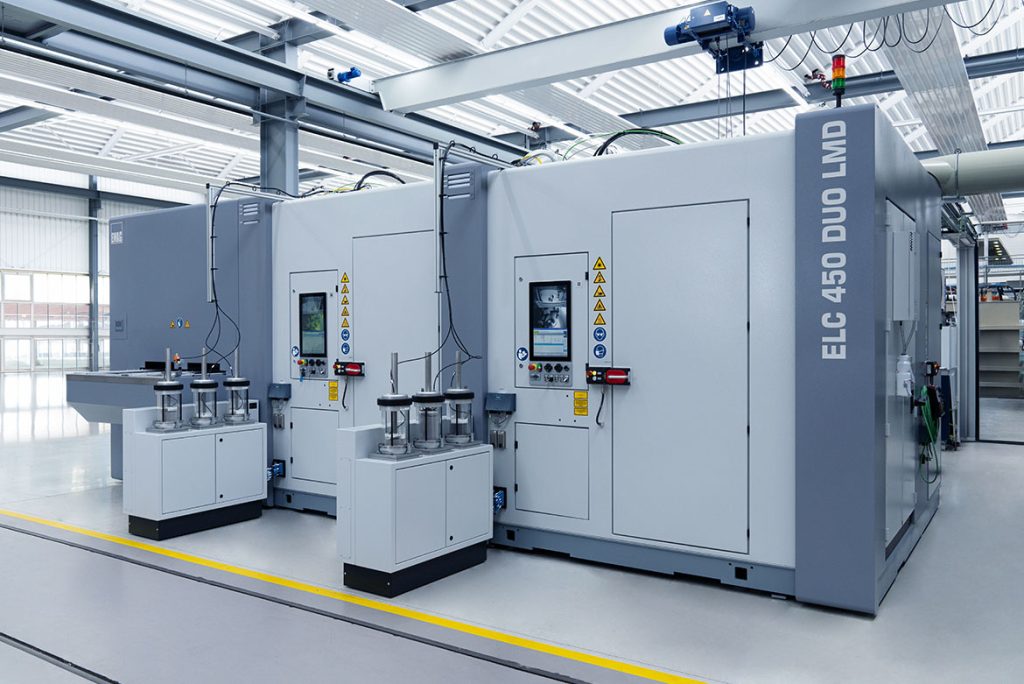
Die ELC 450 DUO LMD mit zwei Prozessmodulen ermöglicht eine gesteigerte Produktivität beim Hartstoffbeschichten von Bremsscheiben.
Wie variabel ist die gesamte Lösung?
Sowohl mit Blick auf den Maschinenbau als auch die benötigten Beschichtungen sind nahezu alle Varianten abdeckbar. So unterstützen wir auf Wunsch sogar bei der Entwicklung der Beschichtungssysteme, wobei sich natürlich auch vorhandene Schicht-Konzepte umsetzen lassen. Insgesamt profitieren Kunden hier von unserem umfassenden Know-how – von der Frage der Laserleistung und den entsprechenden Düsenkonzepten bis zur Parameteroptimierung. Auf der anderen Seite kann EMAG seine Maschinenkonzepte flexibel anpassen und zum Beispiel nur zwei Rundtische in die Maschine integrieren – etwa, wenn es sich um eine einlagige Beschichtung handelt. Zusammenfassend heißt das: Das Ganze steht für ein großes Verfahrens-Know-how und für ganzheitliche Lösungen aus einer Hand.