Es gibt nicht das „eine“ beste Verfahren zum Reinigen oder Entschichten von Werkstücken. Letztlich kommt es auf Grundbedingungen und Zielsetzungen im Produktionsprozess an, die über die Wahl des Verfahrens entscheiden. In diesem Sinn ist das Laserreinigen auch kein Eins-zu-eins-Ersatz für das klassische Waschen – nichtsdestotrotz ist es häufig im Vorteil.
Die Laserreinigung ist sehr energieeffizient und schnell.
Wann genau ist ein Bauteil eigentlich ausreichend sauber oder entschichtet? Die Frage klingt banal. Sie ist für die Konfiguration eines jedes Reinigungsprozesses aber ganz entscheidend, denn er muss idealerweise so konfiguriert sein, dass genau die richtige Menge Energie und Zeit verbraucht werden, um die jeweilige Verschmutzung bzw. Beschichtung in einer bestimmten Weise zu beseitigen – „Nicht mehr als nötig“ ist die einfache Devise. Alles andere wäre ein unnötig aufwändiger (und teurer) Prozess.
Punktgenaue Reinigung
An dieser Stelle punktet das Laserreinigen: Hier kommt ein fokussierter Laserstrahl zum Einsatz, der per Scanner (und gegebenenfalls Maschinenachsen) über die zu reinigende Fläche bewegt wird. Die Parameter dieses Verfahrens wie etwa Leistung und Pulsfrequenz des Lasers, seine Vorschubbewegung und Spurbreite sowie die Bearbeitungsdauer lassen sich flexibel konfigurieren und somit also an den Grad der Verschmutzung und das gewünschte Maß von Sauberkeit perfekt anpassen. Außerdem werden nur definierte Flächen und Geometrien gereinigt oder entschichtet. Dies alles sorgt zusammen für eine optimale Reinigungsleistung bei ebenso optimierter Taktzeit. Das Motto „Nicht mehr als nötig“ lässt sich hier also perfekt umsetzen, was nicht zuletzt zu sehr niedrigen Betriebskosten führt. Waschmaschinen sind hingegen echte „Energiefresser“, der Wartungsaufwand ist sehr hoch und Flüssigkeiten sowie Filter müssen regelmäßig entsorgt werden. Dazu kommen Trocknungs- und Spülprozesse, die den gesamten Produktionsprozess weiter verlangsamen.
Serie oder Batch-Lösung?
Außerdem ist das Laserreinigen ein serieller Prozess, während das Waschen ein Batch- oder Durchlaufprozess ist. In der Folge hat man beim Laserreinigen wesentlich weniger Teile im Reinigungsdurchlauf und es gibt keine Liegezeiten (wie bei Batch-Anlagen). Der gesamte Produktionsprozess lässt sich deshalb optimieren und als One-Piece-Flow konfigurieren. Dazu kommt ein geringerer Platzbedarf beim Laserreinigen. So benötigt die Maschine LC 4 von EMAG nur eine Stellfläche von 4,5 Quadratmetern. Sie lässt sich sowohl in ganzheitliche Produktionslinien einbinden als auch alleinstehend einsetzen. Dazu verfügt sie über einen Rundtisch, der getrennt vom Arbeitsbereich ist. Er kann bei Bedarf per Automation (oder eben per Hand) hauptzeitparallel be- bzw. entladen werden. Außerdem ist es optional möglich, zwei Bauteile gleichzeitig zu spannen, während zwei andere den Reinigungsprozess durchlaufen.
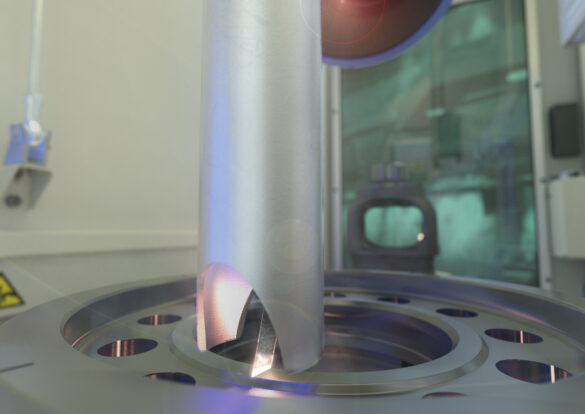
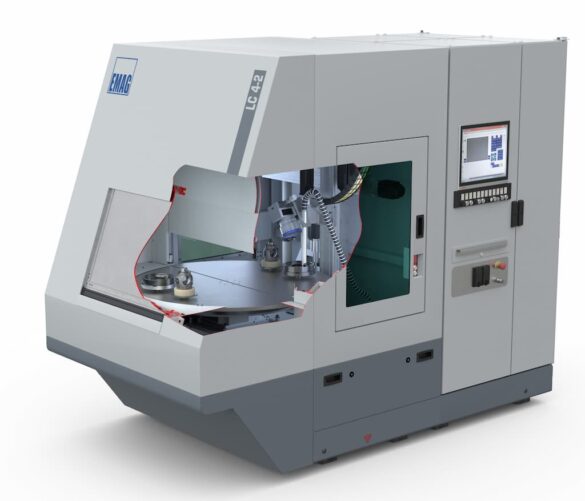
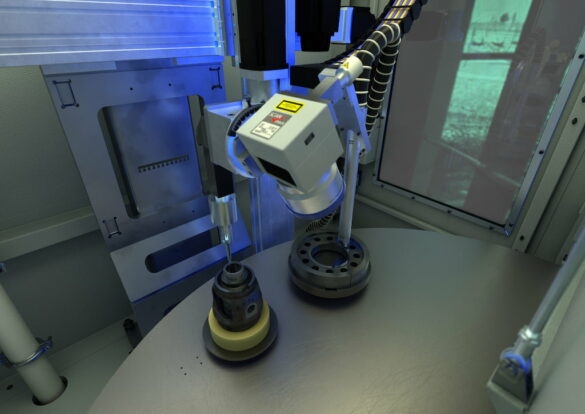
Art der Verunreinigung
Interessant ist abschließend ein Blick auf die Art der Verunreinigung. So ist die Laserreinigung sehr gut geeignet, um dünne Schichten von Fett, Kühlschmierstoffen und Korrosionsschutzschichten abzutragen. Gleiches gilt für die Alternative „Waschen“. Allerdings können manche Kühlmittelschmierstoffe, die insbesondere bei der Minimalmengenschmierung zum Einsatz kommen, aufgrund ihrer chemischen Struktur beim Waschen zu Problemen führen. Das ist bei der Laserreinigung nicht der Fall. Späne und Partikel lassen sich per Laser nicht entfernen. Hier ist der Waschprozess (den man beispielsweise mit einem Späne-Sieb ausstatten kann) im Vorteil. Lackierungen, Zink-Phosphat-Schichten, KTL-Beschichtungen, Pulverbeschichtungen, Oxide und Roste werden hingegen sehr gut per Laser beseitigt. Waschprozesse sind in diesen Anwendungsfeldern praktisch wirkungslos.
EC-Clean-Software von EMAG
Übrigens: Ein wichtiger Erfolgsfaktor für den Laserreinigungsprozess ist die EC-Clean-Software von EMAG, die bei der Maschine LC 4 zum Einsatz kommt. Mithilfe dieser Steuerungssoftware wird das Laserreinigen zu einem leicht handhabbaren Prozess. Alle relevanten Einstellungen wie Laserparameter, Scannerparameter, Geometrie, Vorschubgeschwindigkeit etc. lassen sich mit dieser Lösung einfach beeinflussen. Dabei unterstützt EC-Clean den Anlagenführer bei der Auswahl. Konkret heißt das: Er muss NICHT mit komplizierten Parametern hantieren, sondern kann sich auf wenige Einstellungen wie Teile-Geometrie, Spurbreite und Reinigungsenergie konzentrieren. Alle anderen Parameter werden automatisch berechnet bzw. aus der internen Technologie-Datenbank entnommen.
Weitere Informationen zur Laserreinigungsmaschine LC 4-2 finden Sie hier…